Comprehensive guidelines for maintaining Clean room standards and procedures
1. Introduction
1.1 Scope
All persons, machines, equipment, articles, raw materials, products, etc. entering the clean room are subject to the control scope of this specification.
1.2 Purpose
To maintain the cleanliness of the clean room, control the pollution sources and control the environmental parameters, the persons, machines, equipment, articles, raw materials, etc. in the clean room are controlled to ensure that the cleanliness of the clean room meets the requirements of the product process and improve the product quality.
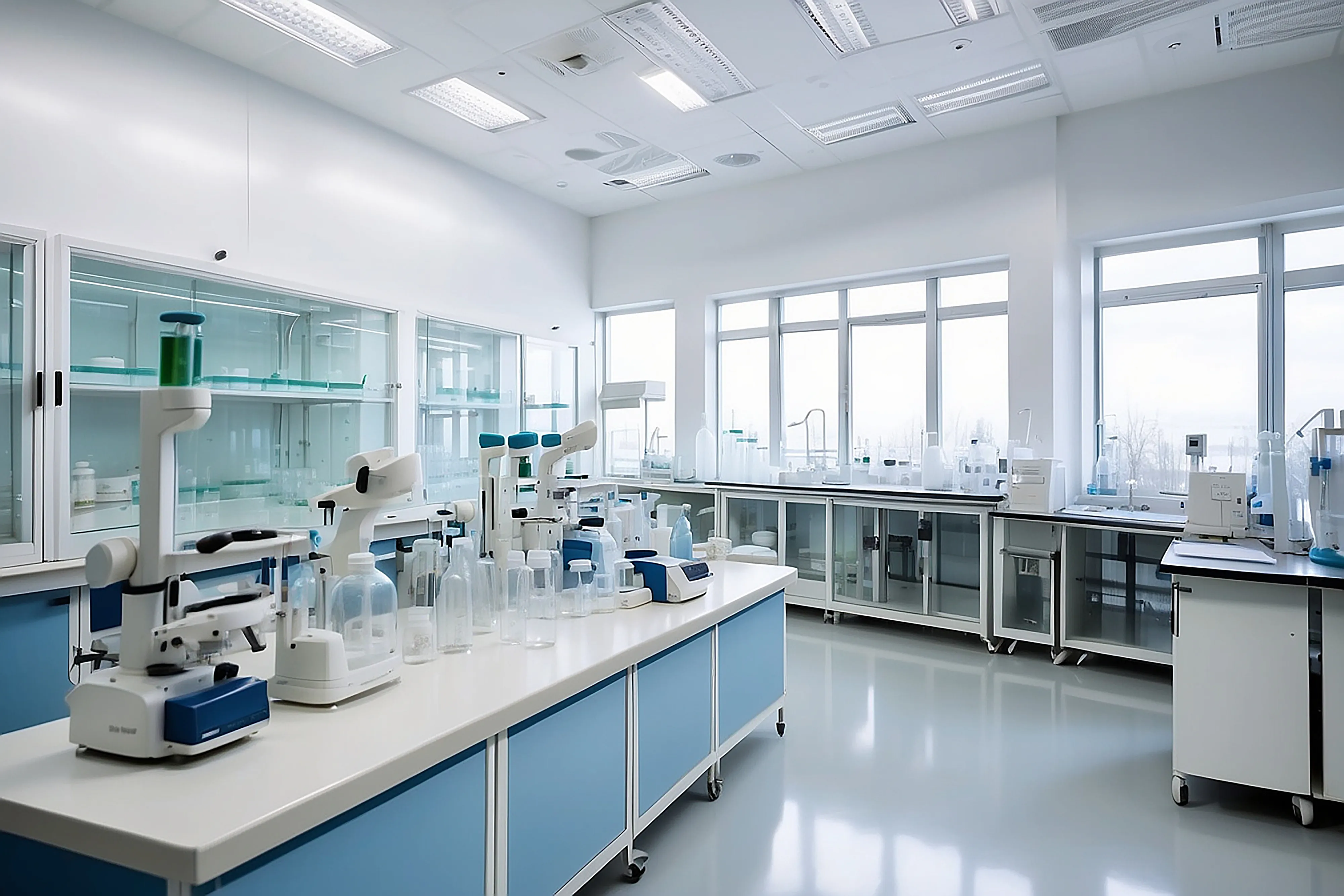
Figure 1: Cleanroom Management
2. Reference Document
U.S. federal standard 209D (U.S. FEDERAL STANDARD 209D) MS-5103 GUIDANCE FOR OPERATION OF CLEAN ROOM.
