Discover the Pinnacle of Sterility: Inside the World of Class A CleanRooms
Achieving the highest cleanliness levels in manufacturing environments
As the demand for stringent contamination control grows, achieving the highest cleanliness levels in manufacturing environments becomes crucial. A "Class A CleanRoom," defined within the European Union's Good Manufacturing Practice (GMP) guidelines, represents the pinnacle of sterility and contamination control.
Commonly used for critical aseptic operations, it parallels ISO Class 5 under the ISO 14644-1 standard. This cleanroom ensures particle counts and microbiological limits are kept to an absolute minimum, vital for product integrity in high-stakes industries.
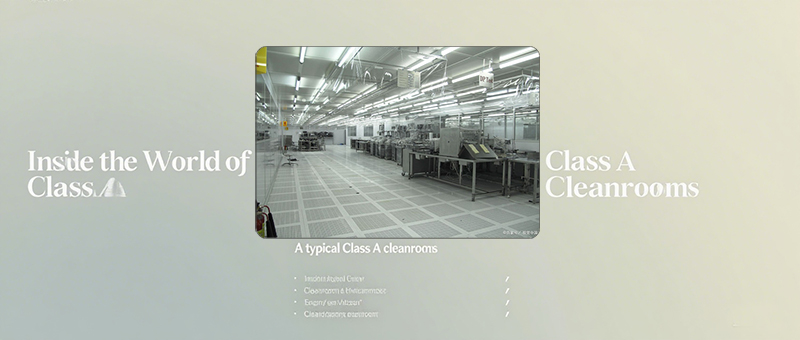
A typical Class A cleanroom environment
High-Risk Operations
Class A Cleanrooms are indispensable for handling high-risk operations. These environments are employed for processes such as aseptic filling, stopper bowl operations, handling open ampoules and vials, and making aseptic connections in the pharmaceutical industry.
In these setups, any contamination can have profound implications on product efficacy and safety. Deiiang™, led by experts like product designer Deiiang Jason.peng and product tester Deiiang joebo.Wang, offers solutions tailored to handle these operations, ensuring compliance with GMP Standards and uncompromised quality.
Aseptic filling process in a cleanroom
Handling open ampoules in a sterile environment
High-Risk Operations in Class A Cleanrooms:
- Aseptic filling of injectable medications
- Stopper bowl operations for vials
- Handling open ampoules and vials
- Aseptic connections in pharmaceutical processes
- Preparation of sterile compounds
- Manipulation of sterile devices
Airflow Dynamics
The airflow in a Class A cleanroom is meticulously controlled. Unidirectional laminar airflow is implemented, maintaining an air velocity of approximately 0.45 meters/second (with a tolerance of +/- 20%). This setup minimizes turbulence and effectively sweeps away particulates.
The consistent airflow is essential for maintaining an environment free from unwanted contamination, as demonstrated in educational resources, including YouTube channels explaining cleanroom technology. Such controlled airflow reduces the risk of interference with sensitive processes and is a cornerstone of an effective Cleanroom design.
