A Class 100,000 cleanroom, also known as an ISO 8 Cleanroom, is a controlled environment designed to maintain air cleanliness by limiting the number of airborne particles. In such a cleanroom, the particle count must not exceed 100,000 particles per cubic foot for particles 0.5 micrometers or larger. These cleanrooms are commonly used in industries like pharmaceuticals, biotechnology, and electronics, where moderate contamination control is required without the need for the strict conditions of more advanced classes. They balance efficiency and cost-effectiveness while providing a safe environment for sensitive processes and products.
What is a Class 100,000 Cleanroom?
A Class 100,000 cleanroom is an environment where the particulate count does not exceed 100,000 particles per cubic foot of air for particles 0.5 micrometers and larger. This classification is crucial in industries where a moderate level of cleanliness is permissible and necessary for certain stages of production but does not require the extreme cleanliness of higher-grade cleanrooms.
These environments are part of a broader CleanRoom Classification system that ensures each cleanroom is tailored to the specific needs of the industry it serves. Deining offers custom solutions to meet these requirements, ensuring that both design and operational efficiencies are maximized.
Class 100,000 Cleanroom Standards
The standards governing Class 100,000 cleanrooms, primarily outlined by ISO 14644-1, provide a comprehensive framework for maintaining air cleanliness. ISO standards have largely replaced older specifications like the US Federal Standard 209E, offering more detailed guidelines for global consistency in cleanroom classification.
In this framework, operators must ensure that the number of particles larger than a specified size remains below predefined thresholds. Implementing these standards involves sophisticated air filtration and ventilation systems, as offered by Deining, which designs systems to maintain air flow and filtration efficiency.
US FED Standard 209E Maximum Number of Particles
The US Federal Standard 209E was an early system used to classify cleanrooms by their airborne particulate levels. Under this standard, a Class 100,000 cleanroom would limit the amount of airborne particles that are 0.5 micrometers or larger to no more than 100,000 particles per cubic foot.
ISO 8 Cleanroom Particle Specifications
ISO 8 specifications extend the principles of Class 100,000 cleanliness to an international audience, providing uniformity across borders. In an ISO 8 cleanroom, particle concentration must not exceed 3,520,000 particles per cubic meter for particles 0.5 micrometers and larger.
Industrial Applications for Class 100,000 Cleanrooms
Class 100,000 cleanrooms find their applications across multiple industries, including pharmaceuticals, biotechnology, and electronics. These environments are particularly effective in stages of manufacturing where stringent contamination control is not necessary, but a controlled environment is still required.
Pharmaceutical Industry
Used in packaging and storage areas to support product safety without high costs.
Electronics Manufacturing
Supports assembly of components where moderate dust control is sufficient.
Biotechnology
Provides controlled environments for various production stages.
Affordable Class 100,000 Cleanroom design
Designing an affordable cleanroom involves careful balance between cost and functionality. Using modular systems can significantly reduce costs while maintaining flexibility in layout and design. Modular systems from Deining allow for scalable solutions that adapt over time without compromising on the standards required for a Class 100,000 cleanroom.
Material selection and efficient system integration play critical roles in keeping initial and operational costs down. By choosing cost-effective materials that do not compromise on durability and effectiveness, cleanroom environments can be maintained at optimal performance levels affordably.
Design Capabilities:
Category | Capabilities |
---|---|
![]() | Custom architectural solutions for cleanroom environments |
![]() | Robust structural engineering for cleanroom stability |
![]() | Airflow management systems design |
![]() | Specialized electrical systems for cleanrooms |
![]() | Heating, ventilation, and air conditioning systems |
![]() | Specialized flooring solutions for cleanroom environments |
![]() | Various cleanroom construction types and configurations |
ISO 8 Cleanroom Requirements
ISO Class 8 is one of the “dirtiest” cleanroom classifications, but these environments are still much cleaner than the average office space.
They use some advanced features, though less than cleanrooms with a stricter cleanliness classification, such as ISO 7, 6, 5, and below.
Entry into an ISO Class 8 Cleanroom does not require progression through cleaner spaces, as is usual for entering other higher-grade cleanrooms. However, implementing control measures to prevent contamination is still important.
Here are some of the basic requirements for these environments.
Airflow
Typically, they do not require unidirectional (laminar) airflow, which is a necessity for ISO 5 and stricter cleanrooms. Instead, they can operate with standard non-directional (turbulent) airflow systems. These systems are much cheaper, as maintaining unidirectional airflow can get expensive.

An air handling unit for a modular cleanroom.
Similarly, they can be either hardwall or softwall. Softwall cleanrooms are much cheaper than hardwall cleanrooms, but they only allow a single pass-through of air. This means that softwall cleanrooms do not support complex HVAC systems.
A softwall cleanroom.
Air Changes Per Hour
These cleanrooms require around 20 air changes per hour (ACPH), which, while much less than the requirements for an ISO 5 environment, still represents a high degree of fresh air, especially compared with a typical residential or office environment.
Environment | Air Changes Per Hour (ACPH) |
---|---|
ISO 8 Cleanroom | ~20 ACPH |
Normal Residential Space | 1-2 ACPH |
A high ACPH rate helps these spaces maintain particle limits by continuously removing and replacing air.
