Unlocking Purity: Understanding Pharmaceutical Clean Room Classification
Ensuring Contamination-Free Manufacturing Environments
Introduction
In the pharmaceutical industry, ensuring that products are manufactured in an environment free from contamination is paramount. This is where CleanRoom Classifications come into play. These classifications dictate the levels of cleanliness required in different manufacturing stages to meet stringent industry standards. By understanding and implementing these classifications, manufacturers can secure product safety and efficacy.
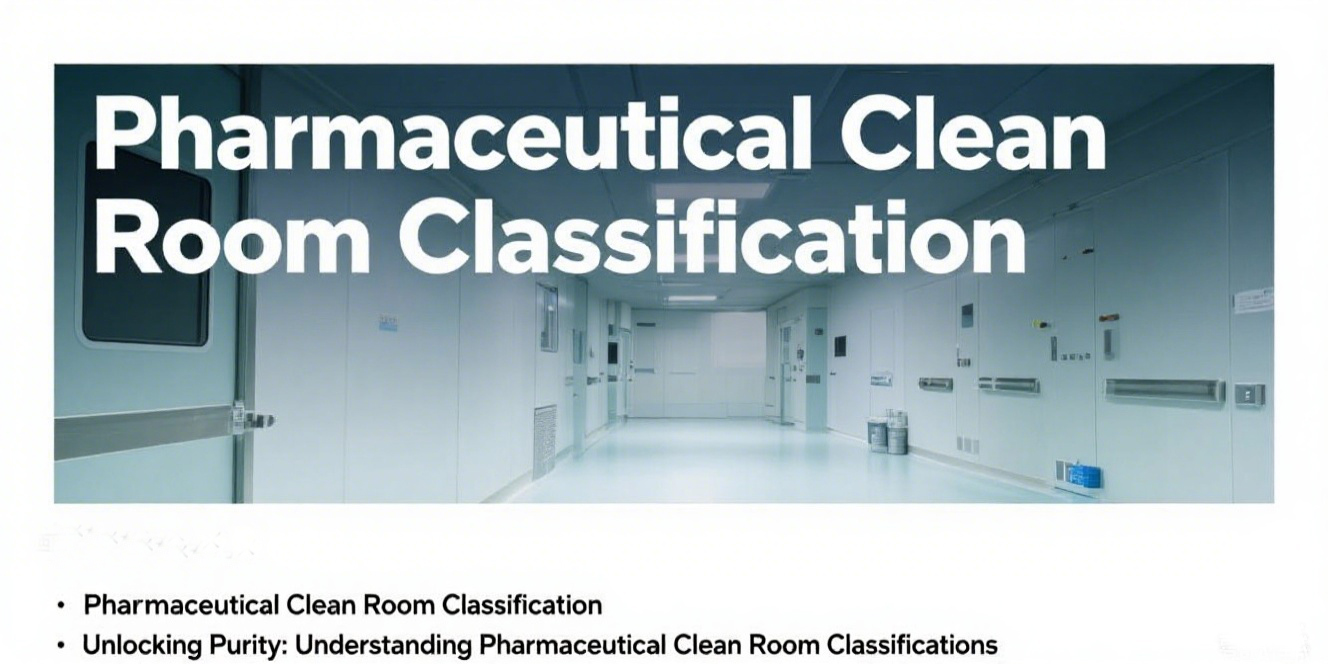
Modern pharmaceutical clean room facility
ISO 14644-1 Standards
The international standard iso 14644-1 serves as the cornerstone for cleanroom classification. It defines cleanliness levels from ISO Class 1, representing the cleanest environments, to ISO Class 9, which is the least clean. The classification is based on measuring airborne particle concentrations, such as particles ≥0.5 µm per cubic meter of air.
ISO Cleanroom Classifications
ISO Class | Particles ≥0.5μm/m³ | Application |
---|---|---|
ISO 5 | 3,520 | Ultra-clean environments for microElectronics |
ISO 6 | 3,5200 | Aseptic filling in pharmaceuticals |
ISO 7 | 352,000 | Weighing and dispensing areas |
ISO 8 | 35,200,000 | Less critical support areas |
EU GMP Grades: A, B, C, D
The European Union's GMP guidelines for sterile medicinal products categorize cleanrooms into Grades A, B, C, and D. Grade A, equivalent to ISO 5, is used in the most critical areas like aseptic filling. Grade B typically acts as a supportive environment for Grade A operations, ensuring seamless transitions.
EU GMP Grades Overview
Grade A: Equivalent to ISO 5, used for aseptic filling and critical operations
Grade B: Support environment for Grade A, with similar air quality standards
Grade C: Aligns with ISO 7, used for less critical manufacturing stages
Grade D: Corresponding to ISO 8, for general manufacturing areas
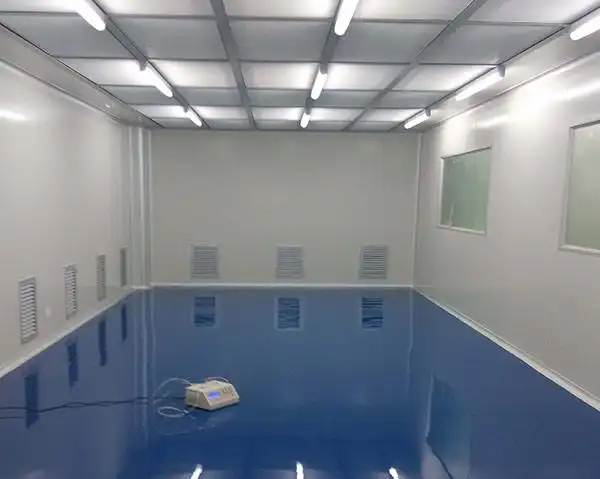
Grade A Clean Room for aseptic filling operations
ISO Classes Commonly Used in Pharmaceuticals
In pharmaceutical manufacturing, ISO classes 5 to 8 are the most commonly applied. ISO 5 environments cater to sterile procedures such as aseptic filling, providing the utmost cleanliness. ISO 6 is frequently used for transitional spaces, while ISO 7 accommodates areas like weighing and dispensing.