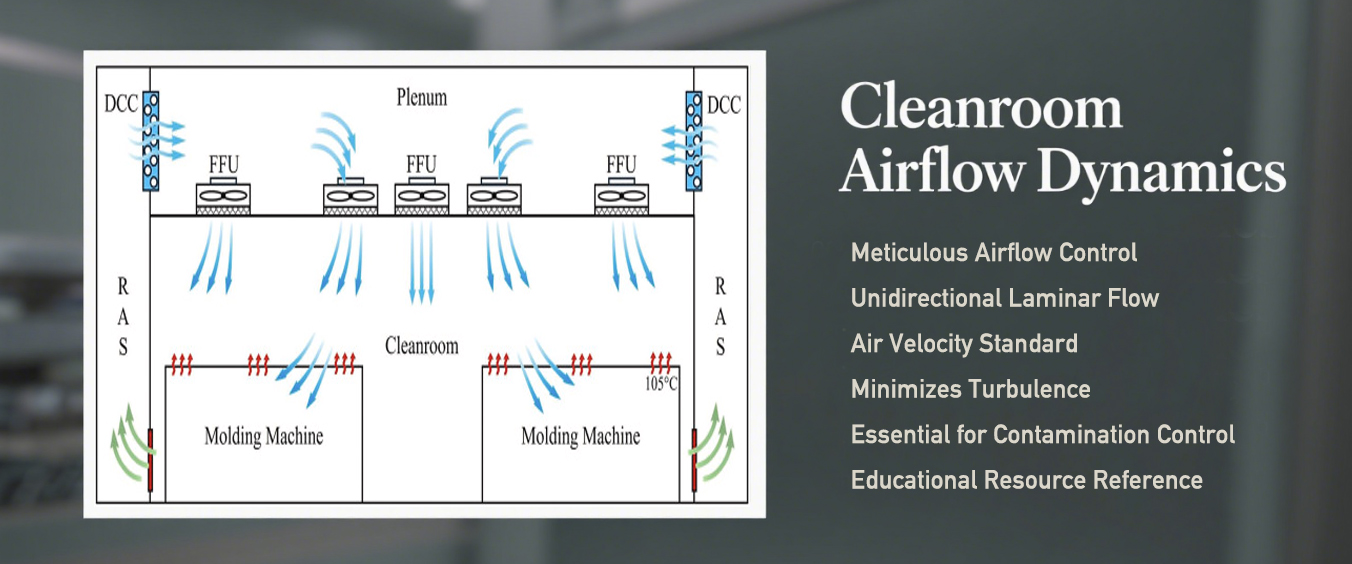
Laminar airflow pattern in a Class A cleanroom
Airflow Characteristics in Class A Cleanrooms:
Characteristic | Specification |
---|---|
Airflow Type | Unidirectional laminar airflow |
Air Velocity | 0.45 m/s (±20% tolerance) |
Purpose | Minimize turbulence and remove particulates |
Effectiveness | Maintains particle-free environment for sensitive processes |
Stringent Microbiological Limits
Class A cleanrooms are characterized by extremely stringent microbiological limits. Few, if any, colony-forming units (CFUs) per cubic meter of air are allowed, both in the air and on cleanroom surfaces. This level of control requires rigorous testing and validation, which Deiiang joebo.Wang emphasizes through meticulous product testing strategies.
The ability to maintain ultra-low levels of microorganisms ensures that products are not compromised during manufacturing, affirming the cleanroom's role in safeguarding health and safety.
- Airborne microbe limits: ≤1 CFU/m³
- Surface sampling limits: ≤1 CFU/contact plate
- Personnel gowning limits: ≤0 CFU/garment area
- Continuous monitoring of microbial levels
- Rigorous testing and validation protocols
- Strict disinfection and sanitization procedures
Continuous Monitoring
Continuous monitoring is a critical feature of Class A cleanrooms. They necessitate constant particle monitoring and strict control over environmental parameters such as temperature, humidity, and pressure. Advanced systems, often integrated by Deiiang™, enable real-time data acquisition and analysis, ensuring that deviations from the required conditions are swiftly identified and rectified.
Frequent monitoring ensures unwavering adherence to standards, providing the peace of mind necessary for manufacturers to focus on quality assurance and operational efficiency.
