6 x 6M ISO 5 Modular Cleanroom
Reference Price:US$13500-20000
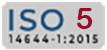


Cleanroom
6 x 6M ISO 5 Modular Cleanroom
Choose your installation & validation options below
Quantity:
Choose your Cleanroom frame structure material
Quantity:
Choose your Cleanroom Wall enclosure materials
Quantity:
Choose your Temperature requirements
Quantity:
Choose your humidity requirements
Quantity:
Choose your Explosion-proof requirements
Quantity:
Summary
6 x 6M ISO 5 Modular Cleanroom
Validation
Installation & Validation
Find Similar Products
-
5 x 10M ISO 5 Modular Cleanroom
US$20000-60000 USD/Set
Min. Order:1 Set -
6 x 6M ISO 5 Modular Cleanroom
US$20000-60000 USD/Set
Min. Order:1 Set -
6 x 8M ISO 5 Modular Cleanroom
US$20000-60000 USD/Set
Min. Order:1 Set -
6 x 10M ISO 5 Modular Cleanroom
US$20000-60000 USD/Set
Min. Order:1 Set -
5 x 6M ISO 5 Modular Cleanroom
US$20000-60000 USD/Set
Min. Order:1 Set -
5 x 7M ISO 5 Modular Cleanroom
US$20000-60000 USD/Set
Min. Order:1 Set
Cleanrooms Detail
An ISO 5 modular cleanroom is a controlled environment that meets stringent cleanliness standards as defined by the International Organization for Standardization (ISO). It is designed to maintain a maximum allowable particle concentration of no more than 3,520 particles per cubic meter for particles ≥0.5 micrometers in size.
Cleanroom Project Scope(from structure, HVAC,electric to autoc ontrol) | 1. Cleanroom Structure: Wall Panel, Ceiling Panel, Windows, Doors, Fttings, Flooring |
2. HVAC: AHU, Chiller, dehumidifier, Ducting, Piping, etc. | |
3. Electric: Lighting, Switch, Cables, Wires, Power Distribution Cabinet, etc | |
4. Auto- control: PLC Controller, Sensors for Humidity and Temperature, Control Panel | |
5. Process Piping System: Gas, Water Pipeline | |
Equipment | Air shower, Cargo shower, Mist shower, Dynamic pass box, Static pass box, Sampling booth,Weighing booth, Dispensing booth, |
Medicine stability test chamber, isolator, VHP sterilizer,Biological safety chamber, FFU, LAF, etc. | |
Temperature | 21-27*C (or as per required) |
Humidity | 30-60°C (or as per required) |
Application | Pharmaceutical factory, hospital, medical device factory, electronics factory, food factory,cosmetics factory, etc. |
Qualification Documents | CE GMP ISO |
Full Service | FAT and SAT Service, Professional Consultation, Training, 24 hours technical support |
an ISO 5 modular cleanroom is essential for processes that require strict control of airborne particulate contamination to ensure product integrity and compliance with industry standards.
Cleanrooms Airflow
The airflow principle in an ISO 5 modular cleanroom is critical for maintaining the required cleanliness levels and ensuring that the environment remains free from contamination. Here are the key aspects of the airflow principle in an ISO 5 cleanroom:
Cleanrooms Installation
Cleanrooms Testing
Cleanroom testing is a series of tests performed on the interior environment of a cleanroom to verify that it meets specific cleanliness requirements. These tests usually involve the measurement of a number of parameters such as air cleanliness, temperature and humidity, air velocity and air volume, noise, illumination, etc. inside the clean room. The purpose of the testing is to ensure that the clean room is able to provide a stable and contamination-free environment during the production process.
FAQ
What are the regulatory requirements for cleanrooms?
Regulatory requirements for cleanrooms typically include compliance with standards set by organizations like ISO, FDA, and cGMP. These standards ensure cleanliness and product safety.
Key components include regular monitoring of air quality, particle counts, and microbial limits. Documentation of procedures, training, and maintenance protocols is also essential.
What is the role of laminar flow in ISO 5 cleanrooms?
Laminar flow plays a crucial role in maintaining the cleanliness of ISO 5 cleanrooms. It ensures unidirectional airflow, which minimizes particle contamination.
This system effectively filters air, providing a sterile environment for sensitive processes. It helps to protect products and personnel from harmful contaminants.
What is the classification of ISO 5 cleanroom?
ISO 5 cleanrooms are classified based on their allowable particulate contamination levels. They permit a maximum of 3,520 particles per cubic meter for particles ≥0.5 micrometers.
