Understanding the Particle Limits for ISO 8 Cleanrooms
Understanding the particle limits for ISO 8 cleanrooms is crucial for anyone involved in industries requiring controlled environments. These cleanrooms support processes that do not need ultra-stringent controls yet must maintain a baseline for cleanliness to ensure product integrity. In this article, we explore what particles mean in the context of cleanrooms, outline the particle concentration limits for ISO 8, and detail the equipment and strategies for monitoring and maintaining these standards.
What Are dust particles?
Dust particles are tiny pieces of matter that can originate from various sources, including skin flakes, soil, pollen, and industrial residues. In A CleanRoom environment, these particles become critical contaminants that can compromise the quality of sensitive processes and products.
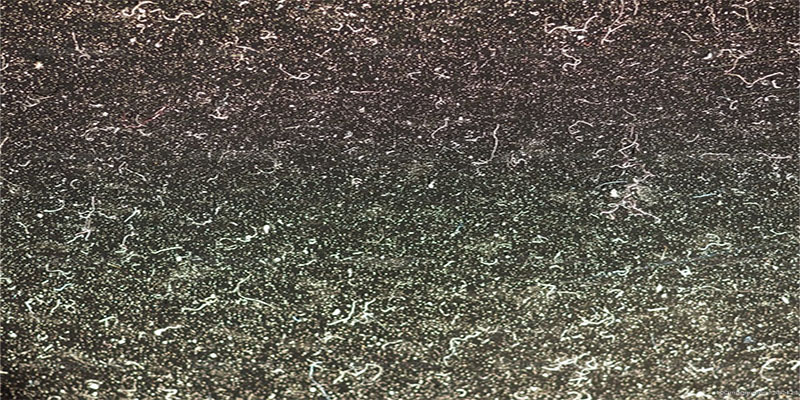
Microscope view of dust particles that can contaminate cleanroom environments
ISO 8 Cleanroom Particle Count
An ISO 8 cleanroom allows a maximum particulate concentration of 3,520,000 particles per cubic meter for particles 0.5 µm and larger. This is based on the international standard ISO 14644-1, which classifies cleanrooms by particle density.
Cleanroom Class | Particle Size (µm) | Maximum Concentration (particles/m³) |
---|---|---|
ISO 8 | ≥0.5 | 3,520,000 |
How to Detect Particle Counts
Detecting particle counts involves sophisticated particle counters that utilize laser-based technology to determine the concentration and size of airborne particles. This technology is crucial for maintaining the environment within the defined ISO class limits.
Key Concepts
To effectively navigate particle counting, it's vital to understand several key concepts.
Instrument Sample Volume refers to the quantity of fluid examined for particles in a given timeframe.
Instrument Flow Rate is the amount of fluid passing through the counting device in that same period.
The Sample Volume Percentage, then, is a straightforward calculation: it’s the sample volume divided by the flow rate, expressed as a percentage. This measure helps evaluate how much of the total flow is actually being analyzed.
Understanding Particle Counters: Exploring Counting Efficiency and Comparisons
