6 ft Medical Clean bench
Reference Price:US$from $1500
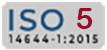



Cleanroom
6 ft Medical Clean bench
Choose your installation & validation options below
Quantity:
Choose your upgrade options
Quantity:
Summary
6 ft Medical Clean bench
Validation
Installation & Validation
Find Similar Products
-
3 ft Medical Clean bench
US$
Min. Order:1 Set -
4 ft Medical Clean bench-Horizontal Flow
US$
Min. Order:1 Set -
6 ft Medical Clean bench
US$
Min. Order:1 Set -
7 ft Medical Clean bench-Single side, Ho
US$
Min. Order:1 Set -
8 ft Medical Clean bench- Horizontal Flo
US$
Min. Order:1 Set -
5 ft Medical Clean bench-Single side, Ho
US$
Min. Order:1 Set
Product Briefing
A 6 ft medical clean bench is a laboratory device designed to provide a sterile, particle-free workspace over a six-foot area, ideal for medical, pharmaceutical, and research applications. Utilizing a HEPA filter to produce laminar airflow, it ensures contamination-free operations across a larger surface, accommodating more extensive experiments and multiple tasks while maintaining a high level of cleanliness and safety.. Here’s a detailed overview of its features, functions, and benefits:
Applications
Microbiology: Ideal for working with cultures, cell lines, and other sensitive biological materials.
Pharmaceuticals: Used in the preparation and compounding of sterile medications.
Electronics: Suitable for assembling and handling sensitive electronic components that may be susceptible to dust or static.
Research: Provides a clean environment for various scientific experiments and procedures.
Models
Vertical Laminar Flow Clean Bench | |||
Model | GDC-SPT-01 | GDC-SPT-02 | GDC-SPT-03 |
3 ft | 4ft | 5ft | |
External size W×D×H(mm) | 1000×850×1500 | 1200×850×1500 | 1500×850×1500 |
Internal Size W×D×H(mm) | 960×600×600 | 1160×600×600 | 1460×600×600 |
HEPA Filter(mm) | 905×585×69×1 Pcs | 1105×585×69×1 Pcs | 1405×585×69×1 Pcs |
HEPA Filter Efficiency | 99.95%@0.3μm | 99.95%@0.3μm | 99.95%@0.3μm |
G4 Pre Filter(mm) | 500×375×21×1 Pcs | 500×375×21×1 Pcs | 745×375×21×1 Pcs |
Noise | 52~62dB(A) | 52~62dB(A) | 52~62dB(A) |
Fan Pressure | 260pa | 260pa | 260pa |
Fan Power (W) | 200W×1 Pcs | 200W×1 Pcs | 200W×1 Pcs |
LED Lamp Power(W) | 12W×1 Pcs | 18W×1 Pcs | 30W×1 Pcs |
Air Velocity(m/s) | 0.45m/s±20% | ||
Clean Level | ISO 5 | ||
Supply Power | AC 1N 220V/50Hz | ||
Control System | 4.3"touch screen,3 stage regulation,light,sterilization |
Vertical Laminar Flow Clean Bench | |||
Model | GDC-SPT-01 | GDC-SPT-02 | GDC-SPT-03 |
3 ft | 4ft | 5ft | |
External size W×D×H(mm) | 1000×850×1500 | 1200×850×1500 | 1500×850×1500 |
Internal Size W×D×H(mm) | 960×600×600 | 1160×600×600 | 1460×600×600 |
HEPA Filter(mm) | 905×585×69×1 Pcs | 1105×585×69×1 Pcs | 1405×585×69×1 Pcs |
HEPA Filter Efficiency | 99.95%@0.3μm | 99.95%@0.3μm | 99.95%@0.3μm |
G4 Pre Filter(mm) | 500×375×21×1 Pcs | 500×375×21×1 Pcs | 745×375×21×1 Pcs |
Noise | 52~62dB(A) | 52~62dB(A) | 52~62dB(A) |
Fan Pressure | 260pa | 260pa | 260pa |
Fan Power (W) | 200W×1 Pcs | 200W×1 Pcs | 200W×1 Pcs |
LED Lamp Power(W) | 12W×1 Pcs | 18W×1 Pcs | 30W×1 Pcs |
Air Velocity(m/s) | 0.45m/s±20% | ||
Clean Level | ISO 5 | ||
Supply Power | AC 1N 220V/50Hz | ||
Control System | 4.3"touch screen,3 stage regulation,light,sterilization |
Features
High-Quality Construction
| |
Quiet Operation
| |
ULPA Filter
| |
Energy-efficient
| |
GDC™ Antimicrobial Powder Coating
|
Principle
Air Intake: Ambient air is drawn into the cabinet through an intake grille.
