Designing an air shower room requires careful consideration of multiple factors that influence its size and functionality. This process is crucial for ensuring that the air shower effectively eliminates contaminants from personnel and equipment entering cleanrooms.
How to Design the Size of an Air Shower Room?
Personnel and Equipment Accommodation
Determine whether the air shower will accommodate just personnel or also include carts, pallets, or large equipment. A standard for personnel might have a width of 3 feet, but with equipment, the requirement might increase to 4 or 5 feet.
Throughput and Flow Rate
Consider the number of individuals or items needing to pass through in a given timeframe. For high throughput environments, a tunnel system can accommodate more users simultaneously, increasing efficiency and reducing wait times.
Height Restrictions
For facilities with lower ceilings (typically below 96 inches), opt for a low-profile air shower. These models are designed to fit into constrained vertical spaces without compromising efficiency.
On-Site Space Constraints
Consider not just the air shower's footprint, but also the ease of integration into existing layouts. Modular design approaches ensure air showers are adaptable to specific spatial constraints.
Door Configuration
Options include single doors, double doors, sliding doors, and roll-up doors, usually with interlocking mechanisms. The setup depends on your facility's layout and clean process flow.
The Purpose of the Air Shower
- .Minimize contamination risk: High-velocity air jets dislodge particles from clothing and equipment.
- .Protect sensitive environments: Acts as a critical barrier preventing contaminants from entering sterile areas.
- .Ensure compliance with Cleanroom standards: Maintains the integrity of cleanroom protocols and regulations.
What are Clean Rooms Used for?
Clean rooms are primarily used in industries such as pharmaceuticals, biotechnology, and aerospace to control contamination levels. These controlled environments ensure that airborne particles, temperature, humidity, and pressure are strictly regulated.
Industry | Application |
---|---|
Semiconductor Fabrication | Even minute contaminants can impact product quality |
Pharmaceuticals | Sterile drug preparation and medical device manufacture |
Biotechnology | Research and production of biological products |
Aerospace | Manufacture of components requiring high cleanliness |
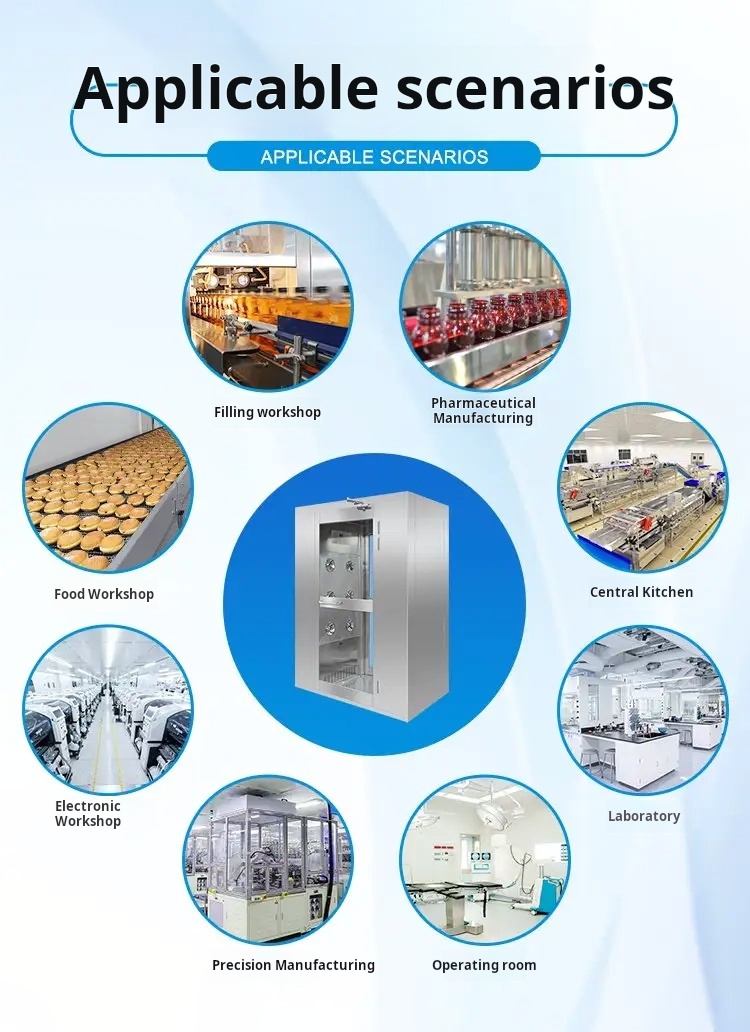
A typical Clean room environment in a pharmaceutical facility
The Cycle Time for an Air Shower
Importance of Cycle Time
The cycle time is critical to ensure that sufficient air changes occur to remove contaminants effectively. Typically, a cycle lasts between 30 seconds to 2 minutes, depending on the design and airflow specifications.