Ceiling Coverage
The requirement for ceiling coverage in these environments is less demanding compared to other cleanrooms. They typically require a ceiling coverage of about 15–25%.
(This percentage refers to the portion of the ceiling equipped with filters through which clean air is circulated.)
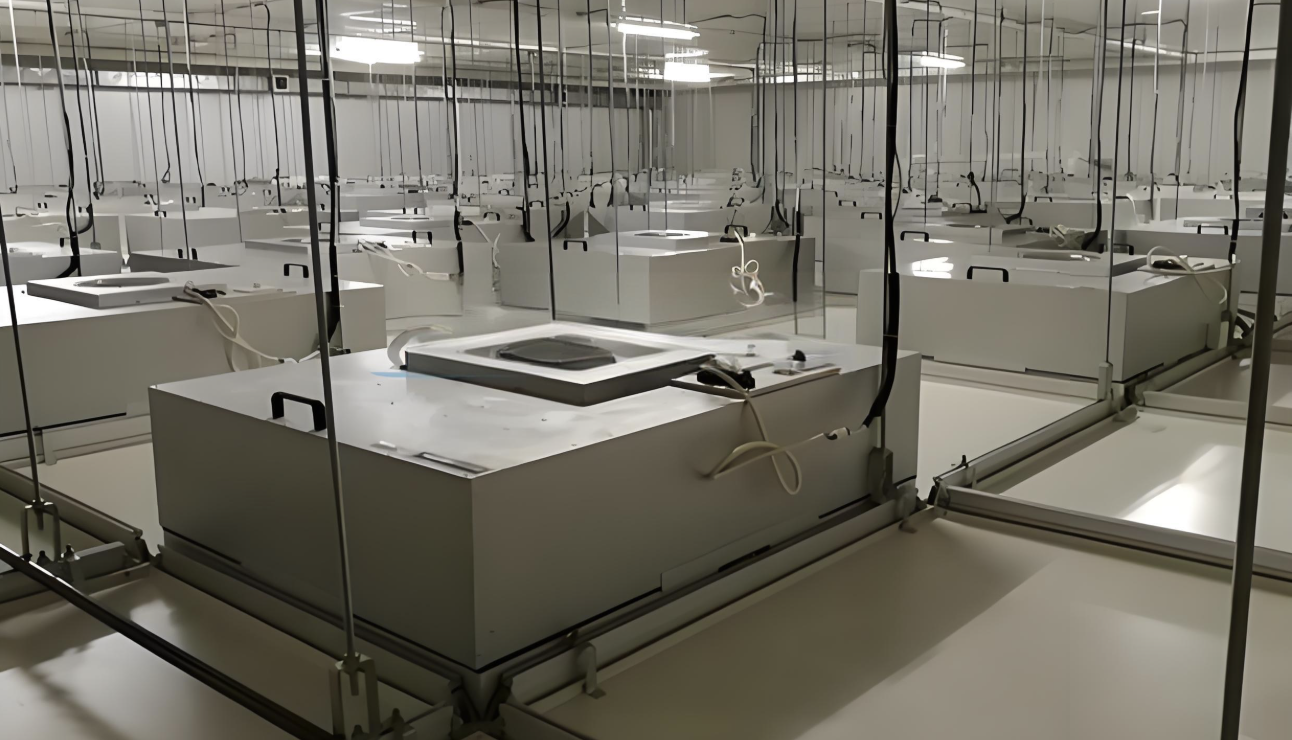
Ductwork over the ceiling.
Filtration
Similarly, in these spaces, the use of high-efficiency particulate air (HEPA) filters is standard. These filters trap 99.97% of particles that are 0.3 micrometers or larger.
HEPA Filters
Trap 99.97% of particles 0.3μm or larger
Suitable for most ISO 8 applications
ULPA Filters
Trap 99.999% of particles 0.12μm or larger
Used for stricter cleanliness requirements
While HEPA filters are sufficient for most ISO 8 applications, the specific requirements for filtration can vary based on the processes being conducted within the cleanroom. The selection of HEPA or ULPA filters depends on the size of the particles that cause issues with products or processes.
Advantages of Class 100,000 Cleanrooms
Minimize contamination risks, supporting product consistency and quality
Provide a controlled setting with explicitly defined air filtration and particle count requirements
Offer a balance between cleanliness and cost-effectiveness
Can be designed with modular systems for flexibility and scalability
FAQ
Question | Answer |
---|---|
What size particles are controlled? | Particles 0.5 micrometers and larger are controlled. |
How does a Class 100,000 cleanroom compare to ISO standards? | It's equivalent to an ISO 8 cleanroom. |
What industries typically use Class 100,000 cleanrooms? | Pharmaceuticals, biotechnology, and electronics industries. |
How are airflow and filtration maintained? | Through HEPA filters and controlled ventilation systems. |
Are Class 100,000 cleanrooms modular? | Yes, they can often be designed with modular systems for flexibility. |
Class 100,000 Cleanroom Guide
Designed for clarity and functionality