ISO Class 6 Clean Room
An ISO Class 6 cleanroom is a controlled environment with strict cleanliness standards designed to minimize particulate contamination in the air. It is classified according to the ISO 16px644-1 standard, which sets limits on the number of airborne particles in a given volume of air, as well as other environmental factors like temperature, humidity, and pressure.
1. Particulate Limits
ISO Class 6 allows a maximum of 35,200 particles per cubic meter (or 1,000 particles per cubic foot) for particles 0.5 microns or larger.
An ISO Class 6 cleanroom typically requires 30 to 60 air changes per hour (ACH) to maintain the cleanliness level. Higher ACH rates help dilute and remove contaminants from the air more effectively.
2. Environmental Control
Humidity: Typically controlled between 30% and 60% relative humidity to prevent static buildup and product degradation.
Pressure: The typical pressure differential is about 10-15 Pa (0.04 to 0.06 inches of water column).
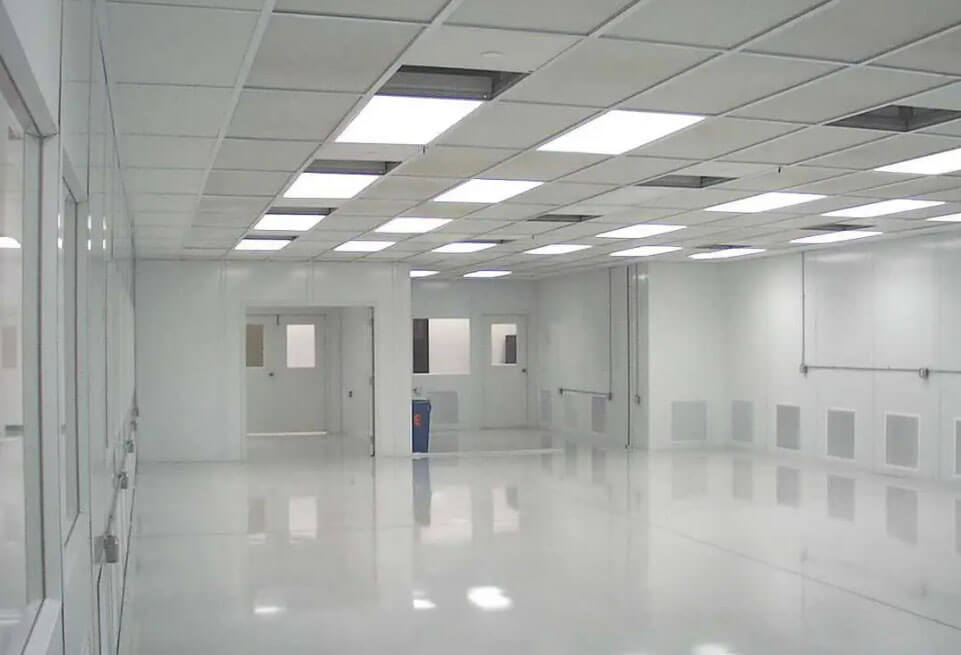
Clean room grade table
ISO Class FED STD 209E Equivalent | |||||||
ISO Class | Maximum Particles/m | FED STD 209E equivalent | |||||
≥0.1μm | ≥0.2um | ≥0.3um | ≥0.5um | ≥11m | ≥5um | ||
ISO1 | 10 | 2 | |||||
ISO2 | 100 | 24 | 10 | 4 | |||
ISO3 | 1,000 | 237 | 102 | 35 | 8 | Class1 | |
ISO4 | 10,000 | 2,370 | 1,020 | 352 | 83 | 3 | Class10 |
ISO5 | 100,000 | 23,700 | 10,200 | 3,520 | 832 | 29 | Class100 |
ISO6 | 1,000,000 | 237,000 | 102,000 | 35,200 | 8,320 | 293 | Class 1,000 |
ISO7 | 352,000 | 83,200 | 2,930 | Class10,000 | |||
ISO8 | 3,520,000 | 832,000 | 29,300 | Class 100,000 | |||
ISO9 | 35,200,000 | 8,320,000 | 293,000 | Room Air |
Comparison Table GMP/USP/ISO/FED209E | ||||||||||||
project | China GMP/Europe GMP | ISO | FED STD 209E | |||||||||
Suspended particles P/m3 | level | Static | dynamic | level | Static | level | dynamic | |||||
≥0.5um | ≥5μm | ≥0.5μm | ≥5μm | ≥0.5um | ≥5μm | ≥0.5um | ≥5μm | |||||
A | 3520 | 20 | 3520 | 20 | M3.5 | 3530 | 100 | 5 | 2220 | 20 | 100 | |
B | 3520 | 29 | 352000 | 2900 | - | - | 6 | 3520 | 29 | 1000 | ||
C | 352000 | 2900 | 3520000 | 29000 | M5.5 | 353000 | 10000 | 7 | 352000 | 2930 | 10000 | |
8. | 3520000 | 29300 | 100000 | |||||||||
D | 3520000 | 29000 | No regulations | No regulations | M6.5 | 3530000 | 100000 | 9 | 3520000 | 29300 | 100000 |
Comparison table of ISO grade standards and ventilation times | |
ISO Class | ACH(AIRCHANGE PER HOUR) |
ISO 3 | 360-540 |
ISO 4 | 300-540 |
ISO 5 | 240-480 |
ISO 6 | 50-60 |
ISO 7 | 30-40 |
ISO 8 | 15-25 |
ISO Class 6 Clean Room Airflow
Air supply from air conditioner:
The air treated by the air conditioner is sent to the return air layer
Air filtration:
The air is deeply filtered through HEPA or ULPA filters to ensure that the cleanliness meets the required ISO level.
