4 x 4M ISO 5 Modular Cleanroom
Reference Price:US$9500-15000

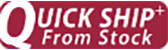

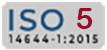
Cleanroom
4 x 4M ISO 5 Modular Cleanroom
Choose your installation & validation options below
Quantity:
Choose your Cleanroom frame structure material
Quantity:
Choose your Cleanroom Wall enclosure materials
Quantity:
Choose your Temperature requirements
Quantity:
Choose your humidity requirements
Quantity:
Choose your Explosion-proof requirements
Quantity:
Summary
4 x 4M ISO 5 Modular Cleanroom
Validation
Installation & Validation
Find Similar Products
-
5 x 10M ISO 5 Modular Cleanroom
US$20000-60000 USD/Set
Min. Order:1 Set -
6 x 6M ISO 5 Modular Cleanroom
US$20000-60000 USD/Set
Min. Order:1 Set -
6 x 8M ISO 5 Modular Cleanroom
US$20000-60000 USD/Set
Min. Order:1 Set -
6 x 10M ISO 5 Modular Cleanroom
US$20000-60000 USD/Set
Min. Order:1 Set -
5 x 6M ISO 5 Modular Cleanroom
US$20000-60000 USD/Set
Min. Order:1 Set -
5 x 7M ISO 5 Modular Cleanroom
US$20000-60000 USD/Set
Min. Order:1 Set
Cleanrooms Detail
An ISO 5 modular cleanroom is a controlled environment that meets stringent cleanliness standards as defined by the International Organization for Standardization (ISO). It is designed to maintain a maximum allowable particle concentration of no more than 3,520 particles per cubic meter for particles ≥0.5 micrometers in size.
Cleanroom Project Scope(from structure, HVAC,electric to autoc ontrol) | 1. Cleanroom Structure: Wall Panel, Ceiling Panel, Windows, Doors, Fttings, Flooring |
2. HVAC: AHU, Chiller, dehumidifier, Ducting, Piping, etc. | |
3. Electric: Lighting, Switch, Cables, Wires, Power Distribution Cabinet, etc | |
4. Auto- control: PLC Controller, Sensors for Humidity and Temperature, Control Panel | |
5. Process Piping System: Gas, Water Pipeline | |
Equipment | Air shower, Cargo shower, Mist shower, Dynamic pass box, Static pass box, Sampling booth,Weighing booth, Dispensing booth, |
Medicine stability test chamber, isolator, VHP sterilizer,Biological safety chamber, FFU, LAF, etc. | |
Temperature | 21-27*C (or as per required) |
Humidity | 30-60°C (or as per required) |
Application | Pharmaceutical factory, hospital, medical device factory, electronics factory, food factory,cosmetics factory, etc. |
Qualification Documents | CE GMP ISO |
Full Service | FAT and SAT Service, Professional Consultation, Training, 24 hours technical support |
an ISO 5 modular cleanroom is essential for processes that require strict control of airborne particulate contamination to ensure product integrity and compliance with industry standards.
Cleanrooms Airflow
The airflow principle in an ISO 5 modular cleanroom is critical for maintaining the required cleanliness levels and ensuring that the environment remains free from contamination. Here are the key aspects of the airflow principle in an ISO 5 cleanroom:
Cleanrooms Installation
Cleanrooms Testing
Cleanroom testing is a series of tests performed on the interior environment of a cleanroom to verify that it meets specific cleanliness requirements. These tests usually involve the measurement of a number of parameters such as air cleanliness, temperature and humidity, air velocity and air volume, noise, illumination, etc. inside the clean room. The purpose of the testing is to ensure that the clean room is able to provide a stable and contamination-free environment during the production process.
FAQ
How to achieve ISO 5 cleanliness?
To achieve ISO 5 cleanliness, maintain a controlled environment. This includes proper airflow and filtration systems to reduce contamination.
Regular monitoring of particulates and microbial levels is essential. Implement strict gowning procedures to minimize human contamination.
What types of filters are used in ISO 5 cleanrooms?
ISO 5 cleanrooms typically use HEPA filters. These filters capture 99.97% of particles 0.3 microns and larger.
ULPA filters may also be used for higher cleanliness levels. Regular replacement and maintenance of filters are crucial for effectiveness.
How does pressure differential work in cleanrooms?
Pressure differentials prevent contamination by controlling airflow. A higher pressure inside the cleanroom compared to adjacent areas ensures that air flows inward.
This setup minimizes the ingress of unfiltered air and maintains cleanliness. Regular monitoring helps maintain the desired pressure levels.
How to calibrate cleanroom monitoring equipment?
Calibrating cleanroom monitoring equipment involves several steps. First, use certified calibration standards for accuracy.
Next, follow manufacturer guidelines for calibration procedures. Regularly schedule recalibration to ensure ongoing precision and compliance.
What are the regulatory requirements for cleanrooms?
Regulatory requirements for cleanrooms vary by industry. Common standards include ISO 14644 and cGMP regulations in pharmaceuticals.
Compliance involves regular audits, documentation, and validation processes. Adhering to these requirements ensures product quality and safety.
What are the benefits of a portable cleanroom?
