Exploring the key sectors relying on controlled environments for precision manufacturing
1. Pharmaceutical industry
The pharmaceutical industry extensively utilizes hardwall clean rooms to ensure product safety and efficacy. According to the FDA, clean rooms are critical in the manufacturing of sterile products, requiring environments that meet at least ISO5 standards for particulate contamination. This ensures that the airborne particulate levels are limited to no more than 3,520 particles per cubic meter for particles ≥0.5 μm.
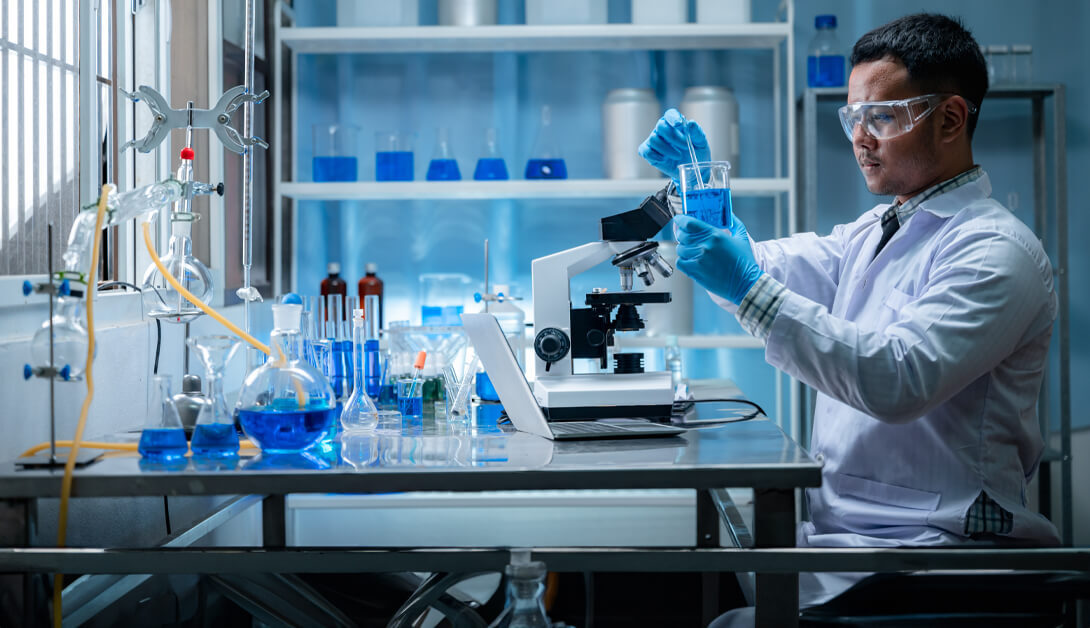
Why Clean Rooms are Essential in Pharma
- • Prevention of microbial contamination in sterile products
- • Ensuring product purity to meet regulatory standards
- • Controlling environmental factors like temperature and humidity
2. Biotechnology Sector
Biotechnology companies rely on hardwall Clean rooms for research and development as well as production processes. These facilities often require ISO7 or better, which permits up to 352,000 particles per cubic meter. The stringent control of contaminants supports the development of biologics, vaccines, and gene therapies, where purity is essential for product safety.
