What is BS EN ISO 14644 ISO 8?
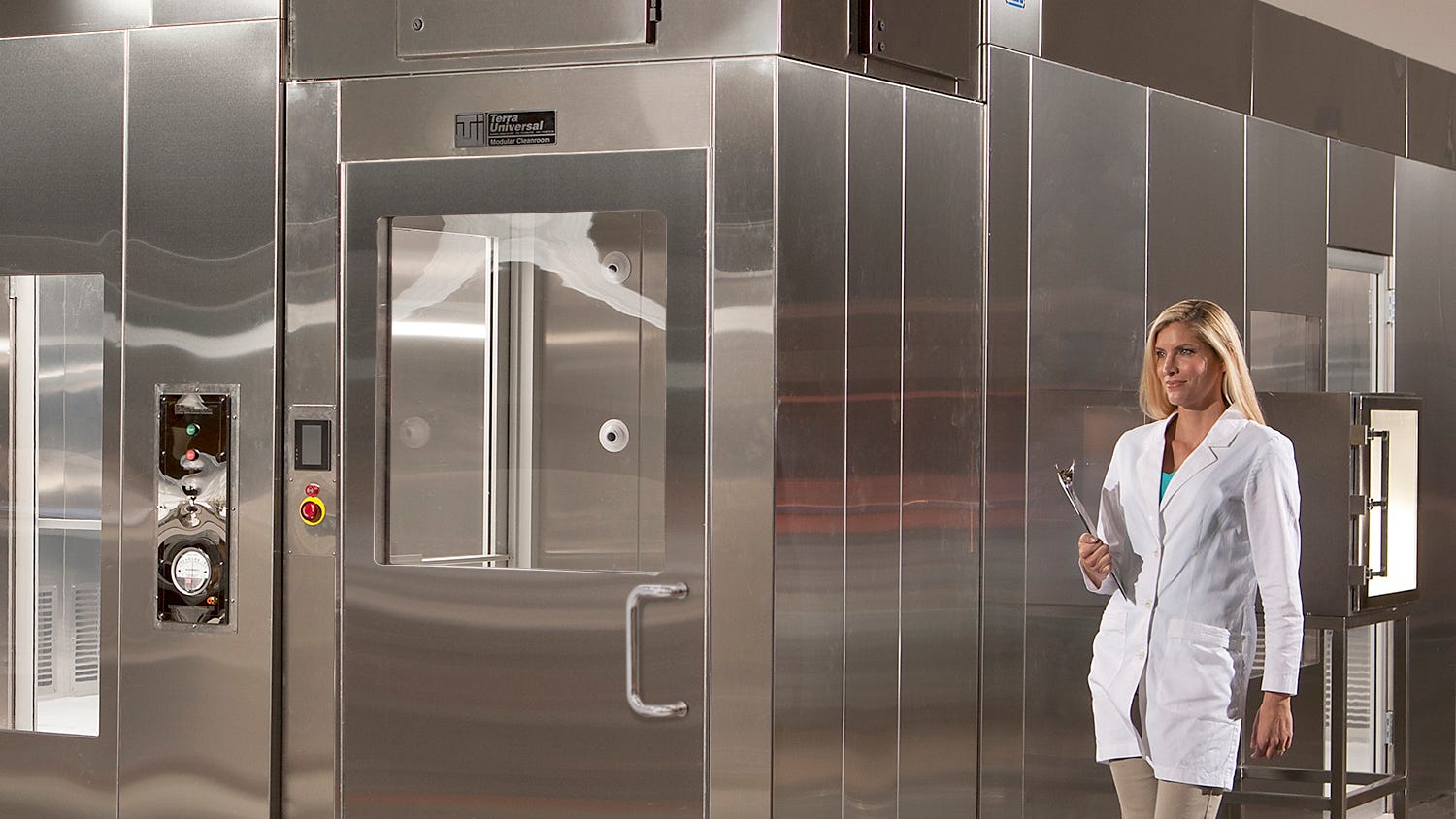
BS EN ISO 14644 ISO 8 refers to a classification of cleanrooms based on the iso 14644-1 standards, which define the cleanliness levels in terms of the concentration of airborne particles. ISO 8 is one of the less stringent classifications in this system, and it is suitable for environments where contamination control is important but not as critical as higher classes such as ISO 7 or ISO 6. Cleanrooms are classified based on the maximum allowable particle count per cubic meter of air, specifically for particles that are 0.5 microns or larger.
