Cleanroom ConstructionDesign Standards, Layout, Materials, System Equipment Configuration, Costing, construction process
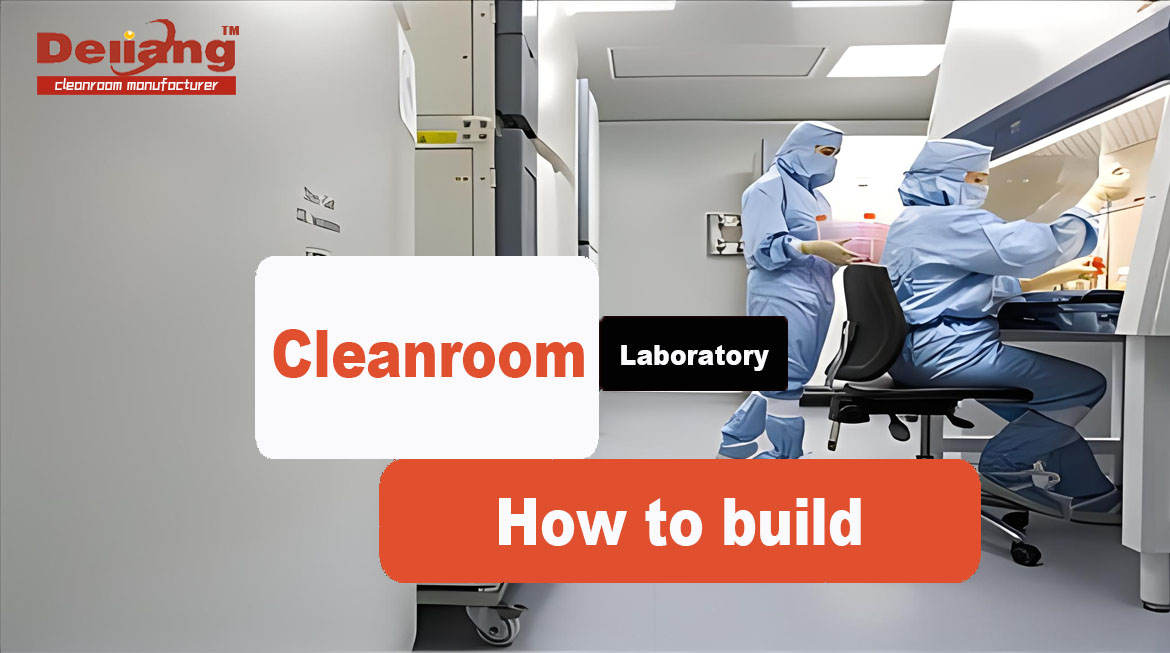
Industry Standards
Cleanroom construction must adhere to stringent industry standards to ensure the highest level of cleanliness. The ISO 14644 series is a widely recognized set of standards governing classification and design specifications.
The standards address various cleanliness levels based on air quality, using particle counts to classify rooms from iso class 1 to ISO Class 9. Compliance with these standards is crucial for validations and certifications, ensuring that cleanrooms meet international requirements.
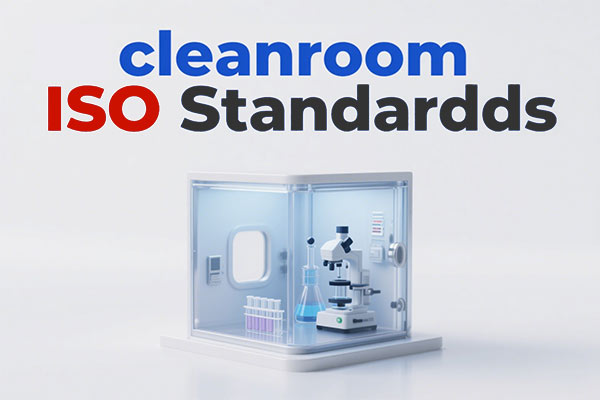
Layout and Design
The layout and design of A CleanRoom are foundational to its functionality. A well-designed CleanRoom layout optimizes space while ensuring smooth workflow and minimizing contamination risks.
Designers must consider the flow of people, materials, and waste to prevent cross-contamination. Cleanroom design also involves strategic placement of equipment and systems to maintain environmental control.