Key Applications in Biotechnology
- • Cell culture and tissue engineering
- • Production of recombinant proteins
- • Development of gene therapy vectors
- • Vaccine formulation and filling
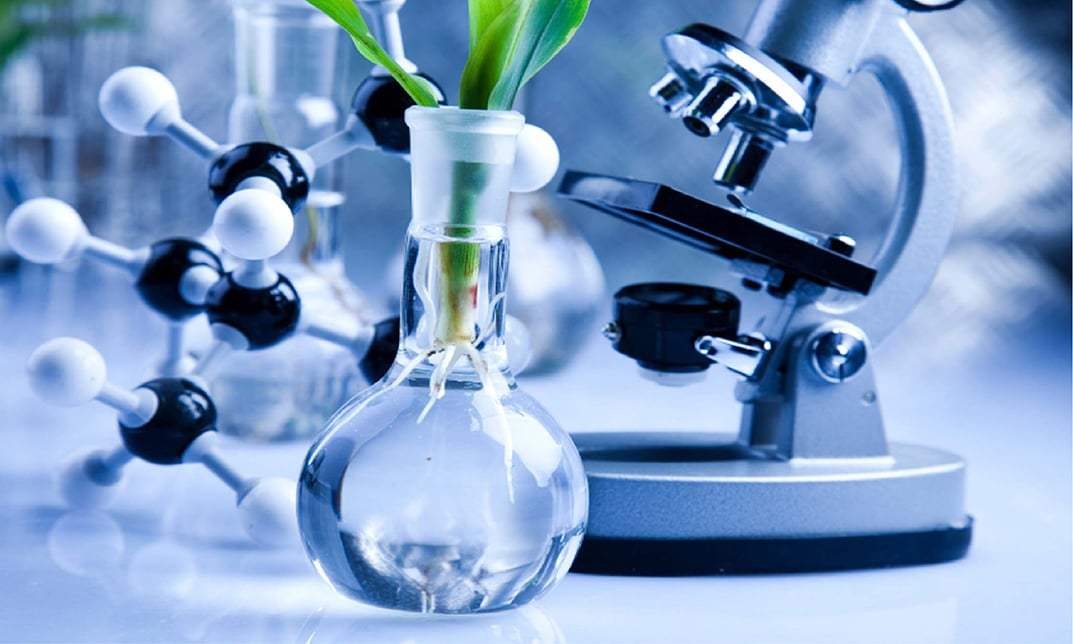
3. Semiconductor Manufacturing
The semiconductor industry mandates highly controlled environments to manufacture chips and other Electronic components. Hardwall clean rooms typically operate at ISO1 to ISO 5 standards, with Class 1 allowing only 1 particle per cubic meter of 0.3 μm size. This extreme cleanliness is vital, as even a single particle can cause defects in microchips, leading to significant financial losses.
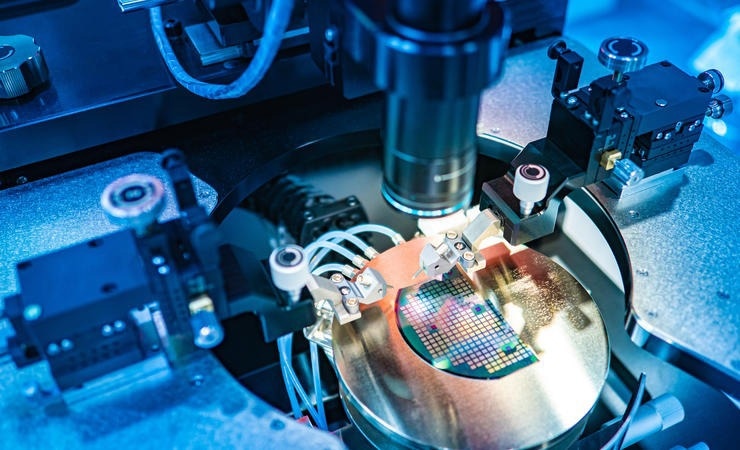
Clean room standards in Semiconductor
Standard | Particle Limit (per cubic meter) | Application |
---|---|---|
ISO 1 | ≤1 particle (≥0.1μm) | Advanced semiconductor manufacturing |
ISO 5 | ≤3,520 particles (≥0.5μm) | General semiconductor processing |
Class 1 | ≤1 particle (≥0.3μm) | Ultra-precision chip manufacturing |
4. Aerospace and Defense
Aerospace and defense industries utilize hardwall clean rooms to assemble sensitive components, such as satellites and aircraft electronics. These environments often meet ISO5 standards, ensuring low levels of contamination. The rigorous requirements help prevent malfunctions in critical systems, which could endanger missions and safety.
Critical Components Assembled in Clean Rooms
- • Satellite avionics and control systems
- • Aircraft communication and navigation equipment
- • Precision sensors for environmental monitoring
- • Defense electronics and guidance systems
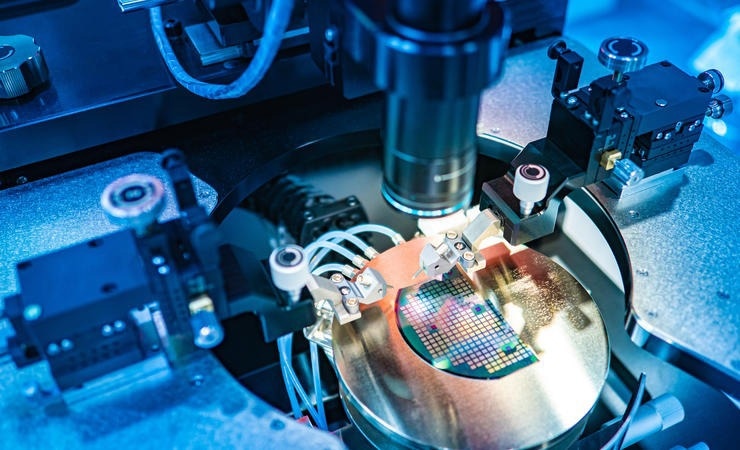
5. Medical Device Manufacturing
The production of medical devices requires strict adherence to cleanliness standards. Hardwall clean rooms are commonly maintained at ISO7 or higher, allowing a reasonable level of particles while ensuring that products are free from contamination. According to ISO 13485, Manufacturers must demonstrate consistent compliance with quality management systems to ensure device safety.