In a ISO 8 Cleanroom, the permissible particle count is higher than in ISO 7 or ISO 6 environments, but it still ensures that contamination is kept at acceptable levels for less sensitive processes. This level of cleanliness is ideal for industries where particle contamination can have an impact on product quality, but the processes involved are less sensitive to small variations in cleanliness than industries such as Semiconductor manufacturing or pharmaceuticals.
1. Particle Limits in ISO 8 Cleanrooms
For a BS EN ISO 14644 ISO 8 cleanroom, the maximum allowable concentration of particles ≥0.5 microns in the air is 3,520,000 particles per cubic meter. This limit is significantly higher than stricter CleanRoom Classifications like ISO 7, which allow fewer particles. The focus is still on maintaining a relatively clean environment, but the application does not require the extreme particle control found in higher classes.
2. Applications of ISO 8 Cleanrooms
ISO 8 cleanrooms are commonly used in industries where contamination risks are moderate but not critical. Typical applications include:
Electronics assembly: In processes where minor particle contamination could affect the quality of products like circuit boards or components.
Non-sterile pharmaceutical production: ISO 8 cleanrooms are appropriate for handling non-sterile pharmaceuticals or for packaging processes where particulate matter can be controlled but does not require a sterile environment.
Food packaging: Although ISO 8 cleanrooms are not as stringent as those used in pharmaceutical or biotechnology industries, they are still ideal for food packaging, where airborne particles need to be controlled to prevent contamination.
3. Airflow and Filtration
Like all cleanrooms, ISO 8 environments use high-efficiency particulate air (HEPA) filters to control airborne particles. The room must also have a defined air change rate (typically between 20 to 60 air changes per hour), ensuring that the air is circulated and filtered frequently to remove any contaminants. The overall airflow design minimizes particle accumulation and keeps the room as clean as possible given the parameters of Class 8.
4. Cost and Complexity
ISO 8 cleanrooms are generally more cost-effective compared to ISO 7 and ISO 6 Cleanrooms, as they require less stringent environmental control and fewer air changes per hour. They are easier to maintain and offer a good balance between cleanliness and cost for applications that do not require the highest levels of contamination control.
What is ISO 14644-1 ISO 8 Standards?
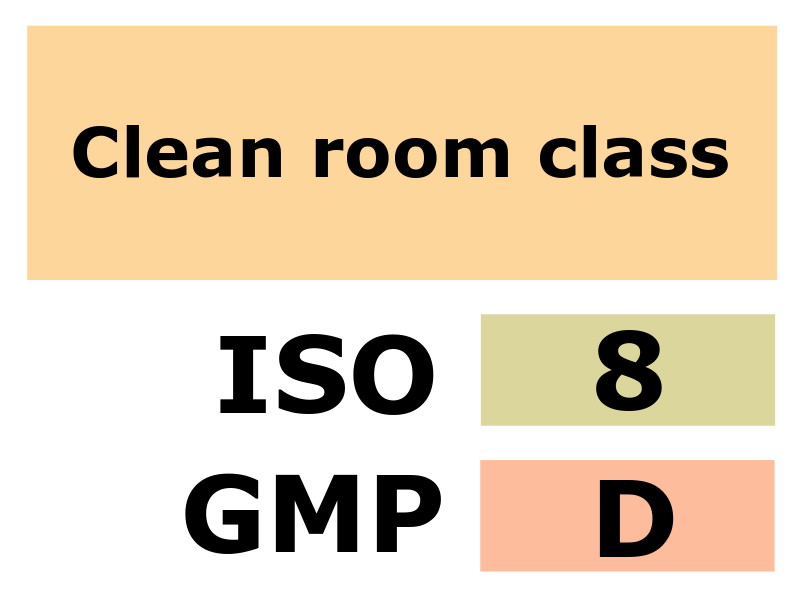
ISO 14644-1 ISO 8 standards define the permissible particle concentration in a cleanroom and specify the cleanliness requirements for different classes of cleanrooms, including ISO 8. The main criterion for this classification is the maximum allowable number of particles of ≥0.5 microns per cubic meter of air. For ISO 8, the standard allows up to 3,520,000 particles per cubic meter.
