A CleanRoom (simple clean room) is a specialized environment established for quick and convenient use, featuring various cleanliness levels and flexible space. It can be designed and produced according to specific needs, making it highly adaptable, easy to install, and quick to construct with the added benefit of being removable. Cleanrooms are often used to provide high cleanliness in local areas within a general-level cleanroom, helping to reduce costs through targeted upgrades.
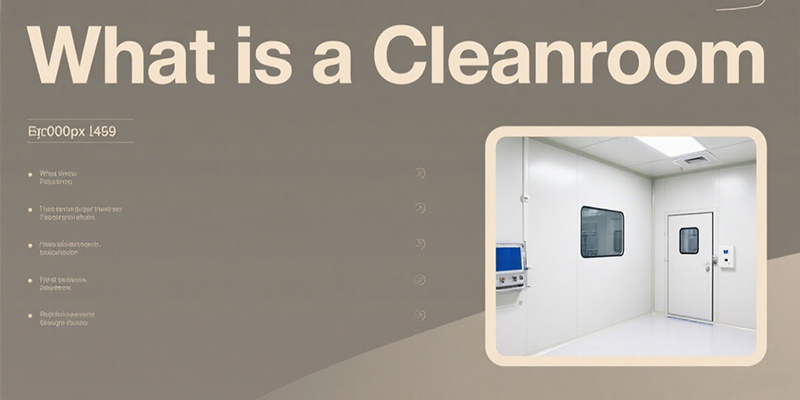
A typical ISO Class 7 Cleanroom environment
Cleanliness Level Standard Grading
The ISO cleanliness level standard is an international benchmark for measuring cleanliness, widely applied in cleanrooms, laboratories, Electronics industry, pharmaceutical industry, and food industry. As per ISO 14644-1, cleanliness levels are categorized from 1 to 9, each corresponding to a specific count of suspended particles in the air.
ISO Level | Particle Limit (≥0.1μm per m³) |
---|---|
ISO 1 | ≤10 |
ISO 2 | ≤100 |
ISO 3 | ≤1,000 |
ISO 4 | ≤10,000 |
ISO 5 | ≤100,000 |
ISO 6 | ≤1,000,000 |
ISO 7 | ≤10,000,000 |
ISO 8 | ≤100,000,000 |
ISO 9 | ≤1,000,000,000 |
ISO 7 Cleanroom Standards
ISO 7 cleanroom standards are defined by both particle concentration and air change rates. Here's a detailed breakdown:
Air Change Requirements
- 25-30 air changes per hour
- Complete air purification time after air exchange: ≤30 minutes
- Maintains a controlled environment with consistent particle removal
Particle Concentration Limits
- ≤10,000,000 particles ≥0.1μm per m³
- For 0.5μm particles: ≤3,500,000 per m³
- For 5μm particles: ≤20,000 per m³
100,000 Clean Room Purification Standard
The 100,000 clean room (equivalent to ISO 7) has specific purification standards to ensure environmental control:
Standard Category | Requirement |
---|---|
dust particles |
|
Microorganisms |
|
Differential Pressure |
|
ISO 7 Cleanroom Application Areas
ISO 7 Cleanrooms find extensive use in various industries where controlled environments are essential to ensure product quality and process integrity:
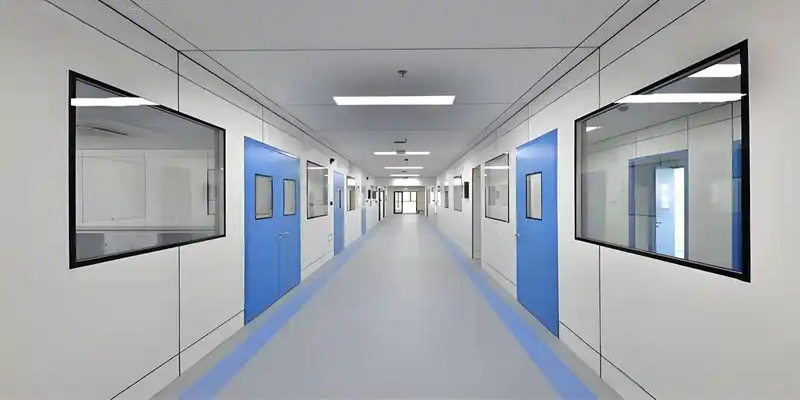
Laboratory
Used for parts of experimental areas requiring clean environments to prevent impurity contamination during experiments.
