4 x 5m ISO 6 Softwall Cleanroom
Reference Price:US$8000.00-9500.00
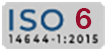
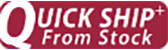
Cleanroom
4 x 5m ISO 6 Softwall Cleanroom
Choose your installation & validation options below
Quantity:
Choose your Cleanroom frame structure material
Quantity:
Choose your Cleanroom Wall enclosure materials
Quantity:
Choose your Temperature requirements
Quantity:
Choose your humidity requirements
Quantity:
Choose your Explosion-proof requirements
Quantity:
Summary
4 x 5m ISO 6 Softwall Cleanroom
Validation
Installation & Validation
Find Similar Products
-
5 x 6 ISO 6 Softwall Cleanroom
US$4000-15000 USD/Set
Min. Order:1 Set -
5 x 5m ISO 6 Softwall Cleanroom
US$4000-15000 USD/Set
Min. Order:1 Set -
4 x 6m ISO 6 Softwall Cleanroom
US$4000-15000 USD/Set
Min. Order:1 Set -
4 x 5m ISO 6 Softwall Cleanroom
US$4000-15000 USD/Set
Min. Order:1 Set -
4 x 4m ISO 6 Softwall Cleanroom
US$4000-15000 USD/Set
Min. Order:1 Set -
3 x 6m ISO 6 Softwall Cleanroom
US$4000-15000 USD/Set
Min. Order:1 Set
Cleanrooms Detail
ISO 6 softwall cleanrooms maintain a controlled environment with a maximum of 3,520 particles per cubic meter. They feature flexible wall systems and advanced HVAC controls, making them ideal for industries like pharmaceuticals, biotechnology, and electronics.
Maximum permissible particle number: 3,520 particles ≥ 0.5 micron per cubic meter
Temperature range: typically 20°C to 24°C
Humidity range: normally 30% to 60
Air exchange rate: 10 to 15 times per hour
ISO 6 softwall cleanrooms offer several key features that enhance their functionality and adaptability for various applications. These cleanrooms are designed for moderate cleanliness, providing a controlled environment that minimizes contamination risks in sensitive processes
Cleanrooms Airflow
In ISO 6 softwall cleanrooms, the airflow principle is crucial for maintaining cleanliness and controlling contamination. The following key elements describe this principle:
Unidirectional Flow: Clean air is supplied in a single direction from the ceiling to the floor, minimizing turbulence and particulate disturbance.
HEPA Filtration: High-Efficiency Particulate Air (HEPA) filters remove contaminants from the air before it enters the cleanroom, ensuring a high level of air purity.
Positive Pressure: The cleanroom is maintained at a higher pressure compared to adjacent areas, preventing outside contaminants from infiltrating the space.
Air Changes Per Hour (ACH): A specified number of air changes per hour is maintained to dilute and remove airborne particles, keeping the environment compliant with ISO 6 standards.
Return Air Systems: Air is usually returned through vents located at the bottom, facilitating proper circulation and ensuring uniform airflow throughout the cleanroom.
Cleanrooms Installation
ISO 6 Softwall Cleanrooms Installation Steps
Site Preparation: Evaluate the installation area for dimensions and utility access. Ensure the space meets cleanroom requirements.
Framework Assembly: Assemble the cleanroom framework, including support structures and flexible wall panels designed for easy maintenance.
Component Installation: Install essential components such as HEPA filters, lighting, and airflow systems to ensure compliance with ISO 6 standards.
Testing and Verification: Conduct rigorous testing of airflow, particle counts, and overall performance to confirm the cleanroom meets ISO 6 cleanliness requirements.
Staff Training: Train personnel on operating procedures and maintenance protocols to ensure effective cleanroom operation.
Cleanrooms Testing
ISO 6 softwall cleanroom testing is essential to ensure that the environment meets the required cleanliness standards and operates effectively. Below are the key aspects of testing and features associated with ISO 6 softwall cleanrooms.
Key Features of ISO 6 Softwall Cleanroom Testing:
Particle Counting:
Regular monitoring of airborne particles to ensure compliance with ISO 6 limits (maximum 3,520 particles per cubic meter for ≥0.5 micrometers).
Airflow and Air Changes:
Assessment of airflow rates and air changes per hour to maintain optimal conditions and prevent contamination.
Temperature and Humidity Control:
Continuous monitoring of temperature and humidity levels to ensure they remain within specified ranges (typically 20°C to 24°C and 30% to 60% humidity).
Pressure Differential Testing:
Verification of pressure differentials between the cleanroom and adjacent areas to prevent contamination ingress.
These testing features are crucial for maintaining the integrity and operational efficiency of ISO 6 softwall cleanrooms, ensuring they provide a suitable environment for sensitive processes.
FAQ
1. What is the impact of cleanroom design on workflow?
Cleanroom design significantly influences workflow efficiency by dictating the flow of materials and personnel. An optimal layout minimizes cross-contamination risks and enhances productivity, enabling smooth transitions between different operational areas.