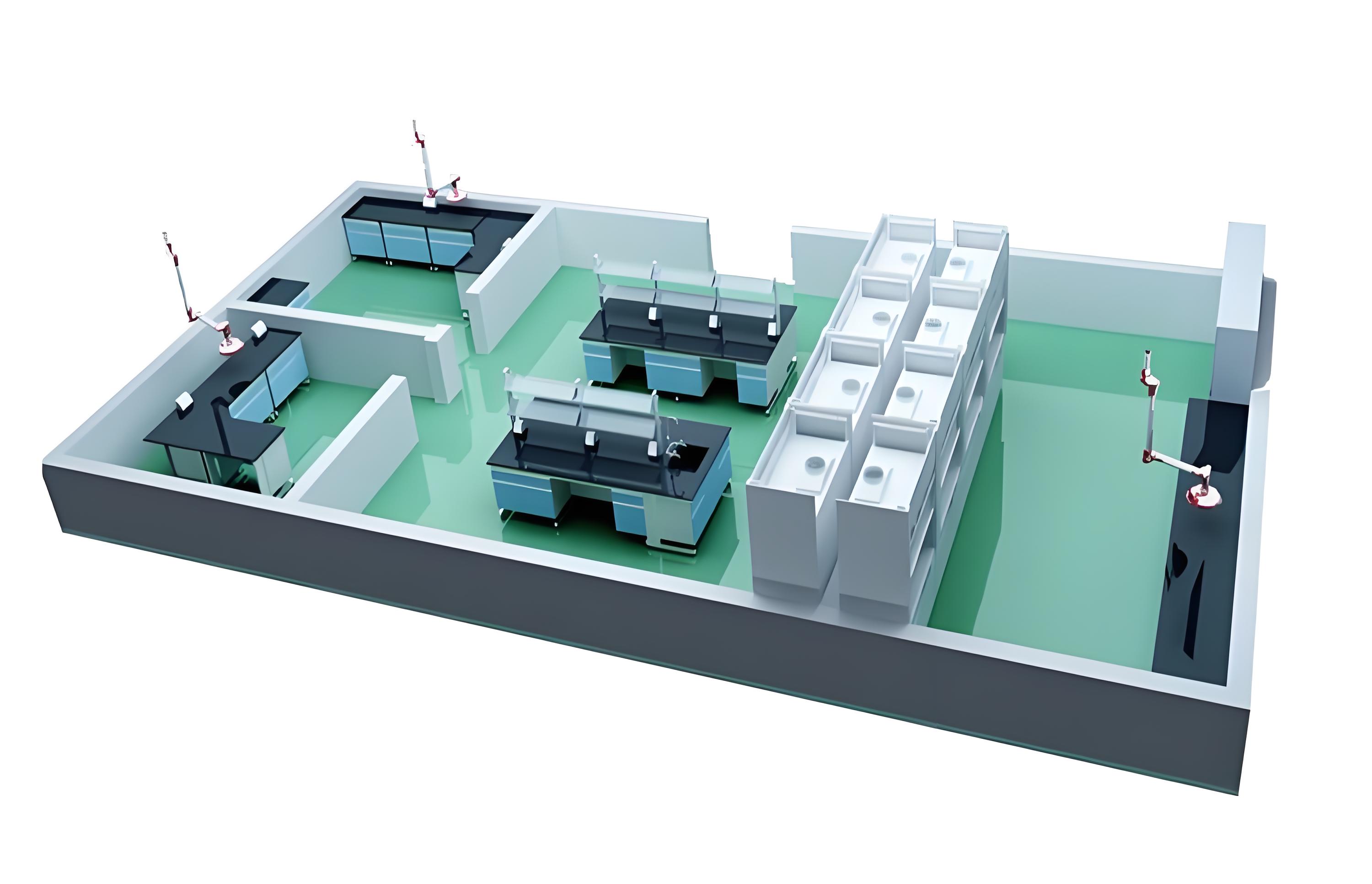
Construction and Materials
The selection of materials for constructing cleanrooms is critical, as they must resist contamination and be easy to clean. Common materials include non-porous walls, ceilings, and floors, made from substances like coated steel or PVC.
These materials must also withstand cleaning agents and not emit particles or gases. The construction process often involves modular systems to allow for scalability and modifications with minimal disruption.
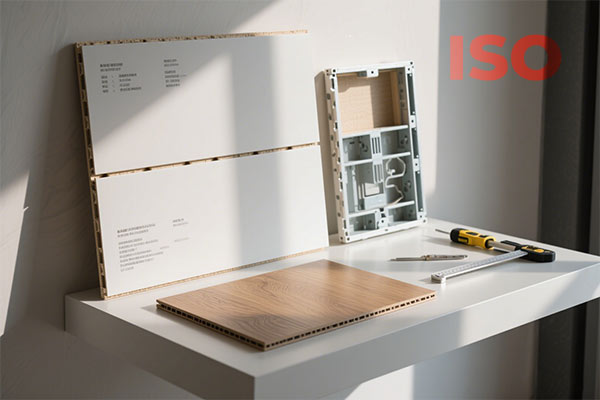
Equipment and Systems
Equipment and systems in A CleanRoom must support its primary function: maintaining a controlled environment. This includes everything from workstations to air filtration and monitoring equipment.
The layout must be planned to facilitate easy access for maintenance and cleaning. Advanced technology enhances efficiency and precision, with systems designed for long-term reliability and compliance with regulatory standards.
