Stainless steels FFU,Fan Filter Unit,22.6' x 46.3',Air volume:1000m³/h
Reference Price:US$from $75


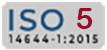
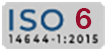
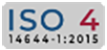
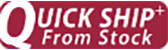
Cleanroom
Stainless steels FFU,Fan Filter Unit,22.6' x 46.3',Air volume:1000m³/h
Choose your installation & validation options below
Quantity:
Choose your Cleanroom frame structure material
Quantity:
Choose your Cleanroom Wall enclosure materials
Quantity:
Choose your Temperature requirements
Quantity:
Choose your humidity requirements
Quantity:
Choose your Explosion-proof requirements
Quantity:
Summary
Stainless steels FFU,Fan Filter Unit,22.6' x 46.3',Air volume:1000m³/h
Validation
Installation & Validation
Find Similar Products
Features
The Stainless Steel FFU (Fan Filter Unit) is designed for efficient air filtration in cleanroom environments. With dimensions of 22.6' x 46.3', it features a robust stainless steel construction that ensures durability and easy maintenance.
This unit provides an air volume of 1000 m³/h, making it suitable for various applications requiring controlled air quality and particulate removal. Ideal for laboratories, pharmaceuticals, and semiconductor manufacturing, the FFU contributes to maintaining a sterile and contaminant-free atmosphere.
Cleanroom FFU Product Details:
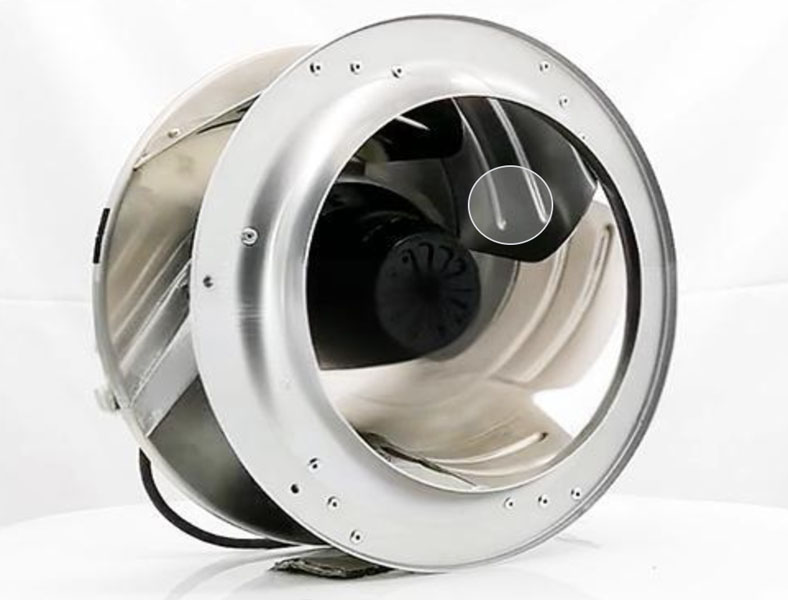
01Advanced fan technology
Low noise operation
Energy saving motor
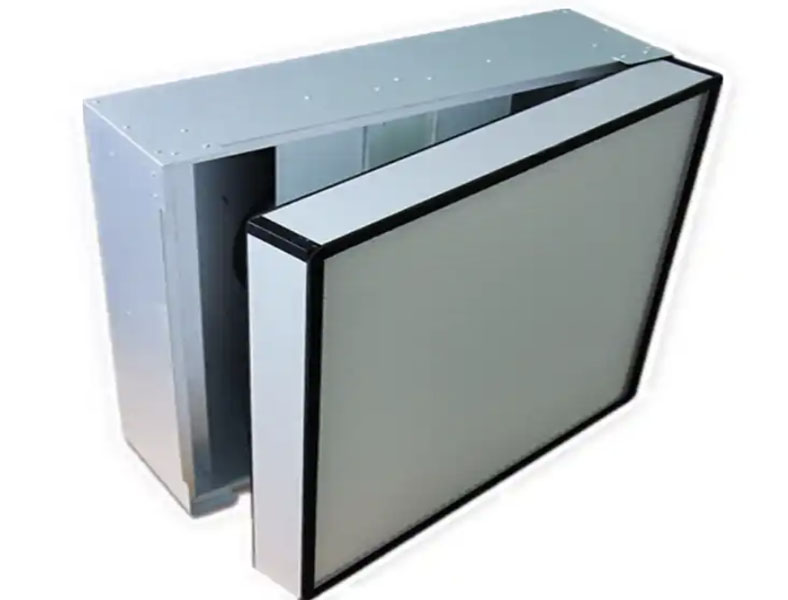
02Air filter
High efficiency HEPA/ULPA filter
Stable airflow distribution
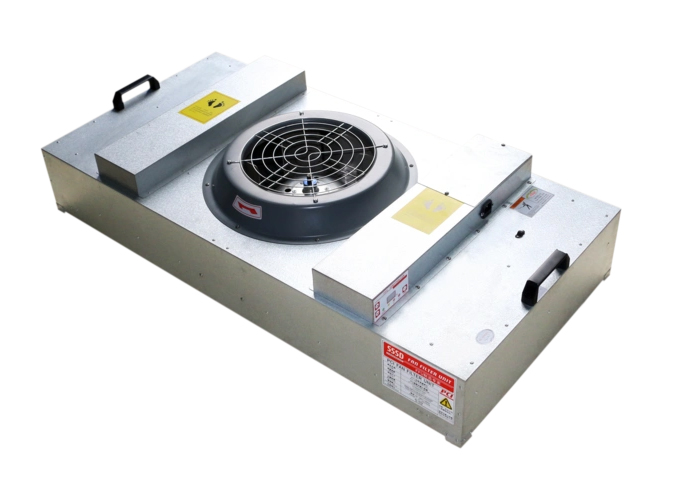
03Installation and Maintenance
Easy to install and maintain
Compact design for flexible integration
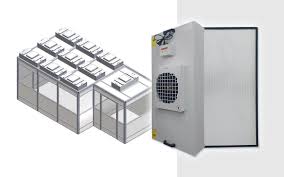
04Compliance with international standards
Compliant with ISO cleanroom standards
Advanced fan technology for improved air circulation
Work Principle
Structural components: fan, filter, housing
Air flow: The fan draws in ambient air, which passes through the filter.
Filtration process: the filter removes particles (e.g. dust, microorganisms) from the air.
Clean air release: Filtered clean air is released from the top or bottom.
Models
Product Name | AC FFU | |||
Product Model | DC-FFU-A01 | DC-FFU-A02 | DC-FFU-A03 | DC-FFU-A04 |
Dimension(mm) | 575x575x220 | 575x1175x220 | 875x1175x275 | 1175x1175x295 |
