Constructing an ISO Class 6 Cleanroom involves meticulous planning and execution to achieve the desired level of cleanliness. This guide explores critical aspects of designing and building an ISO 6 Cleanroom, focusing on layout planning, material selection, airflow, and environmental controls.
Key iso class 6 Requirements
Particle Specifications
An ISO 6 Cleanroom must have fewer than 35,200 particles (0.5 micrometers or larger) per cubic meter of air.
air changes: 150 to 240 per hour
HEPA Filtration
HEPA filters capture 99.99% of particles as small as 0.3 micrometers. Essential for maintaining ISO 6 air purity standards.
Critical Integration: HVAC system optimization
Design Considerations
Layout Planning
- Functional Spaces: Allocate sufficient space for operations with proper separation
- Flow Design: Design pathways for personnel and materials to maintain cleanliness
- Contamination Control: Well-thought-out layout reduces contamination risk
Airflow Patterns
Airflow should transport particulates away from critical areas toward exhaust points using:
- Unidirectional airflow patterns
- Turbulent airflow patterns
Material Selection
Choosing appropriate materials is vital to prevent particle shedding:
- Non-shedding surfaces
- Easy-to-clean materials
- Static-dissipative properties
Environmental Parameters
Careful control of environmental factors:
- Temperature and humidity
- Lighting levels and noise standards
- Static electricity control
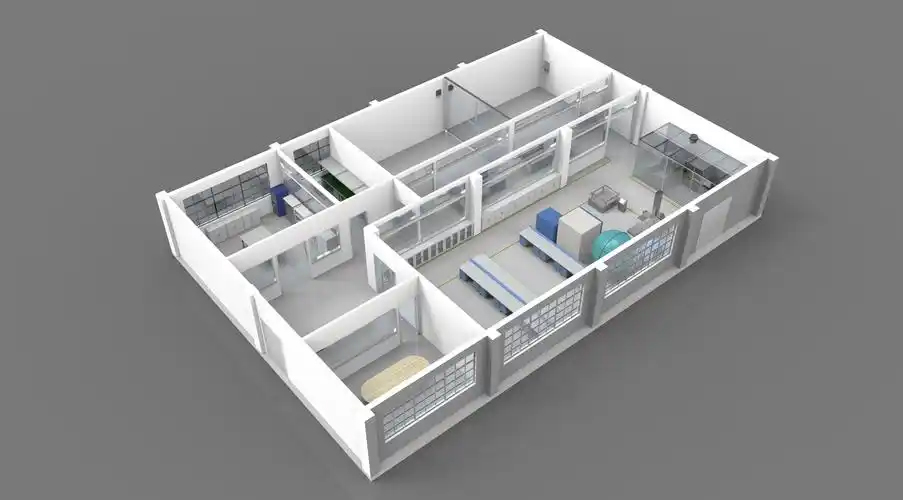
Modern ISO Class 6 Cleanroom design example
Construction & Validation
construction process
- Site Preparation: Level site and connect utilities
- Component Installation: Walls, ceilings, and floors
- HVAC Setup: Install air handlers, filters, and ductwork
Validation Testing
Comprehensive tests to validate Cleanroom performance:
- Particle count verification
- Airflow velocity and uniformity
- Filter integrity testing
Common Questions & Answers
What is the importance of air changes per hour in A CleanRoom?
It ensures continuous contaminant removal, maintaining the required level of cleanliness.
How do HEPA filters contribute to cleanroom performance?
They capture 99.99% of airborne particles as small as 0.3 micrometers, essential for air purity.
Why is material selection critical in cleanroom construction?
To prevent particle shedding and ensure ease of cleaning, maintaining compliance and durability.
References
- International Organization for Standardization. ISO 14644-1: Cleanrooms and Associated Controlled Environments — Part 1: Classification of Air Cleanliness by Particle Concentration.
- International Organization for Standardization. iso 14644-2: Cleanrooms and Associated Controlled Environments — Part 2: monitoring to Provide Evidence of Cleanroom Performance Related to Air Cleanliness by Particle Concentration.
- International Organization for Standardization. ISO 14644-3: Cleanrooms and Associated Controlled Environments — Part 3: Test Methods.
- Deiiang™, Innovative Cleanroom Solutions and Design Practices.
- The Institute of Environmental Sciences and Technology (IEST). IEST-RP-CC001: HEPA and ULPA Filters.
- ASHRAE Handbook. HVAC Applications: Clean Spaces Guidelines.
- U.S. Pharmacopeial Convention. USP General Chapter <797> Pharmaceutical Compounding — Sterile Preparations.
ISO Class 6 Cleanroom Design Guide | Comprehensive Resource for Controlled Environment Construction
© 2023 Cleanroom design Standards. All rights reserved.