5 x 8M ISO 5 Modular Cleanroom
Reference Price:US$17200-22000
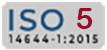



Cleanroom
5 x 8M ISO 5 Modular Cleanroom
Choose your installation & validation options below
Quantity:
Choose your Cleanroom frame structure material
Quantity:
Choose your Cleanroom Wall enclosure materials
Quantity:
Choose your Temperature requirements
Quantity:
Choose your humidity requirements
Quantity:
Choose your Explosion-proof requirements
Quantity:
Summary
5 x 8M ISO 5 Modular Cleanroom
Validation
Installation & Validation
Find Similar Products
-
5 x 10M ISO 5 Modular Cleanroom
US$20000-60000 USD/Set
Min. Order:1 Set -
6 x 6M ISO 5 Modular Cleanroom
US$20000-60000 USD/Set
Min. Order:1 Set -
6 x 8M ISO 5 Modular Cleanroom
US$20000-60000 USD/Set
Min. Order:1 Set -
6 x 10M ISO 5 Modular Cleanroom
US$20000-60000 USD/Set
Min. Order:1 Set -
5 x 6M ISO 5 Modular Cleanroom
US$20000-60000 USD/Set
Min. Order:1 Set -
5 x 7M ISO 5 Modular Cleanroom
US$20000-60000 USD/Set
Min. Order:1 Set
Cleanrooms Detail
An ISO 5 modular cleanroom is a controlled environment that meets stringent cleanliness standards as defined by the International Organization for Standardization (ISO). It is designed to maintain a maximum allowable particle concentration of no more than 3,520 particles per cubic meter for particles ≥0.5 micrometers in size.
Cleanroom Project Scope(from structure, HVAC,electric to autoc ontrol) | 1. Cleanroom Structure: Wall Panel, Ceiling Panel, Windows, Doors, Fttings, Flooring |
2. HVAC: AHU, Chiller, dehumidifier, Ducting, Piping, etc. | |
3. Electric: Lighting, Switch, Cables, Wires, Power Distribution Cabinet, etc | |
4. Auto- control: PLC Controller, Sensors for Humidity and Temperature, Control Panel | |
5. Process Piping System: Gas, Water Pipeline | |
Equipment | Air shower, Cargo shower, Mist shower, Dynamic pass box, Static pass box, Sampling booth,Weighing booth, Dispensing booth, |
Medicine stability test chamber, isolator, VHP sterilizer,Biological safety chamber, FFU, LAF, etc. | |
Temperature | 21-27*C (or as per required) |
Humidity | 30-60°C (or as per required) |
Application | Pharmaceutical factory, hospital, medical device factory, electronics factory, food factory,cosmetics factory, etc. |
Qualification Documents | CE GMP ISO |
Full Service | FAT and SAT Service, Professional Consultation, Training, 24 hours technical support |
an ISO 5 modular cleanroom is essential for processes that require strict control of airborne particulate contamination to ensure product integrity and compliance with industry standards.
Cleanrooms Airflow
The airflow principle in an ISO 5 modular cleanroom is critical for maintaining the required cleanliness levels and ensuring that the environment remains free from contamination. Here are the key aspects of the airflow principle in an ISO 5 cleanroom:
Cleanrooms Installation
Cleanrooms Testing
Cleanroom testing is a series of tests performed on the interior environment of a cleanroom to verify that it meets specific cleanliness requirements. These tests usually involve the measurement of a number of parameters such as air cleanliness, temperature and humidity, air velocity and air volume, noise, illumination, etc. inside the clean room. The purpose of the testing is to ensure that the clean room is able to provide a stable and contamination-free environment during the production process.
FAQ
What is the maximum allowable particle count in ISO 5?
ISO 5 cleanrooms must not exceed 3,520 particles per cubic meter for particles ≥0.5 microns. For particles ≥5 microns, the limit is 29 particles per cubic meter.
Maintaining these limits ensures a controlled environment for critical processes, minimizing contamination risks. Regular monitoring is essential to uphold these standards.
What are the regulatory requirements for cleanrooms?
Cleanrooms must comply with various standards, including ISO 14644 and GMP guidelines. These standards dictate cleanliness, airflow, and design specifications.
Documentation is crucial, detailing procedures for monitoring and maintaining cleanliness. Regular audits ensure compliance and identify areas for improvement.
Training staff on these regulations is also essential to ensure proper practices are followed consistently.
How to integrate automation in a modular cleanroom?
Integrating automation involves selecting suitable systems for monitoring and controlling environmental parameters. Systems may include sensors for temperature, humidity, and particle counts.
