5 x 6M ISO 5 Modular Cleanroom
Reference Price:US$14500-17000
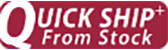

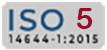
Cleanroom
5 x 6M ISO 5 Modular Cleanroom
Choose your installation & validation options below
Quantity:
Choose your Cleanroom frame structure material
Quantity:
Choose your Cleanroom Wall enclosure materials
Quantity:
Choose your Temperature requirements
Quantity:
Choose your humidity requirements
Quantity:
Choose your Explosion-proof requirements
Quantity:
Summary
5 x 6M ISO 5 Modular Cleanroom
Validation
Installation & Validation
Find Similar Products
-
5 x 10M ISO 5 Modular Cleanroom
US$20000-60000 USD/Set
Min. Order:1 Set -
6 x 6M ISO 5 Modular Cleanroom
US$20000-60000 USD/Set
Min. Order:1 Set -
6 x 8M ISO 5 Modular Cleanroom
US$20000-60000 USD/Set
Min. Order:1 Set -
6 x 10M ISO 5 Modular Cleanroom
US$20000-60000 USD/Set
Min. Order:1 Set -
5 x 6M ISO 5 Modular Cleanroom
US$20000-60000 USD/Set
Min. Order:1 Set -
5 x 7M ISO 5 Modular Cleanroom
US$20000-60000 USD/Set
Min. Order:1 Set
Cleanrooms Detail
An ISO 5 modular cleanroom is a controlled environment that meets stringent cleanliness standards as defined by the International Organization for Standardization (ISO). It is designed to maintain a maximum allowable particle concentration of no more than 3,520 particles per cubic meter for particles ≥0.5 micrometers in size.
Cleanroom Project Scope(from structure, HVAC,electric to autoc ontrol) | 1. Cleanroom Structure: Wall Panel, Ceiling Panel, Windows, Doors, Fttings, Flooring |
2. HVAC: AHU, Chiller, dehumidifier, Ducting, Piping, etc. | |
3. Electric: Lighting, Switch, Cables, Wires, Power Distribution Cabinet, etc | |
4. Auto- control: PLC Controller, Sensors for Humidity and Temperature, Control Panel | |
5. Process Piping System: Gas, Water Pipeline | |
Equipment | Air shower, Cargo shower, Mist shower, Dynamic pass box, Static pass box, Sampling booth,Weighing booth, Dispensing booth, |
Medicine stability test chamber, isolator, VHP sterilizer,Biological safety chamber, FFU, LAF, etc. | |
Temperature | 21-27*C (or as per required) |
Humidity | 30-60°C (or as per required) |
Application | Pharmaceutical factory, hospital, medical device factory, electronics factory, food factory,cosmetics factory, etc. |
Qualification Documents | CE GMP ISO |
Full Service | FAT and SAT Service, Professional Consultation, Training, 24 hours technical support |
an ISO 5 modular cleanroom is essential for processes that require strict control of airborne particulate contamination to ensure product integrity and compliance with industry standards.
Cleanrooms Airflow
The airflow principle in an ISO 5 modular cleanroom is critical for maintaining the required cleanliness levels and ensuring that the environment remains free from contamination. Here are the key aspects of the airflow principle in an ISO 5 cleanroom:
Cleanrooms Installation
Cleanrooms Testing
Cleanroom testing is a series of tests performed on the interior environment of a cleanroom to verify that it meets specific cleanliness requirements. These tests usually involve the measurement of a number of parameters such as air cleanliness, temperature and humidity, air velocity and air volume, noise, illumination, etc. inside the clean room. The purpose of the testing is to ensure that the clean room is able to provide a stable and contamination-free environment during the production process.
FAQ
How to validate a modular cleanroom?
Validating a modular cleanroom involves several key steps. First, perform a Design Qualification (DQ) to ensure specifications meet required standards.
Next, conduct Installation Qualification (IQ) to confirm that the cleanroom is built according to design specifications. Finally, execute Operational Qualification (OQ) to verify that systems function as intended under actual use conditions.
Each step should be thoroughly documented to maintain compliance and facilitate future audits. Regular revalidation is also essential to ensure ongoing performance.
How to achieve ISO 5 cleanliness?
Achieving ISO 5 cleanliness requires strict adherence to particle count limits. The maximum allowable particle count is 3,520 particles per cubic meter for particles ≥0.5 micron.
Start by using high-efficiency particulate air (HEPA) filters in the cleanroom's ventilation system. Regular monitoring of air quality is essential to ensure compliance with ISO standards.
Implement a rigorous cleaning protocol that includes frequent cleaning of surfaces and equipment. Personnel must also follow strict gowning procedures to minimize contamination risks.
