Methods for Evaluating Cleanroom cleanliness and Microbial Levels
Ensuring the cleanliness and microbial integrity of A CleanRoom is crucial for maintaining product quality and safety
Ensuring the cleanliness and microbial integrity of a cleanroom is crucial for maintaining the quality and safety of products, particularly in industries like pharmaceuticals, biotechnology, and Electronics. This article outlines the principal methods used to assess cleanliness and microbial contamination in cleanrooms, incorporating expert insights from Deiiang™ and product designer Deiiang Jason.peng.
Principal Evaluation Methods
Particle Counting
A fundamental method for measuring non-viable particles in cleanroom air, serving as a primary indicator of cleanliness levels per ISO standards. Laser particle counters are utilized to determine particle counts across various sizes, typically in real-time.
Air Sampling
Measures viable microorganisms present in the cleanroom atmosphere, essential for maintaining microbial control. Includes both active and passive sampling methods.
- Active Air Sampling: Draws air over sterile media plates
Passive Air Sampling: Uses settle plates to collect settling particles
Surface Sampling
Essential for understanding and managing contamination on cleanroom surfaces, a critical aspect of cleanroom hygiene.
- Contact Plates (RODAC Plates): Convex agar surface for precise sampling
Swabbing: Useful for hard-to-access areas or complex geometries
Pressure Differential Testing
Crucial for maintaining proper airflow patterns and ensuring contaminants do not ingress from adjacent areas. Measures pressure differences to verify effective airflow design.
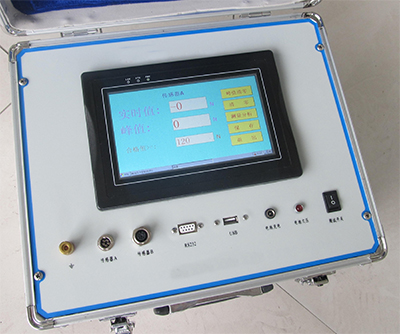
Conclusion: Comprehensive Cleanroom monitoring
Continuous assessment of cleanroom cleanliness and microbial levels is essential to maintain standards and assure product safety. By leveraging state-of-the-art methodologies like particle counting, air and surface sampling, and pressure differential testing, industries can proactively manage contamination risks. Deiiang™, with the innovation of designers like Jason.peng, remains at the forefront of cleanroom technology, offering solutions that ensure compliance and operational excellence.
Cleanliness Determination
1. Construction Acceptance Specification JGJ71
The minimum number of sampling points and sampling volume are specified as follows:
Area (m2) | Level 100 and above | 1000 | 10000 | 100000 |
---|---|---|---|---|
Less than 10 | 2~3 | 2 | 2 | 2 |
10 | 4 | 3 | 2 | 2 |
20 | 8 | 6 | 2 | 2 |
40 | 16 | 13 | 4 | 2 |
Cleanliness level (level) | Particle size (mm) 0.1 | Particle size (mm) 0.2 | Particle size (mm) 0.3 | Particle size (mm) 0.5 | Particle size (mm) 5.0 |
---|---|---|---|---|---|
1 | 17 | 85 | 198 | 566 | - |
10 | 2.83 | 8.5 | 19.8 | 56.6 | - |
100 | - | 2.83 | 2.83 | 5.66 | - |
1000 | - | - | 2.83 | 85 | - |
Sampling Port Orientation: For unidirectional cleanrooms, the sampling port should face the direction of the airflow. For non-unidirectional cleanrooms, the sampling port should face upward. The sampling speed should be as close to the indoor airflow speed as possible.
2. Determination of Cleanliness Measurement Results
If the measured state (empty, static, dynamic) is the same as the state agreed in advance, the upper limit of its cleanliness level is used as the evaluation standard. If the measured state is empty or static, the number of particles in the dynamic state will definitely be high. Sometimes 5 to 10 times the number of particles in the empty state can be used to estimate the number of dust particles in the dynamic state.
Determination of Microbial Particles
1. Arrangement and Requirements of Sampling Points
a. Floating Bacteria Measurement
The location of the sampling point can be the same as the arrangement of the floating particle measurement point. The measurement point is 0.8 to 1.5m from the ground, and the air outlet measurement point is about 30cm away from the air supply surface.
Area(m2) | 100 | 10000 | 100000 | |||
---|---|---|---|---|---|---|
verify | monitor | verify | monitor | verify | monitor | |
Less than 10 | 2~3 | 2 | 2 | |||
10~20 | 4 | 2 | 2 | |||
20~40 | 8 | 3 | 2 |
b. sedimentation bacteria Measurement
The sampling point location can be arranged in the same way as the suspended particle measurement point. The measurement point is 0.8~1.5m from the ground. For the sedimentation bacteria method, not only the minimum total number of samples must be met, but also the minimum number of sampling culture dishes must be met.
Area(m2) | 100 | 10000 | 100000 |
---|---|---|---|
Less than 10 | 2~3 | 2 | 2 |
10~20 | 4 | 2 | 2 |
20~40 | 8 | 2 | 2 |
40~100 | 16 | 4 | 2 |
Cleanliness Level vs. Culture Dishes:
- Cleanliness level above 100: 44 culture dishes
- Cleanliness level 100: 14 culture dishes
- Cleanliness level 1000: 5 culture dishes
- Cleanliness level 10000: 2 culture dishes
- Cleanliness level 100000: 2 culture dishes
Common Questions and Solutions
How often should CleanRoom air sampling be conducted?
This depends on the class and use of the cleanroom, but regular intervals, such as weekly or monthly, are common practice for many industries.
Why is it important to monitor both viable and non-viable particles?
Viable particles can lead to biological contamination, while non-viable particles can cause issues in precision manufacturing processes. Monitoring both ensures comprehensive environmental control.
References
- International Organization for Standardization. ISO 14644 - Cleanrooms and associated controlled environments.
- U.S. Food and Drug Administration. Guidance for Industry: Sterile Drug Products.
By adhering to these standardized methods, cleanroom operators can ensure the highest quality environments, safeguarding both product quality and consumer safety.
© 2025 Cleanroom engineering Services. All rights reserved.