Modular Cleanroom Solutions
Creating Controlled Environments for Critical Applications
What is a Modular Cleanroom?
A modular cleanroom is a flexible, prefabricated system designed to create a controlled environment with stringent requirements for cleanliness, air quality, and temperature. Unlike traditional cleanrooms that are built on-site, modular cleanrooms are made up of standardized, prefabricated components that can be quickly assembled, reconfigured, or expanded as needed.
Modular CleanRoom Classifications
Modular cleanroom grade standards are based on the level of airborne particle contamination, classified by ISO Standards (ISO 14644-1). The most common classes are:
iso class | Cleanliness Level | Applications |
---|---|---|
ISO Class 1 | Highest cleanliness, with less than 10 particles per cubic meter (0.1 microns) | Ultra-high precision manufacturing |
ISO Class 5 | Suitable for pharmaceutical and biotech, with up to 3,520 particles per cubic meter (0.5 microns) | Drug manufacturing, biotechnology |
iso class 7 | For less sensitive environments, with up to 352,000 particles per cubic meter (0.5 microns) | General Electronics assembly |
ISO Class 8 | For general industrial use, with up to 3.5 million particles per cubic meter (0.5 microns) | General industrial manufacturing |
Key Features of Modular Cleanrooms
Quick Installation & Flexibility
Components can be rapidly assembled, reconfigured, or dismantled to meet changing needs.
Scalability
Easily expandable to accommodate increasing production requirements or changes in process.
Efficient Maintenance
Individual modules and components can be replaced or serviced without disrupting the entire cleanroom.
Cost-Effectiveness
Modular design is often more affordable compared to traditional cleanrooms, offering greater resource efficiency.
Modular Cleanroom Working Principle
A modular cleanroom operates on the principle of maintaining a controlled environment where airborne particles, temperature, humidity, and other contaminants are carefully regulated. It uses a combination of filtration systems, such as HEPA or ULPA filters, to remove particles from the air, and an HVAC system to maintain constant airflow and pressure.
The modular cleanroom is designed for flexibility, with pre-fabricated panels that can be easily assembled and reconfigured. The system maintains the desired level of cleanliness by continuously circulating air through the filters and keeping surfaces sanitized.
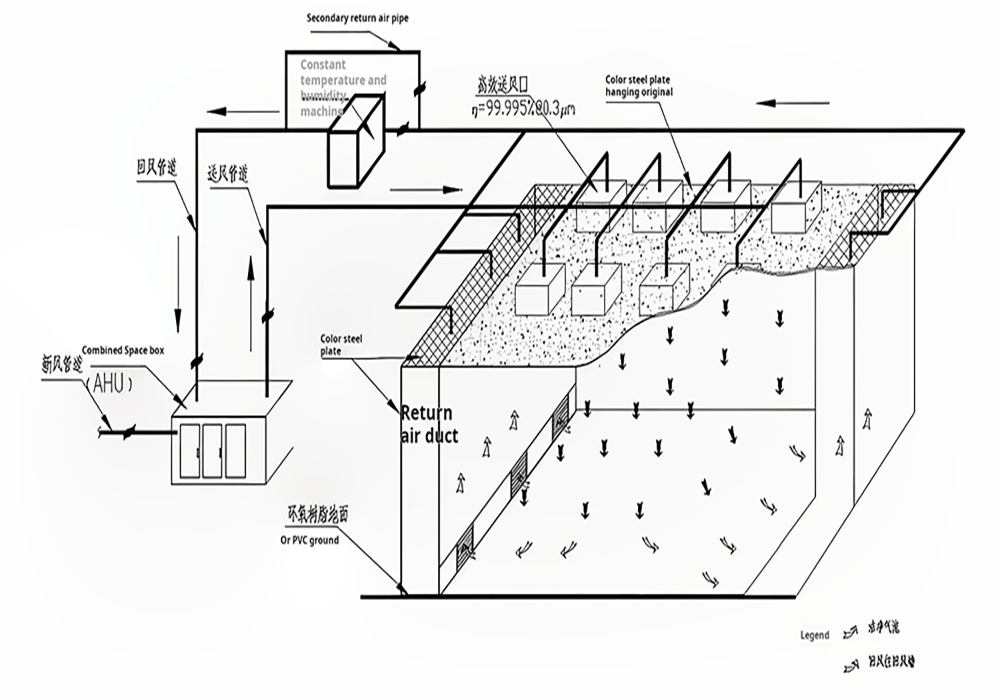
Key Components of Modular Cleanrooms
Wall Systems
- Wall Panels: Made from materials like stainless steel or aluminum, smooth, non-porous, and easy to assemble.
- Doors: Airtight doors with self-closing mechanisms, made from the same materials as wall panels, may include airlocks.
- Windows: Clear, easy-to-clean windows made of acrylic or tempered glass for monitoring.
- Ceiling: Supports HVAC and air filtration, made from cleanable materials for uniform cleanliness.
Airflow Systems
- HVAC System: Regulates air quality, temperature (20-25°C), humidity, and creates positive pressure to prevent contaminants.
- FFU (Fan Filter Unit): Contains a fan and HEPA/ULPA filter, mounted in the ceiling to supply laminar flow of filtered air.
- Filtration: Uses HEPA or ULPA filters to remove airborne particles and maintain cleanliness standards.
- Air Circulation: Continuous air circulation ensures uniform cleanliness and contaminant removal.
Modular cleanroom costs
The costs of a modular cleanroom depend on factors like size, design, and cleanliness requirements:
- Basic modular cleanrooms (ISO Class 7 or 8): $100 to $300 per square foot
- Advanced systems (ISO Class 5 or 6): $400 to $800 per square foot
- Additional costs: installation, specialized equipment, ongoing maintenance
- Modular cleanrooms are generally more affordable than traditional built-in cleanrooms
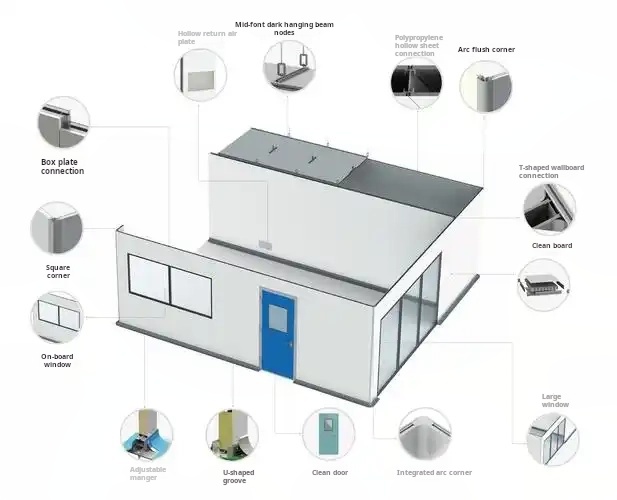
Why Choose Modular Cleanrooms?
Modular cleanrooms are ideal for industries such as pharmaceuticals, biotech, electronics, and manufacturing, where maintaining a sterile and contaminant-free environment is critical. The modular design allows for easy customization to meet specific cleanliness standards, and components can be adjusted or replaced with minimal downtime, making it a cost-effective and scalable solution.