1. Purpose
To ensure the environmental quality of the clean room and reduce the company's management costs, ensure product quality and improve operating efficiency.
2. Scope
All personnel (including our company's personnel, Manufacturers and visiting guests, etc.) and materials and supplies entering the clean room are subject to the constraints and specifications of this management regulation.
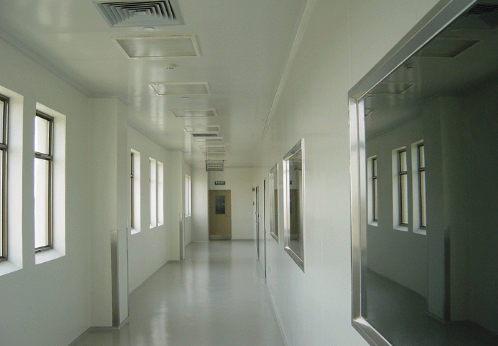
Figure 1: Dust-free workshop management
3. Responsibilities
3.1 Biotechnology Department: Responsible for supervising all personnel entering the clean room to abide by the rules;
3.2 Marketing Department: Responsible for explaining the relevant regulations for entering the clean room to customers who need to Enter the clean room and requiring cooperation.
4. Management content
4.1 Management of entering the clean room
4.1.1 Before entering the clean room, our company's personnel must change their shoes into indoor slippers (or put on shoe covers) in the shoe changing area, and personal belongings (handbags, books, etc.) must be left outdoors and must not be placed in the clean room.
4.1.2 If vendors or guests wish to enter the cleanroom to perform work or visit, they must be accompanied and guided by relevant personnel of the company; vendors or guests who wish to enter the cleanroom must change their shoes into indoor slippers (or put on shoe covers) in the shoe changing area in accordance with regulations.
4.1.3 The following persons are not allowed to enter the cleanroom:
- Non-operating personnel or those without prior permission;
- Those who have not changed into special slippers or shoe covers;
- Those who have just finished intense exercise and are sweating;
