What is Meant by Class 100 Clean room?
A Class 100 clean room is a controlled environment designed to maintain a low level of particulate contamination. Specifically, a Class 100 clean room allows no more than 100 particles per cubic foot of air that are 0.5 microns or larger in size. This classification is part of a broader CleanRoom Classification system defined by the Federal Standard 209E and ISO 14644-1. Clean rooms are essential in industries such as pharmaceuticals, biotechnology, aerospace, and semiconductor manufacturing, where even minute levels of contamination can adversely affect products and processes.
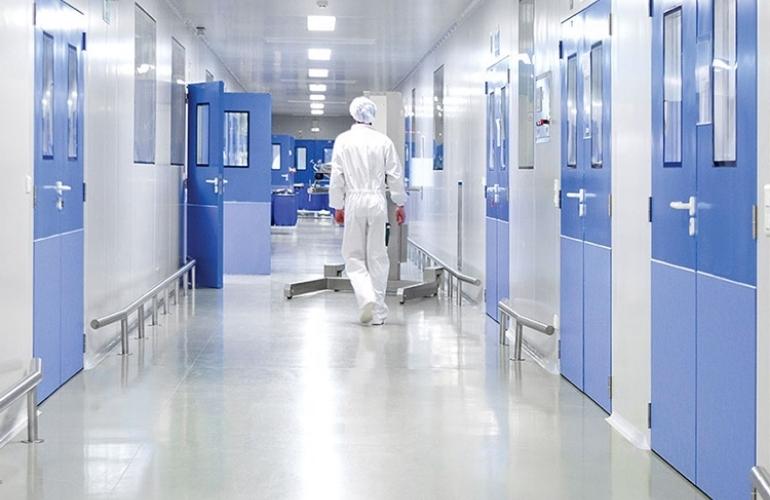
The concept of a Class 100 clean room is vital for protecting sensitive materials and ensuring high-quality production standards. To achieve this environment, strict regulations govern the design, construction, and operation of clean rooms.
Key Features of Class 100 Clean Rooms
- Air Filtration: Class 100 clean rooms are equipped with High-Efficiency Particulate Air (HEPA) filters, which can capture at least 99.97% of particles that are 0.3 microns in diameter. This filtration capability is crucial for minimizing airborne contaminants.
- Airflow and Exchange Rates: These clean rooms typically require a high rate of air changes to maintain cleanliness. The recommendation is to achieve at least 200 air changes per hour, ensuring that any particulate contamination is quickly removed from the environment.
- Temperature and Humidity Control: Class 100 clean rooms must also maintain specific temperature and humidity levels to ensure optimal working conditions and product stability. These parameters are crucial for industries where temperature-sensitive materials are handled.
- Monitoring Systems: Continuous monitoring of particulate levels, temperature, and humidity is essential in Class 100 clean rooms. Automated systems help maintain compliance with cleanliness standards and alert personnel to any deviations.
Relevant Standards and Guidelines
- iso 14644-1: International standard for cleanrooms and controlled environments, specifying cleanliness levels and testing methods.
- Federal Standard 209E: A standard that defines Clean Room Classifications based on airborne particulate contamination.
- iso 14644-5: Guidelines for the operation of cleanrooms, including aspects of cleanliness and contamination control.
What are the Specifications for ISO 5 Class 100?
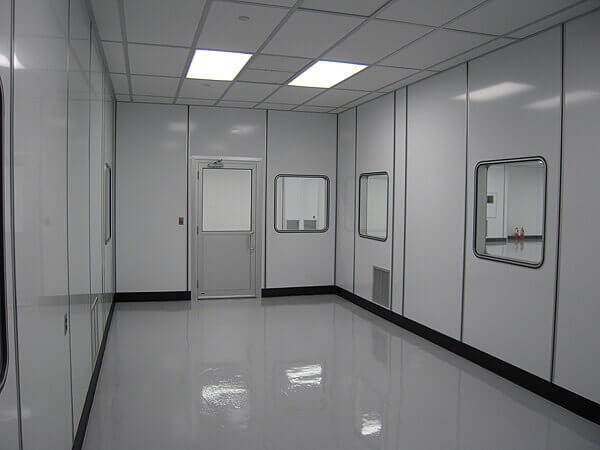
ISO5 cleanrooms allow a maximum of 3,520 particles per cubic meter (≥0.5 microns), essential for industries like pharmaceuticals and microelectronics. They maintain 20-25°C temperature, 30-60% humidity, and 100-200 air changes per hour, utilizing HEPA filters for compliance with ISO 14644-1.
What is the Temperature and Humidity in a Class 100 Cleanroom?
