Ensuring optimal production order, labor productivity, and Clean Room integrity
Purpose
In order to maintain a good production order, improve labor productivity, and ensure the smooth progress of production work, the following management system is specially formulated.
Scope
Applicable to all staff members of the production workshop.
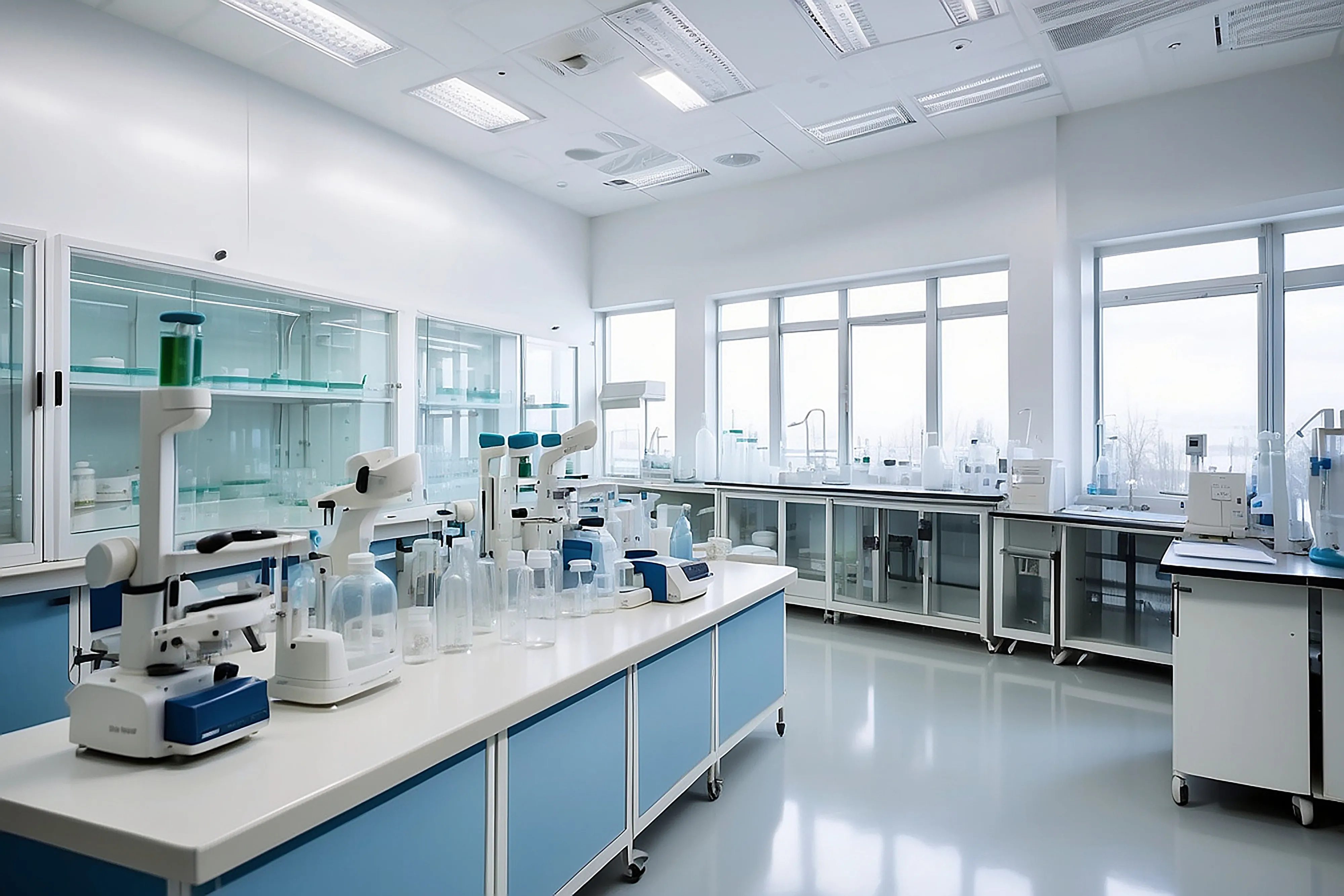
Figure 1: Clean room management
Workshop Policies & Procedures
1. Morning Meeting System
- Employees must arrive at the workshop 5 minutes early for morning meetings every day, and must not be late or leave early.