What are the environmental controls for ISO 5 cleanrooms?
Environmental controls in ISO 5 cleanrooms include:
- Temperature: Maintain between 20-24°C for optimal conditions.
- Humidity: Control relative humidity levels between 30-60%.
- Airflow: Ensure unidirectional airflow to minimize particle distribution.
Proper monitoring equipment should be installed to continuously track these parameters. Regular maintenance of HVAC systems is crucial to ensure performance stability.
How to ensure proper ventilation in an ISO 5 cleanroom?
Proper ventilation in an ISO 5 cleanroom is vital for maintaining air quality. Utilize HEPA filters to ensure that incoming air is free of contaminants.
Design the cleanroom to incorporate a unidirectional airflow system, directing air from clean to less clean areas. This design reduces particle movement and maintains cleanliness.
Regularly monitor airflow velocity and particle counts to ensure compliance with ISO standards. Routine maintenance of HVAC systems is essential to sustain optimal airflow and filtration efficiency.
How to manage waste in an ISO 5 cleanroom?
Managing waste in an ISO 5 cleanroom involves a systematic approach. First, segregate waste into appropriate categories: hazardous, non-hazardous, and recyclable materials.
Second, establish designated waste disposal areas to minimize contamination risks. Use clearly labeled containers and ensure they are easily accessible.
Regularly schedule waste removal to prevent accumulation, and train staff on proper waste handling protocols. Documentation of waste disposal is also important for compliance and auditing purposes.
What is the importance of gowning in an ISO 5 cleanroom?
Gowning is critical in an ISO 5 cleanroom to minimize contamination risks. Proper gowning procedures prevent personnel from introducing particles into the controlled environment.
Personnel must wear sterile gowns, gloves, masks, and hair covers to limit the shedding of skin cells and other contaminants. Each item should be designed for single-use or high-level sterilization.
Regular training on gowning protocols ensures compliance and reinforces the importance of maintaining cleanliness standards. Failure to adhere to these protocols can compromise product integrity and safety.
How to design a cleanroom for biological applications?
Designing a cleanroom for biological applications necessitates careful planning. First, consider airflow patterns to ensure containment and minimize contamination risks.
Install high-efficiency filters and ensure that the cleanroom meets specific ISO standards relevant to biological research. Incorporate proper gowning areas and dedicated equipment zones.
Additionally, implement temperature and humidity controls essential for biological materials. Regular monitoring and maintenance of these systems are crucial for operational integrity.
How does temperature affect cleanroom operations?
Temperature significantly impacts cleanroom operations and should be maintained within specific ranges. In ISO 5 cleanrooms, the recommended range is 20-24°C to ensure optimal conditions.
Extreme temperatures can affect equipment performance and product stability. High temperatures may increase particle generation, while low temperatures can impact material properties.
Regular monitoring of temperature and prompt adjustments are essential to maintain compliance. Consistent temperature control also helps ensure the efficacy of processes conducted within the cleanroom.
What is the maximum allowable particle count in ISO 5?
The maximum allowable particle count in an ISO 5 cleanroom is defined as follows:
- 0.5 microns: 3,520 particles per cubic meter
- 1.0 microns: 832 particles per cubic meter
- 5.0 microns: 29 particles per cubic meter
These limits are crucial for ensuring the cleanliness necessary for sensitive processes. Continuous monitoring and regular audits are required to maintain these standards and ensure compliance.
What are the certification bodies for cleanrooms?
Several organizations provide certification for cleanrooms, ensuring they meet industry standards. Key certification bodies include:
- ISO (International Organization for Standardization)
- ESD Association- Institute of Environmental Sciences and Technology (IEST)
- Federal Standard 209E
These organizations develop and enforce standards for cleanroom design, operation, and maintenance. Engaging with recognized certification bodies ensures compliance with industry regulations and enhances credibility in cleanroom operations.
How to perform a cleanroom audit?
Performing a cleanroom audit involves a systematic evaluation of compliance with cleanliness standards. First, review documentation related to cleanroom procedures, including SOPs and validation reports.
Next, assess the physical environment by inspecting equipment, airflow systems, and gowning protocols. Pay close attention to areas that are prone to contamination.
Finally, compile findings into a comprehensive report detailing non-compliance areas and recommendations for improvements. Regular audits help maintain standards and ensure ongoing operational integrity.
What types of filters are used in ISO 5 cleanrooms?
ISO 5 cleanrooms primarily utilize HEPA (High-Efficiency Particulate Air) filters. These filters capture 99.97% of particles 0.3 microns and larger, ensuring high air quality.
