clean room modular wall systems
Essential solutions for maintaining stringent environmental control in critical industries
Clean room modular wall systems are essential in maintaining stringent environmental control in industries such as pharmaceuticals, biotechnology, and Electronics. These systems facilitate the creation of controlled environments that minimize contamination and ensure compliance with industry standards. At Deiiang Company, we specialize in providing innovative modular wall solutions tailored to meet specific Clean Room requirements. Our designs enhance operational efficiency and adaptability, making them an ideal choice for evolving industry needs.
Clean Room Modular Wall Systems
Clean room modular wall systems offer flexible and efficient solutions for creating clean environments. These systems are designed for easy assembly and disassembly, allowing for quick modifications and expansions.
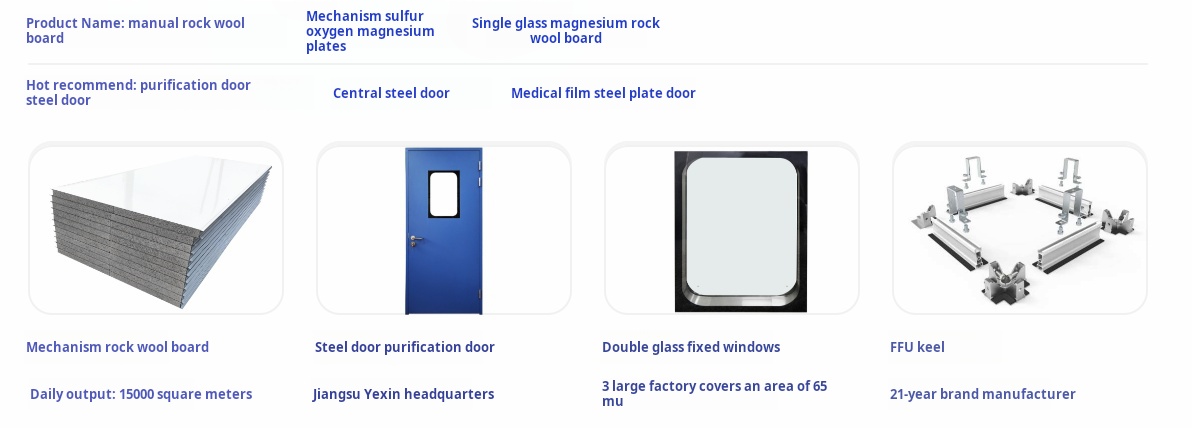
modular clean room Doors
Single Door
Designed for easy access while maintaining clean room integrity. Constructed from non-porous, easy-to-clean materials to ensure minimal contamination risk.
Double Door
Ideal for high-traffic areas, allowing transportation of larger equipment. Features robust design to minimize air leakage, with customizable options like hermetic seals and interlocks.
Sliding Door
Efficient option for clean rooms with limited space. Allows smooth, unobstructed access while minimizing air exchange to maintain cleanliness.
Rolling Door
Provides a space-saving solution, offering quick access to larger areas. Durable construction ensures long-lasting performance in high-usage environments.
Modular Clean room wall Panels