Factors Affecting Cycle Time
- air velocity of the shower jets: Higher velocities lead to quicker decontamination.
- Number of air changes per hour: An optimal range of 20-30 changes ensures thorough cleaning.
- Cleanroom requirements: Different environments have varying contamination control standards.
Best Practices for Cycle Management
Monitor and manage cycle times effectively through regular maintenance of the air shower system, including checking the functionality of air jets and filters. Train personnel on correct usage to minimize delays and ensure compliance.
Deiiang Company Case Introduction
Deiiang Company has established itself as a leader in cleanroom technology solutions. With a commitment to innovation and quality, the company offers tailored air shower designs that meet the specific needs of various industries.
Key Features of Deiiang Solutions
Adaptable designs for various spatial constraints
Compliance with international standards (ISO, GMP, FDA)
Expert design guidance from Jason.peng
Modular systems for easy integration
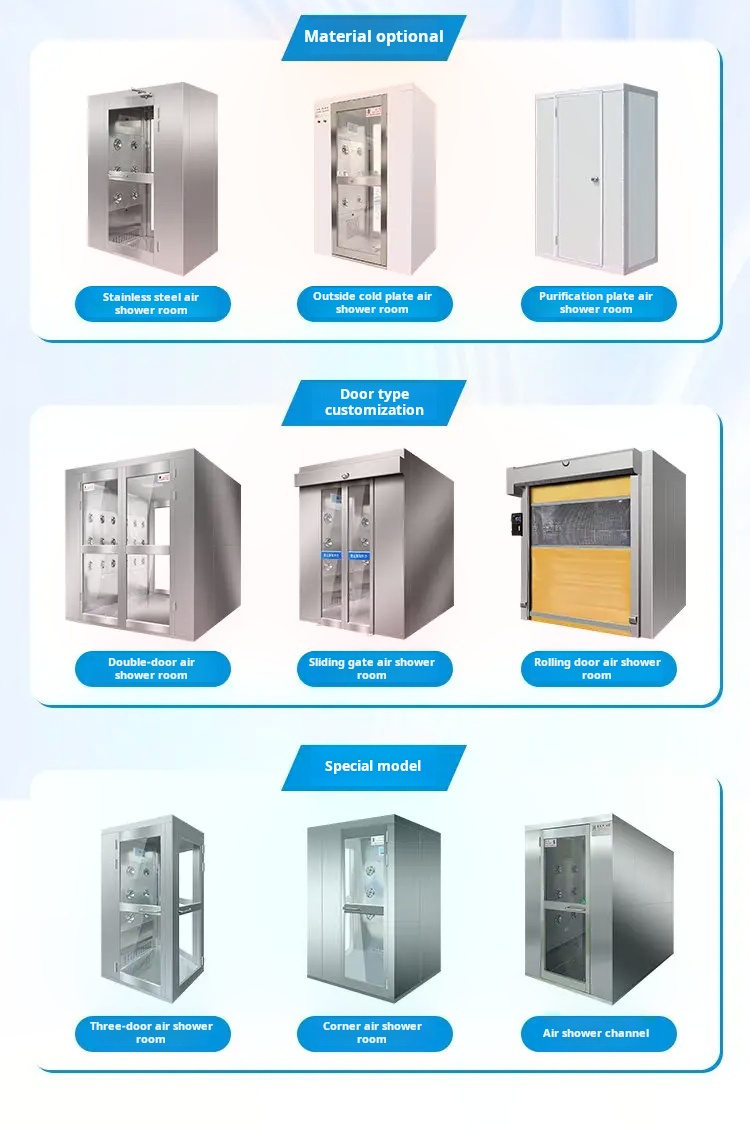
A custom air shower design by Deiiang™
Common Questions and Solutions
What should I consider if integrating an air shower into an existing facility?
Evaluate spatial constraints and potential bottlenecks in current workflows to determine the most effective placement and configuration of the air shower.
How can I ensure the air shower meets international standards?
Engage with certified designers and suppliers like Deiiang™, who have experience with international cleanroom standards and regulations, to ensure compliance.
What are the key standards for air shower design?
Relevant standards include ISO 14644-1, FDA Guidelines for Clean Rooms, and GMP Standards.
Conclusion: Customizing Air Shower Design for Optimal Performance
The design of an air shower room must balance multiple factors to meet operational needs while ensuring cleanliness and efficiency. By considering dimensions for personnel and equipment, throughput requirements, space constraints, and door configurations, you can tailor the air shower to fit seamlessly into your facility.
Solutions from Deiiang™, under the expert guidance of designer Jason.peng, deliver adaptable and robust air shower designs suited to various industrial applications, ensuring the highest standards of hygiene and safety.
© 2025 Air Shower Design Resources. All rights reserved.
Designed for optimal Cleanroom performance and compliance