- Employees must stand upright during the morning meeting, listen carefully to the speeches of supervisors or team leaders, and must not do things unrelated to the morning meeting.
- The team leaders of each line must arrive at the workshop 10 minutes early every day to organize employees to hold morning meetings on time.
- The team leaders of each line must promptly inform employees of the work situation of the day before and the production plan of the day during the morning meeting, and the time should be controlled within 15 minutes.
- The team leader's speech at the morning meeting should be loud and powerful, mainly motivational, and must not criticize or scold employees at will.
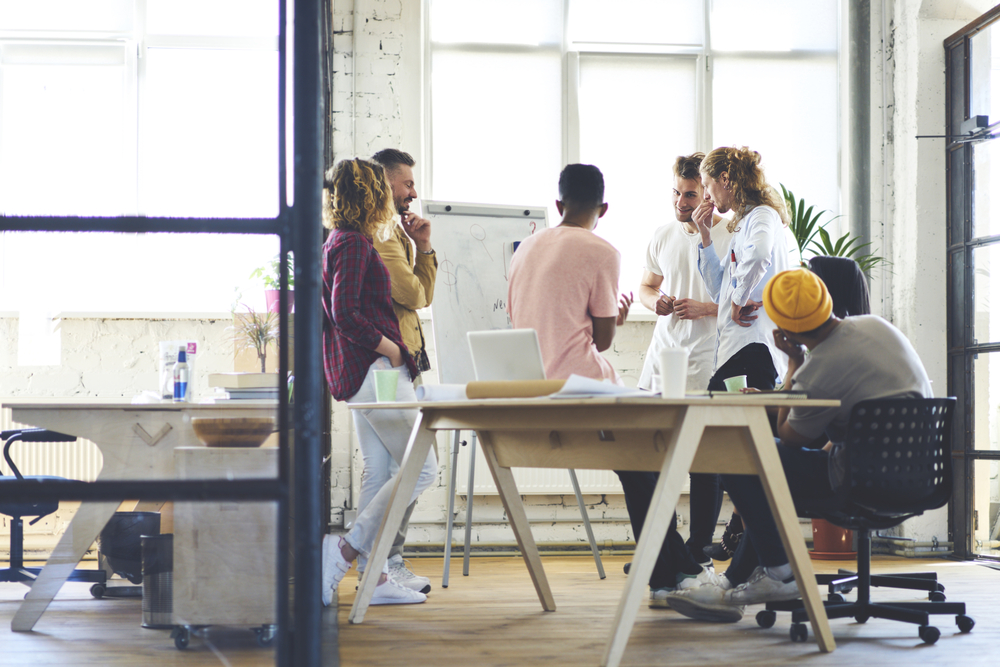
Figure 2: Morning meeting
2. Leave System
- If special matters must be handled in person, leave should be applied for in writing 2 hours in advance. Leave will only be effective after the supervisor and relevant leaders sign.
- Avoid private leave or approval of leave outside working hours.
- Employees may not apply for leave more than twice a month, and the daily leave may not exceed 5%.
