5 x 10M ISO 5 Modular Cleanroom
Reference Price:US$21000-30000


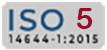
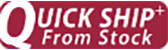
Cleanroom
5 x 10M ISO 5 Modular Cleanroom
Choose your installation & validation options below
Quantity:
Choose your Cleanroom frame structure material
Quantity:
Choose your Cleanroom Wall enclosure materials
Quantity:
Choose your Temperature requirements
Quantity:
Choose your humidity requirements
Quantity:
Choose your Explosion-proof requirements
Quantity:
Summary
5 x 10M ISO 5 Modular Cleanroom
Validation
Installation & Validation
Find Similar Products
-
5 x 10M ISO 5 Modular Cleanroom
US$20000-60000 USD/Set
Min. Order:1 Set -
6 x 6M ISO 5 Modular Cleanroom
US$20000-60000 USD/Set
Min. Order:1 Set -
6 x 8M ISO 5 Modular Cleanroom
US$20000-60000 USD/Set
Min. Order:1 Set -
6 x 10M ISO 5 Modular Cleanroom
US$20000-60000 USD/Set
Min. Order:1 Set -
5 x 6M ISO 5 Modular Cleanroom
US$20000-60000 USD/Set
Min. Order:1 Set -
5 x 7M ISO 5 Modular Cleanroom
US$20000-60000 USD/Set
Min. Order:1 Set
Cleanrooms Detail
An ISO 5 modular cleanroom is a controlled environment that meets stringent cleanliness standards as defined by the International Organization for Standardization (ISO). It is designed to maintain a maximum allowable particle concentration of no more than 3,520 particles per cubic meter for particles ≥0.5 micrometers in size.
Cleanroom Project Scope(from structure, HVAC,electric to autoc ontrol) | 1. Cleanroom Structure: Wall Panel, Ceiling Panel, Windows, Doors, Fttings, Flooring |
2. HVAC: AHU, Chiller, dehumidifier, Ducting, Piping, etc. | |
3. Electric: Lighting, Switch, Cables, Wires, Power Distribution Cabinet, etc | |
4. Auto- control: PLC Controller, Sensors for Humidity and Temperature, Control Panel | |
5. Process Piping System: Gas, Water Pipeline | |
Equipment | Air shower, Cargo shower, Mist shower, Dynamic pass box, Static pass box, Sampling booth,Weighing booth, Dispensing booth, |
Medicine stability test chamber, isolator, VHP sterilizer,Biological safety chamber, FFU, LAF, etc. | |
Temperature | 21-27*C (or as per required) |
Humidity | 30-60°C (or as per required) |
Application | Pharmaceutical factory, hospital, medical device factory, electronics factory, food factory,cosmetics factory, etc. |
Qualification Documents | CE GMP ISO |
Full Service | FAT and SAT Service, Professional Consultation, Training, 24 hours technical support |
an ISO 5 modular cleanroom is essential for processes that require strict control of airborne particulate contamination to ensure product integrity and compliance with industry standards.
Cleanrooms Airflow
The airflow principle in an ISO 5 modular cleanroom is critical for maintaining the required cleanliness levels and ensuring that the environment remains free from contamination. Here are the key aspects of the airflow principle in an ISO 5 cleanroom:
Cleanrooms Installation
Cleanrooms Testing
Cleanroom testing is a series of tests performed on the interior environment of a cleanroom to verify that it meets specific cleanliness requirements. These tests usually involve the measurement of a number of parameters such as air cleanliness, temperature and humidity, air velocity and air volume, noise, illumination, etc. inside the clean room. The purpose of the testing is to ensure that the clean room is able to provide a stable and contamination-free environment during the production process.
FAQ
How often should an ISO 5 cleanroom be tested?
ISO 5 cleanrooms should be tested at least once a month to ensure compliance with cleanliness standards. Regular testing helps identify potential contamination sources.
Routine tests include air particle counts, microbial monitoring, and surface sampling. Adjustments should be made based on test results to maintain standards.
How to manage waste in an ISO 5 cleanroom?
