5 x 5M ISO 5 Modular Cleanroom
Reference Price:US$12800-13500



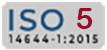
Cleanroom
5 x 5M ISO 5 Modular Cleanroom
Choose your installation & validation options below
Quantity:
Choose your Cleanroom frame structure material
Quantity:
Choose your Cleanroom Wall enclosure materials
Quantity:
Choose your Temperature requirements
Quantity:
Choose your humidity requirements
Quantity:
Choose your Explosion-proof requirements
Quantity:
Summary
5 x 5M ISO 5 Modular Cleanroom
Validation
Installation & Validation
Find Similar Products
-
5 x 10M ISO 5 Modular Cleanroom
US$20000-60000 USD/Set
Min. Order:1 Set -
6 x 6M ISO 5 Modular Cleanroom
US$20000-60000 USD/Set
Min. Order:1 Set -
6 x 8M ISO 5 Modular Cleanroom
US$20000-60000 USD/Set
Min. Order:1 Set -
6 x 10M ISO 5 Modular Cleanroom
US$20000-60000 USD/Set
Min. Order:1 Set -
5 x 6M ISO 5 Modular Cleanroom
US$20000-60000 USD/Set
Min. Order:1 Set -
5 x 7M ISO 5 Modular Cleanroom
US$20000-60000 USD/Set
Min. Order:1 Set
Cleanrooms Detail
An ISO 5 modular cleanroom is a controlled environment that meets stringent cleanliness standards as defined by the International Organization for Standardization (ISO). It is designed to maintain a maximum allowable particle concentration of no more than 3,520 particles per cubic meter for particles ≥0.5 micrometers in size.
Cleanroom Project Scope(from structure, HVAC,electric to autoc ontrol) | 1. Cleanroom Structure: Wall Panel, Ceiling Panel, Windows, Doors, Fttings, Flooring |
2. HVAC: AHU, Chiller, dehumidifier, Ducting, Piping, etc. | |
3. Electric: Lighting, Switch, Cables, Wires, Power Distribution Cabinet, etc | |
4. Auto- control: PLC Controller, Sensors for Humidity and Temperature, Control Panel | |
5. Process Piping System: Gas, Water Pipeline | |
Equipment | Air shower, Cargo shower, Mist shower, Dynamic pass box, Static pass box, Sampling booth,Weighing booth, Dispensing booth, |
Medicine stability test chamber, isolator, VHP sterilizer,Biological safety chamber, FFU, LAF, etc. | |
Temperature | 21-27*C (or as per required) |
Humidity | 30-60°C (or as per required) |
Application | Pharmaceutical factory, hospital, medical device factory, electronics factory, food factory,cosmetics factory, etc. |
Qualification Documents | CE GMP ISO |
Full Service | FAT and SAT Service, Professional Consultation, Training, 24 hours technical support |
an ISO 5 modular cleanroom is essential for processes that require strict control of airborne particulate contamination to ensure product integrity and compliance with industry standards.
Cleanrooms Airflow
The airflow principle in an ISO 5 modular cleanroom is critical for maintaining the required cleanliness levels and ensuring that the environment remains free from contamination. Here are the key aspects of the airflow principle in an ISO 5 cleanroom:
Cleanrooms Installation
Cleanrooms Testing
Cleanroom testing is a series of tests performed on the interior environment of a cleanroom to verify that it meets specific cleanliness requirements. These tests usually involve the measurement of a number of parameters such as air cleanliness, temperature and humidity, air velocity and air volume, noise, illumination, etc. inside the clean room. The purpose of the testing is to ensure that the clean room is able to provide a stable and contamination-free environment during the production process.
FAQ
How to handle equipment in a modular cleanroom?
Handling equipment in a modular cleanroom requires strict adherence to protocols. Always sanitize equipment before entry to prevent contamination.
Use designated cleanroom carts for transporting items. Ensure all personnel are trained in cleanroom etiquette to maintain the environment.
Regularly inspect equipment for cleanliness and functionality. Document any maintenance or cleaning performed to track compliance.
What is the significance of cleanroom airflow patterns?
Cleanroom airflow patterns are crucial for maintaining air quality and minimizing contamination. They help direct particles away from sensitive areas.
Laminar flow systems provide a uniform airflow, reducing turbulence and ensuring that contaminants are effectively removed. Proper airflow design is essential for compliance with ISO standards.
Understanding airflow helps in optimizing the cleanroom layout and positioning of equipment. It also aids in identifying potential contamination sources.
What are the common misconceptions about cleanrooms?
- Cleanrooms are completely free of contaminants; however, they are controlled environments with allowable limits.