Leave Approval Authority
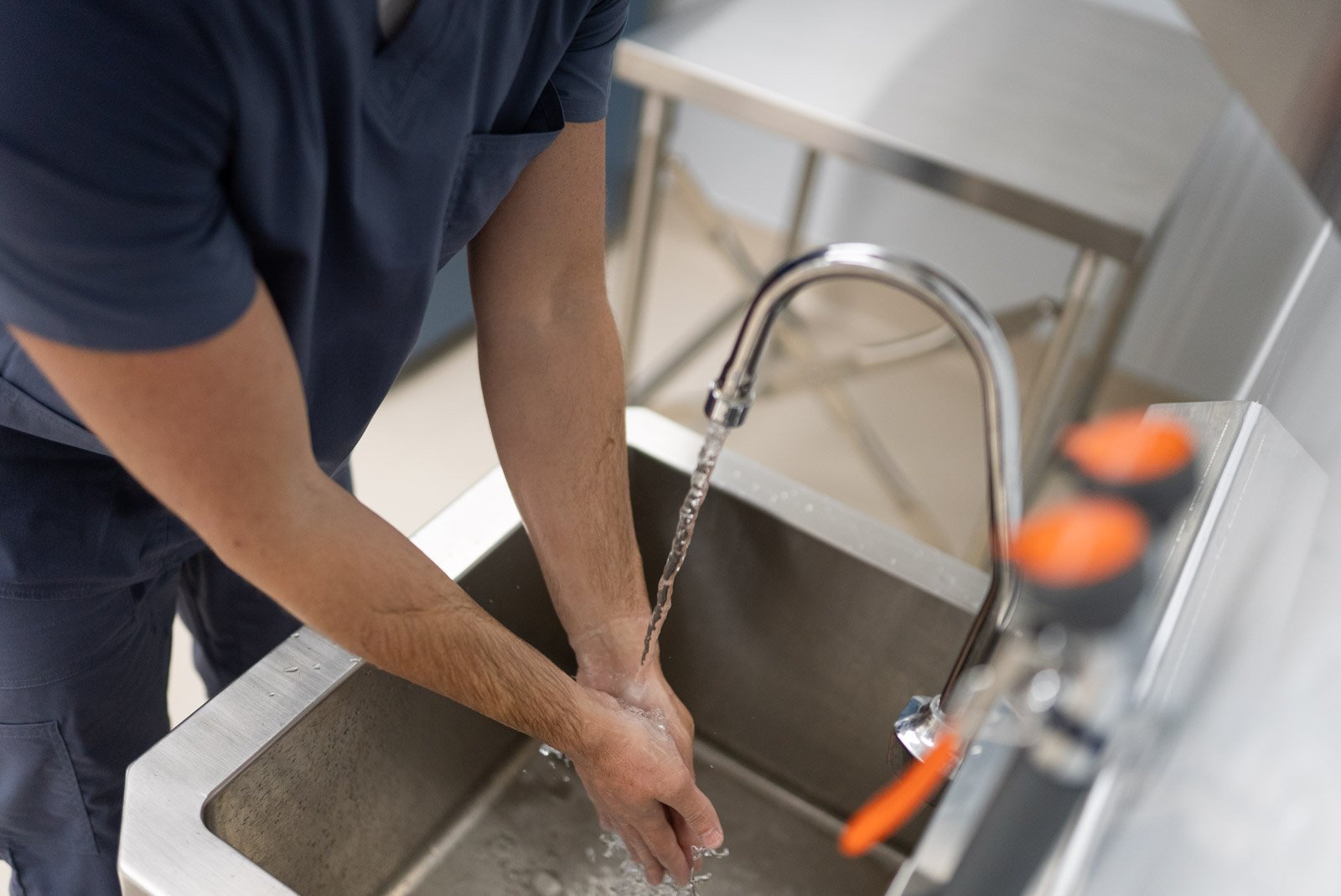
Figure 3: Clean room hygiene
3. Cleanliness and Sanitation System
- Employees must keep their posts clean and tidy, and items must be placed neatly in the specified positions and must not be placed everywhere.
- After get off work every day, the duty students will clean up, and a general cleaning must be done on weekends.
- Sanitary tools must be cleaned and placed in the designated area after use.
- Do not litter or scribble in the company at will.
Cleaning Schedule
- Daily: Post cleaning, tool organization
- After work: Duty cleanup by assigned staff
- Weekends: General cleaning of entire facility
- Continuous: Immediate cleanup of any spills or messes
4. Workshop Production Order Management
- Employees must clean their hands and faces before entering the workshop, and must wear the correct factory badge, work permit, anti-static slippers, anti-static clothes, anti-static hats, and anti-static rings.
- The anti-static ring must be tested before going to work, and signing on behalf of others is strictly prohibited.
- During operation, employees must keep a distance of more than 50-80CM and must not sit together.
- Small accessories must be placed in black anti-static boxes. Only one type of spare parts can be placed in a box.
- All employees must operate in accordance with the operating procedures.
