Air Shower Technology
Critical Components for Maintaining Cleanroom Integrity
Air showers are critical components in cleanroom technology, designed to eliminate particulate contamination from personnel and materials before entering controlled environments. The choice of shell material significantly impacts an air shower's effectiveness, durability, and maintenance. Understanding the various materials used for air shower construction is essential for selecting the right solution for specific CleanRoom applications.
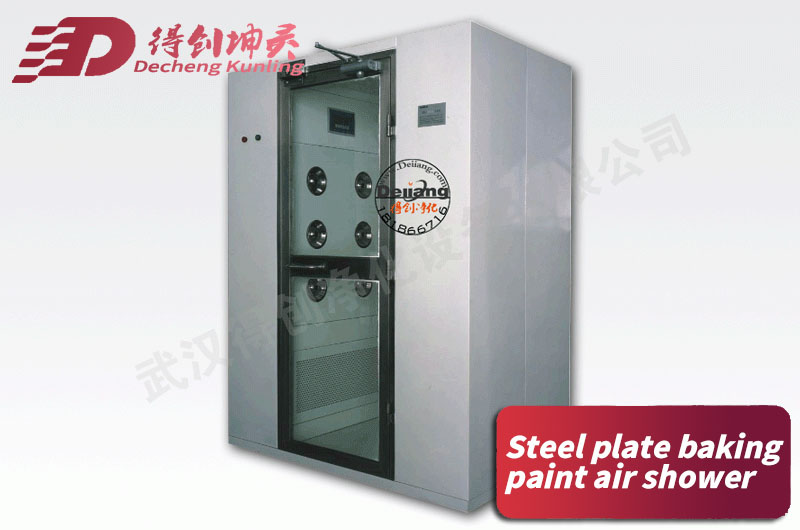
Air Shower Shell Materials
The shell of an air shower is typically constructed from various materials, each offering specific benefits in terms of hygiene, durability, and ease of maintenance. Common materials include stainless steel, painted mild steel, and color-coated steel panels, each suited for different operational environments.
Stainless Steel
Stainless steel is the preferred choice for air shower shells due to its outstanding corrosion resistance and ease of cleaning. Its non-porous surface minimizes bacterial growth, making it ideal for high-hygiene environments such as pharmaceuticals and biotechnology.
Painted Mild Steel
Painted mild steel is an economical alternative that provides adequate structural integrity. The painted finish enhances durability and resistance to wear, making it suitable for less critical environments where cost considerations are essential.
Color-Coated Steel Panels
Color-coated steel panels combine aesthetics with functionality. They offer a balance of corrosion resistance and cost-effectiveness, ideal for facilities that require a visually appealing design without compromising on performance.
Air Shower Specifications
Dimensions
The design can range from single-person units to larger configurations for multiple users.
Airflow Rate
Effective air showers typically achieve airflow rates of 20 m/s or higher to ensure thorough decontamination.
Filtration
High-efficiency particulate air (hepa) filters are standard to capture contaminants effectively.
high-efficiency filtration System
Purpose
High-efficiency filtration systems ensure that airborne particles are effectively removed from the air.
Components
Most air showers utilize hepa filters that can trap 99.97% of particles that are 0.3 microns in diameter, significantly enhancing air cleanliness.
Maintenance
Regular inspection and replacement of filters are crucial for maintaining optimal air quality.
Regulations
Compliance with international standards like ISO 14644 ensures that air showers meet stringent cleanliness requirements.
The Significance of Air Showers
Importance in Cleanrooms
Air showers serve as a transitional barrier, preventing contaminants from entering controlled environments. By providing a high-velocity airflow that dislodges particles from clothing and skin, they significantly reduce the risk of contamination. This is essential in industries such as pharmaceuticals, Electronics, and aerospace, where even minute particles can compromise product quality.
Operational Efficiency
Implementing air showers enhances operational efficiency by streamlining the decontamination process. With a user-friendly interface, personnel can quickly prepare for entry without extensive gowning procedures. Regular use of air showers can lead to a measurable decrease in contamination incidents, thereby increasing productivity and reducing waste.
Health and Safety
By improving air quality and reducing the risk of contamination, air showers contribute to a safer working environment. This is particularly important in sensitive industries, ensuring compliance with health and safety regulations.
Maintaining Air Showers
Routine Cleaning
The shell and interior surfaces should be regularly cleaned with appropriate disinfectants to prevent contamination buildup.
Filter Replacement
HEPA filters must be inspected and replaced according to the manufacturer's guidelines to ensure efficient operation.
Performance Checks
Regular performance checks, including airflow velocity and system functionality, are vital to ensure compliance with industry standards.
Relevant Standards
Following domestic and international standards, such as ISO 14644 for cleanrooms, ensures that air showers operate effectively and maintain the required cleanliness levels.
Air Shower Technology - Cleanroom Essential
© 2025 cleanroom Equipment Solutions. All rights reserved.