How Does a downflow booth Work?
An In-Depth Analysis of Containment and Filtration
Maintaining a sterile environment is critical in industries such as pharmaceuticals, microElectronics, and healthcare. downflow booths, also known as downflow cabinets, utilize advanced filtration and Airflow Principles to ensure contamination-free working conditions. By understanding how these systems operate, users can optimize safety and efficiency.
This article provides a detailed overview of the working mechanisms of downflow booths, supported by industry standards and practical examples, incorporating insights from Deiiang™, with product design by Deiiang Jason.peng.
Filtered Airflow: The Foundation for Contamination Control
hepa Filtration Technology
hepa filters are integral to downflow booths, capable of capturing 99.97% of airborne particles ≥0.3 microns. These filters comply with international standards such as EN 1822 and ASHRAE 170, ensuring high efficiency. Inside the booth, the hepa filter cleans incoming air, creating a consistently purified environment.
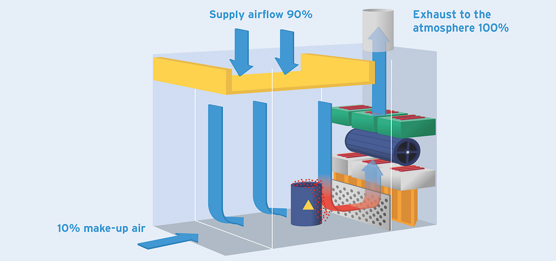
Diagram of a typical downflow booth system
Air Quality and Flow Rate
The filtered air is supplied at a rate typically between 0.36 and 0.45 meters per second, following ISO 14644-4 guidelines. At an area of 1 m², this results in a flow of 0.4 m³/sec, offering approximately 14 air changes per minute, which effectively minimizes particle resuspension.
Downward Direction: Creating a Laminar, Protective Flow
Unidirectional Airflow Pattern
The purified air is directed downward from the ceiling-mounted hepa filters, generating a laminar flow that pushes contaminants away from the operator's workspace. This vertical airflow minimizes turbulence and prevents particles from settling or resuspending within the booth.
Operational Example:
Suppose the cross-sectional area of the airflow is 1 m²; with a velocity of 0.4 m/sec, the volumetric flow rate (Q) is:
Q = Area × Velocity = 1 m² × 0.4 m/sec = 0.4 m³/sec
This airflow ensures rapid removal of airborne particles, maintaining a clean working zone.
Containment: Strategically Capturing Contaminants
Low-Level Exhaust Grilles
Contaminated air is captured through low-level exhaust grilles placed at the booth's base. These grilles are designed to efficiently draw contaminated air through the filtration system before it escapes into the environment.
Filtration System Workflow
Captured air passes sequentially through primary pre-filters, secondary filters, and hepa filters. According to EN 1822 standards, each stage ensures the removal of residual particles, maintaining the integrity of the clean environment.
Step | Description | Standards |
---|---|---|
1 | Air enters filtration system | ISO 14644-4 |
2 | Passes through pre-filters | EN 1822 |
3 | Passes through hepa filters | EN 1822 |
Negative Pressure: Enhancing Containment
A slight negative pressure (around 10-15 Pa) is maintained within the booth by exhausting a portion of the filtered air. This ensures that any leaks cause inward airflow, preventing airborne contaminants from escaping, following OSHA and ASTM E2352 standards.
Quantitative Illustration:
If the inflow is 0.4 m³/sec and the exhaust is adjusted to 0.41 m³/sec, the resulting negative pressure prevents leaks and guarantees containment safety.
What is the Difference Between Downflow and horizontal flow?
Feature | Downflow Booth | horizontal flow Booth |
---|---|---|
Airflow Direction | Vertical from top down | Horizontal from one side to the other |
Application | Minimal particle disturbance | Larger workspaces with multiple operators |
Contamination Control | Prevents contaminants from rising | May allow particles to settle |
Downflow and horizontal flow booths utilize different airflow patterns for cleanroom applications. The vertical airflow in downflow booths effectively prevents contaminants from rising, creating a more stable clean zone compared to horizontal flow systems.
Laminar Flow Principle
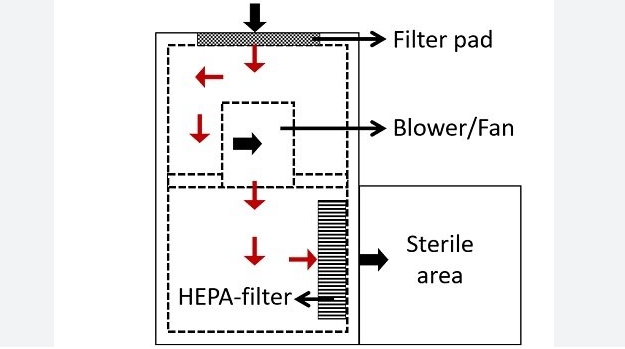
The laminar flow principle is fundamental to the operation of downflow booths. This principle involves the movement of air in smooth, parallel layers, minimizing turbulence and preventing the mixing of clean and contaminated air.
