ISO 9 CleanRoom Classification
ISO 9 is part of the ISO 14644 standard, which categorizes cleanrooms based on the cleanliness of the air within them. Specifically, ISO 9 is the least stringent classification, allowing for a maximum of 35,200,000 particles per cubic meter of air that are 0.5 micrometers or larger. This standard is primarily designed for environments where ultra-clean conditions are not critical, such as in certain manufacturing processes or testing labs where moderate cleanliness is sufficient.
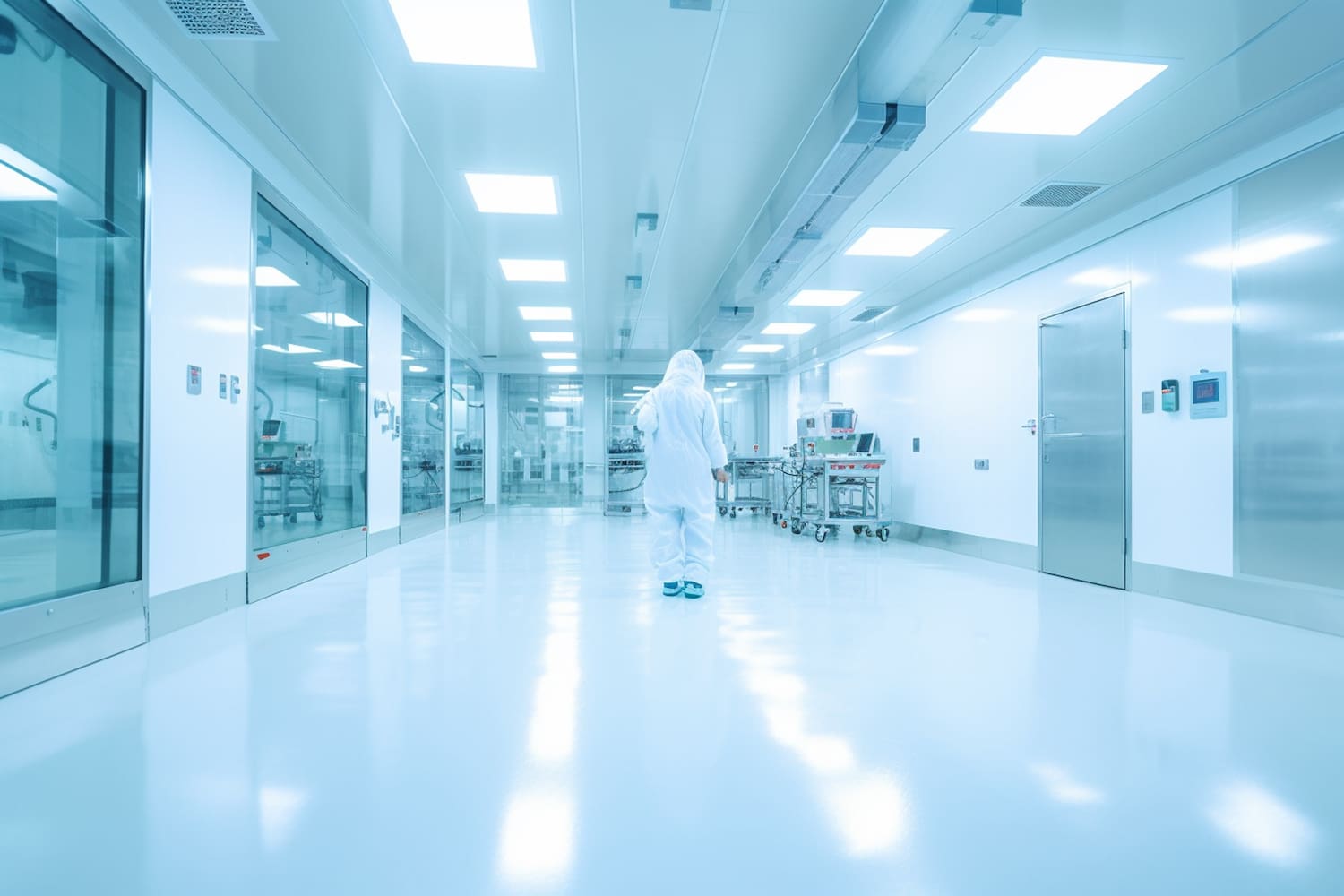
Example of A CleanRoom environment
Key Features of ISO 9 Cleanrooms
Particle Count Limits
The defining characteristic of ISO 9 is its particle concentration limits. For particles of 0.5 micrometers and larger, the acceptable limit is set to 35,200,000 particles per cubic meter.
Application Scope
ISO 9 cleanrooms are suitable for non-critical environments where the risk of contamination is lower. Industries such as food processing, certain manufacturing sectors, and some research laboratories may utilize ISO 9 cleanrooms.
Design Criteria
While ISO 9 cleanrooms can be simpler in design, they still require basic airflow management and filtration systems to maintain lower levels of contamination.
The ISO Classification System
The ISO classification system refers to a set of international standards established by the International Organization for Standardization (ISO) to ensure consistency and quality across various industries. Specifically, in the context of cleanrooms, the ISO classification system categorizes environments based on the levels of particulate contamination present in the air.
This system ranges from ISO 1, which represents the cleanest environment, to ISO 9, which permits the highest levels of airborne particles. Each classification outlines specific limits on particle counts and provides guidelines for Cleanroom design, operation, and monitoring.
ISO Cleanroom Classification | Maximum Particles per m³ (≥ 0.5μm) | Typical Applications |
---|---|---|
ISO 1 | 12 | Semiconductor, Aerospace |
ISO 5 | 3,520 | Aseptic Processing, Clean Packaging |
ISO 8 | 3,520,000 | Food Processing |
ISO 9 | 35,200,000 | Non-critical Applications |
ISO 9 Cleanroom Requirements
Air Quality Standards
The ISO 9 cleanroom must meet specific air quality standards with respect to particle counts, allowing for up to 35,200,000 particles per cubic meter for particles larger than 0.5 micrometers.
Design Specifications
The design of an ISO 9 cleanroom should facilitate effective airflow and filtration. While the requirements are less stringent than those for higher ISO classifications, it is still important to incorporate adequate ventilation and air filtration systems.
Operational Protocols
To maintain compliance with ISO 9 standards, operational protocols should include regular cleaning schedules and personnel training on contamination control.
Monitoring Systems
Continuous monitoring of airborne particles is crucial for maintaining the ISO 9 classification. Regular audits and particle count measurements should be conducted.
ISO 9 cleanroom air Changes Per Hour
Air Change Requirements
Typically, an ISO 9 cleanroom should have a minimum of 20 to 30 air changes per hour. This ensures that the air within the cleanroom is frequently replaced, helping to dilute and remove airborne particulates.
airflow design
Effective airflow design is essential to achieve the desired air change rates. The cleanroom should be designed to promote unidirectional airflow, which helps minimize turbulence.
Monitoring Air Changes
Regular monitoring of air changes is necessary to ensure the cleanroom is functioning correctly. This can be achieved through the installation of airflow sensors and monitoring systems.
Why Only 0.5 and 5 Micron Particle Counts Are Required in Pharma
In pharmaceuticals, monitoring 0.5 and 5-micron particle counts is essential to prevent contamination in sterile products, ensuring patient safety. Regulatory bodies like the FDA emphasize these controls for product efficacy and quality assurance in drug manufacturing.
"ISO 9 cleanroom classification establishes necessary cleanliness standards for various industries, highlighting the importance of understanding its requirements and monitoring strategies to maintain operational integrity."
© 2023 Cleanroom standards Information. All rights reserved.