Filter Dimension(mm) | 570x570x69 | 570x1170x69 | 870x1170x69 | 1170x1170x69 |
Air Volume | 500m³/h | 1000m³/h | 1500m³/h | 2000m³/h |
Noise | 52~62dB(A) | 52~62dB(A) | 52~62dB(A) | 52~62dB(A) |
Air Pressure | 200PA | 200PA | 260PA | 290PA |
Power | 170W | 170W | 200W | 240W |
Weight | 28Kg | 35Kg | 47Kg | 55Kg |
Material | Galvanized/powder coated/SUS 304 plate | |||
Supply Power | AC 1N 110, 220V/50,60Hz | |||
Control System | 3 stage regulation, group reguation | |||
Filter Efficiency | 99.95%MPPS above H13-U16@EN1822 | |||
Pre Filter | G3/G4 Filter, nylon filter | |||
Work Status | power Indicator, work indicator, Error indicator | |||
Connection Type | 3 Pin Aviation Male Female socket, terminat blocks | |||
Overload Protection | Overload protect of motor and controller | |||
Monitor Contact Communication Method | port of reserve and Erro |
Product Name | AC FFU | |||
Product Model | DC-FFU-A01 | DC-FFU-A02 | DC-FFU-A03 | DC-FFU-A04 |
Dimension(mm) | 575x575x220 | 575x1175x220 | 875x1175x275 | 1175x1175x295 |
Filter Dimension(mm) | 570x570x69 | 570x1170x69 | 870x1170x69 | 1170x1170x69 |
Air Volume | 500m³/h | 1000m³/h | 1500m³/h | 2000m³/h |
Noise | 52~62dB(A) | 52~62dB(A) | 52~62dB(A) | 52~62dB(A) |
Air Pressure | 200PA | 200PA | 260PA | 290PA |
Power | 170W | 170W | 200W | 240W |
Weight | 28Kg | 35Kg | 47Kg | 55Kg |
Material | Galvanized/powder coated/SUS 304 plate | |||
Supply Power | AC 1N 110, 220V/50,60Hz | |||
Control System | 3 stage regulation, group reguation | |||
Filter Efficiency | 99.95%MPPS above H13-U16@EN1822 | |||
Pre Filter | G3/G4 Filter, nylon filter | |||
Work Status | power Indicator, work indicator, Error indicator | |||
Connection Type | 3 Pin Aviation Male Female socket, terminat blocks | |||
Overload Protection | Overload protect of motor and controller | |||
Monitor Contact Communication Method | port of reserve and Erro |
Accessories
HEPA Filter
ULPA Filter
Adjustable speed fan
Fixed speed fan
Manual control panel
Digital remote control system
Monitoring sensors (pressure)
FAQ
1. How does airflow rate impact FFU performance?
The airflow rate is crucial for the performance of a Fan Filter Unit (FFU) as it determines the efficiency of air filtration and the maintenance of cleanroom conditions. A higher airflow rate can enhance the removal of airborne contaminants, ensuring a cleaner environment. However, if the rate is too high, it may lead to increased energy consumption and noise levels.
