ISO Class 5 Cleanrooms represent one of the highest levels of cleanliness achievable in a controlled environment and are commonly used in industries such as pharmaceuticals, biotechnology and microelectronics. Achieving ISO Class 5 standards ensures that contamination is minimized, safeguarding process and product integrity.
Key Features and Requirements of ISO Class 5 Cleanrooms
ISO Class 5 cleanrooms are characterized by strict contamination control, thanks to their careful design and advanced filtration systems.
Particle Limits
ISO Class 5 cleanrooms must limit the number of particles larger than 0.5 microns to 3,520 per cubic meter, which emphasizes their stringent cleanliness. Companies like Deiiang™ use precise monitoring to maintain these standards.
Airflow and Air Changes
To ensure the cleanliness of ISO 5 Cleanrooms, airflow is typically unidirectional with air changes ranging from 240 to 480 times per hour. High-efficiency particulate air (HEPA) or ultra-low penetration air (ULPA) filters are typically used.
Cleanroom ISO Class
ISO cleanrooms are classified based on air cleanliness and the number of particles allowed. ISO 5 class requires high standards of air purity and minimal particle contamination.
Architectural design and structural elements
ISO 5 Cleanrooms are a high cleanliness class in ISO 14644 that is designed to limit the number of particles in the air and are suitable for demanding environments such as pharmaceuticals, microelectronics, and aerospace.
The following are some key points related to the construction and design of ISO 5 cleanrooms to ensure that the performance and safety of the cleanroom meet the stringent conditions of ISO 5 class.
Double-layer return air wall panels:
The return air wall panels must be designed to meet the requirements of efficient air circulation and particle control.
The double-layer structure can enhance strength and sound insulation while ensuring the stability of airflow. This design helps to filter particles and reduce airflow disturbances.
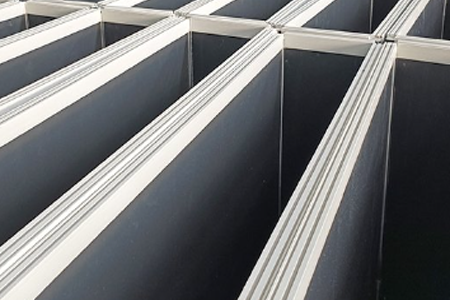
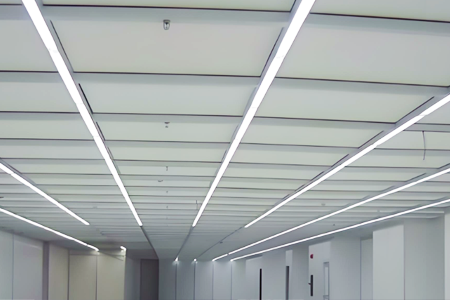
Suspended ceilings:
Suspended ceilings are usually equipped with high-efficiency air filtration systems (HEPA or ULPA filters) to ensure that the air particle concentration meets ISO 5 standards.
The suspended ceiling structure should be tight and seamless to avoid dust accumulation and particle penetration. The material is corrosion-resistant and easy to clean.
Raised aluminum floor:
Raised aluminum floor allows for flexible airflow distribution and cable routing. Its anti-static properties are very important, especially in applications in the electronics industry. The sheet needs to be easy to clean, resistant to chemical corrosion, and provide sufficient load-bearing capacity.
Purification steel door:
Purification steel doors need to be airtight to prevent external contaminants from entering the cleanroom. They are usually made of 304 or 316 stainless steel, remain smooth and seamless, and are easy to disinfect and clean. The design of the door should consider convenient opening in emergency situations.
Double-glazed hollow window
The window design should ensure sound insulation, heat insulation, and avoid condensation. Double-glazed glass provides additional insulation and sound insulation, and the hollow design helps prevent particles from entering the window gap. The window needs to be easy to clean to prevent particle accumulation.
Filter system for ISO 5 cleanroom
HEPA and ULPA filters are essential in ISO 5 environments. They effectively limit the concentration of particulate matter in the air to meet the strict requirements of the iso 14644-1 standard.
Filter Type | Particle Size | Efficiency | Applications |
---|---|---|---|
HEPA | ≥0.3 microns | 99.97% | Pharmaceuticals, Electronics |
ULPA | ≥0.12 microns | 99.999% | Semiconductor, Aerospace |
High efficiency filter:
Use HEPA (High Efficiency Particulate Air) or ULPA (Ultra Low Penetration Air) filters, which can remove particles not less than 0.3 microns and 0.12 microns respectively, with very high efficiency, suitable for environments with extremely high cleanliness requirements.