Effective waste management in an ISO 5 cleanroom includes segregation, labeling, and proper disposal procedures. Identify waste types such as hazardous and non-hazardous.
Implement a waste disposal schedule and train personnel on procedures. Regular audits ensure compliance and minimize contamination risks.
Consider using designated waste containers and color-coded bins to enhance waste sorting efficiency.
How to conduct a cleanroom risk assessment?
To conduct a cleanroom risk assessment, first identify potential contamination sources, including personnel, materials, and equipment. Evaluate the likelihood and impact of contamination events.
Next, assess existing controls and determine their effectiveness. Identify gaps and recommend improvements to minimize risks.
Finally, document findings and regularly review the assessment to adapt to changes in operations or regulations.
What are the safety protocols for cleanroom operations?
Safety protocols for cleanroom operations include:
- Wearing appropriate cleanroom garments.
- Performing regular training for all personnel.
- Adhering to strict hygiene practices.
Following these protocols minimizes contamination risks and ensures a safe working environment.
What are the environmental monitoring requirements for ISO 5?
ISO 5 cleanrooms require continuous environmental monitoring, including:
- Airborne particle counts.
- Microbial monitoring.
- Temperature and humidity control.
Regular sampling and analysis help maintain compliance and ensure operational integrity.
How does temperature affect cleanroom operations?
Temperature affects cleanroom operations by influencing equipment performance and material stability. Excessive heat can lead to increased particle generation and reduced air quality.
Maintaining stable temperatures is essential for process consistency, particularly in sensitive applications. Regular monitoring ensures compliance with specified temperature ranges.
How to handle maintenance in an operating cleanroom?
Maintenance in an operating cleanroom should be carefully planned to minimize disruption and contamination risks. Schedule routine maintenance during off-peak hours when possible.
Use cleanroom-compatible tools and materials to prevent contamination during maintenance activities. Train staff on proper procedures to follow during maintenance tasks.
Document all maintenance activities to ensure compliance and maintain cleanroom integrity. Regular audits can help identify recurring issues.
What are the design considerations for a modular cleanroom?
Key design considerations for a modular cleanroom include air flow, material selection, and layout efficiency. Ensure the design allows for proper air circulation to maintain cleanliness.
Incorporate flexibility in design for future expansion or modifications. Choose materials that are easy to clean and resistant to contamination.
Consider the integration of utilities and services to support operations without compromising cleanliness.
How to achieve ISO 5 cleanliness?
To achieve ISO 5 cleanliness, focus on controlling airborne particles and maintaining environmental conditions. Implement strict gowning procedures and establish cleaning protocols.
Regular monitoring of air quality, particle counts, and microbial levels is essential. Use HEPA filters and appropriate ventilation systems to maintain cleanroom standards.
Finally, ensure continuous training for personnel to uphold cleanliness standards and improve operational practices.
How to monitor air quality in an ISO 5 cleanroom?
Air quality in an ISO 5 cleanroom can be monitored through:
- Continuous particle counting.
- Microbial sampling.
- Regular air exchanges.
Use calibrated equipment and maintain records of air quality assessments for compliance and operational insights.
What are the certification bodies for cleanrooms?
Several reputable certification bodies provide cleanroom certification, including:
- ISO (International Organization for Standardization).
- NSF International.
- PDA (Parenteral Drug Association).
These organizations ensure that cleanrooms meet established standards for cleanliness and operational efficiency.
How does pressure differential work in cleanrooms?
Pressure differential in cleanrooms is crucial for preventing contamination. Higher pressure in the cleanroom compared to adjacent areas ensures that air flows out rather than in.
This flow minimizes the entry of unfiltered air and contaminants. Regular monitoring of pressure differentials is vital to maintain compliance and operational integrity.
How to select cleanroom garments?
When selecting cleanroom garments, consider fabric type and contamination control. Opt for materials that are lint-free and resistant to particulate shedding.
Ensure garments fit properly to prevent gaps that could allow contamination. Evaluate the suitability for specific cleanroom classifications and intended applications.
Training personnel on proper donning and doffing techniques is essential to maintain cleanliness standards.
