Requirements for ISO 14644-1 Class 8 Cleanrooms
Ensuring Optimal Standards
An iso 14644-1 Class 8 cleanroom, also referred to as a Class 100,000 cleanroom, is designed to maintain certain cleanliness levels for various industrial applications. These cleanrooms are commonly used in sectors requiring moderate environmental control, such as pharmaceuticals and Electronics.
Key Features of ISO 8 Cleanrooms
- Moderate environmental control
- Suitable for pharmaceuticals and electronics
- Cost-effective solution for many industries
- Flexible design options
Particle Count Specifications
The most defining characteristic of an ISO 8 cleanroom is its particle count limit. According to ISO 14644-1, these cleanrooms allow up to 3,520,000 particles (0.5 micrometers or larger) per cubic meter of air.
Particle Size (micrometers) | Maximum Particles per m³ |
---|---|
≥ 0.5 | 3,520,000 |
≥ 1 | 832,000 |
≥ 5 | 29,300 |
Equivalent Standards: This classification is equivalent to the former Federal Standard 209E Class 100,000, ensuring compatibility with legacy systems across industries.
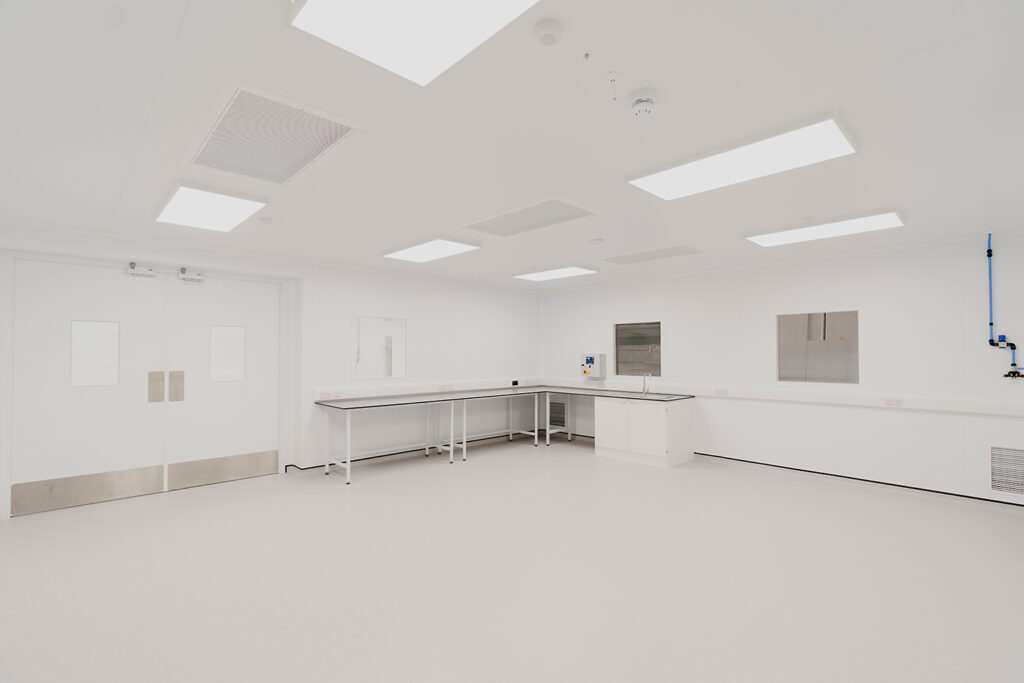
Example of an ISO Class 8 Cleanroom environment
Air Changes per Hour
Air change rate is critical for maintaining cleanliness by ensuring that contaminants are regularly flushed out of the environment. Although the ISO standard does not specify an exact number, it is generally recommended that ISO 8 cleanrooms perform between 10-25 air changes per hour.
Optimal Air Flow: Continuous air exchange helps maintain particle counts within specified limits, ensuring stable environmental conditions.
Airflow Specifications
ISO 8 cleanrooms do not require unidirectional (laminar) airflow, unlike higher-class cleanrooms. Non-unidirectional flow is often sufficient in maintaining the desired cleanliness level without the complexity of laminar systems.
HEPA Filtration
While not explicitly required by ISO 8, the use of HEPA filters is a common practice to achieve necessary cleanliness levels. HEPA filters can capture 99.97% of particles 0.3 micrometers or larger, greatly contributing to air purity.
Example Application
In applications like workspace environments for electronics or pharmaceuticals, HEPA filtration integrated into Deiiang™ systems ensures high air quality among sensitive processes.
Additional Environmental Controls
In addition to particle control, other factors such as temperature, humidity, and static electricity may be regulated depending on specific CleanRoom applications.
Environmental Stability: Proper control of these factors prevents conditions that could compromise product integrity, such as condensation or electrostatic discharge.
Conclusion
Establishing an ISO 8 cleanroom involves implementing specific particle control, air change rates, and filtration methods to maintain standards essential for various industries. By adopting advanced cleanroom technologies from Deiiang™, with the guidance of Deiiang Jason.peng, facilities can achieve optimal performance and maintain compliance with international standards.
Common Questions and Answers
Q: What is the particle count limit for an ISO 8 cleanroom?
A: The limit is up to 3,520,000 particles (0.5 micrometers and larger) per cubic meter of air.
Q: How are air changes managed in an ISO 8 cleanroom?
A: Typically, the environment should have 10-25 air changes per hour to ensure proper air quality.
Q: Is HEPA filtration required in ISO 8 cleanrooms?
A: While not explicitly required, HEPA filters are commonly used to maintain cleanliness standards.
Q: What is the significance of air change rates?
A: Higher air change rates help remove contaminants continuously, maintaining a clean environment.
Q: What additional factors should be managed in an ISO 8 cleanroom?
A: Temperature, humidity, and static electricity controls are crucial for specialized applications.
References
- International Organization for Standardization. ISO 14644-1: Cleanrooms and Associated Controlled Environments.
- Deiiang™, Innovative Cleanroom design Solutions.
- American Society of Heating, Refrigerating and Air-Conditioning Engineers (ASHRAE), Standards for Cleanroom Ventilation.
- U.S. Pharmacopeial Convention. USP Standards for Environmental Control.
- The Institute of Environmental Sciences and Technology (IEST), Cleanroom Guidelines and Practices.
Aligning with these requirements ensures that ISO 8 cleanrooms effectively support industries with strict environmental control needs, facilitating both product safety and operational efficiency.