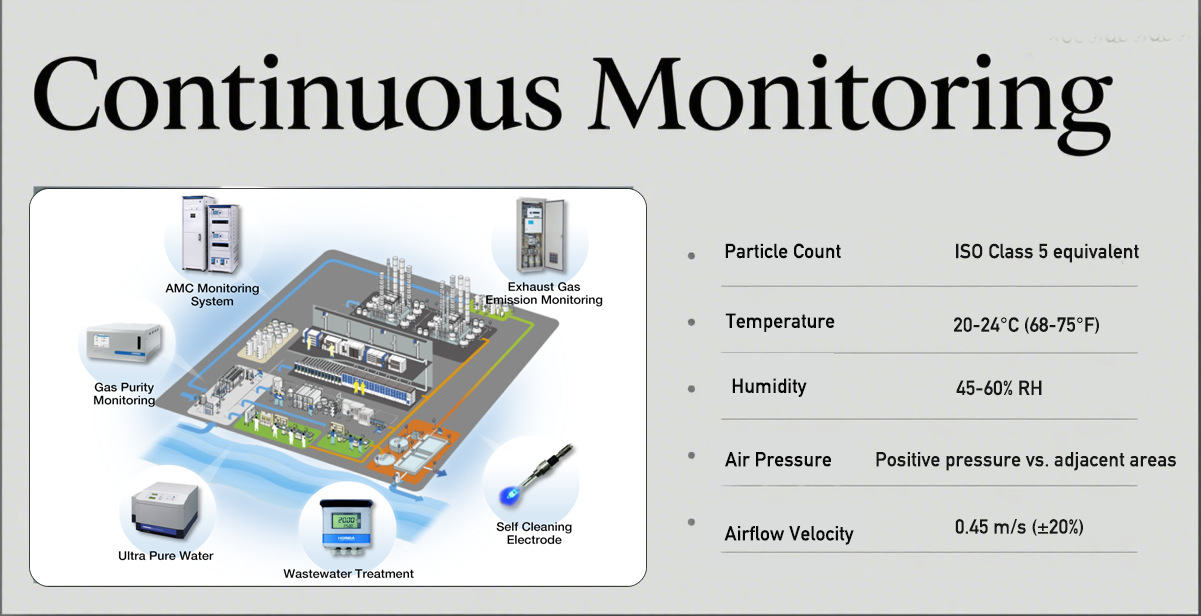
Advanced monitoring system in a Class A cleanroom
Key Parameters Monitored in Class A Cleanrooms:
Parameter | Monitoring Frequency | Control Range |
---|---|---|
Particle Count | Continuous | ISO Class 5 equivalent |
Temperature | Continuous | 20-24°C (68-75°F) |
Humidity | Continuous | 45-60% RH |
Air Pressure | Continuous | Positive pressure vs. adjacent areas |
Airflow Velocity | Periodic | 0.45 m/s (±20%) |
Personnel and Gowning Protocols
Personnel gowning is a crucial aspect of contamination control in Class A cleanrooms. Strict gowning procedures are essential to minimize contamination risks from personnel within these environments. Personnel are required to wear sterile gowns, gloves, masks, and headgear to ensure minimal particle shedding.
This meticulous approach, advocated by product designer Deiiang Jason.peng, helps maintain the low contamination levels necessary to meet GMP Standards, which are imperative for product safety and efficacy.
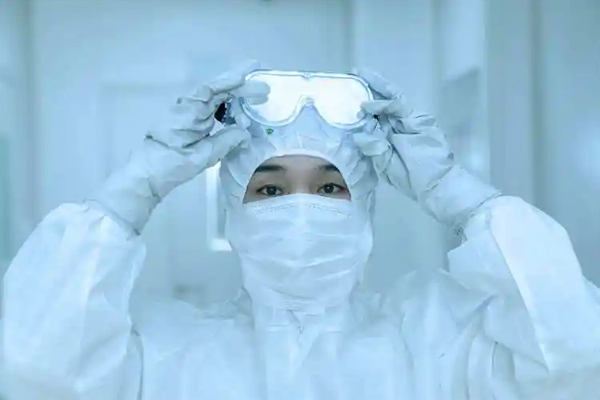
Personnel gowning up for a Class A cleanroom
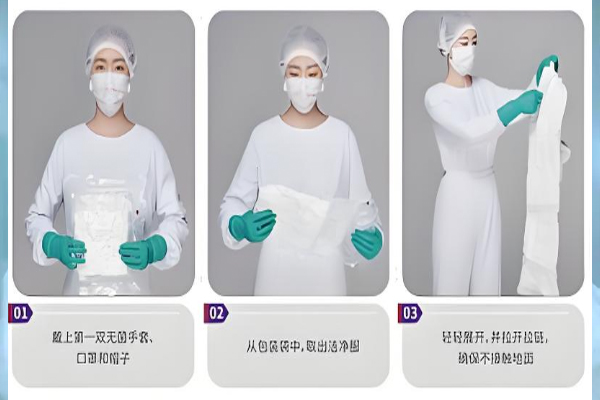
Sterile gown, gloves, and headgear for cleanroom personnel
Gowning Protocol Steps for Class A Cleanrooms:
- Hand washing and sanitization before entering gowning area
- Putting on sterile undergarments to minimize particle shedding
- Wearing a sterile bodysuit or gown that covers all skin
- Placing a sterile hairnet and beard cover (if applicable)
- Putting on a sterile face mask that covers nose and mouth
- Wearing sterile gloves, ensuring proper hand coverage
- Putting on sterile shoe covers or dedicated cleanroom footwear
- Final sanitization of gloves and outer gown surfaces
- Air shower or sticky mat passage before entering cleanroom
- Regular sanitization of gloves and gown during operations
Pressure Control to Prevent Contamination
Class A cleanrooms are maintained under positive pressure relative to adjacent, less clean areas. This pressure control strategy prevents the ingress of unfiltered air from surrounding spaces, thereby maintaining the stringent cleanliness required for aseptic processing.