How to document cleanroom procedures?
Documenting cleanroom procedures involves creating clear, comprehensive protocols. Use standardized templates to ensure consistency acrossall documents. Clearly outline each procedure, including the purpose, scope, responsibilities, and step-by-step instructions.
Regularly review and update documentation to reflect changes in processes or regulations. Ensure all personnel are trained on current procedures to maintain compliance.
Implement a system for tracking revisions and approvals to maintain document integrity and provide a historical record.
What types of filters are used in ISO 5 cleanrooms?
ISO 5 cleanrooms typically utilize HEPA (High-Efficiency Particulate Air) filters to remove airborne particles.
In some cases, ULPA (Ultra-Low Penetration Air) filters may be employed for even higher filtration efficiency.
These filters are crucial for maintaining the cleanroom's air quality and ensuring compliance with cleanliness standards. Regular testing and maintenance of filters are essential.
What is the process for cleanroom certification?
The cleanroom certification process involves several key steps. First, conduct a thorough evaluation of the cleanroom against relevant standards such as ISO 14644.
Next, perform environmental monitoring and testing, including particle counts and microbial sampling, to assess compliance.
Finally, submit the results to a recognized certification body for review. Upon meeting the requirements, the cleanroom will receive certification, confirming its operational standards.
How to design a cleanroom for biological applications?
Designing a cleanroom for biological applications requires a focus on contamination control and environmental stability. Ensure proper air filtration systems, such as HEPA or ULPA filters, are in place.
Incorporate controlled temperature and humidity levels to support biological processes. Design layout to facilitate efficient workflows while minimizing contamination risks.
Regularly review design specifications to adapt to advances in technology and regulatory requirements, ensuring ongoing compliance and operational efficiency.
How to control contamination in a modular cleanroom?
Contamination control in a modular cleanroom involves several strategies:
- Implement strict gowning and hygiene protocols.
- Utilize airlocks and pass-through chambers to minimize exposure.
- Conduct regular cleaning and disinfection of surfaces and equipment.
Training personnel on contamination prevention practices is critical to maintaining cleanroom integrity and compliance.
How to calculate airflow for a modular cleanroom?
To calculate airflow for a modular cleanroom, first determine the required air changes per hour (ACH) based on cleanroom classification.
Next, use the cleanroom volume to calculate the total airflow needed:
- Airflow (CFM) = Volume (cubic feet) × ACH / 60.
Consider factors such as filter efficiency and any additional airflow requirements from equipment. Regularly assess airflow to ensure optimal performance.
How to maintain a modular cleanroom?
Maintaining a modular cleanroom involves regular inspections and adherence to a strict maintenance schedule. Key tasks include:
Routine cleaning and disinfection of surfaces.
Regular monitoring of air quality and environmental conditions.
Maintaining equipment and filtration systems to ensure optimal performance.
Document all maintenance activities to track compliance and identify areas for improvement. Continuous training for personnel is also essential.
Factory Production Workshop Video
Factory Photo
Product Packaging And International Logistics
Product International Certification
Find Other Common Equipment Recommendations
-
Modular CleanRoom
US$9000-10000 USD/Unit
Min. Order:1 Set -
Air Shower
US$1000.00-5000.00 USD/Unit
Min. Order:1 Set -
Downflow Booth
US$3000-6000 USD/Unit
Min. Order:1 Set -
Clean bench
US$600-2000 USD/Unit
Min. Order:1 Set -
Air Filter
US$3-50 USD/Unit
Min. Order:1 Set -
Cleanroom Wall Panels
US$10-20 USD/sq.
Min. Order:1 Set -
Pass Box
US$200-500 USD/Unit
Min. Order:1 Set -
FFU
US$135-350 USD/Unit
Min. Order:1 Set -
Fume Hood
US$700-1500 USD/Unit
Min. Order:1 Set -
Cleanroom HVAC
US$5000-20000 USD/Unit
Min. Order:1 Set -
Clean room floor
US$5-20 USD/Sq.
Min. Order:1 Set -
Clean room ceiling
US$
Min. Order:1 Set