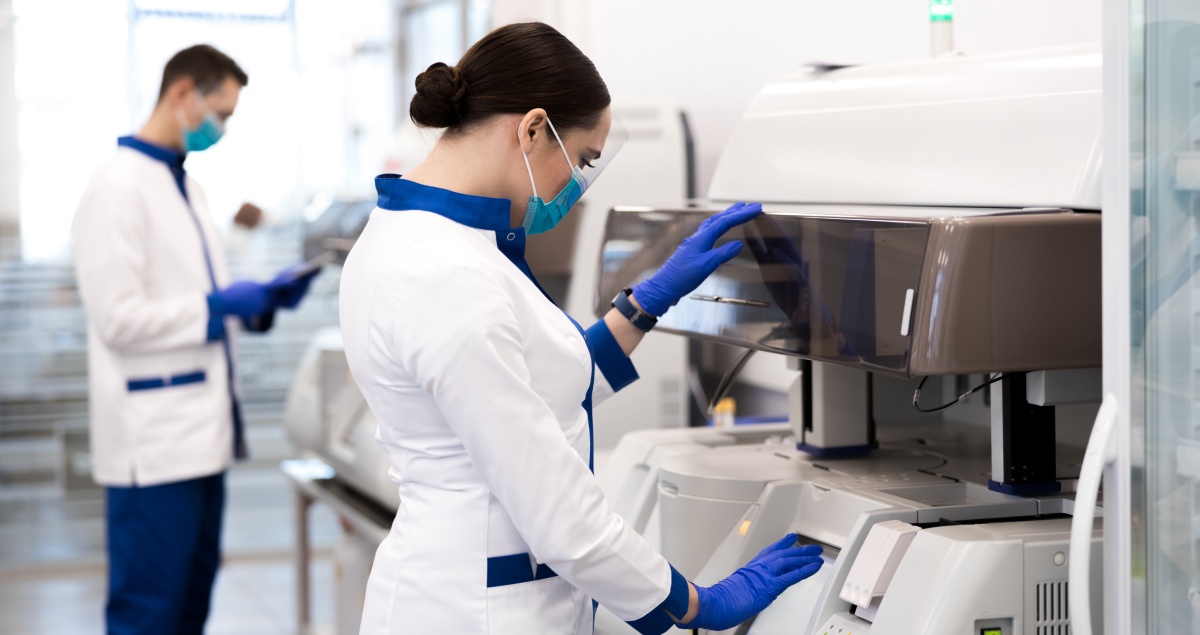
Types of Medical Devices Manufactured in Clean Rooms
Surgical Instruments
Scalpels, forceps, and retractors
Implantable Devices
Stents, pacemakers, and artificial joints
Diagnostic Equipment
Blood analyzers and imaging devices
Disposable Supplies
Syringes, catheters, and surgical gloves
6. Optical Industry
The optical industry, particularly in the manufacturing of lenses and sensors, utilizes hardwall clean rooms to minimize defects caused by dust and other contaminants. Hardwall clean rooms typically operate at ISO6 or better, which allows up to 83,000 particles per cubic meter. This control is crucial for producing high-quality optical products with precise specifications.