- Air is drawn through HEPA or ULPA filters and cleaned
- Creates a protective barrier over the work surface
- Reduces likelihood of airborne particles settling
- Essential for pharmaceuticals, Electronics, and biotechnology
Unlike turbulent flow systems, laminar flow ensures that the air remains clean and stable, making it essential for applications requiring high cleanliness standards.
How to Implement the Design of a Downflow Booth?
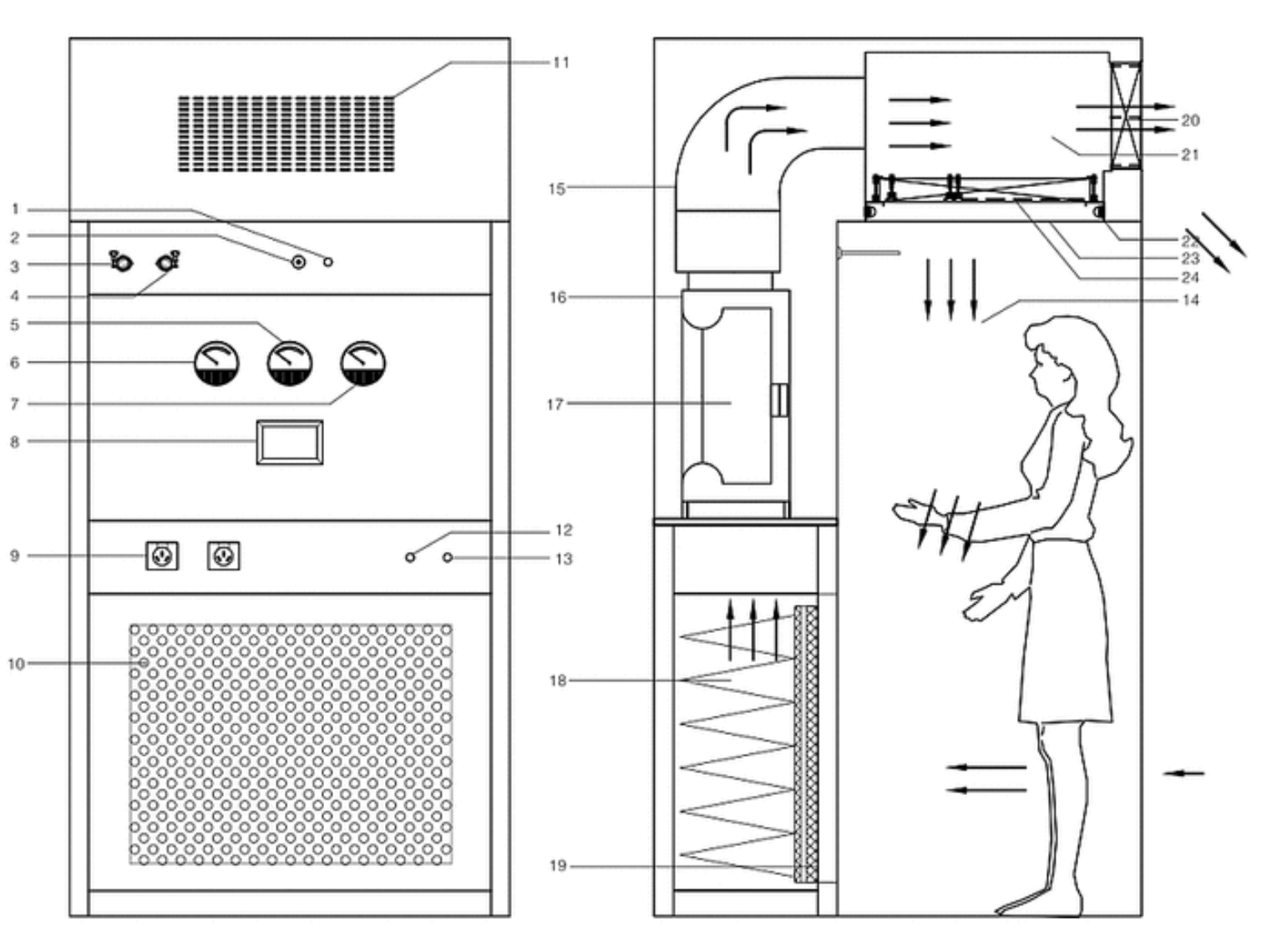
1. Initial Planning
Identify specific needs including cleanliness level and space constraints.
2. Technical Specifications
Include HEPA/ULPA filters, variable-speed fans, and compliant materials.
3. Installation
Test airflow patterns post-installation for effective operation.