Air distribution:
Laminar flow (such as unidirectional flow) or mixed flow is usually used to maintain the uniformity and fluidity of indoor air.
Air return:
The clean room air passes through the return air layer, and 15% of the return air returns to the air conditioner for further treatment
Internal circulation airflow | Vertical unidirectional airflow | Vertical external circulation airflow |
Cleanrooms Wall Panels
Size and appearance
Ensure that the size and shape of the product meet the design requirements and have no obvious defects.
Physical properties
Such as compression, tension, impact resistance and other tests to ensure the strength and durability of the material.
Surface treatment
Confirm that the surface is smooth, the coating is uniform, and there are no bubbles, peeling, etc.
Test report
Fire and corrosion resistance test
MGO Pane | Rock Wool Panel | MGO Rock Wool Panel |
Cleanrooms Doors
Steel standard
Select high-quality steel that meets national and international standards to ensure its corrosion resistance and strength.
Surface treatment
The surface of the door body should be treated with anti-rust treatment (such as spraying, anodizing, etc.) to ensure durability and easy cleaning.
Insulation material
The door core material should have good heat insulation and sound insulation properties, and insulating materials such as polyurethane or rock wool are usually used.
Production process
Production is carried out strictly in accordance with standardized processes, including cutting, forming, welding and painting
single doors | double doors | sliding doors |
Cleanrooms Windows
Steel standard
Select high-quality steel that meets national and international standards to ensure its corrosion resistance and strength.
Surface treatment
The surface of the door body should be treated with anti-rust treatment (such as spraying, anodizing, etc.) to ensure durability and easy cleaning.
Insulation material
The door core material should have good heat insulation and sound insulation properties, usually using insulating materials such as polyurethane or rock wool.
Production process
Strictly follow the standardized process for production, including cutting, forming, welding and painting, to ensure stable quality in each link.
cleanrooms windows | Double hollow window | double decontamination windows |
ISO Class 6 Clean Room Celling
Specifications: Thickness: 980, 1180
Panel material: 50mm, 75mm, 100mm
Core material: color-coated steel plate, stainless steel plate, rock wool, gypsum, glass magnesium, aluminum honeycomb, etc.
Accessories: Keel: 0.8 galvanized plate
Application scope: food, medicine
Others: Coating: PE (polyester), PVDF (fluorocarbon), HDP (high weather-resistant polyester)
![]() | ![]() | ![]() | ![]() |
Easy installation: FFU keels are designed according to the characteristics of clean rooms and are easy to disassemble and assemble
Factory prefabrication: The ceiling system is modularly designed, highly malleable, and can be cut on site
Flexible matching: It can be a double-layer ceiling structure or a single-layer ceiling with FFU keels on the lower layer
![]() | ![]() | ![]() | ![]() |
ISO Class 6 Clean Room Floor
Antistatic performance: Designed for sensitive electronic equipment and laboratory environments, it can effectively prevent static electricity from damaging equipment.
Maintainability: The elevated design makes it easy to maintain and manage pipes and cables under the floor.
Flexibility: The floor height can be adjusted as needed to facilitate the layout and modification of equipment.
Breathability: Certain designs allow air flow to help maintain environmental control in the clean room.
![]() | ![]() | ![]() |
Flexibility: PVC flooring adhesive has good flexibility and impact resistance.
Anti-slip: There is an anti-slip surface treatment to ensure the safety of personnel while working.
Easy to install: Usually provided in roll or tile form, installation is simple and quick.
Diversity: A variety of colors and textures are available for easy visual zoning and aesthetics.
![]() | ![]() | ![]() |
FAQ
What is an lSO class 6 cleanroom?
An ISO Class 6 cleanroom is a high-purity environment with stringent controls over particulate matter, air quality, and environmental conditions. By maintaining strict air filtration and high air change rates, these cleanrooms provide a critical setting for industries that require minimal contamination to ensure product quality and safety.
What is the lsO 6 limit?
Particle Concentration Limits,Maximum allowable concentration of particles per cubic meter:
≥ 0.1 microns: 1,000,000 particles
≥ 0.2 microns: 237,000 particles
≥ 0.3 microns: 102,000 particles
≥ 0.5 microns: 35,200 particles
≥ 1.0 microns: 8,320 particles
≥ 5.0 microns: 293 particles
What are the requirements for lSO 6 cleanroom gowning?
Initial Preparation: Personnel should remove all personal items such as jewelry and watches before entering the gowning area.
Hand Washing: Hands must be thoroughly washed and dried before gowning.