2. What are the advantages of using softwall cleanrooms?
Softwall cleanrooms provide flexibility in design and quick setup, making them ideal for varying operational needs. They allow for easy modifications and expansions while maintaining effective contamination control, which can be crucial for dynamic environments.
3. How to ensure compliance with cleanroom regulations?
Ensuring compliance with cleanroom regulations involves regular training and audits of personnel, equipment, and processes. Documentation of procedures and adherence to industry standards must be consistently maintained to meet regulatory requirements effectively.
4. What is the importance of cleanroom validation?
Cleanroom validation is essential to demonstrate that the facility consistently meets required standards for cleanliness and performance. This process helps ensure that operations are reliable and compliant, thereby reducing contamination risks and protecting product integrity.
5. How to conduct a cleanroom risk assessment?
Conducting a cleanroom risk assessment involves identifying potential contamination sources and analyzing existing control measures. By evaluating the likelihood and impact of various risks, effective strategies can be developed to mitigate them and enhance overall safety.
6. How to test cleanroom integrity?
Testing cleanroom integrity typically involves performing particle count measurements and airflow assessments. These tests help determine if the cleanroom is maintaining the required cleanliness levels and effectively containing contaminants within its environment.
7. What is the difference between cleanroom and controlled environment?
A cleanroom is specifically designed to limit airborne particles and contaminants, adhering to strict cleanliness standards. In contrast, a controlled environment may not have the same stringent requirements, focusing instead on regulating temperature, humidity, or other conditions.
8. What is the role of cleanroom barriers?
Cleanroom barriers serve to separate clean areas from potential contamination sources and facilitate controlled access. These barriers help maintain the integrity of the cleanroom environment while ensuring that personnel and materials can be managed effectively.
9. How to manage personnel flow in a cleanroom?
Managing personnel flow in a cleanroom involves establishing clear pathways and protocols for gowning and de-gowning. This structured approach minimizes contamination risks and ensures that personnel movements do not disrupt the controlled environment.
10. What are the differences between ISO classes?
ISO classes vary in terms of allowed particle counts, with lower classes representing stricter standards for cleanroom environments. Each class defines specific operational requirements that influence the design and functionality of cleanrooms across different industries.
11. What are the key components of a modular cleanroom?
Key components of a modular cleanroom include wall panels, ceiling systems, air filtration units, and HVAC systems. These elements are designed to work together to create a controlled environment that meets specific cleanliness and operational standards.
12. How to calculate airflow in a cleanroom?
Calculating airflow in a cleanroom involves determining the required air changes per hour based on the room's volume and cleanliness class. Proper airflow ensures efficient filtration and helps maintain the necessary environmental conditions for operations.
13. How to install a modular cleanroom?
Installing a modular cleanroom begins with site assessment and design finalization. Once components are assembled, integrating HVAC systems and conducting thorough inspections are crucial to ensure the facility meets cleanliness requirements before operation.
14. How to assess cleanroom performance metrics?
Assessing cleanroom performance metrics involves monitoring key indicators such as particle counts, airflow rates, and environmental conditions. Regular analysis of these metrics helps identify trends and areas for improvement, ensuring compliance with established standards.
15. How to measure contamination levels in a cleanroom?
To measure contamination levels in a cleanroom, utilize particle counters and surface sampling techniques. These methods provide quantitative data to evaluate cleanliness and determine if the cleanroom is meeting the required standards for operation.
16. What are the common cleanroom design mistakes?
Common cleanroom design mistakes include inadequate airflow patterns, poor layout, and insufficient consideration of personnel movement. Such errors can lead to contamination issues and inefficiencies that compromise the cleanroom’s intended functionality.
17. How to develop a cleanroom standard operating procedure?
Developing a cleanroom standard operating procedure requires identifying key processes and compliance requirements. Collaborate with stakeholders to create clear, concise guidelines that ensure all personnel understand their roles and responsibilities in maintaining cleanliness.
18. How to achieve ISO certification for a cleanroom?
Factory Production Workshop Video
Factory Photo
Product Packaging And International Logistics
Product International Certification
Find Other Common Equipment Recommendations
-
Modular CleanRoom
US$9000-10000 USD/Unit
Min. Order:1 Set -
Air Shower
US$1000.00-5000.00 USD/Unit
Min. Order:1 Set -
Downflow Booth
US$3000-6000 USD/Unit
Min. Order:1 Set -
Clean bench
US$600-2000 USD/Unit
Min. Order:1 Set -
Air Filter
US$3-50 USD/Unit
Min. Order:1 Set -
Cleanroom Wall Panels
US$10-20 USD/sq.
Min. Order:1 Set -
Pass Box
US$200-500 USD/Unit
Min. Order:1 Set -
FFU
US$135-350 USD/Unit
Min. Order:1 Set -
Fume Hood
US$700-1500 USD/Unit
Min. Order:1 Set -
Cleanroom HVAC
US$5000-20000 USD/Unit
Min. Order:1 Set -
Clean room floor
US$5-20 USD/Sq.
Min. Order:1 Set -
Clean room ceiling
US$
Min. Order:1 Set