3. Definition
Except for the following terms, this specification is in accordance with JSZ8122 (Contamination Control Terminology). clean room particles are controlled within the specified value. Generally speaking, particles refer to solid or liquid substances with a particle size of 0.001 to 1000μm.
4. Clean room management standard procedures
4.1 Clean room cleanliness level classification and area definition
4.1.1 Front-end panel factory
Area | Class | Includes |
---|---|---|
Area A | Class 100 | yellow light room and assembly room |
Area B | Class 1000 | Other front-end panel production areas except areas A and C |
Area C | Class 10000 | Film projection room |
4.1.2 Back-end panel factory
Area | Class | Includes |
---|---|---|
Area D | Class 1000 | Back-end panel clean room (liquid crystal injection room) |
Area E | Class 1000 | Back-end panel patch area (inside Clean Booth) |
Area F | Class 10000 | Back-end panel general area |
4.1.3 Module workers
Zone | Class | Includes |
---|---|---|
G zone | Class 1000 | Module dust-free rate (C0G room) |
H zone | Class 1000 | Module cleaning area (inside Clean Booth) |
I zone | Class 10000 | Module general area |
4.2 Provisions for wearing and using dust-free clothes/shoes/hats
4.2.1 Classification of dust-free clothes
Type | Class | Colors & Usage |
---|---|---|
One-piece dust-free clothes | Class 100 | White, apple green, blue, green, light yellow (blue for engineers, green for construction and uncertified personnel, light yellow for guests) |
Shawl-style dust-free clothes | Class 1000 | White, blue, light yellow (blue for engineers, light yellow for guests) |
Coat-style anti-static robes | Class 10000 | White, blue, light yellow (blue for engineers, light yellow for guests) |
4.2.2 Classification of dust-free shoes
Type | Class | Colors & Usage |
---|---|---|
Long-type dust-free shoes | Class 100 | White, apple green, blue, green, yellow (blue for engineers, green for construction and uncertified personnel, yellow for guests) |
Open-hole electrostatic shoes | Class 10000 | White (guests use non-woven shoe covers) |
4.2.3 Classification of dust-free hats
Type | Class | Colors & Usage |
---|---|---|
One-piece dust-free hats | Class 100 | White, apple green, blue, green, yellow (connected with dust-free clothes) |
Shawl-type dust-free hats | Class 1000 | White, blue, yellow, pink, light red, dark red (blue for engineers and technicians, yellow for guests, pink for QC, light red for material personnel in the manufacturing department, and dark red for team leaders in the manufacturing department) |
Butterfly dust-free hat | Class 1000 | White, blue, yellow, pink, light red, dark red (blue for engineers and technicians, yellow for guests, pink for QC, light red for material personnel in the manufacturing department, and dark red for team leaders in the manufacturing department) |
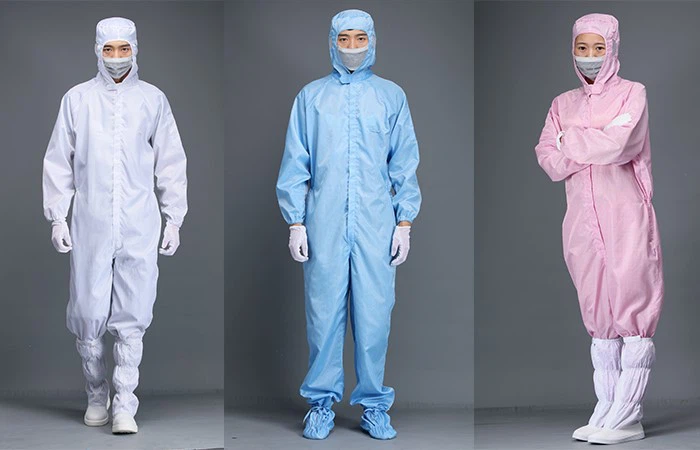
Figure 2: cleanroom dust-free clothing
4.2.4 Dust-free clothing wearing regulations for each area