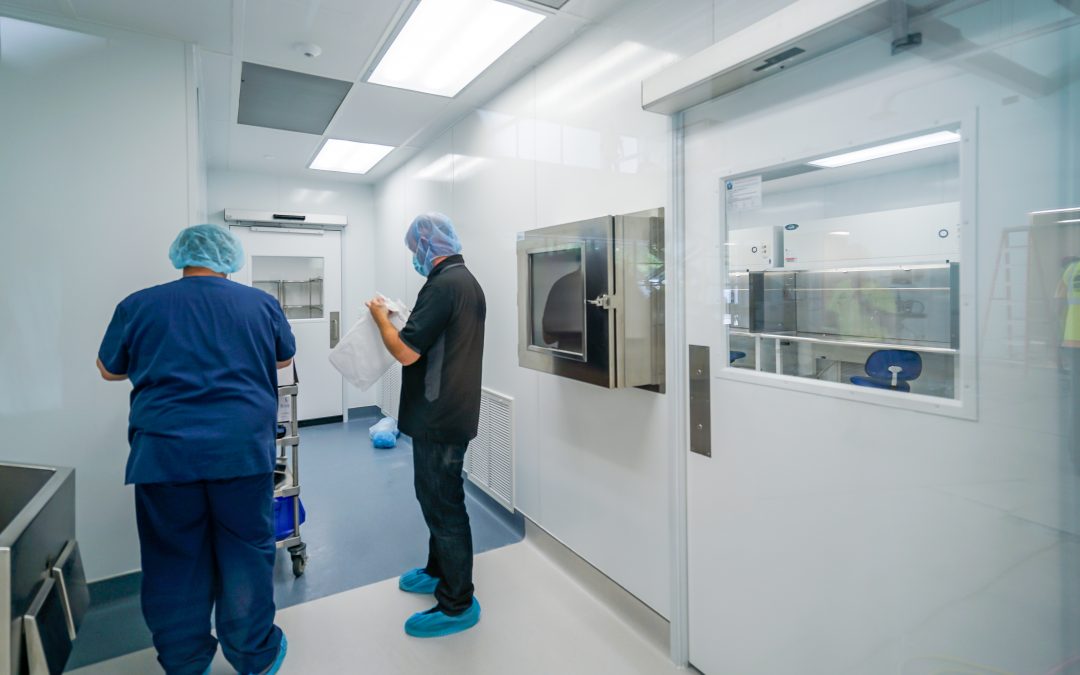
Figure 4: Clean room personnel management
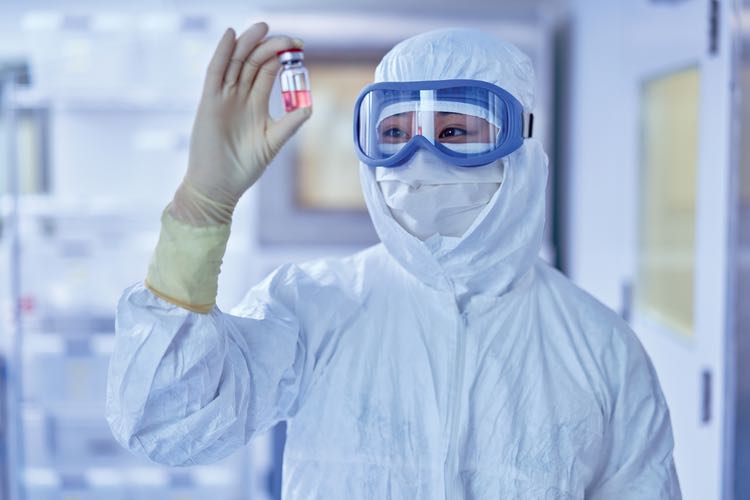
Figure 5: Wearing cleanroom clean clothes
5. Workshop Discipline
- Be on time for work and leave on time
- Start production immediately after entering
- Obtain consent before leaving work station
- No private calls during work
- Do not lie on the assembly line
- Strictly abide by work and rest time
- Save water and electricity
- Organize work area before leaving
- Do not change workstations privately
- No food in the workshop
- No napping during working hours
- No quarreling with colleagues
- No smoking in workshop areas
- Do not carry production items out
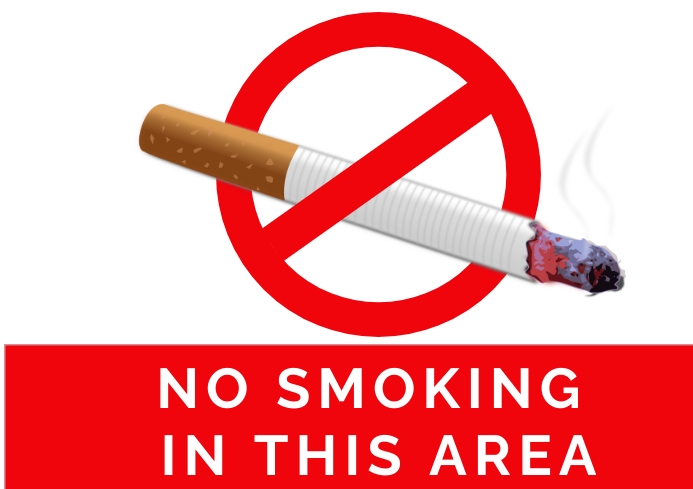
Figure 6: No smoking in workshop
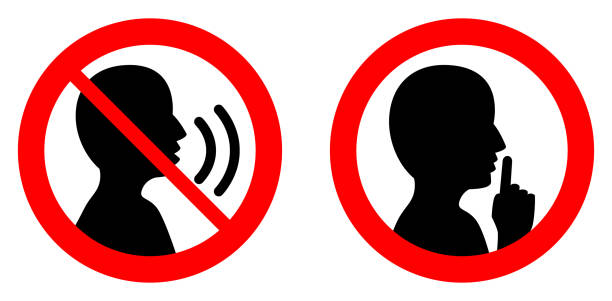
Figure 7: No talking during work
6. Material Control
- Employees should clean up and collect the used components before leaving and collect the scrapped parts.
