6 x 6 ISO 6 Softwall Cleanroom
Reference Price:US$9000.00-10500.00
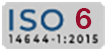


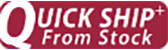

Cleanroom
6 x 6 ISO 6 Softwall Cleanroom
Choose your installation & validation options below
Quantity:
Choose your Cleanroom frame structure material
Quantity:
Choose your Cleanroom Wall enclosure materials
Quantity:
Choose your Temperature requirements
Quantity:
Choose your humidity requirements
Quantity:
Choose your Explosion-proof requirements
Quantity:
Summary
6 x 6 ISO 6 Softwall Cleanroom
Validation
Installation & Validation
Find Similar Products
-
5 x 6 ISO 6 Softwall Cleanroom
US$4000-15000 USD/Set
Min. Order:1 Set -
5 x 5m ISO 6 Softwall Cleanroom
US$4000-15000 USD/Set
Min. Order:1 Set -
4 x 6m ISO 6 Softwall Cleanroom
US$4000-15000 USD/Set
Min. Order:1 Set -
4 x 5m ISO 6 Softwall Cleanroom
US$4000-15000 USD/Set
Min. Order:1 Set -
4 x 4m ISO 6 Softwall Cleanroom
US$4000-15000 USD/Set
Min. Order:1 Set -
3 x 6m ISO 6 Softwall Cleanroom
US$4000-15000 USD/Set
Min. Order:1 Set
Cleanrooms Detail
Air changes
The number of air changes is a very important parameter in a clean room, which determines the frequency of air renewal in the clean room. The specific value depends on the cleanliness level of the clean room, for example, 7 class clean room air change times should not be less than 20 times, while the 6 class requires a higher number of air changes, at least 30 times. The number of air changes directly affects the cleanliness inside the clean room, so it is an important indicator for evaluating the performance of the clean room.
Differential pressure
Differential pressure refers to the pressure difference between the clean room and its neighboring areas, this parameter ensures that the gas inside the clean room will not flow to the outside world, thus avoiding the intrusion of pollutants. In general, the pressure difference between the main workshop and the neighboring rooms should be maintained above 5Pa.
Average wind speed
Average wind speed is an important parameter to measure the speed of air flow inside the clean room. In class 10 and class 100 clean room, the average wind speed is usually controlled between 3-0.5m/s. The proper wind speed is not only effective, it is also important for the air flow. Proper air velocity not only effectively conveys and distributes air, but also reduces the accumulation of dust particles and maintains the cleanliness inside the clean room.
Cleanliness level table
Cleanrooms Airflow
Working Principle
The working principle of the clean room is based on air filtration and flow control. The fan is located at the top of the clean room and is responsible for drawing air in and passing it through a primary filter for initial filtration to remove larger particles. Subsequently, the air is further purified by a high-efficiency filter, which removes even finer particles, and finally it is delivered uniformly at a certain air speed, forming a homogenous layer that ensures a vertical unidirectional flow of clean air, thus maintaining the cleanliness of the work area.
Structural Characteristics
The clean room is usually designed as an assembled structure with a solid and beautiful frame that does not rust or produce dust. Antistatic curtains or toughened glass are usually used on the periphery to achieve good anti-static effect and high transparency. The internal purification level can range from class 100 to class 10,000, which is suitable for areas that require localized high cleanliness, such as assembly line operation areas or high-precision product assembly areas.
Cleanrooms Installation
Installation Steps
Assemble the frame
According to the design drawings, determine the installation location and size requirements, use aluminum alloy profiles and other materials to assemble the frame and support structure of the clean room to ensure stability and reliability.
Installation of high efficiency filter and FFU fan
First, install the high-efficiency filter, and then install the FFU fan in the specified position and connect it to the power supply; the FFU fan is the key component for maintaining air circulation in the clean room.
Installation of walls and ceilings
Special materials such as stainless steel are used to ensure the cleanliness of the interior of the clean room and to provide good maintenance performance.
Installation of doors and windows
According to the design requirements, use appropriate materials such as PVC curtains or automatic doors to ensure good sealing performance.
Installation of lighting and ventilation equipment
According to the requirements of the clean room, select the appropriate lighting and ventilation equipment and install and debug to ensure the uniformity of lighting and ventilation effectiveness.
System debugging and testing
After the installation is completed, carry out comprehensive debugging of the clean room, including checking the operation of the FFU fan, the working condition of the filter, and whether there is any air leakage and other problems inside the clean room.
Precautions
Avoid installing the clean room in dusty, humid or salty places.
During installation, clean dust from the surface of all components, especially the frame and FFU fan.
Installers should wear dust-free clothing and take appropriate protective measures as required.
Cleanrooms Testing
Dust Particle Count Test
Dust particle count is a key indicator for evaluating the performance of a clean room. According to ISO 14644-1, the number of suspended particles inside the clean room should be controlled within a specific range. The maximum permissible number is 3500 particles/m³ for static conditions and 7500 particles/m³ for dynamic conditions. For testing, a laser dust particle counter is usually used to count and analyze the dust particles by collecting air samples.
Air Velocity Measurement
Wind speed test is used to measure the air mobility in the clean room to ensure the normal operation and reasonable configuration of air purification equipment. The air velocity in the clean room is generally maintained between 0.2-0.5m/s. The air velocity in the clean room can be measured using an anemometer. When testing, you can use an anemometer to measure the air velocity at the air outlet or air duct.
The number of air changes detection
The number of air changes reflects the frequency of air renewal in the clean room, directly related to the cleanliness and purification equipment load. In general, the number of air changes should be controlled at 3-5 times per hour.
Temperature and humidity detection
Temperature and humidity on the clean room environment has a significant impact on the appropriate temperature and humidity not only to ensure comfort, but also to ensure the stability of product quality. Generally speaking, the temperature in the clean room should be controlled between 22-25°C, and the humidity should be controlled between 50-70%.
Pressure testing
Pressure testing is used to measure the sealing performance of the cleanroom to ensure that no contamination can penetrate from the outside while preventing the clean air inside from leaking out. The pressure inside the clean room should be slightly higher than the outdoor pressure by 5-10 Pa.
FAQ
Factory Production Workshop Video
Factory Photo
Product Packaging And International Logistics
Product International Certification
Find Other Common Equipment Recommendations
-
Modular CleanRoom
US$9000-10000 USD/Unit
Min. Order:1 Set -
Air Shower
US$1000.00-5000.00 USD/Unit
Min. Order:1 Set -
Downflow Booth
US$3000-6000 USD/Unit
Min. Order:1 Set -
Clean bench
US$600-2000 USD/Unit
Min. Order:1 Set -
Air Filter
US$3-50 USD/Unit
Min. Order:1 Set -
Cleanroom Wall Panels
US$10-20 USD/sq.
Min. Order:1 Set -
Pass Box
US$200-500 USD/Unit
Min. Order:1 Set -
FFU
US$135-350 USD/Unit
Min. Order:1 Set -
Fume Hood
US$700-1500 USD/Unit
Min. Order:1 Set -
Cleanroom HVAC
US$5000-20000 USD/Unit
Min. Order:1 Set -
Clean room floor
US$5-20 USD/Sq.
Min. Order:1 Set -
Clean room ceiling
US$
Min. Order:1 Set