In addition to particle control, the standards also specify airflow rates, air filtration efficiency, and temperature and humidity control to maintain a stable cleanroom environment. Personnel working in ISO 8 cleanrooms must adhere to gowning requirements, including coveralls, gloves, and hair covers, to minimize contamination from human sources.
The standards also require cleanroom operators to perform regular monitoring and testing to ensure that the room continues to meet the required cleanliness levels. These guidelines are crucial for industries like electronics manufacturing, non-sterile pharmaceuticals, and food processing, where particle contamination could affect product quality but is not as critical as in more sensitive environments.
Which ISO is the Cleanest?
The cleanest ISO class is ISO1, which is the most stringent classification for cleanrooms. This class allows fewer than 10 particles of ≥0.5 microns per cubic meter of air, making it suitable for environments where even the smallest contaminants could pose a risk, such as in semiconductor fabrication, biotechnology research, and pharmaceutical manufacturing.
Below is a comparison of the cleanliness levels in different ISO classes:
What is a ISO 8 Dust Level?
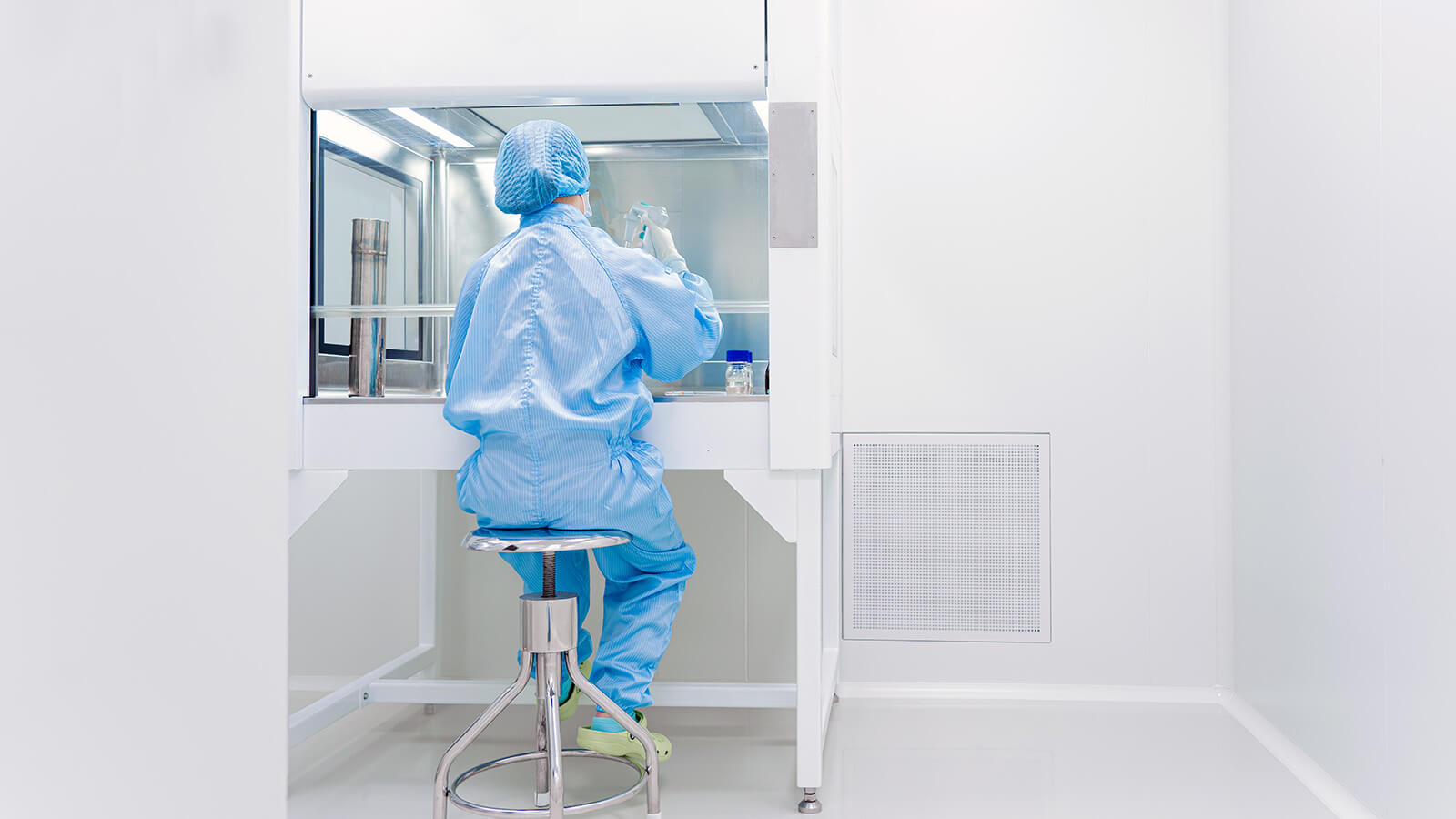
In the context of cleanrooms, ISO 8 dust level refers to the maximum allowable number of particles ≥ 0.5 microns in a cubic meter of air. Specifically, for ISO 8 cleanrooms, the dust level is capped at 3,520,000 particles per cubic meter. This dust level is indicative of the acceptable cleanliness standard for environments where moderate contamination control is needed.
1. Dust Control in ISO 8 Cleanrooms: To manage dust levels in a ISO 8 cleanroom, various strategies are employed, including air filtration, air circulation, and gowning procedures. HEPA filters are the standard for capturing particles from the air, ensuring that dust particles are minimized. Additionally, positive pressure airflow within the cleanroom helps to prevent contaminants from entering the room from the outside.