A and B areas:
- MGMT/PROD White or apple green one-piece, long shoes, mesh hats, masks, gloves
- ENG/R&D Blue one-piece, shawls, long shoes, mesh hats, masks, gloves
- QC Pink one-piece, long shoes, mesh hats, masks, gloves
- CONSTR Green one-piece, long shoes, mesh caps, masks, gloves
- GUEST Yellow one-piece, capes, long shoes, mesh caps, masks, gloves
Area D, G:
- MGMT/PROD/QC White/blue cape-style, capes, long shoes, mesh caps, masks, gloves
- ENG/R&D Blue cape-style, capes, long shoes, mesh caps, masks, gloves
- GUEST Yellow shawl-style, shawl hats, long shoe covers, net hats, masks, gloves
Areas C, F, H, I:
- MGMT/PROD/QC White/blue coat-style anti-static robes, butterfly hats, open-hole shoes
- ENG/R&D Blue coat-style anti-static clothing, butterfly hats, open-hole shoes
- GUEST Light yellow coat-style anti-static robes, butterfly hats, non-woven shoe covers
4.2.5 Cleaning and changing regulations for clean clothes
Clean clothes must be cleaned regularly every two weeks, and are cleaned uniformly by outsourced professional laundry factories and sent back to the factory to maintain the cleanliness of clean clothes.
4.2.6 Damage and repair of cleanroom clothing
If cleanroom clothing is damaged, the zipper is damaged, the elastic band is loose, the magic sticky tape falls off, etc., the clothing should be stopped from use immediately. If it can be repaired, it should be placed in the repair area. If it cannot be repaired, it should be scrapped and a new one should be used.
4.3 Obtaining the qualification to enter the cleanroom
4.3.1 General employees
Those who often work in the cleanroom or enter the cleanroom from time to time should first take the "Cleanroom Management Standards" or other related courses by the manufacturing department, and pass the examination before they are qualified to enter and exit the cleanroom. Those who pass the examination will be registered and managed by the manufacturing department, and then they can receive cleanroom clothing and other related items from the manufacturing department.
4.3.2 Senior managers
After being familiar with and understanding the cleanroom management standards and other relevant regulations, they are qualified to enter and exit the cleanroom. (Senior manager definition: refers to the chairman, general manager, deputy general manager, etc.)
4.3.3 Guests (manufacturers)
The reception department should have the clean room entry and exit qualifications, and explain the various regulations and precautions in the clean room first, and then they can Enter the clean room accompanied by relevant personnel.
4.3.4 Clean room entry qualification acquisition process
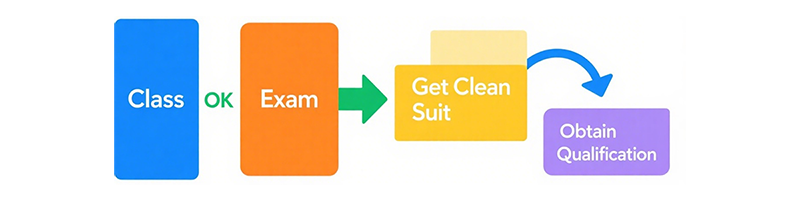
Figure 3: Clean room entry qualification acquisition process
4.4 Cancellation of clean room entry qualifications
If the following situations occur, the clean room entry qualification will be cancelled:
- When the employee resigns or the leave of absence period exceeds 3 months.