Data management software should be implemented to analyze trends and generate reports, enhancing operational efficiency. Additionally, consider automated material handling systems to reduce human interaction.
Training staff to operate these automated systems effectively is crucial for seamless integration and maintenance. Regular updates and system checks should also be scheduled.
How to achieve ISO 5 cleanliness?
Achieving ISO 5 cleanliness requires strict adherence to protocols for air filtration and circulation. High-efficiency particulate air (HEPA) filters should be used to purify incoming air.
Regular cleaning and maintenance schedules must be established, focusing on surfaces and equipment to eliminate contamination sources. Personnel must follow strict gowning procedures to minimize particulate introduction.
Monitoring particle counts with calibrated equipment is essential to ensure ongoing compliance. Conduct regular training sessions to reinforce best practices among staff.
What are the common challenges in modular cleanroom design?
- Space Limitations: Available space may restrict modular design options and airflow management.
- Integration with Existing Systems: Ensuring compatibility with current infrastructure can be complex.
- Regulatory Compliance: Adhering to stringent regulations during design and construction can be challenging.
- Flexibility Needs: Designing for future scalability while maintaining current operational efficiency is often difficult.
How to control airflow direction in a cleanroom?
To control airflow direction, utilize strategically placed HEPA filters and fan systems to create a unidirectional airflow pattern. Proper placement ensures contaminants are effectively swept away from critical areas.
Regular monitoring of airflow velocity is essential to maintain desired conditions. Adjustments may be needed based on operational changes or equipment modifications.
Staff training on airflow management is important to ensure adherence to protocols for maintaining cleanroom integrity.
What are the safety protocols for cleanroom operations?
Safety protocols in cleanrooms include:
- Gowning Procedures: Strict adherence to gowning protocols to minimize contamination.
- Personal Hygiene: Regular hand washing and use of antiseptics.
- Equipment Handling: Proper training on equipment use and maintenance.
- Emergency Procedures: Clear protocols for emergencies, including spills and contamination events.
These measures ensure a safe and compliant cleanroom environment.
What is the significance of cleanroom airflow patterns?
Cleanroom airflow patterns play a crucial role in maintaining cleanliness by controlling the movement of particles. Proper airflow prevents contaminants from settling on surfaces and protects sensitive processes.
Understanding airflow patterns helps in designing effective cleanrooms, ensuring that clean air flows towards critical areas. Regular assessments are necessary to optimize these patterns for efficiency.
What is the classification of ISO 5 cleanroom?
ISO 5 is classified based on its allowable particle counts in a specified volume of air. Cleanrooms in this category must maintain a maximum of 3,520 particles per cubic meter for ≥0.5 microns.
This classification indicates a highly controlled environment suitable for sensitive processes, such as semiconductor manufacturing and pharmaceutical production. Regular testing ensures compliance with these stringent standards.
What are the key components of a modular cleanroom?
Key components of a modular cleanroom include:
- Walls and Ceilings: Prefabricated panels that are easy to install and modify.
- Air Filtration Systems: HEPA or ULPA filters for maintaining air quality.
- HVAC Systems: Controlled heating, ventilation, and air conditioning for optimal conditions.
- Lighting: Specialized lighting that meets cleanroom standards without generating contaminants.
These components work together to create a compliant cleanroom environment.
What is the significance of a cleanroom logbook?
A cleanroom logbook is vital for documenting all activities related to cleanliness and compliance. It provides a historical record of monitoring data, maintenance activities, and personnel training.
This logbook aids in regulatory compliance and can be essential during audits, showcasingthe adherence to protocols and highlighting any issues that arose. Regular entries help identify trends and potential areas for improvement in cleanroom practices.
Maintaining an accurate logbook fosters accountability among staff and supports continuous quality assurance efforts.
What are the common misconceptions about cleanrooms?
- Cleanrooms are Germ-Free: Many believe cleanrooms are sterile, but they are controlled environments, not completely free of microbes.
- Any Cleanroom is Sufficient for All Applications: Different processes require specific cleanroom classifications; not all are suitable for sensitive tasks.
- Gowning is Optional: Proper gowning is crucial; it significantly reduces contamination risks and is mandatory in cleanroom protocols.
- Air Quality is Always Perfect: Air quality can fluctuate; continuous monitoring is essential to maintain compliance.
How to train staff for modular cleanroom operations?
Training staff for modular cleanroom operations involves comprehensive programs covering protocols, gowning procedures, and equipment usage. Initial training should include theoretical knowledge and practical demonstrations.