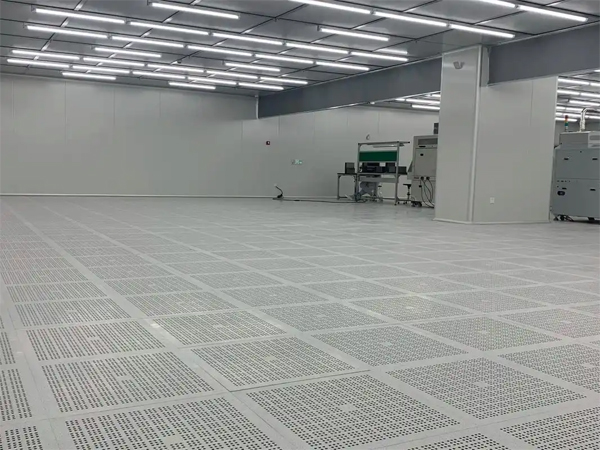
ISO 5: Aseptic Filling
Strictest cleanliness for sterile product handling
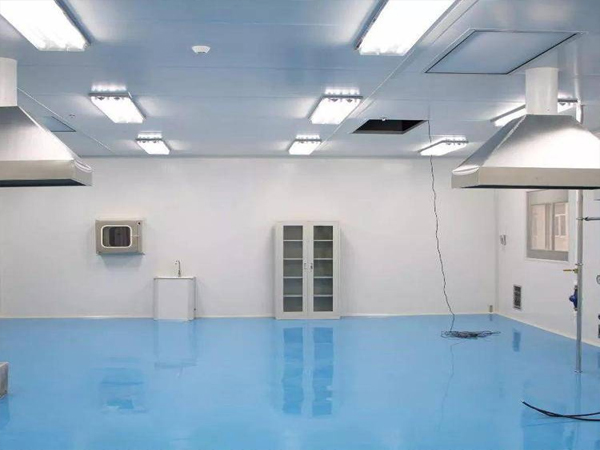
ISO 7: Weighing & Dispensing
Controlled environment for material preparation
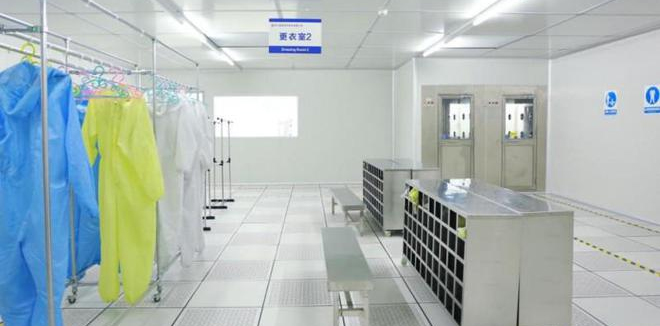
ISO 8: Gowning Areas
Hygiene control before entering critical zones
USP
The United States Pharmacopeia (USP) provides additional guidance with its
797USP
Focuses on sterile compounding preparations, requiring:
- ISO 7 Clean rooms for compounding
- HEPA filtration systems
- Strict microbial control measures
800USP
Addresses hazardous drug handling, specifying:
- ISO 8 gowning rooms
- Pressure differential controls
- Specialized personal protective equipment
Factors Influencing Cleanroom Classifications
Several factors determine cleanroom classifications, including the control of airborne particles and viable microorganisms. The room size, equipment presence, and personnel movements significantly affect the required air change rates and filtration levels.
1Airborne Particles
Measurement of particles ≥0.5μm/m³ is critical for classification, with stricter limits for higher cleanliness grades.
2Microbial Control
Viable microorganism counts must be controlled, especially in sterile manufacturing environments.
3Room & Equipment Factors
Room size, equipment heat output, and layout influence air change rates and filtration requirements.
4 Personnel Activity
Movement and number of personnel affect contamination levels, requiring proper gowning and protocol adherence.
Conclusion
Cleanroom classification is foundational to maintaining sterilized environments in pharmaceutical manufacturing. Through the application of ISO 14644-1 and EU GMP Standards, facilities are equipped to handle diverse contamination risks effectively. From the stringent requirements of a Grade A environment to the more relaxed, yet controlled, Grade D settings, these classifications ensure that products meet safety and efficacy standards.
Common Standards and References
- International Standards Organization. "Cleanrooms and associated controlled environments — Part 1: Classification of air cleanliness by particle concentration," ISO Standard No. 14644-1:2015 (2015).
European Commission. "The Rules Governing Medicinal Products in the European Union Volume 4 EU Guidelines for Good Manufacturing Practice for Medicinal Products for Human and Veterinary Use: Annex 1, Manufacture of Sterile Medicinal Products," Annex 1 (2022).
USP Compounding Compendium, "General Chapter
USP Compounding Compendium, "General Chapter