- People often believe that all cleanrooms are the same; in reality, they differ based on class and application.
- Another misconception is that cleanroom attire is unnecessary; proper gowns are essential to minimize contamination risks.
- Lastly, some think regular cleaning suffices; ongoing monitoring and maintenance are crucial for cleanroom integrity.
How to use monitoring equipment in cleanrooms?
Monitoring equipment in cleanrooms is vital for ensuring compliance with cleanliness standards. Regularly check and calibrate devices for accurate readings.
Utilize particle counters, temperature, and humidity sensors to maintain optimal conditions. Data should be logged and reviewed to spot trends or deviations.
Train personnel on how to operate and interpret monitoring equipment. This knowledge is essential for quick responses to any environmental changes.
What are the common contaminants in a cleanroom?
Common contaminants in cleanrooms include:
- Particulate matter: dust, skin flakes, and fibers.
- Microbial contamination: bacteria, fungi, and viruses.
- Chemical contaminants: volatile organic compounds and residues from materials.
- Equipment off-gassing: emissions from materials used in cleanroom construction.
Understanding these contaminants helps in establishing effective control measures to maintain the cleanroom environment.
What types of industries use modular cleanrooms?
Modular cleanrooms are utilized across various industries, including:
- Pharmaceuticals: for drug manufacturing and testing.
- Biotechnology: to conduct sensitive research and development.
- Electronics: for semiconductor fabrication and assembly.
- Aerospace: to ensure precision in component manufacturing.
These industries depend on cleanrooms to maintain product integrity and compliance with regulatory standards.
What are the applications of ISO 5 cleanrooms?
ISO 5 cleanrooms are critical for several applications, such as:
- Pharmaceutical production: sterile drug formulation and filling processes.
- Biotechnology: cell culture and microbiological studies.
- Electronics manufacturing: assembly of sensitive electronic components.
- Aerospace: production of precision components that require contamination control.
These applications benefit from the stringent cleanliness levels provided by ISO 5 standards.
What are the key components of a modular cleanroom?
Key components of a modular cleanroom include:
- Wall panels: designed to minimize particle generation.
- HEPA filters: crucial for air purification and contamination control.
- Ceiling systems: often integrated with lighting and airflow management.
- Flooring: durable and easy to clean, ensuring a contamination-free surface.
- Doors and pass-throughs: designed to maintain airflow and minimize human traffic.
Each component plays a vital role in maintaining the cleanroom's integrity.
How to write a cleanroom SOP (Standard Operating Procedure)?
Writing a cleanroom SOP involves several steps. Start by defining the purpose and scope of the procedure. Clearly outline the responsibilities of personnel involved.
Next, detail the step-by-step procedures, including material handling, cleaning protocols, and equipment usage. Ensure the language is clear and concise for easy understanding.
Finally, include sections on training requirements, compliance monitoring, and revision history. Regularly review and update the SOP to reflect any changes in procedures or regulations.
How to evaluate cleanroom performance?
Evaluating cleanroom performance involves monitoring various factors. Regular particle counts should be conducted to ensure compliance with cleanliness standards.
Temperature and humidity levels must be monitored and maintained within specified ranges. Additionally, airflow patterns should be assessed for any anomalies or disruptions.
Documentation of all evaluations is crucial for compliance checks and audits. Review results periodically to identify trends or areas for improvement.
How to select the right modular cleanroom supplier?
Choosing the right modular cleanroom supplier requires careful consideration. Start by evaluating their experience and expertise in cleanroom design.
Review customer testimonials and case studies to assess their reliability and quality of work. It’s also essential to compare product offerings, including materials and technology used.
Finally, considerfactors like customer support, warranty, and after-sales service. A supplier that provides comprehensive support can ensure long-term success in maintaining your cleanroom.
How to choose the right flooring for an ISO 5 cleanroom?
Selecting the right flooring for an ISO 5 cleanroom involves several key considerations. The flooring must be non-porous and seamless to prevent contamination.
Materials like vinyl or epoxy resin are often recommended for their durability and ease of cleaning. Additionally, the flooring should be resistant to chemicals and static buildup.
Consider the slip resistance of the flooring to ensure safety for personnel. Regular maintenance should also be planned to maintain cleanliness and integrity over time.
What is the role of cleanroom furniture?
Cleanroom furniture plays a critical role in maintaining a contamination-free environment. It must be designed to minimize particle generation and be easy to clean.
Common types of cleanroom furniture include workbenches, storage cabinets, and seating. All furniture should be made from non-porous materials to prevent contamination.
Properly designed furniture aids in efficient workflow and organization within the cleanroom. It also supports compliance with cleanroom standards and regulations.