Filter level setting:
Set different levels of filters in different areas as needed, for example, use pre-filters to remove larger particles when supplying air, and then use HEPA or ULPA filters for fine filtration.
Layer-by-layer filtration:
Design a multi-stage filtration system to ensure that large particles are removed in the primary filtration stage, reduce the burden on HEPA/ULPA filters, and extend their service life.
Air flow design:
Most ISO 5 Clean rooms use non-unidirectional flow (turbulent) or unidirectional flow (laminar) systems, and select appropriate airflow patterns according to application needs to reduce particle deposition and cross contamination.
Pressure control:
Maintain a positive pressure slightly greater than the external environment in the clean room to prevent external unfiltered air from infiltrating the room. Configure a differential pressure monitoring system when necessary.
Regular testing and maintenance:
Develop a rigorous maintenance and monitoring strategy, including regular leak detection, efficiency testing, and replacement of filters when necessary, to ensure that the filtration system is always in optimal performance.
ISO-5 Cleanroom Flooring
ISO 5 cleanroom floors are designed to be safe, easy to clean, and help maintain high standards of air cleanliness. Here are some key considerations for cleanroom floors:
Material selection: Floor materials should be smooth, seamless, dust-proof, and anti-static. For example, epoxy resin flooring or PVC membrane, which have excellent chemical resistance and abrasion resistance and are easy to clean.
Anti-static properties: Especially in the electronics or semiconductor industries, floors must have anti-static functions to prevent static electricity accumulation and discharge, which may damage delicate equipment or contaminate products.
Seamless installation: Floors should be seamless to reduce the possibility of particle accumulation and easy to clean. The treatment of seams and corners should be smooth to prevent particles from hiding.
Chemical resistance: Floor materials should be able to resist a variety of cleaners, disinfectants, and other chemicals that may be used to ensure durability and easy maintenance.
Color and light reflection: Light-colored floors are often used to help reflect light, increase the brightness of the indoor environment, and help detect particulate contamination.
Load-bearing capacity: The floor must be able to withstand the load of personnel, equipment, and various processing operations to ensure durability and safety.
ISO-5 Cleanroom Ceiling
The ceiling is designed to support integrated air filtration devices to ensure consistent air quality and airflow distribution. The ceiling design of an ISO 5 cleanroom is very critical because it plays an important role in the air circulation and cleanliness of the cleanroom. Here are some design features about ISO 5 cleanroom ceilings:
High-efficiency air filter (HEPA/ULPA) integration:
The ceiling system usually integrates HEPA or ULPA filters, which can effectively remove particulates from the air to ensure cleanliness reaches ISO 5 standards.
Dust-free structure:
The ceiling surface should be smooth and seamless to prevent dust adhesion and particulate aggregation to reduce the risk of contamination.
Corrosion resistance and easy cleaning:
The material used to make the ceiling should be durable and chemically resistant, while being easy to clean and disinfect to maintain strict hygiene conditions.
Airflow optimization:
The design should ensure uniform downflow to reduce turbulence and recirculation of particles. Fully distributed ceilings or integrated air supply designs are usually selected to achieve the best airflow pattern.
Stable structural support
The ceiling needs a solid support structure to support filters and other equipment while withstanding the pressure during cleanroom maintenance operations.
Flexibility:
The ceiling system should be able to adapt to the installation requirements of different lamps and equipment, providing sufficient flexibility for technical maintenance and space adjustments.
ISO-5 Cleanroom Lighting
The lighting must provide sufficient illumination while minimizing the generation of particles. LED lamps are widely used due to their low particle emission and energy-saving characteristics.
In ISO 5 cleanrooms, the lighting design not only needs to meet basic lighting needs, but also needs to take into account air cleanliness and operational convenience. The following are some important considerations for ISO 5 cleanroom lighting:
Dust-proof design:
The lighting fixture must be sealed to prevent dust and particles from entering the interior of the fixture, thereby avoiding the impact on cleanliness. The surface of the fixture should be smooth, seamless, and easy to clean.
Light source type:
LED lamps are a common choice because they are energy efficient, have low heat dissipation and long life, while not releasing too much heat, which helps maintain temperature control in the room.
Uniform lighting:
The lighting design should support uniform light coverage to reduce shadows and wrap all operating spaces to ensure good visibility for operators. Consider using diffusers or light-homogenizing hoods to achieve this.
Maintenance convenience:
The lighting system should be easy to maintain and replace light sources without affecting the Cleanroom cleanliness requirements. Usually, the design reserves areas for easy maintenance.