In some instances, ULPA (Ultra-Low Penetration Air) filters may also be used for even stricter particle control. The choice of filter depends on the specific cleanliness requirements of the application.
Regular maintenance and testing of filters are vital to ensure their effectiveness. Scheduled replacements based on manufacturer recommendations help maintain compliance with ISO standards.
What are the key components of a modular cleanroom?
Key components of a modular cleanroom include:
- Wall Panels: Constructed from cleanroom-grade materials for optimal cleanliness.
- Ceiling Systems: Designed for easy access to HVAC and lighting systems.
- Flooring: Smooth, non-porous surfaces that facilitate cleaning.
In addition to these structural components, essential systems such as HVAC, lighting, and filtering systems are integrated to maintain environmental controls. Regular maintenance ensures these systems function optimally.
How to ensure compliance in an ISO 5 cleanroom?
Ensuring compliance in an ISO 5 cleanroom requires a multi-faceted approach. First, establish clear Standard Operating Procedures (SOPs) that align with ISO standards and train personnel accordingly.
Regular monitoring of environmental parameters such as temperature, humidity, and particle counts is essential. Use calibrated equipment to ensure accurate readings and compliance with established limits.
Conduct routine inspections and audits to identify non-conformities. Implement corrective actions promptly and keep thorough documentation to demonstrate compliance during audits.
What is the lead time for constructing a modular cleanroom?
The lead time for constructing a modular cleanroom can vary widely based on several factors. Typically, the design and planning phase may take 4-8 weeks, depending on complexity.
Once the design is approved, construction can take an additional 4-12 weeks. This timeline can be influenced by factors such as the size of the cleanroom and the availability of materials.
However, modular cleanrooms often allow for quicker installation compared to traditional construction methods. Proper project management and coordination with contractors can further expedite the process.
How to integrate automation in a modular cleanroom?
Integrating automation in a modular cleanroom enhances efficiency and consistency. Start by identifying key processes that can benefit from automation, such as material handling and monitoring.
Utilize automated systems for environmental monitoring, including temperature and particle count, ensuring real-time data collection. This integration facilitates immediate responses to deviations from established parameters.
Additionally, consider automated gowning systems and robotic handling for sensitive materials to minimize human intervention. Regularly update software and systems to keep pace with technological advancements.
How to use monitoring equipment in cleanrooms?
Using monitoring equipment in cleanrooms is vital for maintaining compliance with cleanliness standards. Begin by selecting appropriate devices for measuring parameters like temperature, humidity, and particle counts.
Set up continuous monitoring systems that provide real-time data and alerts for deviations from established thresholds. This proactive approach helps prevent contamination risks.
Regularly calibrate and maintain monitoring equipment to ensure accuracy. Document all measurements and any corrective actions taken to create an audit trail for compliance verification.
How to choose the right flooring for an ISO 5 cleanroom?
Choosing the right flooring for an ISO 5 cleanroom is crucial for cleanliness and functionality. Select flooring that is non-porous, smooth, and resistant to chemical spills for easy cleaning.
Common materials used include vinyl, epoxy, and polyurethane, which provide durability and ease of maintenance. Ensure the flooring meets anti-static requirements if necessary.
Additionally, consider the flooring's slip resistance to enhance safety for personnel. Regular inspections and maintenance are essential to prolong the lifecycle of the flooring and maintain cleanliness standards.
What is the impact of vibrations in a cleanroom?
Vibrations in a cleanroom can significantly affect sensitive processes and equipment. Even minor vibrations can lead to particle generation and compromise product integrity.
Factory Production Workshop Video
Factory Photo
Product Packaging And International Logistics
Product International Certification
Find Other Common Equipment Recommendations
-
Modular CleanRoom
US$9000-10000 USD/Unit
Min. Order:1 Set -
Air Shower
US$1000.00-5000.00 USD/Unit
Min. Order:1 Set -
Downflow Booth
US$3000-6000 USD/Unit
Min. Order:1 Set -
Clean bench
US$600-2000 USD/Unit
Min. Order:1 Set -
Air Filter
US$3-50 USD/Unit
Min. Order:1 Set -
Cleanroom Wall Panels
US$10-20 USD/sq.
Min. Order:1 Set -
Pass Box
US$200-500 USD/Unit
Min. Order:1 Set -
FFU
US$135-350 USD/Unit
Min. Order:1 Set -
Fume Hood
US$700-1500 USD/Unit
Min. Order:1 Set -
Cleanroom HVAC
US$5000-20000 USD/Unit
Min. Order:1 Set -
Clean room floor
US$5-20 USD/Sq.
Min. Order:1 Set -
Clean room ceiling
US$
Min. Order:1 Set