Optical Products Requiring Clean Rooms
- • Camera lenses for smartphones and DSLRs
- • Optical fibers for telecommunications
- • Microscope objectives and eyepieces
- • Sensors for medical imaging equipment
- • Laser components and optical mirrors
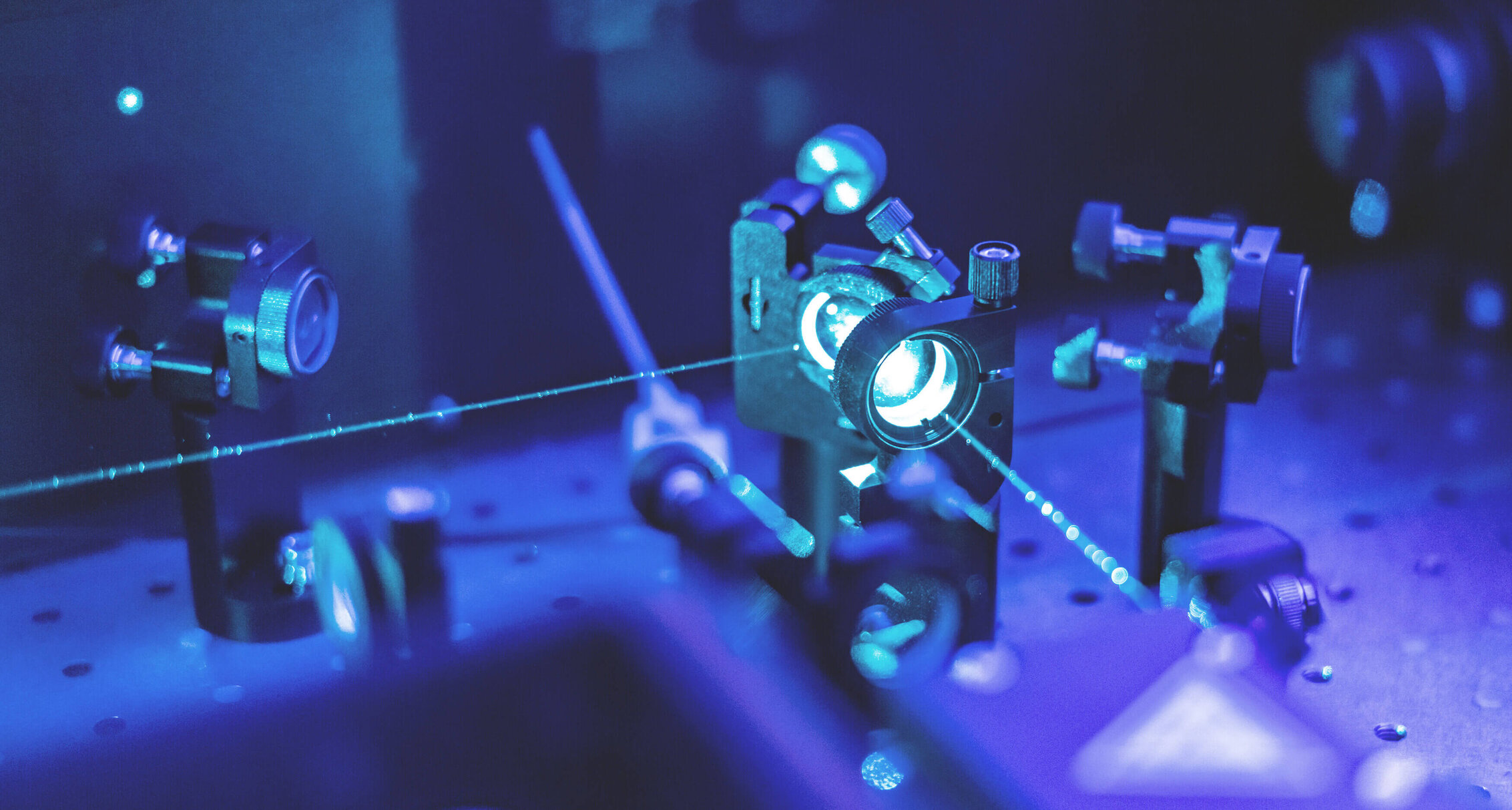
Key Clean Room Standards and Guidelines
Standard/Guideline | Description | Relevant Industries |
---|---|---|
ISO 14644 | Specifies air cleanliness classification for clean rooms | All industries using clean rooms |
ISO 13485 | Quality management for medical device industry | Medical device manufacturing |
FDA Guidelines | Regulations for pharmaceutical and biotech industries | Pharmaceuticals, biotechnology |
CFR Title 21 | Current Good Manufacturing Practices (cGMP) | Pharmaceuticals, medical devices |
ISO 9001 | General quality management system standard | All industries with quality management needs |
Information on hardwall clean room applications in various industries