Introduction to Cleanroom Standards
While both ISO and GMP Standards regulate the quality and environment of cleanrooms, their focus differs significantly.
- ISO 14644 primarily sets guidelines for cleanliness levels based on particulate counts
- GMP (Good Manufacturing Practice) addresses broader operational processes
- GMP ensures environments, personnel, and equipment adhere to strict standards for safety and efficacy
D-Grade vs ISO 8 Cleanrooms
Cleanliness Standards
Both classifications maintain similar particulate thresholds:
- Allow up to 3,520,000 particles per cubic meter for 0.5μm particles
- D-Grade often implies more stringent operational controls
Note: This parity defines the level of cleanliness both classifications maintain.
Application Areas
Classification | Primary Industries |
---|---|
D-Grade | Pharmaceutical and biotechnology sectors |
ISO 8 | Electronics, aerospace, and some pharmaceutical applications |
D-Grade environments are critical where minor contamination impacts product quality and patient safety.
Gowning and Protocols
D-Grade Requirements
- Multiple layers including coveralls
- Gloves, masks, and shoe covers
- Strict protocols to prevent particulate transfer
ISO 8 Requirements
- Similar gowning to D-Grade
- May allow slightly less stringent requirements
- Tailored to specific operational context
ISO Classification Scale
Overview of ISO Standards
The ISO scale classifies cleanrooms based on air cleanliness levels:
- Ranges from ISO 1 (the cleanest) to ISO 9 (the least clean)
- Each class specifies particle limits
- Ensures suitable environments for sensitive processes
ISO 8 Characteristics
- Allows up to 3,520,000 particles/m³ for 0.5μm particles
- Suitable for electronics and some pharmaceutical applications
- Appropriate where moderate contamination control is necessary
ISO Class Comparison
ISO Class | Particles ≥0.5μm per m³ | Typical Applications |
---|---|---|
ISO 5 | 3,520 | Critical pharmaceutical processes |
ISO 7 | 352,000 | Sterile drug production, medical devices |
ISO 8 | 3,520,000 | Electronics assembly, packaging |
ISO 9 | 35,200,000 | General manufacturing |
ISO 7 vs ISO 8: Which is Better?
The appropriate classification depends entirely on your application requirements
ISO 7 Cleanrooms
- Particle Limit: 352,000 particles/m³
- Air Changes: Minimum 30 per hour
- Applications: Sterile pharmaceuticals, sensitive electronics, medical devices
- Key Features: HEPA filtration, positive pressure, strict environmental controls
Best for: High-precision applications where contamination risks are moderate
ISO 8 Cleanrooms
- Particle Limit: 3,520,000 particles/m³
- Air Changes: Typically 10-20 per hour
- Applications: Electronics packaging, non-sterile pharmaceuticals
- Key Features: Moderate filtration, less stringent environmental controls
Best for: Applications requiring contamination control but not ultra-pure environments
Key Consideration:
ISO 8 is not equivalent to Grade C. Grade c CleanRooms have stricter limits (352,000 particles/m³) and are used for sterile drug production.
ISO vs. GMP Standards Comparison
ISO 14644 Focus
- CleanRoom Classification based on particulate counts
- Physical cleanliness of the environment
- Testing and monitoring guidelines
- Airborne particle concentration thresholds
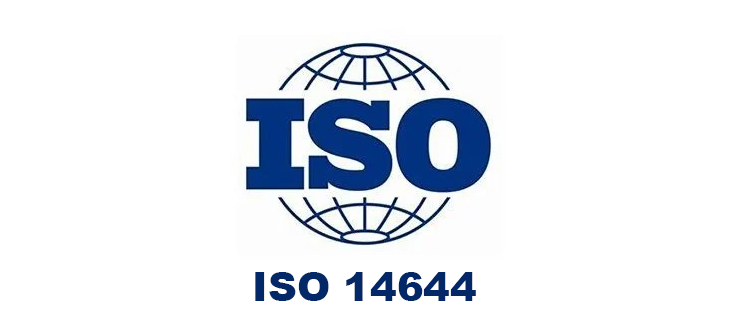
GMP Focus
- Broader operational processes
- Personnel behavior and training
- Equipment validation and maintenance
- Quality management systems
- Documentation and record keeping
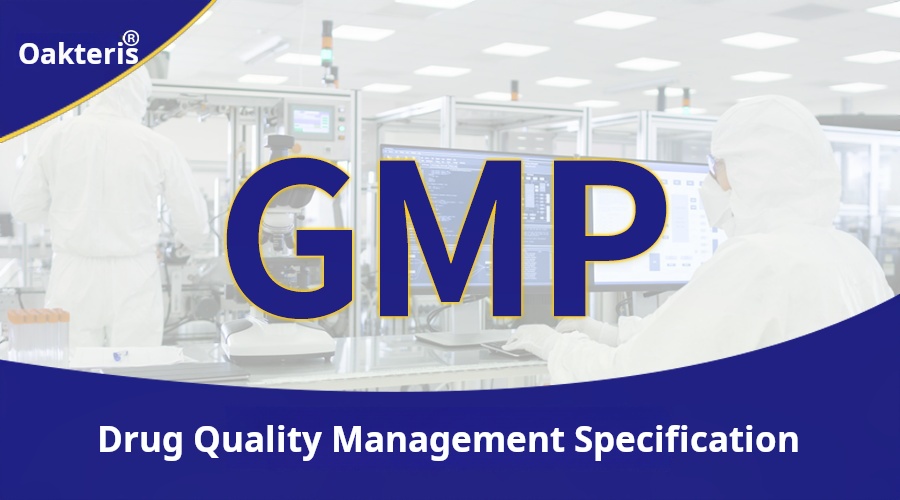
Complementary Relationship
While ISO focuses on the physical environment specifications, GMP addresses how that environment supports quality and safety in manufacturing processes. Most regulated facilities implement both standards to ensure comprehensive quality control.
Key Cleanroom Standards & Regulations
iso 14644-1
International standard for cleanroom classification based on particle counts.
iso 14644-2
Guidance for testing Cleanroom cleanliness and ongoing monitoring.
FDA 21 CFR Part 210 & 211
Regulations covering drug manufacturing and quality control.
EU GMP Annex 1
Specifications for manufacturing sterile medicinal products.
ISO 13485
Quality management standard for medical devices including cleanroom requirements.
Summary of Key Points
The relationship between D-Grade cleanrooms and ISO 8 cleanrooms is critical in understanding the standards of cleanliness required in various industries. Both classifications serve specific purposes in controlling contamination, yet they differ in their requirements and applications.
- D-Grade cleanrooms emphasize stringent operational controls for pharmaceutical applications
- ISO 8 provides a standardized classification for moderate cleanliness requirements
- ISO standards focus on particulate measurements while GMP covers broader operational quality
- Proper classification is essential for regulatory compliance and product safety
Cleanroom Standards Reference Guide | ISO vs. GMP | D-Grade vs. ISO 8 Classification
Information compiled from industry standards and regulatory documentation