Downflow Booth Construction Cost
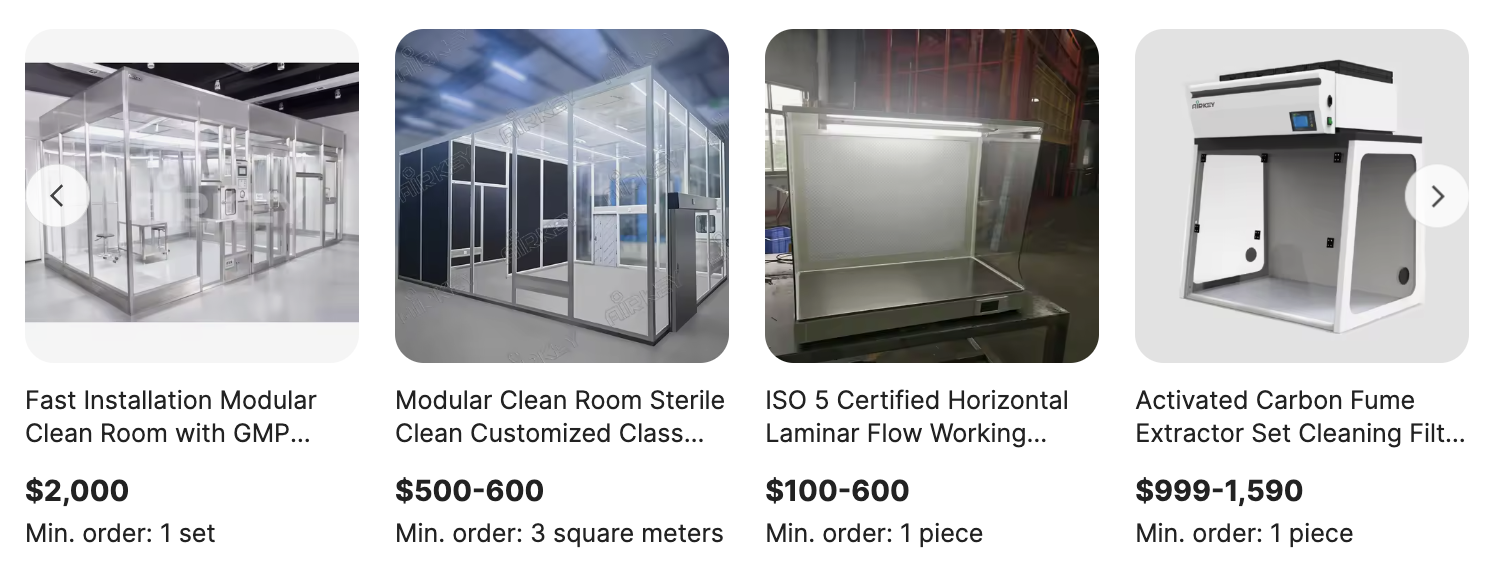
Factor | Impact on Cost |
---|---|
Size and Specifications | Larger booths or advanced features increase cost |
Material Selection | High-quality materials increase initial cost but ensure durability |
Installation and Maintenance | Professional services add to overall expenses |
Compliance Requirements | Meeting standards like ISO 14644 may increase costs |
How to Extend the Life of a Downflow Booth?
Routine Filter Replacement
Replace filters according to manufacturer guidelines to ensure effective air purification.
Scheduled Maintenance
Implement regular cleaning and inspection of components like fans and ducts.
Operator Training
Train operators on best practices to prevent misuse and contamination.
monitoring Systems
Track airflow rates, pressure differentials, and filter conditions.
Environmental Control
Minimize dust and particulate matter in the surrounding area.
Documentation
Maintain records of maintenance activities and compliance with standards.
By implementing these strategies, the life of a downflow booth can be significantly extended, ensuring continued high performance.
Summary and Conclusion
A downflow booth operates by drawing clean, HEPA-filtered air downward at a controlled velocity, creating a laminar flow that pushes contaminants away from the operator. Contamination is captured by low-level exhausts, passing through multi-stage filtration before recirculation or external exhaust. The slight negative pressure maintained inside the booth ensures robust containment, aligning with international standards such as iso 14644-4 and EN 1822. With the expertise of Deiiang™, product designer Deiiang Jason.peng has crafted solutions that maximize efficiency, safety, and compliance.
Frequently Asked Questions
1. What is the primary function of HEPA filters in a downflow booth?
To eliminate 99.97% of particles ≥0.3 microns, ensuring air purity.
2. How does downward airflow prevent contamination?
It creates a unidirectional laminar flow that pushes contaminants away from the work zone.
3. Why is negative pressure important in a downflow booth?
It ensures any leaks result in inward airflow, preventing contaminants from escaping.
4. What international standards govern downflow booth performance?
ISO 14644-4, EN 1822, ASTM E2352, and OSHA guidelines.
5. How often should filters be checked or replaced?
In general, filters should be inspected annually or when pressure differentials increase beyond recommended levels.
© 2023 Downflow Booth Technology | Technical Article