Difference Between ISO 4 and ISO 5 Cleanroom
Specialized environments with strict contamination control standards
Key Differences
Criteria | iso 4 cleanroom | ISO 5 Cleanroom |
---|---|---|
Particle Count (0.1 µm) | ≤ 10 particles/m³ | - |
Particle Count (0.2 µm) | ≤ 2 particles/m³ | - |
Particle Count (0.5 µm) | - | ≤ 3,520 particles/m³ |
Particle Count (1.0 µm) | - | ≤ 29 particles/m³ |
air changes per Hour (ACH) | > 600 ACH | 240 - 480 ACH |
Typical Applications | Semiconductor manufacturing, aerospace components, critical pharmaceutical processes | Biotechnology, medical device manufacturing, some pharmaceutical operations |
ISO 4 Cleanroom Requirements
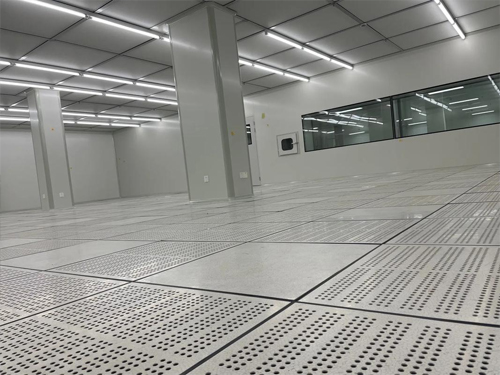
Particle Count Standards
Strict limits with no more than 10 particles per cubic meter for 0.1 µm and 2 particles per cubic meter for 0.2 µm.
Applications
- Semiconductor manufacturing
- Aerospace components production
- Critical pharmaceutical processes
Airflow and Filtration
Requires over 600 air changes per hour (ACH) with advanced HEPA or ULPA filtration systems to maintain rigorous cleanliness standards.
iso 5 cleanroom requirements
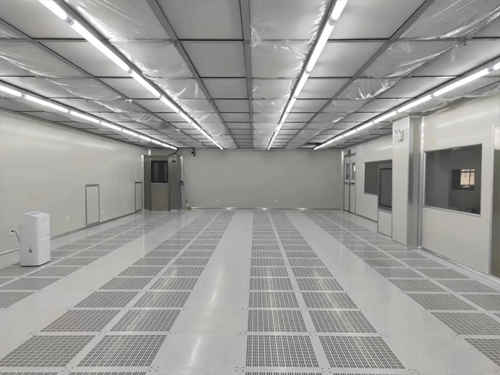
Particle Count Limits
- ≤ 3,520 particles/m³ for 0.5 µm
- ≤ 29 particles/m³ for 1.0 µm
- ≤ 8 particles/m³ for 5.0 µm
Environmental Controls
- Temperature: 20-24°C (68-75°F)
- Humidity: 30-60%
- Positive pressure relative to surrounding areas
Personnel and Maintenance
Strict gowning protocols, regular monitoring of particle counts, and routine maintenance of filtration systems.
Cleanroom temperature and Ventilation
Ideal Temperature
Maintaining 20-24°C (68-75°F) is essential for:
- Product integrity in sensitive processes
- Personnel comfort and focus
- Prevention of thermal fluctuations
Ventilation Rates
Expressed as air changes per hour (ACH):
- ISO 4: Over 600 ACH
- ISO 5: 240-480 ACH
- Uses HEPA or ULPA filters for air purification
Laminar flow systems are often used to ensure uniform airflow and effective contamination removal.
Prohibited Items in Cleanrooms
Items Not Allowed
- Food and drinks: Increase risk of organic contamination
- Personal items: Bags, coats, unapproved Electronics
- Cosmetics and fragrances: Emits VOCs and contaminants
- Unapproved equipment: Must be designed for cleanroom use
Access and Protocols
Strict controls must be in place for:
- Personnel gowning and decontamination
- Monitored entry and exit procedures
- Training on cleanroom protocols
ISO 6 Cleanroom Overview
An ISO 6 cleanroom is a controlled environment that meets specific cleanliness standards as defined by the International Organization for Standardization. It is commonly used in industries where the risk of contamination is moderate.
Particle Count Limits
- ≤ 1,000 particles/m³ for 0.5 µm
- ≤ 29 particles/m³ for 1.0 µm
Typical Applications
- Certain pharmaceutical applications
- Electronics manufacturing
- Research laboratories
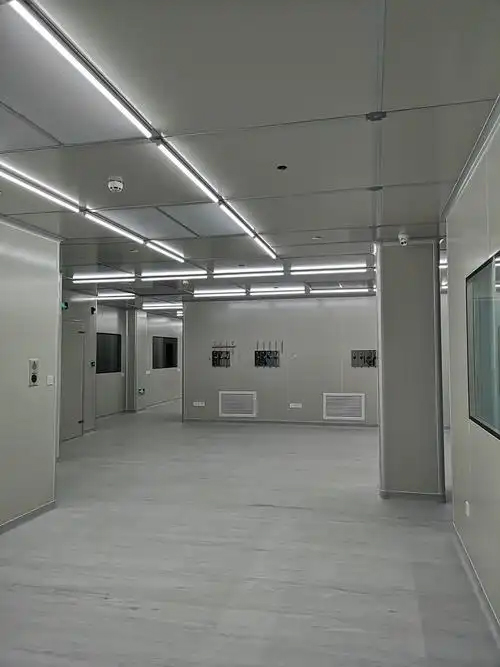
© 2025 Cleanroom Information Portal. All rights reserved.