- The cumulative violation of the clean room management regulations or other relevant regulations within 1 month is registered by the quality control or audit personnel for 2 times (inclusive) or more.
- Violation of the clean room management regulations or other relevant regulations is serious.
- When the clean room management regulations or other relevant regulations are significantly modified and re-certification is required.
4.5 Clean Room Qualification Examination
- Pre-exam preparation: Before the exam, the Manufacturing Department shall give a unified lecture on clean room management regulations and other related regulations.
- Test papers: There are 4 test papers in total, A, B, C, and D. Each paper consists of 15 multiple-choice questions and 10 true-or-false questions, each worth 4 points, and the score is calculated without deduction.
- Exam time: 10 minutes.
- Passing score: 80 points.
- Re-examination regulations: Those who fail the first test can retake the test after attending the class. If they still fail, they will not be qualified to work in the clean room.
4.6 Clean room entry and exit control regulations
4.6.1 Personnel restrictions
- Company employees: Those who must work in the clean room due to job requirements must first take the "Clean Room Management Regulations" and other clean room-related regulations courses and pass the examination before they can enter the clean room.
- Non-employees: To maintain cleanliness requirements and avoid unnecessary interference with production operations to ensure product quality, except for specific circumstances, no one is allowed to visit the clean room.
- Non-employees must be accompanied by the receptionist or relevant department personnel when entering the clean room.
- Application procedure for guests: When a guest needs to enter the clean room, the receptionist or relevant department personnel should apply to the head of the manufacturing department and can enter only after approval.
- Guests must swipe their card to enter the clean room.
Note: People with the following health conditions or physical conditions are generally not allowed to enter the clean room:
- People with skin problems due to sun exposure, eczema, or burns
- People who are allergic to chemical fibers
- People who are allergic to chemical agents such as solvents
- People who sweat easily or have sweaty hands
- People who are prone to runny noses or often have discharge from their noses
- People who often cough, sneeze, or suffer from asthma
- People who have the habit of scratching frequently
- People who have mental illness, neurosis or closed-door phobia
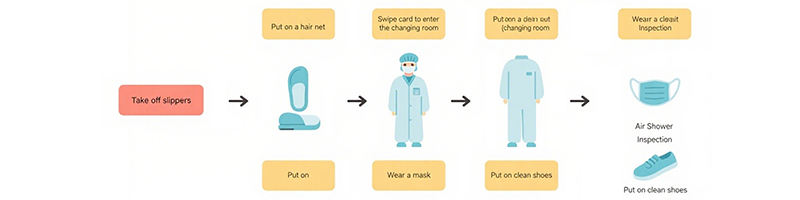
Figure 4: Entering and exiting the clean room
4.6.2 Restrictions on items
- All items that are not used for production or work are prohibited from being brought into the clean room.
- Paper items (not clean paper) on the front of the panel are prohibited from being brought into the clean room. If they must be brought in, they must be sealed or covered with plastic.
- The following items are prohibited from being brought into the clean room:
- Pencils, erasers, correction fluid (correction tape) and other stationery that are easy to generate dust or evaporate (only in A, B, C, D, G areas)
- Ordinary paper, cartons, ordinary notebooks, paper loose-leaf books, etc. (only in A, B, C areas)
- Wooden items that do not have polyethylene or other materials on the surface
- Iron items that have not been rust-proofed and are rusty
- Dirty or rusty items
- Styrofoam items (only in A, B, C, D, G areas)
- Other items that are easy to pollute the environment or produce particles
- Before bringing items into the clean room, they must be wiped clean before they can be brought in.