Essential components in creating controlled environments, providing flexibility, ease of installation, and compliance with cleanliness standards.
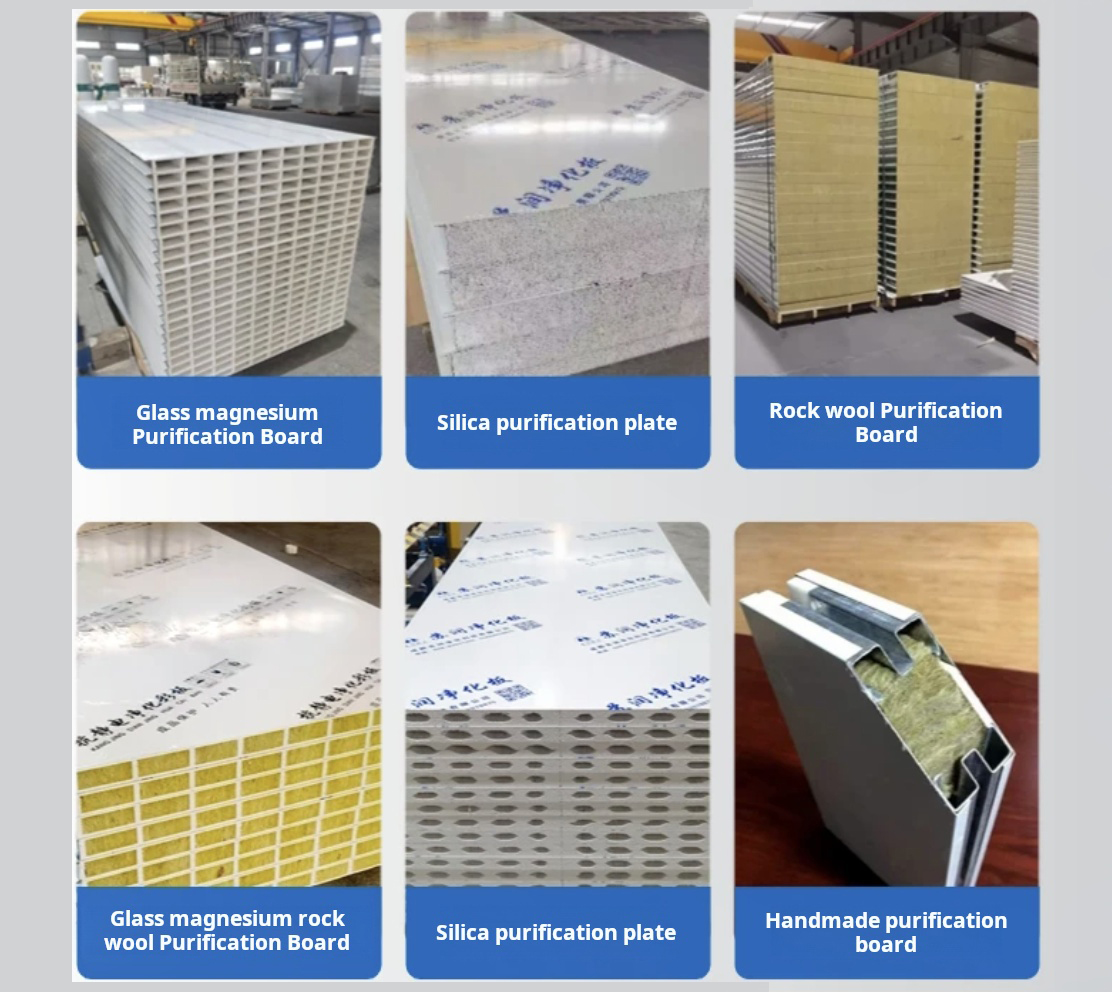
Key Features
- Made from high-quality, durable, and easy-to-clean materials
- Customizable to meet specific facility requirements
- Options for insulation, soundproofing, and electrical system integration
- Meets international standards such as ISO 14644
Installation and Maintenance
The installation process is straightforward, requiring minimal downtime. Their modular nature allows easy replacement or upgrade, simplifying maintenance and renovations, contributing to long-term efficiency.
Clean room ceiling Modules
Play a vital role in maintaining the integrity of controlled environments, designed to complement modular wall systems for seamless integration.
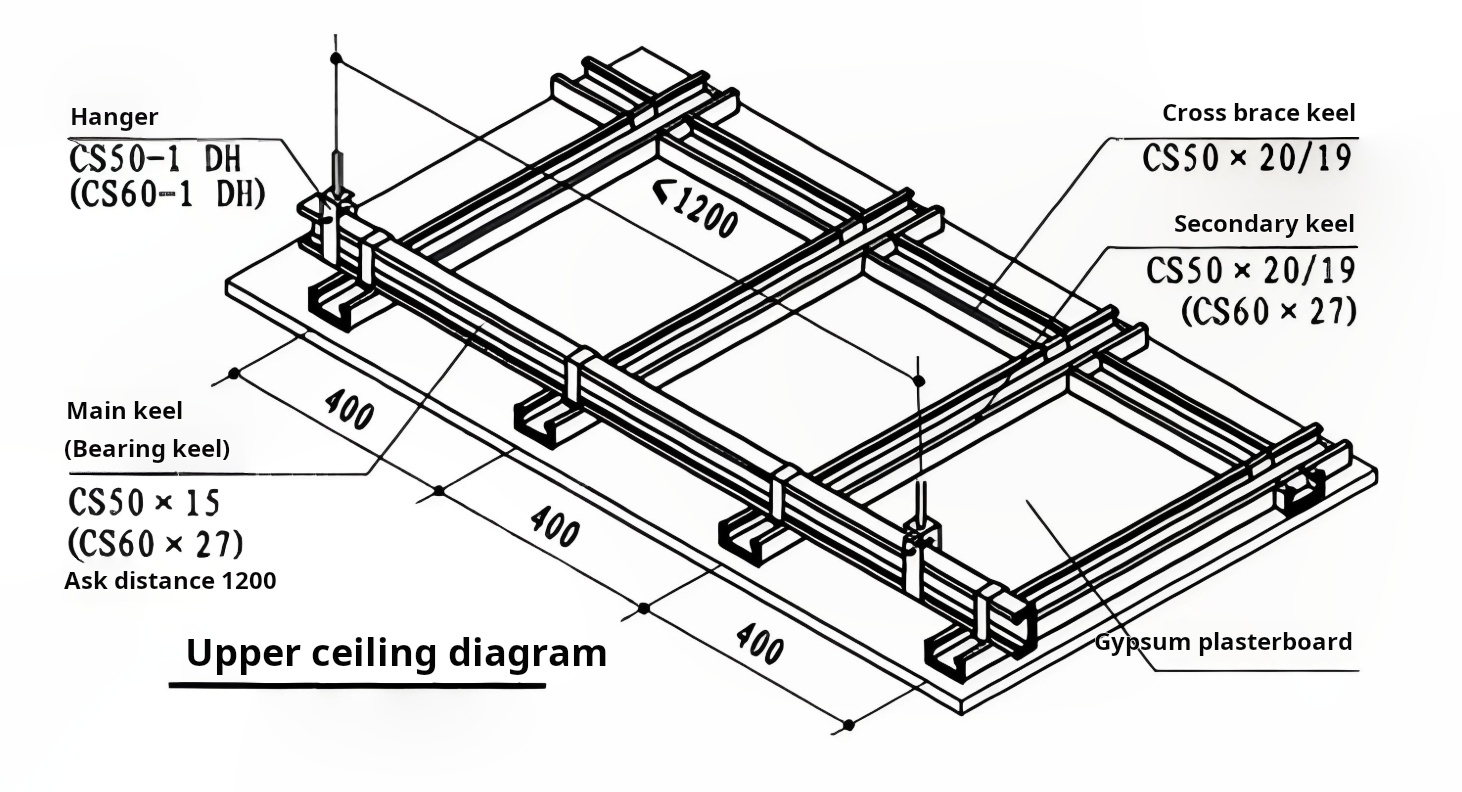
Constructed with non-porous materials that resist contamination, easy to clean and maintain. Available in various configurations to incorporate air handling units, lighting, and other essential equipment while maintaining optimal airflow and cleanliness.Complies with industry standards such as ISO 14644 and GMP regulations, ensuring safety and performance criteria are met.
Modular Clean Room Accessories
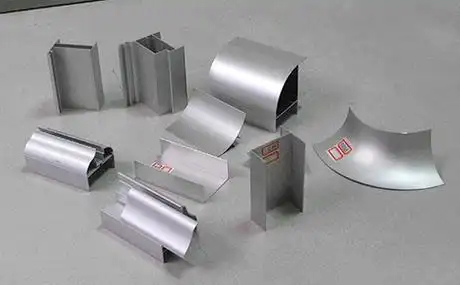
Wall Panels
Acrylic Panels
Used for optical clarity, allowing visibility while maintaining a clean, smooth surface. Lightweight, chemical-resistant, and impact-resistant.
PVC Soft Curtains
Flexible partitioning solution, made from soft, transparent PVC. Easy to clean, cost-effective, and quick to install for entrances or temporary partitions.
Doors and Windows
Cleanroom Doors