- Those who wear makeup and lipstick.
4.1.5 The following items are not allowed to be brought into the cleanroom:
- Equipment, spare parts, measuring instruments and other items that have not been cleaned;
- Cardboard boxes and untreated recording or note paper, photocopied data, etc.;
- Pencils, erasers, ink, etc.;
- Cigarettes, cosmetics, toilet paper, food and beverages, etc.;
- Operators' personal items such as lighters, jewels, decorations, wallets, keys, handbags, small diaries or other personal items.
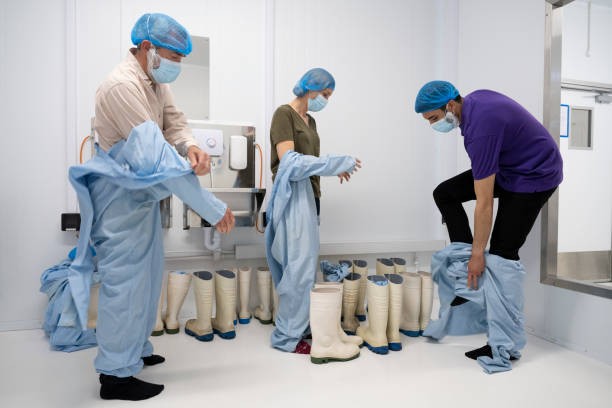
Figure 2: Cleanroom personnel management
4.4 Hygiene requirements for clean room personnel
- 4.4.1 Work clothes and work hats must be neatly worn
- 4.4.2 Keep hands, nails and face clean and hygienic
- 4.4.3 People wearing glasses must wash their eyes when entering the clean room
- 4.4.4 Do not comb your hair in the clean room, and do not touch your hair
- 4.4.5 Do not use cosmetics or nail polish in the clean room
- 4.4.6 Do not use jewelry in the clean room
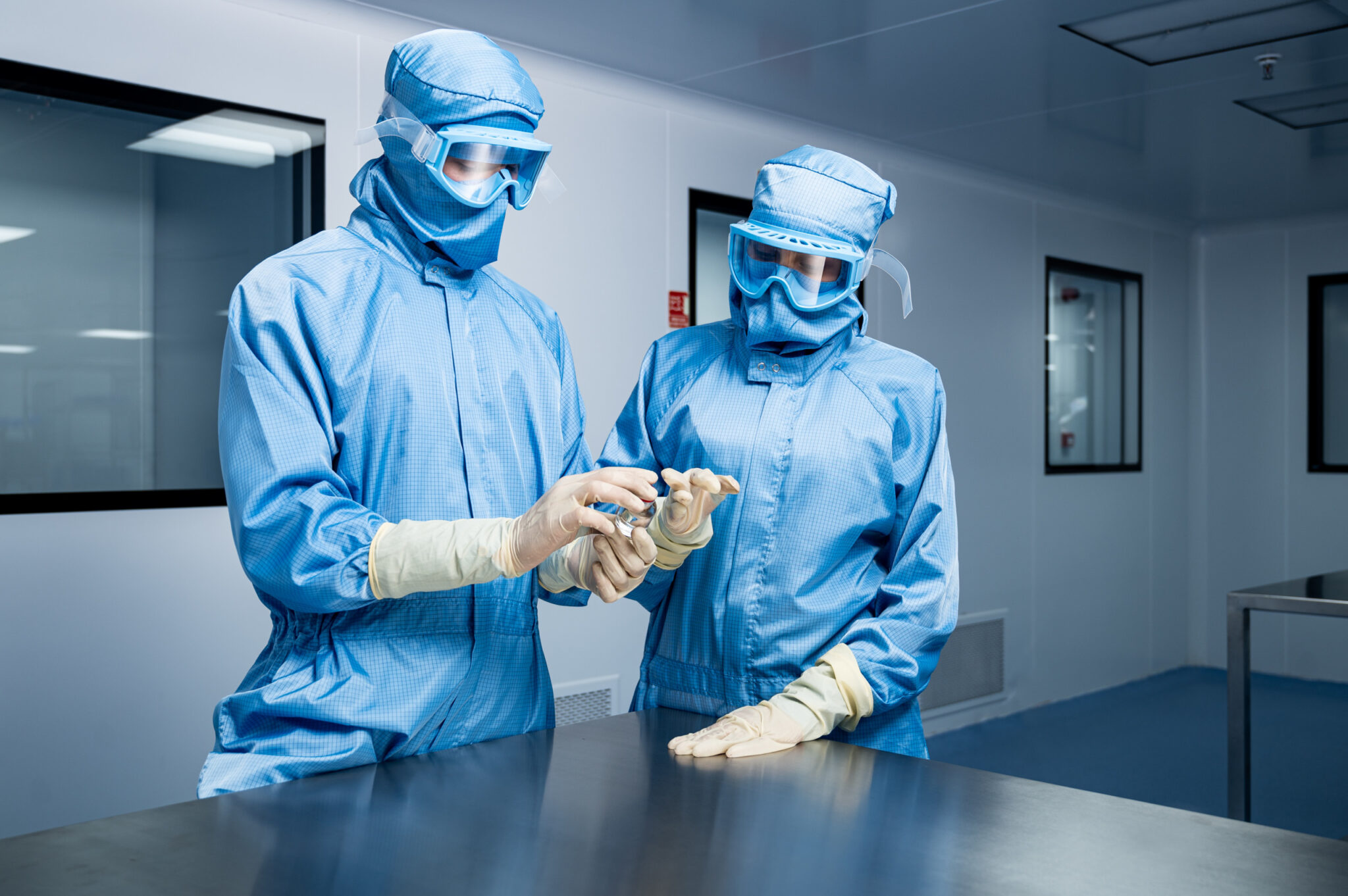
Figure 3: Hygiene requirements for clean room personnel
Related Information
What is A CleanRoom management system?
Users often want a clear explanation of what constitutes a cleanroom management system, including its role in maintaining cleanliness, managing contamination, and ensuring that the environment meets specific industry standards.
What are the components of a cleanroom management system?
People are curious about the essential components of the system, such as air filtration (hepa/ULPA filters), HVAC systems, environmental monitoring tools, contamination control measures, and personnel management protocols.