How does a downflow cleanroom work?
Downflow spray booths utilize filtered, controlled airflow to minimize contamination and are essential to maintaining a clean environment across a variety of industries.
Contaminants are removed from the incoming air using either a high - efficiency particulate air (hepa) or ultra - low penetration air (ULPA) filter. The filtered air then flows downward in a laminar flow to create a sterile work environment. This downward airflow acts as a barrier to prevent contaminants from rising back into the clean zone while removing any particles that may have settled on the work surfaces.
The design often incorporates a negative pressure system to ensure that the air in the spray booth is always cleaner than the surrounding environment. This pressure differential prevents unfiltered air from entering the spray booth, protecting the integrity of the workspace.
In addition, spray booths are often equipped with monitoring systems that track airflow and filter conditions, allowing operators to maintain optimal working conditions.
How a Downflow Cleanroom Works
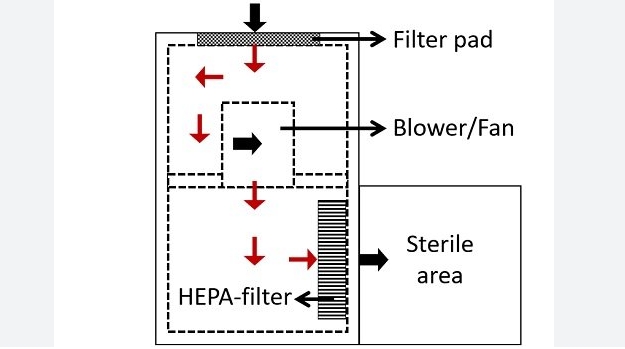
Supply Air: Fresh air is drawn into the system and purified by a high - efficiency particulate air (HEPA) or ultra - high - efficiency particulate air (ULPA) filter to ensure that only Clean air enters the cleanroom.
Downflow Airflow: Filtered air flows downward, surrounding the workspace with contaminant - free air.
Contaminant Removal: The airflow captures any particulate matter, preventing it from settling on surfaces or being inhaled by operators.
Air Circulation or Exhaust: Air can be circulated through additional filters or exhausted outside the building to maintain optimal environmental conditions within the cleanroom.
Negative Pressure: A slightly negative pressure can be maintained, preventing contaminants from escaping the work area, thereby improving safety and compliance.
Construction of a Downflow Cleanroom
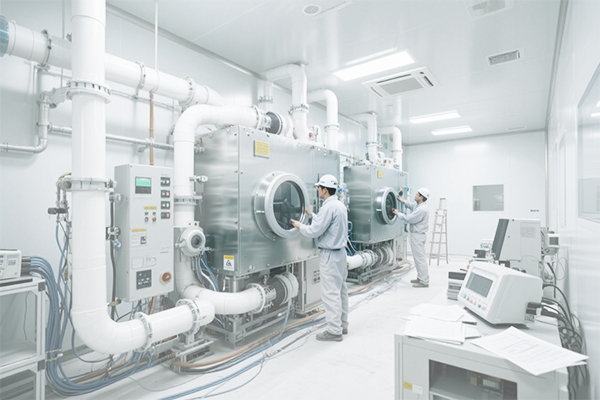
The specific operational needs need to be considered from the design stage, including space, airflow requirements, and compliance with standards such as ISO Cleanroom standards. Incorporating the latest filtration and airflow technologies ensures that the cleanroom maintains a clean environment efficiently. The construction phase includes precise calibration and testing to ensure that the cleanroom meets all operational and safety requirements.
Cost of a Downflow Cleanroom
Factors Affecting Cost | Details |
---|---|
Size Specifications | Larger or more specialized Cleanrooms require more resources |
Material Selection | Quality materials extend life and improve efficiency, reducing long - term costs |
Installation | Requires professional setup with necessary budget allocation |
Maintenance | Regular upkeep includes filter replacement and inspections |
Factors that affect the cost of a downflow cleanroom include size specifications, material selection, installation, and maintenance calculations. Larger or more specialized CleanRooms require more resources, and quality materials help extend life and improve efficiency, thereby reducing initial investment, and installation and regular maintenance also require the necessary budget.
Maintenance of Downflow Spray Booths

Maintenance Item | Frequency/Details |
---|---|
Filter Replacement | Every 6 - 12 months (varies by usage and environment) |
Component Inspections | Regular checks to ensure proper function |
Operator Training | On proper use and safety procedures |
Monitoring System | Continuous use to detect issues early |
Regular maintenance is essential for optimal performance of downflow spray booths. This includes regular filter replacement to maintain air purity; regular inspections to ensure that all components are functioning properly; operator training on proper use and safety procedures; monitoring system use to help detect problems early and maintain compliance with safety standards; maintaining a good environment in the spray booth is essential for long - term operation, and finally keeping accurate records and adhering to compliance standards is essential to the integrity and safety of operations. This includes maintaining a maintenance schedule, logs of filter changes and performance indicators.
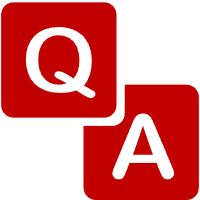
What is the main function of a downflow spray booth?
Downflow spray booths provide a controlled environment by controlling airflow to effectively remove contaminants.
How often should filters in downflow spray booths be changed?
The frequency of replacement depends on usage and environmental conditions, but it is generally replaced every 6 - 12 months.