2. How long do FFU filters last?
The lifespan of FFU filters can vary based on several factors, including the type of filter, the environment in which it operates, and the volume of air processed. Typically, most FFU filters last between 6 months to 2 years. To maximize their effectiveness, regular monitoring and maintenance are recommended.
3. What are the typical filter grades used in FFUs?
FFUs commonly utilize several filter grades to ensure high air quality. These include:
HEPA (High-Efficiency Particulate Air) - captures 99.97% of particles down to 0.3 microns.
ULPA (Ultra-Low Penetration Air) - captures 99.999% of particles down to 0.1 microns.
Pre-filters - used to extend the life of HEPA/ULPA filters by capturing larger particles.
The selection of filter grade depends on the specific cleanliness requirements of the application.
4. How does a Fan Filter Unit work?
A Fan Filter Unit operates by drawing in ambient air through its filters. The fan creates a negative pressure that pulls air through the pre-filter and primary filter, effectively removing airborne particles and contaminants. The clean air is then recirculated back into the environment, maintaining the desired cleanliness levels.
5. Can FFUs be used in cleanroom ceiling applications?
Yes, FFUs are often used in cleanroom ceiling applications. They can be integrated into the ceiling structure to provide a uniform airflow and filtration throughout the cleanroom. This setup helps maintain consistent air quality and minimizes the risk of contamination.
6. How does a fan's RPM affect FFU performance?
The RPM (Revolutions Per Minute) of a fan in an FFU directly influences its airflow rate and efficiency. Higher RPM generally increases the airflow, leading to better contaminant removal. However, excessive RPM can also result in higher energy consumption and noise levels, which must be balanced for optimal performance.
7. What are the most common applications for SUS 304 Fan Filter Units?
SUS 304 Fan Filter Units are widely used in various applications, including:
Pharmaceutical manufacturing
Semiconductor production
Biotechnology labs
Food processing
These applications benefit from the corrosion resistance and durability of SUS 304 stainless steel, ensuring longevity and reliability in clean environments.