Portable cleanrooms offer flexibility and mobility for various applications. They can be quickly set up and relocated as needed.
Additionally, they are often cost-effective for temporary projects. Their adaptability makes them ideal for diverse industries.
How to integrate automation in a modular cleanroom?
Integrating automation involves selecting appropriate technologies. Options include automated monitoring systems and robotics for material handling.
Ensure all automated systems are compatible with cleanroom standards. Training personnel on these technologies is essential for successful implementation.
What are the common contaminants in a cleanroom?
Common contaminants in cleanrooms include:
- Dust and particles
- Microorganisms
- Chemical vapors
Regular monitoring and strict protocols help control these contaminants.
What is the importance of cleanroom validation?
Cleanroom validation ensures compliance with cleanliness standards. This process verifies that the cleanroom meets its intended purpose.
Regular validation helps identify potential issues and maintains product quality. Documentation of validation results is essential for audits.
How to ensure compliance in an ISO 5 cleanroom?
Ensure compliance in an ISO 5 cleanroom by following established protocols. Regular audits and inspections help identify deviations.
Training staff on cleanroom procedures is crucial for maintaining standards. Consistent documentation of all processes aids in compliance efforts.
What are the best practices for cleanroom gowning?
Best practices for cleanroom gowning include:
- Using appropriate garments to prevent contamination.
- Following a specific gowning sequence to minimize exposure.
- Regularly inspecting garments for damage.
Adhering to these practices enhances overall cleanroom cleanliness.
What is the significance of a cleanroom logbook?
A cleanroom logbook documents all activities and changes. This includes maintenance, inspections, and personnel entries.
It serves as a critical tool for audits and compliance verification. Regular entries help track issues and ensure accountability.
What is the maximum allowable particle count in ISO 5?
The maximum allowable particle count in ISO 5 is:
- 3 particles ≥0.5 microns per cubic meter
- 0 particles ≥1.0 microns
- 0 particles ≥5.0 microns
These limits ensure a controlled environment for sensitive operations.
What are the best practices for cleanroom entry?
Best practices for cleanroom entry include:
- Following strict gowning procedures.
- Limiting access to authorized personnel only.
- Conducting air showers before entry.
These practices minimize contamination risks and maintain cleanroom integrity.
How to implement a cleanroom training program?
To implement a cleanroom training program, start by defining training objectives. Identify key topics relevant to cleanroom operations and compliance.
Develop training materials and schedule regular sessions. Assess staff understanding through evaluations and feedback.
What are ISO 5 cleanroom standards?
ISO 5 cleanroom standards specify the maximum allowable levels of airborne particulates. They detail cleanliness requirements and operational procedures.
Compliance with these standards ensures a controlled environment essential for sensitive processes. Regular validation and monitoring are necessary for adherence.
How to document cleanroom procedures?
Document cleanroom procedures by outlining each step clearly. Use concise language and include relevant diagrams if necessary.
Regularly review and update documentation to reflect current practices. Maintain a centralized repository for easy access by personnel.
How to write a cleanroom SOP (Standard Operating Procedure)?
To write a cleanroom SOP, begin by defining its purpose clearly. Outline the scope to specify who it applies to and what it covers.
Use a step-by-step format for easy understanding. Include necessary references and ensure the document### How to write a cleanroom SOP (Standard Operating Procedure)?
is reviewed and approved by relevant personnel. Regularly update the SOP to reflect changes in processes or regulations.
Train staff on the SOP to ensure compliance and understanding. Keep records of training for future reference.
What are the common challenges in modular cleanroom design?
Common challenges in modular cleanroom design include:
- Ensuring compliance with cleanliness standards.
- Managing space limitations and workflow efficiency.
- Integrating utilities while maintaining flexibility.
Addressing these challenges requires careful planning and collaboration with stakeholders.
How to evaluate cleanroom performance?
To evaluate cleanroom performance, monitor key metrics regularly. These include particle counts, airflow rates, and temperature/humidity levels.
Conduct routine audits and assessments to identify areas for improvement. Use data from evaluations to inform maintenance and operational adjustments.
Factory Production Workshop Video
Factory Photo
Product Packaging And International Logistics
Product International Certification
Find Other Common Equipment Recommendations
-
Modular CleanRoom
US$9000-10000 USD/Unit
Min. Order:1 Set -
Air Shower
US$1000.00-5000.00 USD/Unit
Min. Order:1 Set -
Downflow Booth
US$3000-6000 USD/Unit
Min. Order:1 Set -
Clean bench
US$600-2000 USD/Unit
Min. Order:1 Set -
Air Filter
US$3-50 USD/Unit
Min. Order:1 Set -
Cleanroom Wall Panels
US$10-20 USD/sq.
Min. Order:1 Set -
Pass Box
US$200-500 USD/Unit
Min. Order:1 Set -
FFU
US$135-350 USD/Unit
Min. Order:1 Set -
Fume Hood
US$700-1500 USD/Unit
Min. Order:1 Set -
Cleanroom HVAC
US$5000-20000 USD/Unit
Min. Order:1 Set -
Clean room floor
US$5-20 USD/Sq.
Min. Order:1 Set -
Clean room ceiling
US$
Min. Order:1 Set