5 x 6 ISO 6 Softwall Cleanroom
Reference Price:US$8000.00-9500.00
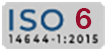


Cleanroom
5 x 6 ISO 6 Softwall Cleanroom
Choose your installation & validation options below
Quantity:
Choose your Cleanroom frame structure material
Quantity:
Choose your Cleanroom Wall enclosure materials
Quantity:
Choose your Temperature requirements
Quantity:
Choose your humidity requirements
Quantity:
Choose your Explosion-proof requirements
Quantity:
Summary
5 x 6 ISO 6 Softwall Cleanroom
Validation
Installation & Validation
Find Similar Products
-
5 x 6 ISO 6 Softwall Cleanroom
US$4000-15000 USD/Set
Min. Order:1 Set -
5 x 5m ISO 6 Softwall Cleanroom
US$4000-15000 USD/Set
Min. Order:1 Set -
4 x 6m ISO 6 Softwall Cleanroom
US$4000-15000 USD/Set
Min. Order:1 Set -
4 x 5m ISO 6 Softwall Cleanroom
US$4000-15000 USD/Set
Min. Order:1 Set -
4 x 4m ISO 6 Softwall Cleanroom
US$4000-15000 USD/Set
Min. Order:1 Set -
3 x 6m ISO 6 Softwall Cleanroom
US$4000-15000 USD/Set
Min. Order:1 Set
Cleanrooms Detail
Class 6 clean room standard
Class 6 clean room refers to a clean room in which the number of particles with a diameter greater than or equal to 0.5 microns per cubic meter of air does not exceed 6 particles. This level of clean room is mainly used for the cleanliness of certain requirements of industrial production, such as the assembly of certain electronic products, fine chemicals production.
Clean room principles
The design and construction of clean rooms need to follow a series of principles, including effective air filtration systems, appropriate temperature and humidity control, reasonable layout and material selection. In addition, the clean room also needs to meet the fire prevention, anti-static, anti-radiation and other related safety standards.
Technical parameters
The technical parameters of class 6 clean room mainly include the number of air changes, temperature and humidity control, noise control. The number of air changes is usually required 15-19 times per hour to ensure the freshness and cleanliness of the air. Temperature control is 20-22℃ in winter and 24-26℃ in summer, and humidity control is between 30-50% (winter) and 50-70% (summer).
Standard Requirements
The standard requirements for a Class 6 clean room include limits on the number of particles in the air, limits on the number of microorganisms, and differential pressure control. Specifically, the maximum allowable number of particles is no more than 3.5 million at 30.5 microns and no more than 20,000 at 5 microns. The number of planktonic bacteria does not exceed 50/m³, and the number of settled bacteria shall not exceed 1/ Petri dish.
Cleanliness level table
Cleanrooms Airflow
Ventilation System
The ventilation system of a clean room is one of its most important components. This system is designed to keep the air moving and reduce particles and other contaminants in the air. Through an efficient ventilation system, unclean air can be expelled and fresh, filtered air can be introduced. This design ensures the air quality inside the clean room, providing the necessary environmental safeguards for precision manufacturing and research activities.
Filters
The filters in a clean room are critical to ensuring the cleanliness of the air. Common filters include HEPA (High Efficiency Particulate Air) and ULPA (Ultra High Efficiency Particulate Air). These filters capture and remove minute particulate matter, ensuring that airborne particulate matter is maintained at an acceptable concentration level.
Air Quality Control
Cleanrooms typically use negative or positive pressure systems to control air quality. A negative pressure system maintains the indoor air pressure lower than the outside world, preventing the entry of contaminated air from the outside; on the contrary, a positive pressure system maintains the indoor air pressure higher than the outside world, avoiding the spread of internal air contamination to the outside. This design helps maintain a relatively closed and clean environment.
Clean Clothing
Operators working in a clean room are often required to wear special clean suits, including helmets, face masks, gloves and specialized clothing. This equipment minimizes contamination from personnel and maintains the cleanliness of the cleanroom.