Gowning Sequence:
Don Hair Cover: A hairnet or hood to cover all hair.
Don Face Mask: A mask to cover the nose and mouth, preventing contamination from respiratory particles.
Don Beard Cover: If applicable, a beard cover for any facial hair.
Don Shoe Covers: Shoe covers to prevent contamination from footwear.
Don Coverall: A full-body coverall made from non-shedding material, such as Tyvek or similar fabric. The coverall should be zipped up completely.
Don Gloves: Gloves made of nitrile or latex, covering the wrists and fitting snugly over the sleeves of the coverall.
Don Goggles or Safety Glasses: Eye protection may be required to prevent contamination from skin flakes or hair.
Don Hood: A hood to cover the head and neck, ensuring no skin or hair is exposed.
Final Check: Ensure all gowning items are properly worn and securely in place, with no gaps where particles can escape.
What are the ISO guidelines for clean rooms?
The ISO (International Organization for Standardization) provides comprehensive guidelines for cleanrooms and controlled environments through the ISO 14644 series. The primary standard in this series is ISO 14644-1, which establishes the classification of air cleanliness by particle concentration.
What is the difference between iso6 and iso7?
The main difference between ISO Class 6 and ISO Class 7 cleanrooms is the allowable concentration of airborne particles, with ISO Class 6 being significantly cleaner. This difference impacts various aspects of cleanroom design, operation, and usage, including air filtration, HVAC requirements, gowning protocols, and application suitability.
An ISO 7 cleanroom is a controlled environment classified under the ISO 14644-1 standard, which specifies the maximum allowable concentration of airborne particles per cubic meter. This classification defines the cleanliness level of the air within the cleanroom and is used in various industries to ensure that processes sensitive to contamination are carried out under stringent conditions.
What is an ISO-6 Cleanroom Classification?
ISO-6 cleanrooms are clean environments classified according to ISO 14644-1, where the concentration of particles in the air must be below specified limits. Specifically, the number of particles allowed per cubic meter of air is: no more than 35,200 particles greater than or equal to 0.5 microns, and no more than 8,320 particles greater than or equal to 1.0 microns. ISO-6 cleanrooms are often used in industries that require high air cleanliness, such as semiconductor manufacturing, biotechnology, and pharmaceutical fields.
ISO 6 Cleanroom Standards and Applications
An ISO 6 cleanroom, as defined by the ISO 14644-1 standard, is a controlled environment where the concentration of airborne particles is strictly regulated, allowing no more than 35,200 particles per cubic meter for particles ≥0.5 microns and no more than 8,320 particles per cubic meter for particles ≥1.0 microns. These cleanrooms are essential for industries requiring high levels of air cleanliness, such as semiconductor manufacturing, biotechnology, and pharmaceuticals, to ensure product quality and prevent contamination. The stringent standards necessitate advanced filtration systems, frequent air changes, and strict operational protocols, including specialized gowning and cleaning procedures.
What are the requirements for lSO Class 6 cleanroom?
An ISO Class 6 cleanroom, as per ISO 14644-1 standards, must maintain a controlled environment with strict limits on airborne particle concentrations, specifically allowing no more than 35,200 particles per cubic meter for particles ≥0.5 microns and no more than 8,320 particles per cubic meter for particles ≥1.0 microns. To meet these requirements, the cleanroom must implement advanced HEPA or ULPA filtration systems, maintain high air change rates typically around 150-240 air changes per hour, and follow stringent operational protocols. These protocols include rigorous gowning procedures, regular and thorough cleaning routines, and strict behavioral guidelines for personnel to minimize contamination risks.
What are the requirements for lSO 6 cleanroom gowning?
Gowning requirements for an ISO 6 cleanroom are stringent to ensure minimal contamination from personnel. Individuals must wear full-body coveralls, including hoods, face masks, gloves, and shoe covers made of low-shedding materials to prevent particles from entering the cleanroom environment. The gowning process typically includes a specific sequence to don the attire, starting with hand washing and application of gloves, followed by putting on the coverall, hood, mask, and finally the shoe covers, often in a designated gowning area to maintain cleanliness. These procedures are designed to minimize the introduction of contaminants from skin, hair, and personal clothing, thereby maintaining the strict particle limits required for an ISO 6 cleanroom.
ISO Class 6 Cleanroom Design and Build
Designing and building an ISO Class 6 cleanroom involves creating a controlled environment with strict limits on airborne particle concentrations, requiring advanced engineering and construction practices. The cleanroom must be equipped with HEPA or ULPA filtration systems to achieve high air purity, maintaining no more than 35,200 particles per cubic meter for particles ≥0.5 microns. The design includes high air change rates, typically 150-240 air changes per hour, to continuously remove contaminants. Surfaces and materials used in construction are smooth, non-shedding, and easy to clean. The layout includes airlocks and gowning areas to control personnel entry and prevent contamination. Additionally, the cleanroom is maintained under positive pressure to prevent the ingress of contaminants from adjacent areas, ensuring a consistently clean environment suitable for sensitive operations in industries like pharmaceuticals, biotechnology, and semiconductor manufacturing.