Filtration: The air passes through a HEPA filter, removing 99.97% of particles ≥0.3 microns.
Laminar Airflow: Filtered air is directed vertically downward in a smooth, uninterrupted flow.
Clean Workspace: The downward airflow creates a contamination-free zone, protecting the work area and materials.
User Safety: The design minimizes exposure to airborne contaminants, enhancing operator safety.
Maintained Pressure: The cabinet maintains a slight negative pressure to prevent external contaminants from entering.
Consistent Environment: Provides a stable and sterile environment for sensitive applications.
Accessories
Stainless Steel Orifice Tabletop
ULPA Ultra GX Filter
UV Germicidal Lamps
De-static equipment
Support Stand with Caster Wheels
FAQ
1. How to avoid turbulence in a clean bench?
To avoid turbulence in a clean bench, arrange equipment and materials in a manner that does not obstruct the airflow. Ensure that the work surface is clean and free of clutter, and minimize rapid movements within the bench to prevent disrupting the laminar flow. Regularly check and maintain the HEPA filter to ensure optimal performance.
2. How to optimize work practices in a clean bench?
Optimizing work practices in a clean bench involves organizing tools and materials efficiently, minimizing unnecessary movements, and following strict protocols.
Organization: Keep frequently used items within easy reach.
Movement: Reduce rapid hand motions to maintain airflow.
Cleanliness: Regularly clean the work surface and tools.
3. How to validate a medical clean bench?
Validating a medical clean bench involves performing a series of tests to ensure it meets performance standards. These tests typically include airflow velocity measurements, HEPA filter integrity tests, and particle count assessments. Document the results and compare them against regulatory requirements to confirm the bench's effectiveness.
4. What are the power requirements for a medical clean bench?
The power requirements for a medical clean bench generally range from 100 to 400 watts, depending on the model and additional features like lighting and ventilation systems. It's crucial to connect the bench to a stable and reliable power source to ensure consistent performance and avoid interruptions during critical procedures.
5. How to select the right filter for a clean bench?
Selecting the right filter for a clean bench involves considering the type of contaminants that need to be removed, the required level of air cleanliness, and the specific requirements of the application. HEPA filters are commonly used for their high efficiency in capturing particles as small as 0.3 microns. Consult the manufacturer's guidelines to ensure compatibility and optimal performance.
6. How to measure airflow in a horizontal flow clean bench?
To measure airflow in a horizontal flow clean bench, use an anemometer to check the velocity of the air at various points across the work surface. Position the anemometer at several locations to ensure uniform airflow distribution. Record the measurements and compare them to the manufacturer's specifications to verify proper operation.
7. How to ensure laminar flow in a clean bench?
Ensuring laminar flow in a clean bench involves maintaining a clean and unobstructed work area, regularly checking and replacing HEPA filters, and minimizing disturbances within the bench. Perform routine airflow tests to confirm that the air is moving uniformly across the work surface, and adjust as necessary.
8. How to perform routine inspections on a clean bench?
Performing routine inspections on a clean bench involves:
Visual Check: Look for any visible damage or obstructions.
Airflow Testing: Measure airflow velocity and uniformity.
Filter Inspection: Check HEPA filters for integrity and replace if necessary.
Document all findings and take corrective actions if any issues are identified to maintain optimal performance.
9. What are common contaminants in a clean bench?
Common contaminants in a clean bench include dust particles, microorganisms, chemical vapors, and human skin cells. These contaminants can originate from the environment, the materials being handled, and the operators themselves. Regular cleaning and proper use of personal protective equipment (PPE) help minimize contamination.