Cleanrooms Installation
Preparation before installation
Before installing an FFU in the top of a clean shed, the clean shed must be thoroughly cleaned and wiped to ensure that the inside of the purified air conditioning system is free of dust. If a high-efficiency filter is to be installed in a technical mezzanine or suspended ceiling, the technical mezzanine or suspended ceiling also needs to be thoroughly cleaned and wiped.
FFU system testing
After the clean booth and FFU system have met the cleaning requirements, the FFU system should be tested. After 12 hours or more of continuous operation, clean the clean room again and immediately install the FFU matching high-efficiency filter.
Transportation and storage of FFU high-efficiency filter
The transportation and storage of FFU high-efficiency filters should be carried out according to the direction of the manufacturer's instructions. During transportation, it should be held lightly to prevent violent vibration and collision.
Inspection before installation
Before installing FFU high-efficiency filter, the package should be unpacked and inspected at the installation site, including whether the filter paper, sealant and frame are damaged; whether the side length, diagonal and thickness dimensions are in accordance with the requirements; whether there are burrs and rust spots on the frame (for metal frames); whether there is a certificate of conformity of the product, and whether the technical performance is in accordance with the design requirements. After that, check whether there is leakage, and those qualified by inspection and leakage detection should be installed immediately.
Allocation of filter resistance
The installation should be reasonably allocated according to the resistance of each filter. For unidirectional flow, between the filters of the same air outlet or air supply surface, the difference between the rated resistance of each filter and the average resistance of each filter should be less than 5%.
Cleanrooms Testing
The Importance of Clean Rooms
Clean rooms are widely used in industries such as semiconductor manufacturing, biomedical, and food processing, where the control of contaminants such as particles, microorganisms, and chemicals is particularly critical. As a result, the testing of clean rooms has become a key part of ensuring product quality.
Testing Standards
The cleanliness of a clean room is usually measured in terms of particle counts per cubic meter (PCM) or per cubic foot (PCF). This is regulated in detail by the Chinese standard ISO 14644 and the U.S. Federal Standard 209E. For example, the ISO 14644-1 standard specifies particle count limits for different cleanliness levels.
Testing Programs
Testing programs for clean rooms include, but are not limited to, temperature, humidity, airborne particles, fresh air volume, differential pressure, and airflow conditions. These tests are essential to ensure the environmental conditions in the clean room.
Testing Process
The testing process of a clean room usually includes on-site sampling, laboratory testing, and issuance of a test report. The testing period is usually 7 working days.
Testing Equipment
Commonly used testing equipment includes particle counters, differential pressure meters, anemometers, air volume hoods, noise meters, illuminance meters, temperature and humidity meters, etc.
FAQ
Factory Production Workshop Video
Factory Photo
Product Packaging And International Logistics
Product International Certification
Find Other Common Equipment Recommendations
-
Modular CleanRoom
US$9000-10000 USD/Unit
Min. Order:1 Set -
Air Shower
US$1000.00-5000.00 USD/Unit
Min. Order:1 Set -
Downflow Booth
US$3000-6000 USD/Unit
Min. Order:1 Set -
Clean bench
US$600-2000 USD/Unit
Min. Order:1 Set -
Air Filter
US$3-50 USD/Unit
Min. Order:1 Set -
Cleanroom Wall Panels
US$10-20 USD/sq.
Min. Order:1 Set -
Pass Box
US$200-500 USD/Unit
Min. Order:1 Set -
FFU
US$135-350 USD/Unit
Min. Order:1 Set -
Fume Hood
US$700-1500 USD/Unit
Min. Order:1 Set -
Cleanroom HVAC
US$5000-20000 USD/Unit
Min. Order:1 Set -
Clean room floor
US$5-20 USD/Sq.
Min. Order:1 Set -
Clean room ceiling
US$
Min. Order:1 Set