How to prevent cross-contamination in a cleanroom?
Preventing cross-contamination in a cleanroom requires strict adherence to protocols. Implementing a gowning procedure ensures that personnel do not introduce contaminants.
Establish designated areas for different processes to limit the movement of materials and personnel. Using separate tools and equipment for each area can further reduce risks.
Regular training of staff on contamination control measures is crucial. Additionally, routine cleaning and monitoring protocols should be enforced to maintain a clean environment.
How to maintain humidity levels in ISO 5 cleanrooms?
Maintaining humidity levels in an ISO 5 cleanroom is essential for compliance and product integrity. Utilize HVAC systems equipped with humidity control features.
Regularly monitor humidity levels using calibrated sensors. Ideally, maintain levels between 30% and 60% relative humidity to prevent static and contamination issues.
Schedule routine maintenance of the HVAC system to ensure optimal performance. Adjust settings based on seasonal changes to maintain consistent humidity levels.
How to conduct a cleanroom risk assessment?
Conducting a cleanroom risk assessment involves several steps. Begin by identifying potential contamination sources, including personnel, equipment, and materials.
Evaluate the likelihood and impact of each risk, considering the specific cleanroom environment and processes. Develop mitigation strategies to address identified risks effectively.
Document all findings and regularly review the assessment to accommodate changes in processes or regulations. Continuous monitoring and improvement are crucial for maintaining cleanroom integrity.
What are the regulatory requirements for cleanrooms?
Regulatory requirements for cleanrooms vary by industry but generally include adherence to specific ISO standards. Compliance with ISO 14644 outlines cleanroom classification based on particle count.
Pharmaceutical and biotechnology industries often follow Good Manufacturing Practices (GMP) to ensure product safety and quality. Environmental monitoring and documentation are essential components of compliance.
Regular audits and inspections by regulatory bodies may also be required to ensure ongoing adherence to standards. Staying informed about changes in regulations is vital for maintaining compliance.
What is the typical size of an ISO 5 cleanroom?
The typical size of an ISO 5 cleanroom can vary based on its application and requirements. Common sizes range from small units of around 100 square feet to larger facilities exceeding 1,000 square feet.
Factors influencing size include the number of personnel, equipment needs, and workflow design. It's essential to ensure adequate space for operations while maintaining air circulation and cleanliness.
Custom designs may be necessary for specific processes, allowing for flexibility in space utilization. Consulting with cleanroom design experts can help optimize the layout for efficiency and compliance.
What is the importance of cleanroom training?
Cleanroom training is vital for all personnel to understand contamination control protocols. Proper training ensures that staff follow established procedures, minimizing the risk of contamination.
Training programs should cover gowning procedures, equipment usage, and emergency protocols. Regular refresher courses can help maintain awareness of best practices and regulatory changes.
An informed workforce contributes significantly to the overall integrity of the cleanroom environment. Investing in training fosters a culture of cleanliness and compliance within the organization.
How to design a cleanroom for biological applications?
Designing a cleanroom for biological applications requires careful consideration of specific needs. First, select an appropriate classification, such as ISO 5 or higher, to ensure sterility.
Implement features like controlled airflow, dedicated zones for different processes, and adequate waste disposal systems. Additionally, ensure surfaces are non-porous and easy to sanitize.
Regular monitoring of environmental conditions, including temperature and humidity, is crucial. Collaborate with experts in biological processes to tailor the design to specific operational requirements.
Factory Production Workshop Video
Factory Photo
Product Packaging And International Logistics
Product International Certification
Find Other Common Equipment Recommendations
-
Modular CleanRoom
US$9000-10000 USD/Unit
Min. Order:1 Set -
Air Shower
US$1000.00-5000.00 USD/Unit
Min. Order:1 Set -
Downflow Booth
US$3000-6000 USD/Unit
Min. Order:1 Set -
Clean bench
US$600-2000 USD/Unit
Min. Order:1 Set -
Air Filter
US$3-50 USD/Unit
Min. Order:1 Set -
Cleanroom Wall Panels
US$10-20 USD/sq.
Min. Order:1 Set -
Pass Box
US$200-500 USD/Unit
Min. Order:1 Set -
FFU
US$135-350 USD/Unit
Min. Order:1 Set -
Fume Hood
US$700-1500 USD/Unit
Min. Order:1 Set -
Cleanroom HVAC
US$5000-20000 USD/Unit
Min. Order:1 Set -
Clean room floor
US$5-20 USD/Sq.
Min. Order:1 Set -
Clean room ceiling
US$
Min. Order:1 Set