Regular refresher courses should be scheduled to keep staff updated on the latest standards and techniques. Incorporating hands-on training with simulations can enhance understanding.
Assessment and feedback should follow training sessions to ensure comprehension and adherence to cleanroom protocols.
How often should an ISO 5 cleanroom be tested?
An ISO 5 cleanroom should be tested at least every six months to ensure compliance with cleanliness standards. This includes particle count testing and airflow assessments.
In addition to regular testing, cleanrooms should be evaluated after any significant changes, such as equipment installation or layout modifications.
Routine maintenance and validation of the cleanroom systems are also essential to uphold operational integrity. Documentation of all tests is crucial for regulatory compliance.
What is the importance of airlocks in modular cleanrooms?
Airlocks serve as transitional spaces that help maintain cleanroom integrity by preventing contamination during personnel and material entry. They minimize the influx of particles from outside the cleanroom environment.
Airlocks often incorporate interlocking doors to ensure only one door is opened at a time, further reducing contamination risks. They can also be equipped with air showers to decontaminate personnel.
Effective airlock design is crucial for maintaining ISO 5 conditions, ensuring that cleanroom operations remain efficient and compliant.
What are the benefits of a modular cleanroom?
- Flexibility: Modular cleanrooms can be easily reconfigured or expanded to meet changing operational needs.
- Cost-Effectiveness: They often have lower initial construction costs and quicker installation times compared to traditional cleanrooms.
- Rapid Deployment: Modular designs can be built and operational in a shorter timeframe, allowing for faster project turnaround.
- Reduced Downtime: Upgrades and modifications can be implemented with minimal disruption to ongoing operations.
These benefits make modular cleanrooms an attractive option for various industries.
What is the role of gowning rooms in a cleanroom?
Gowning rooms serve as essential transition areas where personnel prepare to enter the cleanroom environment. These rooms help maintain cleanroom integrity by reducing the introduction of contaminants.
Proper gowning procedures must be followed, including the use of specialized clothing, masks, gloves, and footwear. This process is critical in minimizing particulates and biological contaminants.
Regular training and monitoring in gowning rooms help ensure compliance and effectiveness in contamination control.
How to upgrade an existing cleanroom to ISO 5?
Upgrading an existing cleanroom to ISO 5 involves several critical steps. First, assess the current cleanroom design and identify areas that require modifications, such as airflow and filtration systems.
Next, install high-efficiency particulate air (HEPA) filters and ensure proper airflow patterns to meet ISO 5 standards. Regular testing and monitoring of particle counts must be established for ongoing compliance.
Finally, train staff on new protocols and ensure adequate documentation is maintained to reflect the upgraded status.
What is the difference between class 100 and ISO 5 cleanrooms?
Class 100 cleanrooms, defined by the Federal Standard 209E, allow a maximum of 100 particles ≥0.5 microns per cubic foot, while ISO 5 cleanrooms permit 3,520 particles per cubic meter for the same size.
ISO 5 is a more contemporary classification that is based on cubic meters, emphasizing global standards. The differences reflect varying regulatory approaches to cleanroom design and operation.
Class 100 is largely considered equivalent to ISO 5 but may not encompass the full range of cleanliness criteria required by ISO standards.
What is the significance of airflow velocity in cleanrooms?
Airflow velocity is critical in cleanrooms as it directly impacts the effectiveness of contamination control. Maintaining appropriate airflow ensures that particles are efficiently removed from the environment and prevents them from settling on surfaces.
Factory Production Workshop Video
Factory Photo
Product Packaging And International Logistics
Product International Certification
Find Other Common Equipment Recommendations
-
Modular CleanRoom
US$9000-10000 USD/Unit
Min. Order:1 Set -
Air Shower
US$1000.00-5000.00 USD/Unit
Min. Order:1 Set -
Downflow Booth
US$3000-6000 USD/Unit
Min. Order:1 Set -
Clean bench
US$600-2000 USD/Unit
Min. Order:1 Set -
Air Filter
US$3-50 USD/Unit
Min. Order:1 Set -
Cleanroom Wall Panels
US$10-20 USD/sq.
Min. Order:1 Set -
Pass Box
US$200-500 USD/Unit
Min. Order:1 Set -
FFU
US$135-350 USD/Unit
Min. Order:1 Set -
Fume Hood
US$700-1500 USD/Unit
Min. Order:1 Set -
Cleanroom HVAC
US$5000-20000 USD/Unit
Min. Order:1 Set -
Clean room floor
US$5-20 USD/Sq.
Min. Order:1 Set -
Clean room ceiling
US$
Min. Order:1 Set