2. Airflow and Filtration: ISO 8 cleanrooms require an air change rate of 20 to 60 air changes per hour (ACH). This frequent air exchange helps dilute the concentration of airborne dust and ensures that contaminants are efficiently removed from the environment. The HEPA filters used in these cleanrooms are effective at trapping particles down to 0.3 microns, ensuring that dust and other particles are kept at acceptable levels.
3. Maintenance of Dust Levels: Maintaining the required dust level in a ISO 8 cleanroom involves regular monitoring of particle concentration and continuous calibration of filtration systems. Routine cleaning procedures are also crucial, as even small amounts of dust can accumulate over time, affecting both the cleanliness of the room and the quality of the products being manufactured.
What is iso 14644-8 Classification of Airborne Molecular Contamination?
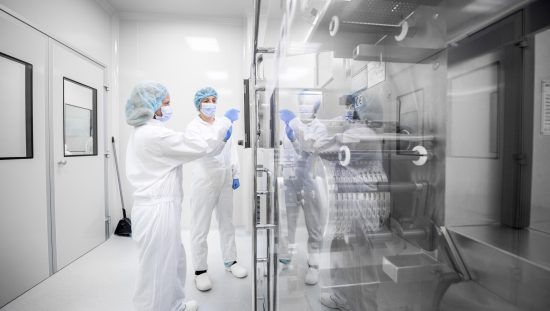
ISO 14644-8 addresses the classification of airborne molecular contamination (AMC), which includes gases, vapors, and other molecular substances that can affect the performance of sensitive products or processes in cleanrooms. AMC can come from various sources, including cleaning agents, outgassing from materials, or even human activities.
AMC in ISO 8 Cleanrooms: While ISO 8 cleanrooms are primarily concerned with controlling particulate contamination, airborne molecular contamination also needs to be monitored and managed. These contaminants can affect sensitive processes, especially in industries like semiconductor manufacturing or pharmaceutical production.
Monitoring and Control of AMC: ISO 14644-8 outlines methods for measuring and controlling airborne molecular contamination. This includes using specific sensors to monitor gases such as ammonia, ozone, and formaldehyde, which can be harmful to sensitive manufacturing processes. Proper ventilation, filtration, and material selection are critical to minimizing AMC in ISO 8 cleanrooms.
Applications of AMC Control: In ISO 8 cleanrooms, AMC control is particularly relevant in industries where molecular contaminants can damage delicate products or processes. Regular air quality testing, careful material selection, and monitoring of the environment are essential to maintaining the cleanliness and integrity of the manufacturing process.