3 x 5m ISO 6 Softwall cleanroom
Reference Price:US$4200.00-5500.00
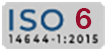
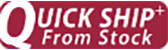


Cleanroom
3 x 5m ISO 6 Softwall cleanroom
Choose your installation & validation options below
Quantity:
Choose your Cleanroom frame structure material
Quantity:
Choose your Cleanroom Wall enclosure materials
Quantity:
Choose your Temperature requirements
Quantity:
Choose your humidity requirements
Quantity:
Choose your Explosion-proof requirements
Quantity:
Summary
3 x 5m ISO 6 Softwall cleanroom
Validation
Installation & Validation
Find Similar Products
-
5 x 6 ISO 6 Softwall Cleanroom
US$4000-15000 USD/Set
Min. Order:1 Set -
5 x 5m ISO 6 Softwall Cleanroom
US$4000-15000 USD/Set
Min. Order:1 Set -
4 x 6m ISO 6 Softwall Cleanroom
US$4000-15000 USD/Set
Min. Order:1 Set -
4 x 5m ISO 6 Softwall Cleanroom
US$4000-15000 USD/Set
Min. Order:1 Set -
4 x 4m ISO 6 Softwall Cleanroom
US$4000-15000 USD/Set
Min. Order:1 Set -
3 x 6m ISO 6 Softwall Cleanroom
US$4000-15000 USD/Set
Min. Order:1 Set
Cleanrooms Detail
ISO 6 softwall cleanrooms maintain a controlled environment with a maximum of 3,520 particles per cubic meter. They feature flexible wall systems and advanced HVAC controls, making them ideal for industries like pharmaceuticals, biotechnology, and electronics.
Maximum permissible particle number: 3,520 particles ≥ 0.5 micron per cubic meter
Temperature range: typically 20°C to 24°C
Humidity range: normally 30% to 60
Air exchange rate: 10 to 15 times per hour
ISO 6 softwall cleanrooms offer several key features that enhance their functionality and adaptability for various applications. These cleanrooms are designed for moderate cleanliness, providing a controlled environment that minimizes contamination risks in sensitive processes
Cleanrooms Airflow
In ISO 6 softwall cleanrooms, the airflow principle is crucial for maintaining cleanliness and controlling contamination. The following key elements describe this principle:
Unidirectional Flow: Clean air is supplied in a single direction from the ceiling to the floor, minimizing turbulence and particulate disturbance.
HEPA Filtration: High-Efficiency Particulate Air (HEPA) filters remove contaminants from the air before it enters the cleanroom, ensuring a high level of air purity.
Positive Pressure: The cleanroom is maintained at a higher pressure compared to adjacent areas, preventing outside contaminants from infiltrating the space.
Air Changes Per Hour (ACH): A specified number of air changes per hour is maintained to dilute and remove airborne particles, keeping the environment compliant with ISO 6 standards.
Return Air Systems: Air is usually returned through vents located at the bottom, facilitating proper circulation and ensuring uniform airflow throughout the cleanroom.
Cleanrooms Installation
ISO 6 Softwall Cleanrooms Installation Steps
Site Preparation: Evaluate the installation area for dimensions and utility access. Ensure the space meets cleanroom requirements.
Framework Assembly: Assemble the cleanroom framework, including support structures and flexible wall panels designed for easy maintenance.
Component Installation: Install essential components such as HEPA filters, lighting, and airflow systems to ensure compliance with ISO 6 standards.
Testing and Verification: Conduct rigorous testing of airflow, particle counts, and overall performance to confirm the cleanroom meets ISO 6 cleanliness requirements.
Staff Training: Train personnel on operating procedures and maintenance protocols to ensure effective cleanroom operation.
Cleanrooms Testing
ISO 6 softwall cleanroom testing is essential to ensure that the environment meets the required cleanliness standards and operates effectively. Below are the key aspects of testing and features associated with ISO 6 softwall cleanrooms.
Key Features of ISO 6 Softwall Cleanroom Testing:
Particle Counting:
Regular monitoring of airborne particles to ensure compliance with ISO 6 limits (maximum 3,520 particles per cubic meter for ≥0.5 micrometers).
Airflow and Air Changes:
Assessment of airflow rates and air changes per hour to maintain optimal conditions and prevent contamination.
Temperature and Humidity Control:
Continuous monitoring of temperature and humidity levels to ensure they remain within specified ranges (typically 20°C to 24°C and 30% to 60% humidity).
Pressure Differential Testing:
Verification of pressure differentials between the cleanroom and adjacent areas to prevent contamination ingress.
These testing features are crucial for maintaining the integrity and operational efficiency of ISO 6 softwall cleanrooms, ensuring they provide a suitable environment for sensitive processes.
FAQ
What is the difference between cleanroom and controlled environment?
A cleanroom is designed specifically to minimize airborne particles and contaminants, while a controlled environment regulates factors like temperature and humidity. Both play crucial roles in maintaining quality in sensitive processes.
What is the typical size of a modular cleanroom?