10. How to monitor the performance of a clean bench?
Monitoring the performance of a clean bench involves regularly checking airflow velocity, HEPA filter integrity, and particle counts. Use instruments like anemometers and particle counters to assess these parameters. Perform scheduled maintenance and keep detailed records of all tests to ensure the bench consistently meets performance standards.
11. How to perform a certification audit for a clean bench?
Performing a certification audit for a clean bench involves a thorough examination of its components and performance. Key steps include:
Airflow Testing: Measure and record airflow velocity.
HEPA Filter Integrity: Conduct leak tests on the filters.
Particle Counts: Use particle counters to ensure air cleanliness.
Document all findings and ensure compliance with relevant standards to certify the bench.
12. How to conduct a risk assessment for using a clean bench?
Conducting a risk assessment for using a clean bench involves identifying potential hazards, evaluating the likelihood and impact of each risk, and implementing control measures. Consider factors such as material handling, operator training, and environmental conditions. Develop protocols to mitigate identified risks and ensure safe operation.
13. How to ensure compliance with clean bench regulations?
Ensuring compliance with clean bench regulations involves staying updated with current standards, conducting regular audits, and maintaining thorough documentation. Implement standard operating procedures (SOPs) that align with regulatory requirements and provide training to all operators. Regularly review and update practices based on new guidelines and findings.
14. How does HEPA filtration work in a clean bench?
HEPA filtration in a clean bench works by drawing air through a HEPA filter that captures 99.97% of particles as small as 0.3 microns. The filtered air is then directed over the work surface, ensuring a clean and sterile environment by removing contaminants. This process is essential for maintaining the integrity of sensitive procedures.
15. How to balance airflow in a clean bench?
Balancing airflow in a clean bench involves adjusting the fan speed and ensuring that the HEPA filter is properly seated and not obstructed. Perform airflow velocity tests at different points across the work surface to check for uniformity. Make necessary adjustments to achieve consistent and even airflow throughout the bench.
16. How to conduct airflow mapping in a clean bench?
Conducting airflow mapping in a clean bench involves using an anemometer to measure airflow velocity at various points across the work surface. Create a grid pattern on the work surface and record the airflow readings at each grid point. Analyze the data to identify any areas with insufficient or excessive airflow and make adjustments as needed.
17. How to ensure proper grounding of a clean bench?
Ensuring proper grounding of a clean bench involves connecting it to a grounded electrical outlet and verifying the grounding with a multimeter. Regularly inspect the electrical connections and cables for any signs of wear or damage. Proper grounding is crucial to prevent static discharge, which can interfere with sensitive operations.
18. How does a clean bench differ from a laminar flow hood?
A clean bench provides a sterile, particle-free environment by directing HEPA-filtered air over the work surface, primarily protecting the product. A laminar flow hood, while similar, is designed to protect both the product and the operator by ensuring unidirectional airflow and may include additional features for handling hazardous materials.
Factory Production Workshop Video
Factory Photo
Product Packaging And International Logistics
Product International Certification
Find Other Common Equipment Recommendations
-
Modular CleanRoom
US$9000-10000 USD/Unit
Min. Order:1 Set -
Air Shower
US$1000.00-5000.00 USD/Unit
Min. Order:1 Set -
Downflow Booth
US$3000-6000 USD/Unit
Min. Order:1 Set -
Clean bench
US$600-2000 USD/Unit
Min. Order:1 Set -
Air Filter
US$3-50 USD/Unit
Min. Order:1 Set -
Cleanroom Wall Panels
US$10-20 USD/sq.
Min. Order:1 Set -
Pass Box
US$200-500 USD/Unit
Min. Order:1 Set -
FFU
US$135-350 USD/Unit
Min. Order:1 Set -
Fume Hood
US$700-1500 USD/Unit
Min. Order:1 Set -
Cleanroom HVAC
US$5000-20000 USD/Unit
Min. Order:1 Set -
Clean room floor
US$5-20 USD/Sq.
Min. Order:1 Set -
Clean room ceiling
US$
Min. Order:1 Set