Requirements for a Class 10,000 (ISO 7) Cleanroom
Ensuring Optimal Cleanliness
In various high-tech industries such as Semiconductors, pharmaceuticals, and aerospace, maintaining a controlled environment with minimal contamination is paramount. A Class 10,000 cleanroom, also known as an ISO 7 Cleanroom, is designed to uphold high cleanliness standards by restricting particle concentration in the air. This article details the key requirements necessary to achieve and maintain the ISO 7 classification effectively.
Air Quality Requirements
Particle Count
At its core, the defining characteristic of a Class 10,000 cleanroom is its particle count limit. The environment must contain no more than 10,000 particles measuring 0.5 micrometers or larger per cubic foot of air. This level of control ensures that critical processes are not compromised by airborne contaminants.
Air Changes and Filtration
Achieving a high rate of air changes per hour is essential for contaminant removal and maintaining air purity. Class 10,000 cleanrooms typically enforce between 60 and 90 air changes per hour, which helps in continual purging of particles from the environment.
Filtration Efficiency: HEPA filters play a pivotal role, tasked with removing airborne particles. These filters generally cover 15-25% of the ceiling area to ensure thorough air purification.
Design and Construction Considerations
Modular Construction
Class 10,000 cleanrooms frequently employ modular wall systems to enhance flexibility and streamline maintenance processes. This approach permits quick reconfiguration or expansion, catering to evolving needs without significant disruption.
Positive Pressure Maintenance
Maintaining positive pressure relative to adjacent areas is fundamental to preventing the ingress of contaminants. This pressure differential ensures that any leaks push air out instead of allowing contaminated air in, safeguarding internal processes.
Materials and Cleanability
Construction materials must be chosen for their non-shedding properties and ease of cleaning. Ensuring minimal particle generation and efficient cleanability supports ongoing compliance with air cleanliness standards.
Typical Class 10,000 Cleanroom Features
- ✓ Gowning room / air locks
- ✓ Product pass thru's
- ✓ Heat welded vinyl or epoxy floors
- ✓ Air conditioning for temperature control
- ✓ HEPA fan filter units
- ✓ Sealed CleanRoom lighting
- ✓ Magnahelic gauge for pressure monitoring
- ✓ Cleanroom bunny suits, booties and hoods
- ✓ Air showers for entry
- ✓ Sticky mats at entrance and exit
- ✓ Stainless steel bench
- ✓ Gown racks
- ✓ Stainless steel hands-free sinks
Class 10,000 Applications
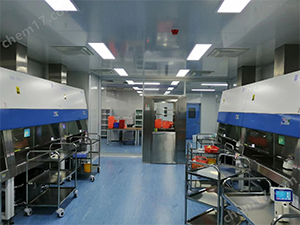
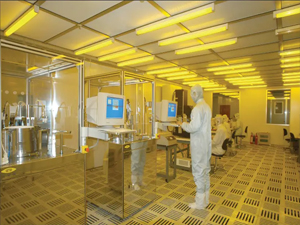
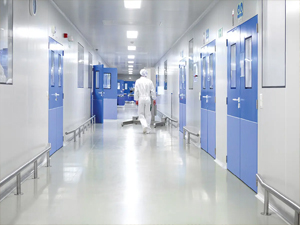
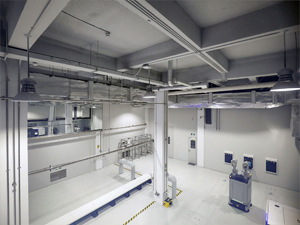
Conclusion
Building and maintaining a Class 10,000 (ISO 7) cleanroom involves adhering to strict air quality, filtration, and construction guidelines. Through efficient design and strategic use of materials, facilities can meet these standards and provide environments that support critical processes. By employing solutions from Deiiang™, guided by Deiiang Jason.peng, organizations can ensure their cleanrooms remain compliant, efficient, and adaptable to future needs.
Common Questions and Answers
A: It ensures continuous contaminant removal, maintaining air purity and protection for sensitive manufacturing processes.
A: They remove 99.97% of airborne particles, essential for keeping the environment within stratified cleanliness levels.
A: It allows for easy reconfiguration and scalability, which can adapt to changing operational demands.
A: By integrating cutting-edge filtration and construction materials into their Cleanroom designs, ensuring long-term operational excellence.
A: Positive pressure prevents outside contaminants from entering the cleanroom, maintaining a controlled internal environment.
References
- International Organization for Standardization. ISO 14644-1: Cleanrooms and Associated Controlled Environments.
- Deiiang™, Advanced Cleanroom Design and Implementation.
- American Society of Heating, Refrigerating and Air-Conditioning Engineers (ASHRAE), Standards for Cleanroom ventilation.
- U.S. Pharmacopeial Convention. USP Standards for Environmental Control in Cleanrooms.
- The Institute of Environmental Sciences and Technology (IEST), Recommended Practices for Cleanroom Construction and Operation.