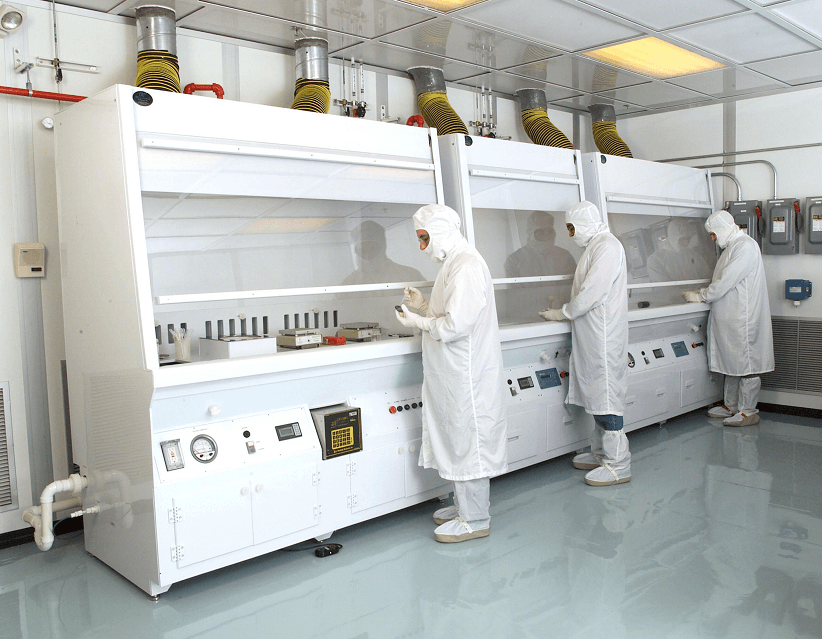
Maintaining optimal temperature and humidity levels in a Class 100 clean room is crucial for both product stability and personnel comfort. Typically, the temperature ranges from 20°C to 25°C (68°F to 77°F). This range is important for ensuring that temperature-sensitive materials do not degrade or alter in quality.
Temperature Control
The consistent maintenance of a temperature range ensures that processes remain stable. Fluctuations in temperature can lead to variations in material properties, affecting product quality and safety.
Humidity Management
Maintaining optimal humidity levels helps in reducing the risk of contamination and protecting sensitive materials from moisture-related damage. High humidity can lead to condensation, which poses a risk to equipment and products.
Monitoring Systems
Continuous monitoring of both temperature and humidity is essential for compliance with regulatory standards. Automated systems allow for real-time data collection and alerts for any deviations, ensuring immediate corrective actions can be taken.
These parameters are integral to maintaining a controlled clean room environment and ensuring compliance with industry standards.
How Much Air Change for Class 100 Cleanroom?

The air change rate is a vital factor for ensuring that the particulate levels in a Class 100 clean room remain within acceptable limits. Generally, a Class 100 clean room should achieve a minimum of 200 air changes per hour (ACH), although some applications may require even higher rates. This means that the entire volume of air in the room should be replaced 200 times every hour, which effectively dilutes and removes airborne contaminants.
Importance of High Air Change Rates
High air change rates are crucial in maintaining cleanliness. The rapid exchange of air helps reduce the concentration of particles in the room, thereby minimizing the risk of contamination. This is particularly important in environments where sensitive products are manufactured, such as pharmaceuticals and semiconductor devices. The goal is to ensure that the air quality remains at a level that meets the stringent requirements set forth by industry standards.
Airflow Design
The design of the airflow system is critical to achieving the desired air changes. Clean rooms often utilize laminar airflow systems, which provide a continuous flow of filtered air in a unidirectional pattern. This design helps to sweep contaminants away from critical areas and ensures that clean air reaches all parts of the room. Additionally, proper placement of HEPA filters and airflow diffusers is essential for optimal performance.
Monitoring and Validation
Continuous monitoring of airflow rates is necessary to ensure compliance with clean room standards. Instruments such as airflow meters and particle counters can be used to validate that the air change rates are being maintained. Regular testing and maintenance of the HVAC (Heating, Ventilation, and Air Conditioning) systems are also essential to ensure that the clean room operates effectively over time. Any deviations from the required air change rates must be addressed immediately to maintain the integrity of the controlled environment.
What is the Particle Size of a Class 100 Clean Room?
In a Class 100 clean room, the particle size that is of primary concern is typically 0.5 microns and larger. The classification allows for a maximum of 100 particles of this size per cubic foot of air. Understanding the implications of particle size is essential for maintaining the cleanliness of the environment.