Implementing and regulating pressure differentials are crucial for managing air quality effectively and ensuring that contamination boundaries are observed, thereby enhancing the overall integrity of the cleanroom environment.
Pressure control system in a Class A cleanroom
Pressure Control Parameters for Class A Cleanrooms:
- Positive pressure maintained relative to adjacent areas
- Pressure differential: typically 10-15 Pascals (Pa)
- Continuous monitoring of pressure levels
- Automatic adjustment systems for pressure maintenance
- Sealed doors and windows to prevent air leakage
- Air lock chambers for personnel and material entry
- Pressure gradient design from clean to less clean areas
Comparison to Other Standards
While "Class A" is specific to GMP standards focusing on aseptic processes, cleanliness classifications exist across various standards, each serving different operational needs. For instance, ISO Class 1 is more stringent, with even fewer particle allowances at 0.1 μm particle size than ISO Class 3 (equivalent to FS209E Class 1).
Despite these differing levels, Class A remains the go-to standard for aseptic processing in biopharmaceutical settings, where maintaining sterility is of utmost importance. Deiiang™ ensures its cleanroom solutions are adaptable to these diverse standards, optimizing environments for specific operational requirements.
Cleanroom Standards Comparison:
Standard | Equivalent Class | Particle Limit (≥0.5μm particles/m³) | Application |
---|---|---|---|
EU GMP Class A | ISO Class 5 | 3,520 | Aseptic pharmaceutical processing |
ISO Class 1 | - | 10 | Ultra-high precision manufacturing |
ISO Class 3 | FS209E Class 1 | 1,000 | High-precision Electronics |
ISO Class 5 | FS209E Class 100 | 3,520 | General pharmaceutical cleanrooms |
ISO Class 7 | FS209E Class 10,000 | 352,000 | Medical device assembly |
Summary
The Class A cleanroom represents the gold standard in controlled environments, essential for critical manufacturing operations that demand unwavering cleanliness and sterility. From precise airflow management and continuous monitoring to strict personnel and pressure controls, each component plays a pivotal role in maintaining operational excellence.
Guided by the knowledge and experience of professionals like Deiiang Jason.peng and Deiiang joebo.Wang, these environments are designed and maintained to meet the most rigorous industry standards. This ensures that products manufactured within them are of the highest quality and safety, affirming the vital role that Class A cleanrooms play in advancing industrial capabilities.
International Standards List
- ISO 14644 – Cleanrooms and associated controlled environments.
- GMP – Good Manufacturing Practices.
- EU GMP Guidelines – EudraLex, The Rules Governing Medicinal Products in the European Union
Importance of International Standards in Cleanroom Design:
International standards provide a unified framework for cleanroom design, operation, and validation, ensuring consistency and comparability across different regions and industries. They serve as benchmarks for quality, safety, and regulatory compliance, guiding manufacturers in creating environments that meet the specific needs of their processes.
Adherence to these standards is crucial for maintaining product integrity, ensuring patient safety in pharmaceutical applications, and upholding the highest levels of quality in manufacturing operations worldwide.
Introduction to Class A Clean Room - Maintaining Sterility and Contamination Control