4.7 Procedures for entering the clean room
- Procedures for personnel to enter the clean room (CR)
- Procedures for items to enter the clean room
- Procedures for instruments and equipment to enter the clean room
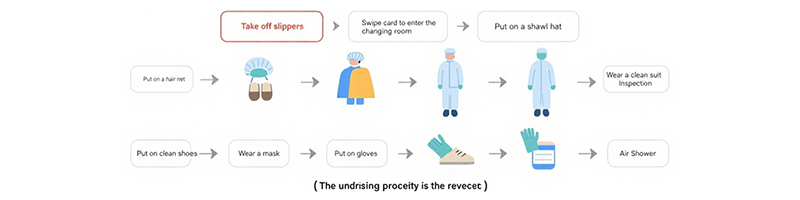
Figure 5: Clean room entry procedures
4.8 Procedures for wearing clean clothes
- Procedures for wearing one-piece clean clothes (the procedure for taking off clothes is the opposite)
- Procedures for wearing shawl-style clean clothes (the procedure for taking off clothes is the opposite)
- Procedures for wearing coat-style anti-static robes (the procedure for taking off clothes is the opposite)
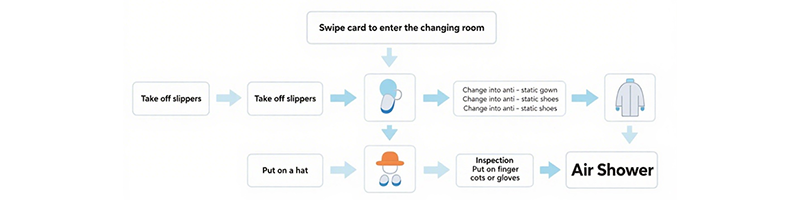
Figure 6: Clean clothes wearing procedures
4.9 Steps for wearing cleanroom clothing
4.9.1 Steps for wearing one-piece cleanroom clothing
4.9.2 Steps for wearing a shawl-style cleanroom clothing
4.9.3 Steps for wearing a coat-style anti-static clothing
4.10 Notes for wearing cleanroom clothing
- Place changed slippers neatly in the designated area
- Place clean, well-packaged clothing/shoes/hats in your personal closet
- Clothing in use should be neatly hung on the hanger of the Clean Booth (HEPA)
- When changing, avoid clothing touching the ground
- When wearing a net hat, cover hair and ears completely
- Zippers should be pulled to the bottom; buttons fastened; Velcro attached
- Clothing should be worn with moderate tightness
- Damaged clothing should not be worn
- When wearing cleanroom shoes, wear socks to maintain hygiene
- Wear shoes completely - don't step on heels
- Casual trouser legs should not be exposed
- Mask should cover mouth and nose completely
- Gloves should be completely stuffed into cuffs
- Don't walk while putting on clothing, masks or gloves
- Cap should be pressed inside clothing with brim not exposed
- Do not doze off in the cleanroom
Replacement frequency:
- Net cap: Once a week (replace immediately if dirty/damaged)
- Mask: Every 2 days (replace immediately if dirty/damaged; disposable masks every entry/exit)
- Gloves: Every entry/exit (replace immediately if dirty/damaged)
- Finger gloves: Every two hours (every half hour for patch stations)

Figure 7: Clean room environment
4.11 Check the top of the clean clothes before wearing them
Before wearing the clean clothes and entering the air shower, you should check the following items in front of the mirror:
- Hair and net hat should not be exposed
- Mouth and nose should not be exposed
- Trousers should not be exposed (except for coat-style anti-static robes)
- Clean clothes and shoes should not be damaged or dirty
- Zippers, buttons, magic sticky tape, etc. should be pulled up and not loose
- The edge of the gloves should not be exposed
- Identification name tags should be fitted and fixed securely (except for new employees without tags)
- The brim of the shawl and hat should not be exposed
4.12 General prohibitions and precautions for clean rooms
- No entry without qualification
- Never touch product with bare hands
- Forms should be filled accurately; changes signed and dated
- Keep gloves dry and clean; no writing on gloves
- No sitting/laying on tables, footrests, floors, trash cans, etc.
