4 x 5m ISO 7 Softwall Cleanroom
Reference Price:US$5500.00-7500.00
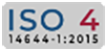
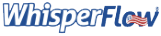



Cleanroom
4 x 5m ISO 7 Softwall Cleanroom
Choose your installation & validation options below
Quantity:
Choose your Cleanroom frame structure material
Quantity:
Choose your Cleanroom Wall enclosure materials
Quantity:
Choose your Temperature requirements
Quantity:
Choose your humidity requirements
Quantity:
Choose your Explosion-proof requirements
Quantity:
Summary
4 x 5m ISO 7 Softwall Cleanroom
Validation
Installation & Validation
Find Similar Products
-
5 x 5m ISO 7 Softwall Cleanroom
US$4000-13000 USD/Set
Min. Order:1 Set -
4 x 5m ISO 7 Softwall Cleanroom
US$4000-13000 USD/Set
Min. Order:1 Set -
4 x 4m ISO 7 Softwall Cleanroom
US$4000-13000 USD/Set
Min. Order:1 Set -
3 x 6m ISO 7 Softwall Cleanroom
US$4000-13000 USD/Set
Min. Order:1 Set -
3 x 5m ISO 7 Softwall Cleanroom
US$4000-13000 USD/Set
Min. Order:1 Set -
3 x 4m ISO 7 Softwall Cleanroom
US$4000-13000 USD/Set
Min. Order:1 Set
Cleanrooms Detail
An ISO 7 softwall cleanroom is a controlled environment designed to limit airborne particulate contamination to a specific level, defined by the ISO 14644-1 standard. In an ISO 7 cleanroom, the maximum allowable particle count is 352,000 particles per cubic meter for particles ≥0.5 micrometers.
Key Parameters and Standards
Air Quality:
352,000 particles/m³ (≥0.5 µm)
83,200 particles/m³ (≥1.0 µm)
Air Changes:Typically requires 30 to 60 air changes per hour, depending on the specific application.
Temperature: Usually maintained between 20°C to 22°C (68°F to 72°F).
Humidity: Typically kept between 30% to 60% relative humidity.
Applications
ISO 7 softwall cleanrooms are commonly used in various industries, including:
Pharmaceutical Manufacturing: Required for the production of sterile products and medications.
Biotechnology: Used in cell culture and research applications where contamination control is critical.
Electronics Manufacturing: Essential for the production of semiconductors and sensitive electronic components.
Medical Device Manufacturing: Ensures the cleanliness needed for the production of sterile devices.
These cleanrooms provide a flexible and cost-effective solution for industries that require stringent contamination control while allowing for easy configuration and scalability.
Cleanrooms Airflow
The airflow principles in an ISO 7 softwall cleanroom are essential for maintaining the desired cleanliness levels and controlling contamination. Here’s a brief overview of the key concepts involved:
Unidirectional Flow:
ISO 7 cleanrooms typically employ unidirectional airflow, where air moves in a consistent direction (usually from top to bottom or side to side). This design helps to sweep particles away from critical areas and minimizes stagnation, reducing the risk of contamination.HEPA Filtration:
High-Efficiency Particulate Air (HEPA) filters are crucial in maintaining cleanroom air quality. These filters remove at least 99.97% of particles ≥0.3 micrometers. In an ISO 7 cleanroom, air is drawn through these filters before being distributed throughout the space, ensuring that the air supplied is clean.Air Changes per Hour (ACH):
An ISO 7 cleanroom typically requires 30 to 60 air changes per hour. This rate ensures that the air within the cleanroom is regularly replaced, reducing the concentration of airborne particles and maintaining overall air quality.Positive Pressure:
The cleanroom is maintained at a positive pressure relative to adjacent areas. This pressure differential helps prevent unfiltered air from entering the cleanroom, further ensuring that contamination is kept to a minimum.Return Air Path:
Air is usually exhausted from the cleanroom through return air grilles, which are strategically placed to enhance airflow patterns. The return air is then filtered and conditioned before being reintroduced into the cleanroom, creating a continuous circulation loop.
By understanding and implementing these airflow principles, ISO 7 softwall cleanrooms can effectively maintain the required cleanliness levels necessary for various sensitive applications.
Cleanrooms Installation
ISO 7 Softwall Cleanrooms Installation Steps
Site Preparation: Clean the area and ensure a suitable, level floor.
Framework Construction: Build the support structure for softwall panels.
Wall Installation: Attach softwall panels securely to minimize gaps.
Ceiling and Lighting: Install cleanroom-compatible ceiling panels and lighting fixtures.
Airflow System Setup: Install HEPA filters, ductwork, and air supply vents.
Pressure and Temperature Control: Set up HVAC systems to maintain desired conditions.
Testing and Validation: Conduct airflow and particle count tests to ensure compliance with ISO 7 standards.
Final Inspection: Verify installation and obtain certification of cleanliness.
These steps ensure the effective installation of an ISO 7 softwall cleanroom.
Cleanrooms Testing
Air Cleanliness: The clean room must be able to control the number of particles and microorganisms in the air so that the air cleanliness meets the specified requirements.
Temperature and humidity: The clean room needs to control the indoor temperature and humidity to adapt to different production needs. Temperatures typically need to be controlled at 20-24°C and relative humidity at 45-60%.
Lighting: Clean rooms need to provide adequate lighting to ensure that staff can clearly see the objects being operated. In general, the illumination should be greater than 300 lux.
Pressure difference: In order to prevent external contamination into the clean room, need to maintain a certain indoor and outdoor pressure difference. Generally speaking, the indoor pressure should be slightly higher than the outdoor pressure.