Low glare:
Designing lighting with low glare can reduce eye fatigue and improve operator comfort and work efficiency.
Dimming capability:
According to specific operational needs, equipped with an adjustable lighting system to achieve the best light intensity in different scenarios.
ISO-5 Cleanroom Dressing Room/Airlock
The design and management of dressing rooms and airlocks directly affect the overall cleanliness of ISO 5 cleanrooms. Reasonable planning and strict operating specifications can effectively reduce particulate contamination and keep indoor air clean. The following are some design and operation suggestions for dressing rooms and airlocks:
1. Dressing Room
Zoning Management: Set up multiple partitions, such as outerwear changing area, hand cleaning area and clean clothing wearing area, to reduce the risk of pollutants being brought in step by step.
High-efficiency filtration and ventilation: The dressing room should be equipped with a HEPA or ULPA filtration system to ensure that the air cleanliness is close to or reaches the ISO 5 standard, especially in the clean clothing wearing area.
Material selection: Walls, floors and ceilings should use smooth, easy-to-clean, anti-static materials to prevent the accumulation of particles.
Storage facilities: There are dedicated lockers and hanging facilities for storing personal items and clean clothing to keep the clothing clean.
Mirrors and other auxiliary facilities: Install mirrors and hand disinfection facilities to facilitate personnel to wear clean clothing correctly and disinfect their hands.
2. Airlock
Access control: Airlocks are usually located at the entrance and exit of cleanrooms. Double-door systems are used to ensure that only one door is open at the same time to prevent cross-contamination of air.
Air flow control: Equipped with airflow guidance system or positive pressure system to push airflow to less polluted areas, and cooperate with high-efficiency filtration equipment to keep airflow clean.
Interface reminders and instructions: Provide clear signs and operation guidelines to let staff understand the correct entry procedures and cleanroom clothing requirements.
Monitoring and recording: Equipped with monitoring equipment to record personnel entry and exit, if necessary, keep records of regional pressure, temperature and humidity, etc., so that they can be reviewed when necessary.
Cost of building an ISO 5 cleanroom
The cost of building an ISO 5 cleanroom can be high and will vary depending on the size of the cleanroom, the complexity of the design, and the integration of materials and technologies.
1. Size of the cleanroom
The size of the cleanroom is one of the main factors that determine its construction cost. Typically, the cost per square foot of an ISO 5 cleanroom ranges from $250 to $600, depending on specific requirements and regional construction costs.
For example, a 1,000-square-foot cleanroom may cost between $250,000 and $600,000. Larger cleanrooms may benefit from economies of scale, potentially reducing the cost per square foot.
2. Complexity of design
The complexity of a cleanroom design can significantly affect costs. More complex designs require advanced HVAC systems, specialized wall materials, or unique layouts, which will increase costs. For example, a simple cleanroom that meets basic requirements may cost about $250 per square foot, while a complex design with advanced control systems may cost up to $600 per square foot or more.
3. Required materials and technologies
The selection of materials and technologies is also critical to overall expenditures. Cleanroom environments require high-quality materials that meet stringent cleanliness standards. For example, the use of stainless steel, specialized wall panels, and HEPA or ULPA filtration systems will increase costs.
High-efficiency particulate air (HEPA) filters cost between $300 and $1,500, depending on their size and efficiency rating. In addition, advanced monitoring systems to ensure compliance with ISO standards will further increase construction costs.
Factor | Cost Range | Impact |
---|---|---|
Size | $250 - $600 per sq ft | Larger size reduces cost per sq ft |
Complexity | $250 - $600 per sq ft | Advanced systems increase cost |
Materials | Varies | Specialized materials add cost |
Maintenance and Protective Clothing Procedures
Regular maintenance includes ongoing monitoring and verification of air quality and particulate counts. Protective clothing procedures are essential and include full-body suits, gloves, masks, and other protective gear to minimize contamination.
For companies like Deiiang™, maintaining these standards is not just about compliance, but about providing the best environment for their operations.
FAQs
How often should an ISO Class 5 cleanroom be tested?
Typically, they should be tested and verified at least annually, but critical process areas may require more frequent inspections.
What is the difference between a HEPA filter and a ULPA filter?
HEPA filters remove 99.97% of particles larger than 0.3 microns, while ULPA filters capture 99.999% of particles smaller than 0.12 microns, providing greater efficiency.
Understanding the nuances of an ISO Class 5 cleanroom can significantly impact product quality and consistency, helping to ensure the highest standards of cleanliness and operational efficiency.