- Those with sweaty or allergic hands can wear cotton gloves under PVC/latex
- Pay attention to announcements and slogans
- Support each other but don't operate uncertified machines alone
- Correct non-compliant items and notify supervisor
- Always ensure no hair, mouth, or nose exposure
- Don't place clean clothes/hats on the floor
- Dressing/undressing only in dressing room
- Air shower front/rear doors cannot be open simultaneously
- No running, playing, noise, sleeping in clean room
- No eating or drinking
- Avoid large gatherings to prevent particle production
- Don't enter immediately after strenuous exercise or sweating
- Smokers must wait 30 minutes after smoking and wash hands/rince mouth
- No general paper, notebooks, cartons, toilet paper, books, etc.
- No grinding, filing, sawing, sandpaper, abrasives
- Maintain hair and body cleanliness; wash regularly
- No perfume, lipstick, hairspray or cosmetics
- Raw materials must be unpacked and wiped clean before entry
- Don't talk facing product, cassette or machine
- Reduce unnecessary contact with product, even with gloves
- Don't remove documents, items or tools without permission
- Don't pull down mask when talking
- Keep phone calls brief and to the point
- Keep escape routes clear
- Keep all items neatly placed
- Before air shower, step on sticky mat to clean shoe soles
- In air shower: raise hands and slowly rotate body (at least 3 times)
- Don't exceed specified number in air shower
- Safety door for emergencies only
- Don't wear clean clothes/shoes outside clean room
4.13 Special attention to the yellow light room
- No more than 5 people in the yellow light room
- Must use air shower when entering
- Be careful with light source to avoid affecting process
- No interfering factors affecting temperature/humidity during production
- Minimize walking around or entering/exiting
4.14 Things to note for guests (vendors) entering the clean room