- During work, employees should collect loose materials at any time and stack them neatly.
- Materials should be handled with care, and quality problems should be promptly reported.
- Material clerks should carefully write return material orders and scrap orders.
- It is strictly forbidden to throw waste materials into the trash can.
- The material clerk of the previous shift should prepare enough materials for the next shift.
- Employees have the right and obligation to stop anyone from taking materials without permission.
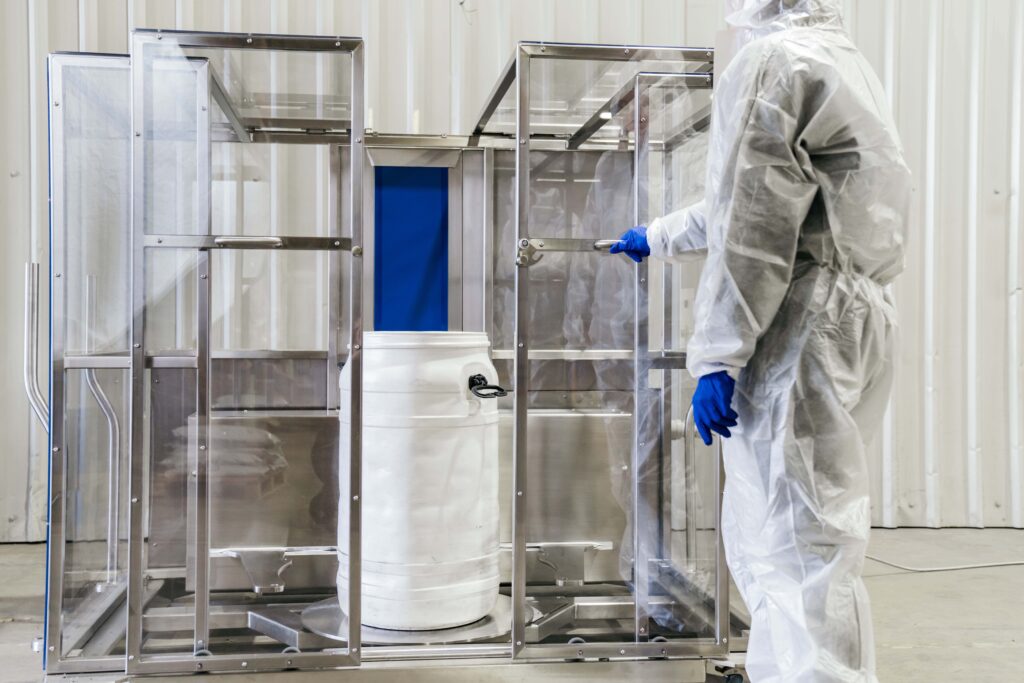
Figure 8: Cleanroom material control
Employee Incentives
Recognition
Regular acknowledgment of outstanding performance
Suggestions
Encouraged to promote good suggestions with rewards
Safety
Safe working environment with clear procedures
Teamwork
Collaborative work culture with mutual respect
Clean Room Workshop Management System | Ensuring Productivity and Quality
All employees must comply with these regulations to maintain clean room integrity