This classification is crucial for industries like pharmaceuticals and semiconductor manufacturing, where contamination control is vital. The cleanroom must maintain specific environmental conditions to achieve this classification.
What are the common misconceptions about cleanrooms?
Common misconceptions about cleanrooms include the belief that they are completely sterile. In reality, cleanrooms control contamination rather than eliminate it entirely.
Another misconception is that cleanrooms are only for pharmaceutical applications. In fact, various industries, including electronics and aerospace, utilize cleanrooms extensively.
Many also underestimate the importance of personnel training in contamination control. Proper training ensures that employees understand protocols and maintain cleanliness standards effectively.
How to validate a modular cleanroom?
Validating a modular cleanroom involves a series of systematic procedures. First, conduct a design qualification to ensure the facility meets specifications.
Next, perform installation qualification to verify that equipment is installed correctly. Then, execute operational qualification to confirm systems operate within defined parameters.
Finally, conduct performance qualification by testing the cleanroom under operational conditions. This process ensures compliance with regulatory standards and operational efficiency.
What is the temperature and humidity requirement for ISO 5?
ISO 5 cleanrooms typically require a temperature range of 20-24°C (68-75°F) for optimal operation. This range helps maintain product integrity and personnel comfort.
Humidity levels should be kept between 30-60% relative humidity. This balance prevents static electricity and supports the stability of sensitive materials.
What are the common challenges in modular cleanroom design?
Common challenges in modular cleanroom design include maintaining adequate airflow and filtration efficiency. Ensuring proper air distribution can be complex in modular setups.
Another challenge is integrating utilities while maintaining cleanroom integrity. This includes electrical, plumbing, and HVAC systems.
Finally, adhering to regulatory compliance throughout the design process poses challenges. Designers must ensure that all components meet stringent cleanliness standards.
What is the role of gowning rooms in a cleanroom?
Gowning rooms serve as a critical transition area between controlled and uncontrolled environments. They help prevent contamination by ensuring personnel are properly attired before entering cleanrooms.
In gowning rooms, employees don specialized garments, gloves, and masks. This minimizes the introduction of particles and microbes into the cleanroom environment.
What is the role of cleanroom furniture?
Cleanroom furniture is designed to minimize contamination and support cleanliness. It typically features smooth surfaces, rounded edges, and materials that resist particle accumulation.
This specialized furniture also facilitates easy cleaning and maintenance, ensuring that it does not harbor contaminants. Properly chosen furniture enhances workflow and maintains the integrity of the cleanroom environment.
What are the environmental controls for ISO 5 cleanrooms?
Environmental controls for ISO 5 cleanrooms include air filtration, temperature, humidity, and airflow management. These factors are essential for maintaining cleanliness and product integrity.
Key elements involve HEPA or ULPA filters for air purification, as well as precise HVAC systems for temperature and humidity control. Regular monitoring and maintenance are crucial to ensure compliance with ISO standards.
How to perform a cleanroom audit?
Performing a cleanroom audit involves several key steps. Start by reviewing documentation, including procedures, records, and maintenance logs.
Next, conduct a physical inspection to assess cleanliness and compliance with regulations. Check air quality, pressure differentials, and gowning protocols.
Finally, compile findings into a report, identifying any non-conformities and areas for improvement. This audit supports ongoing compliance and operational efficiency.
What is the process for cleanroom certification?
The cleanroom certification process typically involves multiple steps. First, perform a thorough assessment of the cleanroom's design, construction, and operational protocols.
Next, conduct testing for air quality, particle counts, and microbial limits to ensure compliance with standards. This includes HEPA filter testing and airflow measurements.
Finally, a certification body reviews the results and issues a certificate if all standards aremet. Ongoing monitoring and re-certification are essential to maintain compliance over time.
How to certify a modular cleanroom?
To certify a modular cleanroom, follow a structured approach. Begin with a comprehensive design review, ensuring that all components comply with applicable standards.
Conduct installation qualification by verifying that all modular units are assembled correctly according to specifications. Next, perform operational qualification to confirm that systems function as intended.
Finally, execute performance qualification tests under real operating conditions, assessing air quality, particle counts, and humidity levels. Successful completion leads to certification.
What is the importance of gowning in an ISO 5 cleanroom?
Gowning in an ISO 5 cleanroom is critical for contamination control. It prevents particles from personnel, such as skin flakes and hair, from entering the clean environment.