Must apply for permission before entering and be accompanied by relevant personnel.
- Guests must be accompanied throughout their activities
- No photography or photo taking
- Don't bring prohibited items
- Must wear special clean clothes (yellow)
- Long clean shoe covers for A/B areas; non-woven for C/D/E/F
- No touching or operating machines without permission
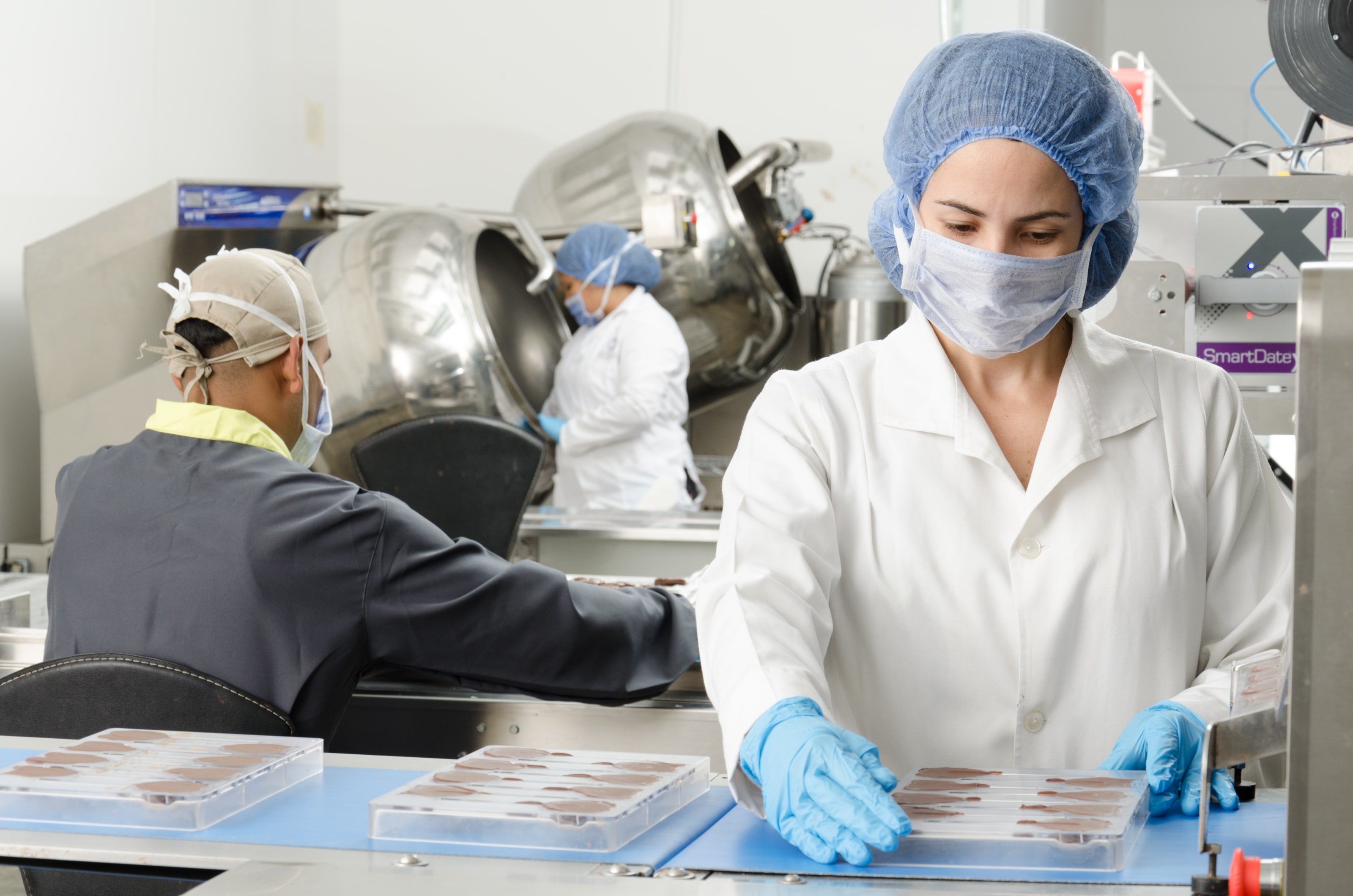
Figure 8: Cleanroom Safety Precautions
4.15 Safety precautions for cleanrooms
- Operate machines only after certification
- Follow operating specifications for special operations
- Clean spills (oil, water, chemicals) immediately
- Keep aisles unobstructed
- No flammable items unless with safety protection
- Don't bypass safety measures; repair if damaged
- Report unsafe conditions to supervisor
- Follow all safety warning signs
- Keep emergency equipment in designated locations
- Close caps on liquids and chemicals immediately after use
- For construction/maintenance: obtain permission for high-altitude work, fire, etc.
- Avoid working alone
- Ensure all electrical equipment is grounded and insulated
- Don't look directly at high-energy light sources
- Check safety gear daily and keep ready for use
4.16 Clean room environmental condition control
Panel front section
- Temperature: T=(23+1)℃
- Humidity: (50+5) RH
Panel rear section
- General environment:
- Temperature: T<25℃
- Humidity: (62.5+17.5) RH
- Clean room:
- Temperature: T=(23±2)℃
- Humidity: (62.5+17.5) RH
Module
- General environment:
- Temperature: T<25℃
- Humidity: (65+15) RH
- Clean room:
- Temperature: T=(23+2)℃
- Humidity: (65±15) RH
Summary
These comprehensive clean room management rules and regulations ensure the highest standards of cleanliness, safety, and operational efficiency. By following these guidelines meticulously, organizations can maintain optimal environmental conditions, prevent contamination, and ensure product quality in sensitive manufacturing environments.