Comprehensive Guide to Cleanroom Management Standards and Regulations
Ensuring precision and safety in contamination-controlled environments
In the realm of industries that depend on stringent contamination control, cleanroom management is a critical component. Cleanrooms must adhere to a set of standards and regulations to maintain their classification and to ensure the efficacy and safety of their environments. This guide explores the key standards and regulations governing cleanroom management, their applications in different industries, and best practices for maintaining these environments.
ISO 14644 Series: Foundational Cleanroom Standards
The ISO 14644 series provides a comprehensive international framework outlining the requirements for the design, classification, testing, and monitoring of cleanrooms.
iso 14644-1
This standard defines CleanRoom Classifications based on the concentration of particles of specified sizes per cubic meter of air. Cleanrooms are classified from ISO 1 to ISO 9, with ISO 1 being the cleanest.
iso 14644-2
It specifies the practices for testing and monitoring cleanrooms to ensure continued compliance with classification standards, including regular particle counting and airflow testing.
ISO 14644-3
Offers methods for measuring and testing cleanroom performance, covering factors such as air velocity, pressure, and particle counts to maintain efficient operations.
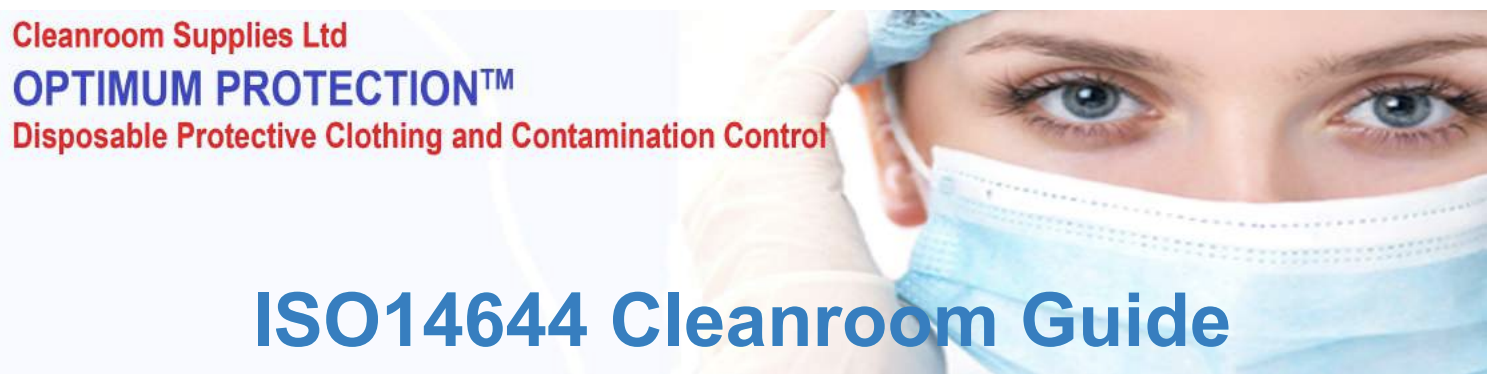
Cleanroom classification and testing according to ISO 14644 standards
Industry-Specific Regulations
Cleanroom management must also comply with industry-specific regulations that dictate additional standards and practices.
Regulation | Description | Industry Focus |
---|---|---|
FDA cGMP | Addresses air filtration, temperature, humidity control, and personnel practices | Pharmaceuticals (US) |
EU GMP | Covers a spectrum of issues relevant to pharmaceutical cleanrooms | Pharmaceuticals (Europe) |
Health Canada GMP | Aligns with FDA's cGMP Standards for Canadian operations | Pharmaceuticals (Canada) |
Core Aspects of Cleanroom Management
Managing A CleanRoom relies on several fundamental aspects to maintain hygiene and operational standards.
Classification and Monitoring
Establish and maintain the correct ISO classification. Regular monitoring of particle counts, airflow, and pressure differentials is crucial.
Contamination Control
Implement measures to minimize particle introduction, including advanced air filtration, proper gowning procedures, and personnel training.
Environmental Control
Use advanced HVAC systems to maintain precise control over temperature, humidity, and other environmental parameters.
Personnel Practices
Strict adherence to gowning procedures, behavioral protocols, and comprehensive training to minimize human contamination.
Equipment & Materials
Ensure all equipment and materials meet cleanliness standards to maintain contamination control levels.
Conclusion: Ensuring Excellence in Cleanroom Management
Cleanroom management is a meticulous process that requires adherence to international standards and industry-specific regulations. By understanding and implementing these guidelines, facilities can maintain high levels of cleanliness and operational efficacy. Expert solutions and insights, such as those provided by Deiiang™, support the precise management of cleanroom environments to ensure product safety and quality.
Common Questions and Solutions
What is the importance of ISO 14644 compliance in cleanroom operation?
Compliance with ISO 14644 ensures a cleanroom meets international benchmarks for air cleanliness, mitigating contamination risks and safeguarding product integrity. It provides a standardized framework for design, classification, and testing, ensuring consistency and reliability.
How can personnel contamination in cleanrooms be minimized?
Personnel are a primary source of contamination in cleanrooms. This can be minimized through rigorous training on proper gowning procedures, strict adherence to behavioral protocols, and continuous education on contamination control best practices. Specialized clothing and equipment also play a crucial role in reducing particle release.
References
- International Organization for Standardization. ISO 14644 - Cleanrooms and associated controlled environments.
- U.S. Food and Drug Administration. Guidance for Industry: Sterile Drug Products.
- European Medicines Agency. EU GMP guidelines.
Delivering safe and high-quality products starts with maintaining unwavering cleanroom standards, achieved by aligning with best practices and leveraging specialized expertise.