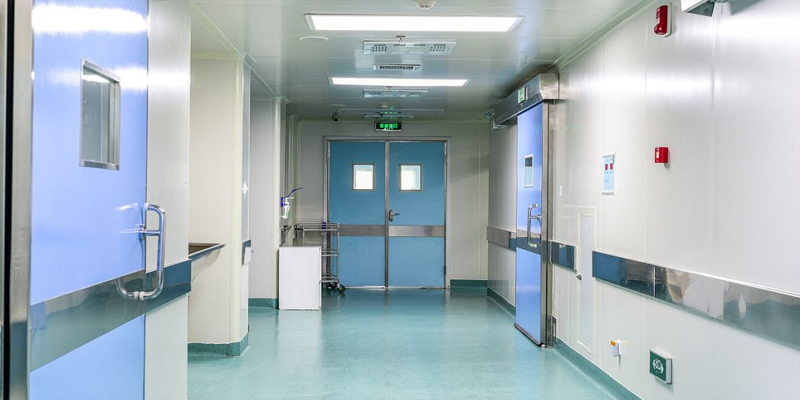
Medical Industry
Applied in operating rooms, clean laboratories, and clean pharmacies to reduce the risk of intraoperative infections.
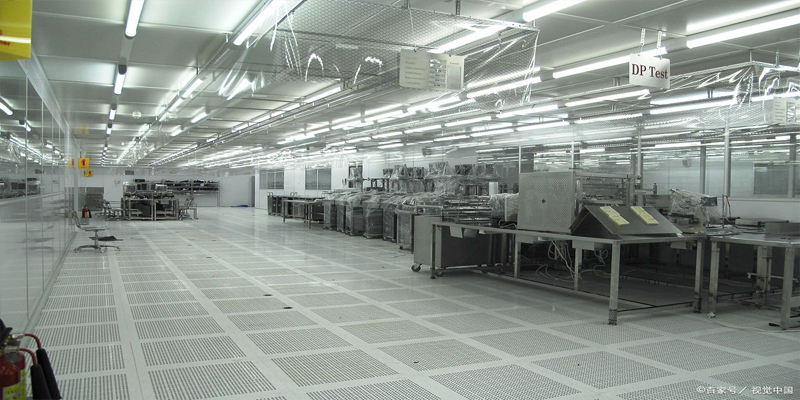
Electronic Industry
Widely used in the manufacturing process of electronic components to prevent dust and other impurities from contaminating products.
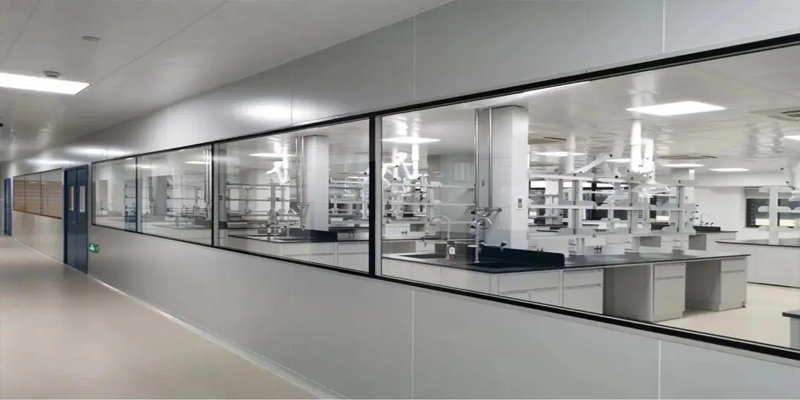
Pharmaceutical Industry
Used in drug packaging, preparation, and blending processes to ensure product cleanliness and quality requirements.
Principle of ISO 7 Cleanroom
The working principle of an ISO 7 cleanroom revolves around several key technologies and control mechanisms to maintain the required cleanliness level:
Air Filtration Technology
Air is filtered through multi-layer high-efficiency filters (HEPA and ULPA), effectively reducing the number of particles and microorganisms in the air.
Positive Pressure Maintenance
Maintaining positive pressure inside the cleanroom ensures air flows from inside to outside, preventing external contaminants from entering and ensuring air fully passes through filters.
Environmental Control
Precise control of internal parameters such as temperature, humidity, and static electricity to ensure stability within defined ranges, avoiding impacts on products and experiments.
ISO 7 Cleanroom Management Requirements
Effective management of ISO 7 cleanrooms is crucial to maintaining the required cleanliness levels and ensuring operational integrity:
Personnel Control
- Personnel must wear specialized clean suits
- Strict entry and exit procedures to follow
- Special training on cleanroom practices required
- Limited movement and specific behavioral guidelines
Material Transportation
- Materials kept dry and airtight during transport
- Strict control of temperature and humidity
- Specialized cleaning and decontamination procedures
- Designated transport routes and protocols
ISO Class 7 Cleanroom Guide © 2025