Modular cleanrooms come in various sizes, often tailored to specific needs. They can range from small setups for research to larger configurations for manufacturing, allowing flexibility in design and usage.
What are the benefits of a modular cleanroom?
Modular cleanrooms provide several advantages, including quick installation, customization, and cost efficiency. They are easily adaptable to changing requirements, making them suitable for diverse industries and applications.
What is the role of cleanroom barriers?
Cleanroom barriers are essential for maintaining cleanliness by preventing contamination from outside sources. They also create physical separation between clean and non-clean areas, which is vital for protecting sensitive processes.
What industries use modular cleanrooms?
Modular cleanrooms are widely used in industries such as pharmaceuticals, biotechnology, electronics, and aerospace. Their adaptability and efficiency make them ideal for environments that require strict contamination control.
How does a modular cleanroom reduce contamination?
A modular cleanroom reduces contamination through controlled airflow, filtration systems, and strict hygiene protocols. These features ensure that airborne particles and contaminants are minimized, protecting sensitive processes.
What is the process for cleanroom installation?
The cleanroom installation process typically begins with planning and design, followed by site preparation. Once the infrastructure is in place, modular components are assembled, and systems for air filtration and temperature control are integrated.
What is a modular cleanroom?
A modular cleanroom is a pre-fabricated structure designed to provide controlled environments with minimal contamination. They offer flexibility in design and can be customized to meet specific industry requirements, making them versatile solutions.
How to create a cleanroom contingency plan?
Creating a cleanroom contingency plan involves identifying potential risks, establishing protocols for emergencies, and training personnel on procedures. Regular drills and reviews ensure everyone is prepared to respond effectively to unforeseen situations.
What is the airflow rate in an ISO 6 cleanroom?
The airflow rate in an ISO 6 cleanroom typically ranges between 300 and 450 air changes per hour. This high rate helps maintain stringent cleanliness standards by continuously filtering out airborne contaminants.
What are the thermal requirements for cleanrooms?
Cleanrooms need to maintain specific thermal conditions, usually between 20°C and 24°C. These temperature ranges help ensure that equipment operates effectively and that chemical processes remain stable without contamination risks.
How does a modular cleanroom work?
A modular cleanroom works by maintaining controlled airflow, temperature, and humidity levels. Advanced filtration systems and positive pressure help keep contaminants out, while strict protocols govern personnel and material movement.
How to ensure effective cleanroom training?
Effective cleanroom training involves comprehensive programs covering protocols, equipment usage, and contamination control. Regular assessments and refresher courses help reinforce knowledge and ensure compliance with best practices in cleanroom environments.
What are the differences between ISO classes?
ISO classes differ in the allowable particle counts and cleanliness levels. For example, ISO 1 has the lowest allowable particle count, while ISO 9 permits more contamination, making each class suitable for different applications.
How to handle hazardous materials in a cleanroom?
Handling hazardous materials in a cleanroom requires strict adherence to safety protocols, including proper personal protective equipment and containment methods. Training personnel on these procedures is crucial for maintaining safety and cleanliness.
What materials are used in modular cleanrooms?
Modular cleanrooms are typically constructed from materials like stainless steel, aluminum, and cleanroom-compatible panels. These materials are chosen for their durability, ease of cleaning, and ability to minimize contamination.
What is the lifespan of a modular cleanroom?
The lifespan of a modular cleanroom can range from 10 to 20 years, depending on usage and maintenance. Regular inspections and upkeep can extend the longevity and efficiency of the cleanroom environment.
How to manage personnel flow in a cleanroom?
Managing personnel flow in a cleanroom involves establishing clear protocols for entry and exit. Designating specific pathways and implementing gowning procedures can help minimize contamination risks while ensuring efficiency.
How to monitor temperature and humidity in a cleanroom?
Monitoring temperature and humidity in a cleanroom typically involves using calibrated sensors and data loggers. Continuous monitoring ensures that conditions remain within specified limits, crucial for maintaining product quality and safety.
Factory Production Workshop Video
Factory Photo
Product Packaging And International Logistics
Product International Certification
Find Other Common Equipment Recommendations
-
Modular CleanRoom
US$9000-10000 USD/Unit
Min. Order:1 Set -
Air Shower
US$1000.00-5000.00 USD/Unit
Min. Order:1 Set -
Downflow Booth
US$3000-6000 USD/Unit
Min. Order:1 Set -
Clean bench
US$600-2000 USD/Unit
Min. Order:1 Set -
Air Filter
US$3-50 USD/Unit
Min. Order:1 Set -
Cleanroom Wall Panels
US$10-20 USD/sq.
Min. Order:1 Set -
Pass Box
US$200-500 USD/Unit
Min. Order:1 Set -
FFU
US$135-350 USD/Unit
Min. Order:1 Set -
Fume Hood
US$700-1500 USD/Unit
Min. Order:1 Set -
Cleanroom HVAC
US$5000-20000 USD/Unit
Min. Order:1 Set -
Clean room floor
US$5-20 USD/Sq.
Min. Order:1 Set -
Clean room ceiling
US$
Min. Order:1 Set