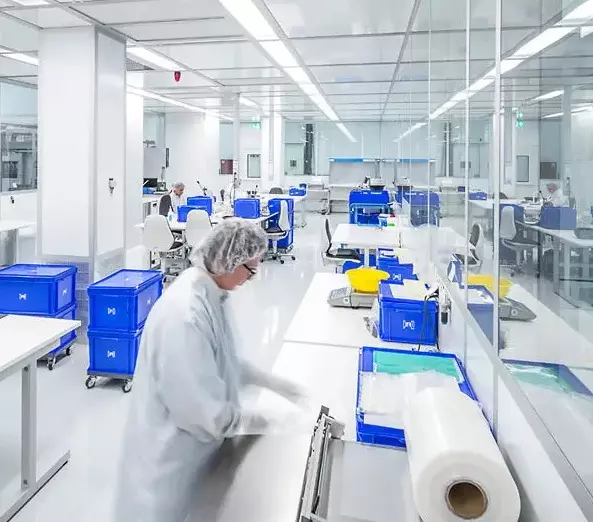
Critical Particle Size:
Particles of 0.5 microns are significant because they are small enough to penetrate most filtration systems and can settle on surfaces, potentially contaminating sensitive products.
Impact on Operations:
The presence of particles larger than 0.5 microns can adversely affect various operations within the clean room. In semiconductor fabrication, for instance, even a single particle can lead to defects in microchips, resulting in significant financial losses. Therefore, strict adherence to the Class 100 standards helps mitigate these risks.
Measurement and Control:
Continuous monitoring of particle counts is essential in a Class 100 clean room. Particle counters are used to measure the concentration of particulate matter in the air, and they should be calibrated regularly to ensure accuracy. Implementing effective cleaning protocols and using proper gowning procedures also help in controlling particle levels within the clean room environment.
How Do You Measure Cleanroom Class?
Measuring the cleanliness of a clean room involves several steps and methodologies to ensure compliance with established standards. The primary methods for determining the clean room class are based on particle count measurements and air change rates.
Particle Count Testing
The most common method for measuring clean room class is through particle count testing. This process involves using a particle counter to measure the number of airborne particles of various sizes in a specified volume of air. For instance, to classify a room as Class 100, the measurement must not exceed 100 particles per cubic foot that are 0.5 microns or larger.
Testing Procedure
The testing should be conducted under worst-case conditions, typically after the room has been fully operational for some time to ensure that the air quality reflects normal operating conditions. The measurements should be taken at various locations and heights within the clean room to obtain a comprehensive overview of the cleanliness.
Data Analysis and Reporting
Once the measurements are collected, they are analyzed against the standards outlined in ISO 14644-1 or Federal Standard 209E. The results are compiled into a report that includes particle counts, testing conditions, and recommendations for any necessary improvements. This documentation is crucial for regulatory compliance and for maintaining certification of the clean room.
What is the Ideal Temperature for a Cleanroom?
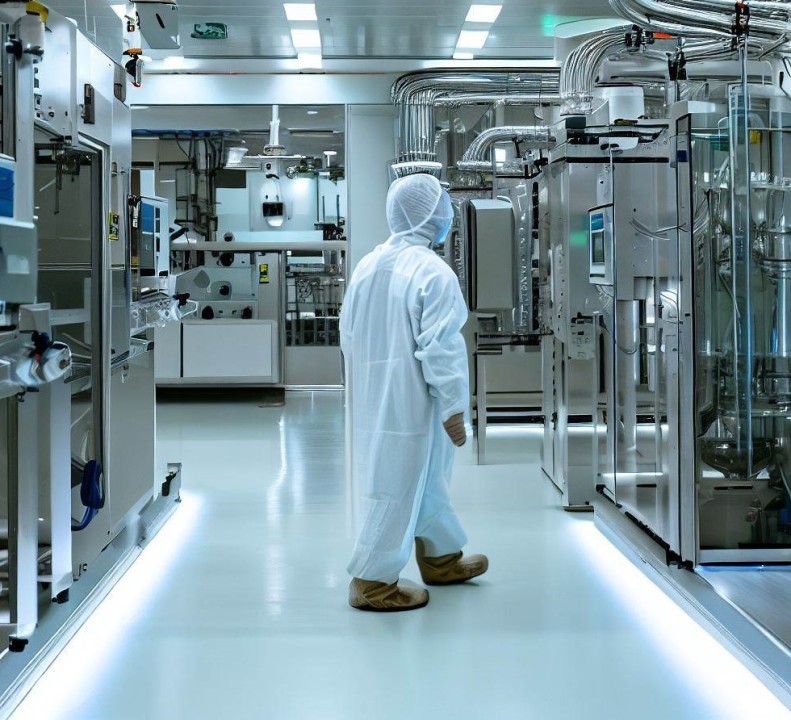
The ideal cleanroom temperature is maintained between 20°C and 24°C (68°F to 75°F) to ensure optimal conditions for sensitive materials in industries like pharmaceuticals and semiconductors. Humidity is controlled between 30% and 60% to prevent contamination, crucial for regulatory compliance.