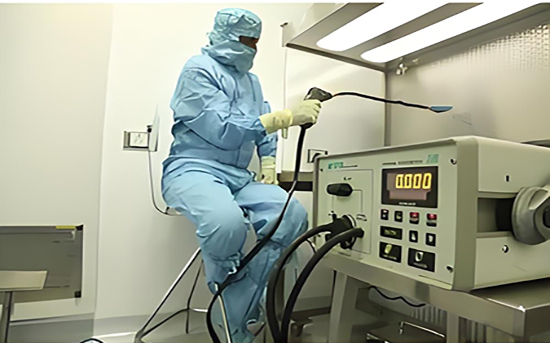
HVAC and Make-up Air
The HVAC system is a core component of cleanroom functionality, responsible for regulating temperature, humidity, and air cleanliness. The system must supply a steady flow of Clean air to maintain positive pressure, preventing contaminated air from entering.
Make-up air systems replace conditioned air lost through exhaust, maintaining balance and preventing air pressure issues. Incorporating cutting-edge HVAC solutions ensures optimal air quality and consistent environmental conditions, critical for Cleanroom operations.
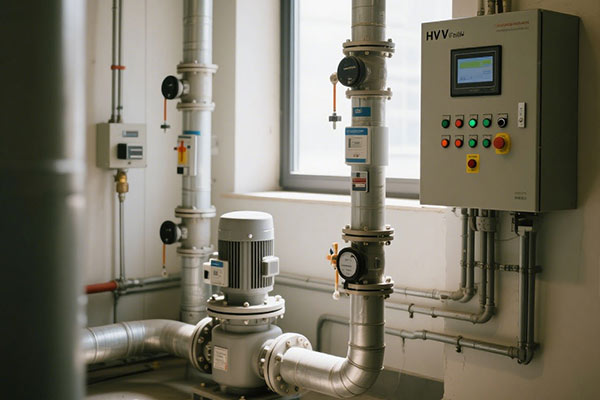
Circulating Air System
A circulating air system is vital for maintaining the cleanliness and stability of the cleanroom environment. It involves the continuous filtration and recirculation of air to remove contaminants and maintain temperature and humidity levels.
High-efficiency particulate air (hepa) or ultra-low penetration air (ULPA) filters are used to achieve the required air purity. State-of-the-art filtration technology ensures systems are efficient and meet international cleanliness standards.
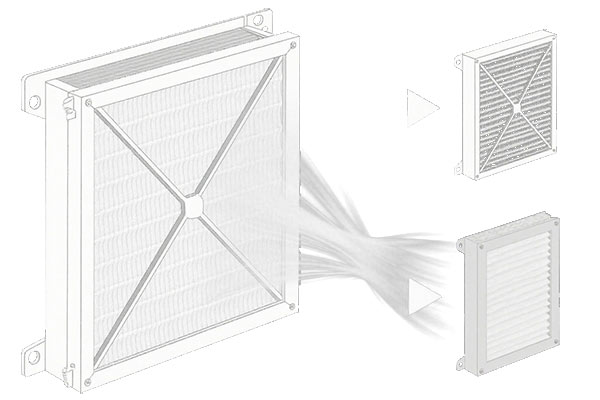
Cleanroom Construction Process
The construction process for cleanrooms involves several critical steps, including design conceptualization, material selection, and installation of systems. Initial planning must consider all functional requirements and regulatory standards.
The construction phase involves rigorous testing and validation to ensure everything meets prescribed cleanliness and operational standards. Finally, the cleanroom undergoes comprehensive testing to verify compliance.
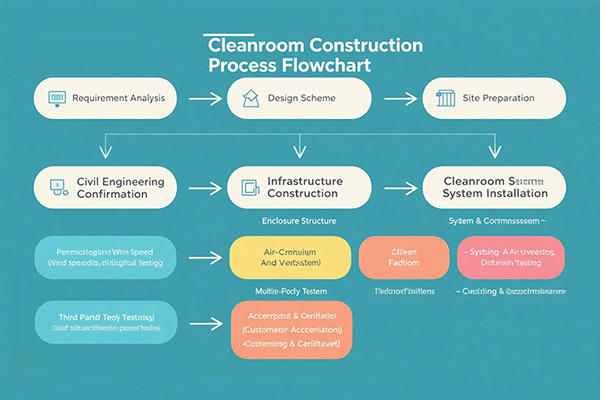
Frequently Asked Questions
Question | Answer |
---|
1. What is the most important standard for cleanrooms? | ISO 14644 is crucial for CleanRoom Classification and design. |
2. Why is positive pressure important? | It prevents contaminated air from entering the cleanroom. |
3. What materials are best for cleanrooms? | Non-porous materials like coated steel or PVC are ideal. |
4. What role does Deiiang™ play in cleanroom construction? | Deiiang™ provides innovative, compliant designs and materials. |
5. How do HVAC systems maintain cleanrooms? | They regulate air quality, temperature, and humidity. |
6. Why are hepa filters used in cleanrooms? | They effectively remove small particles to maintain cleanliness. |
7. What is the main function of circulating air systems? | To filter and recirculate air, maintaining purity and stability. |
8. How is compliance ensured in cleanroom construction? | Through adherence to standards like ISO 14644 and rigorous testing. |