8. Are Stainless Steel FFUs energy-efficient?
Stainless Steel FFUs can be energy-efficient, especially when designed with modern, low-power motors and variable speed drives. These features allow for better control of airflow rates, reducing energy consumption while maintaining performance. Additionally, using high-efficiency filters can prolong filter life and further enhance energy efficiency.
9. What is the airflow pattern created by an FFU?
The airflow pattern created by an FFU is typically laminar, meaning that air flows in parallel layers with minimal turbulence. This design ensures that clean air is uniformly distributed across the cleanroom, which helps to minimize the risk of contamination and maintain a stable environment for sensitive processes.
10. What are the common failure modes of FFUs?
Common failure modes of FFUs include:
Fan motor failure - can lead to reduced airflow or complete system failure.
Filter clogging - can decrease efficiency and airflow.
Electrical issues - such as wiring failures or power supply problems.
Regular maintenance and monitoring can help mitigate these issues and extend the lifespan of FFUs.
11. What are the noise reduction options for FFUs?
Noise reduction options for FFUs include the use of sound-dampening materials, variable speed fans that operate at lower RPMs, and vibration isolation mounts. These features help minimize operational noise, making FFUs suitable for environments where noise levels must be kept to a minimum.
12. How often should FFU filters be replaced?
FFU filters should typically be replaced every 6 to 12 months, depending on the operating conditions and the level of contamination in the environment. Regular monitoring of pressure differentials across the filters can help determine when replacement is necessary. Signs of clogging or reduced airflow are indicators that filters may need to be changed sooner.
13. What are the energy-saving technologies available for FFUs?
Energy-saving technologies for FFUs include:
EC (Electronically Commutated) motors - offer higher efficiency and lower energy consumption.
Variable speed drives - allow for adjusting airflow based on real-time requirements.
Smart control systems - optimize operation based on environmental data.
Implementing these technologies can significantly reduce operational costs while maintaining effective air filtration.
14. What are the installation challenges for FFUs?
Installation challenges for FFUs may include ensuring proper alignment with the ceiling grid, managing weight distribution, and maintaining adequate electrical connections. Additionally, achieving a tight seal to prevent air leaks is essential for optimal performance. Careful planning and coordination with other systems in the cleanroom are necessary to address these challenges effectively.
15. Can FFUs be customized for specific needs?
Yes, FFUs can be customized to meet specific requirements. Customization options may include varying dimensions, airflow rates, filter types, and materials based on the application. Manufacturers often work closely with clients to design FFUs that fit unique cleanroom specifications and operational needs.
16. What type of motors are used in FFUs?
FFUs typically use either AC or EC (Electronically Commutated) motors. AC motors are common for standard applications, providing reliable performance. In contrast, EC motors are preferred for energy efficiency and variable speed capabilities, allowing for better airflow control and reduced operational costs.
Factory Production Workshop Video
Factory Photo
Product Packaging And International Logistics
Product International Certification
Find Other Common Equipment Recommendations
-
Modular CleanRoom
US$9000-10000 USD/Unit
Min. Order:1 Set -
Air Shower
US$1000.00-5000.00 USD/Unit
Min. Order:1 Set -
Downflow Booth
US$3000-6000 USD/Unit
Min. Order:1 Set -
Clean bench
US$600-2000 USD/Unit
Min. Order:1 Set -
Air Filter
US$3-50 USD/Unit
Min. Order:1 Set -
Cleanroom Wall Panels
US$10-20 USD/sq.
Min. Order:1 Set -
Pass Box
US$200-500 USD/Unit
Min. Order:1 Set -
FFU
US$135-350 USD/Unit
Min. Order:1 Set -
Fume Hood
US$700-1500 USD/Unit
Min. Order:1 Set -
Cleanroom HVAC
US$5000-20000 USD/Unit
Min. Order:1 Set -
Clean room floor
US$5-20 USD/Sq.
Min. Order:1 Set -
Clean room ceiling
US$
Min. Order:1 Set