Particle counting technology is indispensable across many industries. For example, in Semiconductor manufacturing, maintaining pristine fluid systems is essential for product quality. While particle counting is critical, the methods used can differ significantly and sometimes cause confusion. By focusing on these core definitions and understanding their implications, users can better comprehend the functionality and efficiency of various particle counting systems. At Deiiang, we help demystify these technologies, ensuring our clients use the most effective methods for their specific needs.
Instruments for Monitoring Particle Counts
- Laser particle counters - measure the number and size of particles in the air
- Optical counters - provide additional capabilities for heavier particle loads
- Condensation particle counters - designed for smaller particle detection
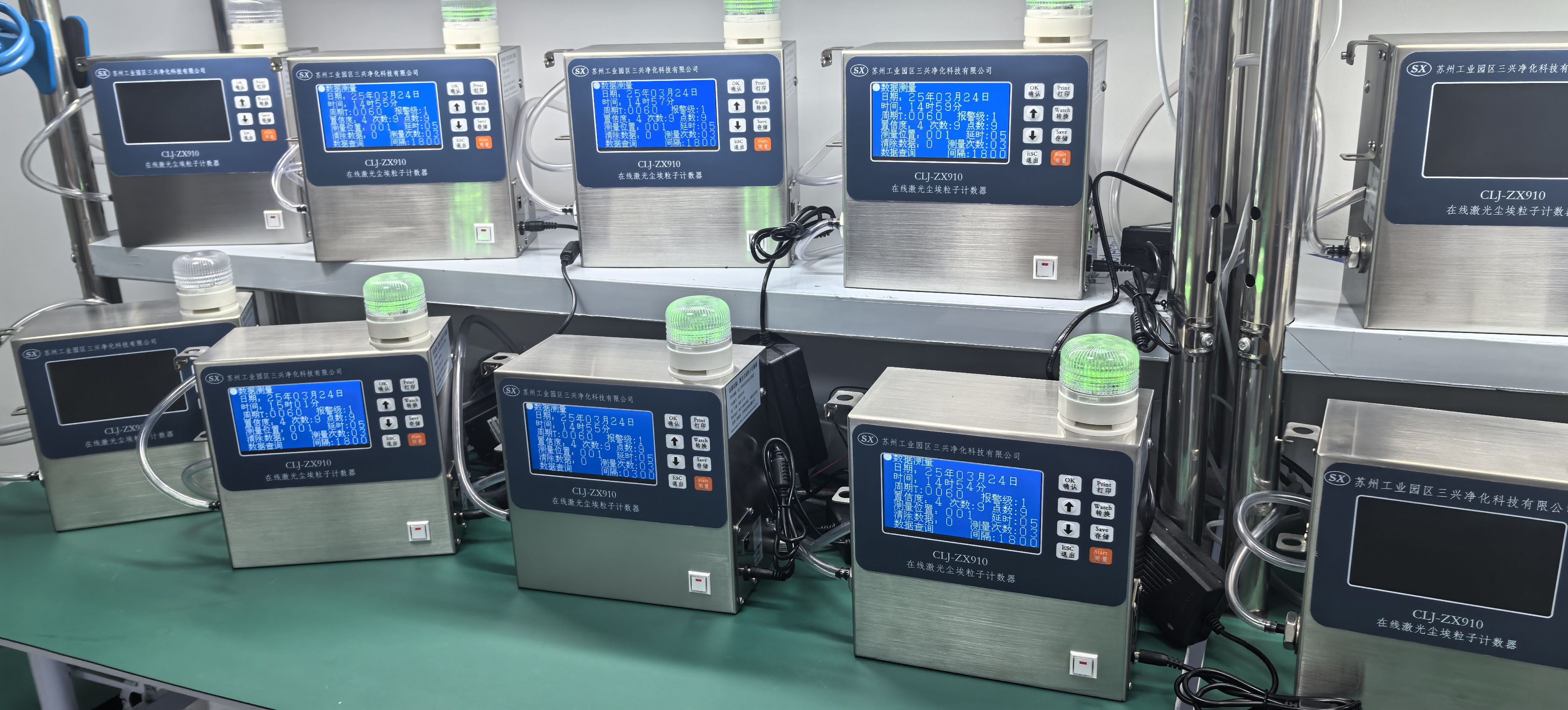
Laser particle counter used for monitoring cleanroom environments
The Impact of 0.5µm Particle Counts on CleanRoom Classification
Particles measuring 0.5 µm are significant in cleanroom classifications because of their potential to interfere with intricate processes. Even at the ISO 8 level, where more leeway is allowed compared to classes like ISO 6, maintaining low levels of these particles is critical to prevent contamination of products.
ISO Standard for Particle Counting
iso 14644-1 provides the framework for classifying cleanrooms by air cleanliness levels determined by particle concentration. These standards dictate the measurement protocols and the thresholds for each cleanroom class, ensuring that cleanrooms around the world maintain comparable levels of air purity.
How to Control Particle Counts in an ISO 8 Cleanroom
Controlling particle counts involves a comprehensive strategy that includes air filtration, proper gowning procedures, and regular Environmental monitoring. HEPA or ULPA filters are integrated into the HVAC systems to capture and eliminate airborne particles effectively.
Key Control Strategies:
- High-efficiency air filtration systems (HEPA/ULPA)
- Strict gowning and personnel hygiene protocols
- Regular environmental monitoring and particle counting
- Controlled access and movement within the cleanroom
- Periodic equipment and facility maintenance
Conclusion
Maintaining particle limits in an ISO 8 cleanroom is an attainable goal with proper equipment, systematic monitoring, and the implementation of international standards. Through innovative design, expert planning, and advanced technology, businesses can ensure their cleanroom environments meet or exceed required cleanliness levels, safeguarding both processes and products.
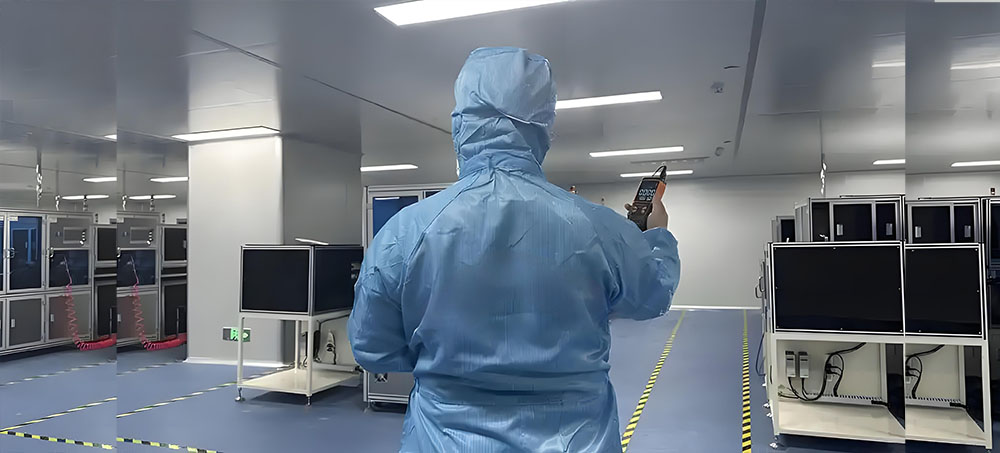
Well-maintained ISO 8 cleanroom environment