Designed to prevent contamination, made from stainless steel, aluminum, or composite materials. Equipped with interlocking systems to maintain air pressure.
Windows
Made of tempered glass or acrylic in stainless steel frames, allowing visibility without compromising cleanliness. Ideal for observation and inspection.
Purification Aluminum Profiles
Specialized frames for modular Cleanroom designs, supporting installation of HEPA/ULPA filters, ceiling panels, etc. Made from lightweight, corrosion-resistant aluminum.
FFU (Fan Filter Units)
Critical for maintaining airflow and particulate control, combining a fan and HEPA/ULPA filter. Mounted in ceilings to provide continuous air filtration and maintain cleanliness levels.
Summary of Modular Cleanroom Accessories
Accessory Type | Description |
---|---|
Wall Panels | Acrylic panels for visibility and PVC soft curtains for flexibility |
Doors and Windows | Stainless steel/acrylic doors and observation windows for contamination control |
Purification Aluminum Profiles | Structural supports for air filtration and ceiling systems |
FFU (Fan Filter Units) | Integrated air filtration and airflow systems for cleanliness maintenance |
Conclusion
Modular Cleanroom wall systems provide an efficient, flexible, and cost-effective solution for maintaining controlled environments. Their easy installation, customizability, and adaptability make them an ideal choice for industries that require strict contamination control while maintaining the ability to expand or modify the space as needed. These systems are particularly useful in industries like pharmaceuticals, biotechnology, and electronics, where environmental conditions are critical for product quality and safety.