Proper gowning practices include wearing gloves, masks, and specialized garments that cover all exposed skin. This reduces the risk of microbial contamination and maintains the integrity of processes.
Training employees on gowning protocols is essential. Knowledgeable staff ensure compliance, contributing to a consistently clean environment essential for sensitive operations.
How to maintain a modular cleanroom?
Maintaining a modular cleanroom requires regular cleaning and monitoring. Establish a routine cleaning schedule using appropriate cleaning agents that do not leave residues.
Monitor environmental parameters, including air quality, temperature, and humidity, to ensure compliance with ISO standards. Regular inspections for equipment performance and integrity are also necessary.
Additionally, train personnel on proper maintenance practices and gowning procedures. This helps to prevent contamination and ensures the cleanroom operates efficiently over time.
How to manage airflow in a modular cleanroom?
Managing airflow in a modular cleanroom involves strategic planning and equipment selection. Utilize a well-designed HVAC system that ensures balanced air pressure and consistent airflow rates.
Incorporate HEPA or ULPA filters to remove particles effectively. Regularly monitor airflow patterns and adjust diffusers to maintain laminar flow, minimizing contamination risks.
Conduct routine assessments to identify any airflow issues, such as dead spots or turbulence. Addressing these promptly helps maintain a controlled environment for sensitive operations.
What is the difference between class 100 and ISO 5 cleanrooms?
Class 100 cleanrooms, defined by the Federal Standard 209E, allow a maximum of 100 particles ≥0.5 micrometers per cubic foot. In contrast, ISO 5 cleanrooms permit a maximum of 3,520 particles per cubic meter for the same size particles.
While both classifications aim for high cleanliness, ISO 5 is more widely recognized internationally. The ISO classification system also provides a broader framework for various cleanliness levels.
Understanding these differences is crucial for industries that require specific cleanliness standards, ensuring compliance with regulatory requirements and operational effectiveness.
How to maintain humidity levels in ISO 5 cleanrooms?
Maintaining humidity levels in ISO 5 cleanrooms is vital for operational integrity. Use HVAC systems equipped with humidifiers or dehumidifiers to control moisture levels effectively.
Regularly monitor humidity using calibrated sensors. Aim to keep levels between 30-60% relative humidity to prevent static electricity and material degradation.
Routine maintenance of the HVAC system is essential to ensure optimal performance. This includes cleaning filters and checking for any leaks that could affect humidity control.
What types of industries use modular cleanrooms?
Modular cleanrooms are utilized across various industries, including:
- Pharmaceuticals: For drug manufacturing and testing.
- Biotechnology: In processes requiring sterile environments.
- Semiconductors: For microchip production and assembly.
- Aerospace: To ensure contamination-free manufacturing of sensitive components.
These industries benefit from the flexibility and scalability that modular cleanrooms provide, accommodating changing regulatory and operational needs.
How to implement a cleanroom training program?
Implementing a cleanroom training program involves several key steps. First, develop a comprehensive curriculum covering contamination control, gowning procedures, and equipment usage.
Next, conduct hands-on training sessions to ensure employees understand protocols and their importance. Use real-life scenarios to enhance learning and retention.
Finally, establish a system for ongoing training and assessments to keep staff updated on best practices and regulatory changes. Continuous improvement ensures sustained compliance and operational efficiency.
Factory Production Workshop Video
Factory Photo
Product Packaging And International Logistics
Product International Certification
Find Other Common Equipment Recommendations
-
Modular CleanRoom
US$9000-10000 USD/Unit
Min. Order:1 Set -
Air Shower
US$1000.00-5000.00 USD/Unit
Min. Order:1 Set -
Downflow Booth
US$3000-6000 USD/Unit
Min. Order:1 Set -
Clean bench
US$600-2000 USD/Unit
Min. Order:1 Set -
Air Filter
US$3-50 USD/Unit
Min. Order:1 Set -
Cleanroom Wall Panels
US$10-20 USD/sq.
Min. Order:1 Set -
Pass Box
US$200-500 USD/Unit
Min. Order:1 Set -
FFU
US$135-350 USD/Unit
Min. Order:1 Set -
Fume Hood
US$700-1500 USD/Unit
Min. Order:1 Set -
Cleanroom HVAC
US$5000-20000 USD/Unit
Min. Order:1 Set -
Clean room floor
US$5-20 USD/Sq.
Min. Order:1 Set -
Clean room ceiling
US$
Min. Order:1 Set