Noise: Noise at work in the clean room should be kept within permissible limits to protect the physical and mental health of staff.
FAQ
1. What is the significance of particle counting in cleanrooms?
Particle counting is essential in cleanrooms as it measures the concentration of airborne particles, determining the cleanliness level of the environment. This data is crucial for ensuring compliance with industry standards and maintaining product integrity in sensitive manufacturing processes.
2. What are the best practices for gowning in a cleanroom?
Best practices for gowning in a cleanroom include following a specific order when donning garments, starting with shoe covers, and moving to coveralls, gloves, and hoods. Personnel should be trained regularly to ensure compliance, minimizing contamination risks effectively.
3. How does cross-contamination occur in cleanrooms?
Cross-contamination in cleanrooms occurs primarily through personnel movement, equipment transfer, and inadequate airflow. Contaminants can be introduced from outside sources or migrate between areas, highlighting the need for strict protocols and training to prevent these risks.
4. How are cleanroom systems integrated with existing facilities?
Integrating cleanroom systems with existing facilities requires careful planning and assessment of current infrastructure. This includes evaluating HVAC systems, electrical supply, and structural modifications necessary to ensure compatibility and maintain regulatory compliance throughout the integration process.
5. What types of flooring are suitable for cleanrooms?
Suitable flooring for cleanrooms includes vinyl, epoxy, and polished concrete, each offering benefits like durability and ease of maintenance. The choice depends on cleanliness requirements, chemical resistance, and the specific cleanroom classification to ensure optimal performance.
6. How do you handle waste in a cleanroom?
Handling waste in a cleanroom involves strict protocols for segregation and disposal. Waste should be placed in labeled containers based on type, and personnel must wear protective gear during handling. Regular removal prevents overflow and maintains cleanliness.
7. How can I improve airflow in my cleanroom?
To improve airflow in a cleanroom, assess current airflow patterns to identify stagnant areas. Implementing a balanced HVAC system, conducting regular maintenance, and strategically placing air diffusers can enhance air circulation and ensure even distribution throughout the space.
8. What are the benefits of a softwall cleanroom?
Softwall cleanrooms offer flexibility and cost-effectiveness, allowing for easy modifications or expansions as needed. Their modular design simplifies installation and maintenance while providing a controlled environment, making them suitable for various applications in cleanroom settings.
9. Can you customize a modular cleanroom design?
Yes, modular cleanroom designs can be customized to meet specific requirements, including size, layout, and airflow specifications. This flexibility allows organizations to tailor cleanroom solutions based on unique processes and regulatory standards, ensuring optimal functionality.
10. What are the most common cleanroom standards?
The most common cleanroom standards include ISO 14644-1, which specifies classifications based on airborne particulate cleanliness, and Federal Standard 209E, which categorizes cleanrooms by cleanliness levels. Compliance with these standards ensures consistent quality and safety in controlled environments.
11. How do I budget for a cleanroom project?
Budgeting for a cleanroom project involves estimating costs for construction, equipment, and compliance measures. Consider factors like size, design complexity, and intended use, along with ongoing operational expenses, to create a comprehensive budget that meets project requirements.
12. Can you relocate a modular cleanroom?
Yes, a modular cleanroom can be relocated, as its design allows for disassembly and reconfiguration. This flexibility enables organizations to adapt to changing needs or facility layouts while maintaining the cleanroom's integrity and operational standards throughout the process.
13. What is the typical size of a modular cleanroom?
The typical size of a modular cleanroom varies widely, depending on the application and requirements. Common configurations range from small rooms of around 100 square feet to larger installations exceeding 1,000 square feet, tailored to specific operational needs.
14. What is a modular cleanroom?
A modular cleanroom is a prefabricated, customizable cleanroom structure that can be easily assembled and modified. Designed for flexibility and efficiency, it provides controlled environments for sensitive processes while ensuring compliance with industry cleanliness standards.
15. How do contaminants enter a cleanroom?
Contaminants can enter a cleanroom through various channels, including personnel, equipment, and inadequate air filtration. Proper gowning protocols, thorough cleaning, and an effective HVAC system are essential to minimize the risk of contamination in these controlled environments.
16. What is the role of an HVAC system in a cleanroom?
The HVAC system in a cleanroom is crucial for maintaining the required temperature, humidity, and air cleanliness levels. It ensures proper air circulation, filtration, and pressurization to prevent contamination, thus supporting the overall integrity of cleanroom operations.
17. What are the key performance indicators for cleanrooms?
Key performance indicators (KPIs) for cleanrooms include particle counts, air change rates, temperature and humidity levels, and system pressure differentials. Regular monitoring of these metrics helps ensure compliance with cleanliness standards and supports the overall effectiveness of cleanroom operations.
Factory Production Workshop Video
Factory Photo
Product Packaging And International Logistics
Product International Certification
Find Other Common Equipment Recommendations
-
Modular CleanRoom
US$9000-10000 USD/Unit
Min. Order:1 Set -
Air Shower
US$1000.00-5000.00 USD/Unit
Min. Order:1 Set -
Downflow Booth
US$3000-6000 USD/Unit
Min. Order:1 Set -
Clean bench
US$600-2000 USD/Unit
Min. Order:1 Set -
Air Filter
US$3-50 USD/Unit
Min. Order:1 Set -
Cleanroom Wall Panels
US$10-20 USD/sq.
Min. Order:1 Set -
Pass Box
US$200-500 USD/Unit
Min. Order:1 Set -
FFU
US$135-350 USD/Unit
Min. Order:1 Set -
Fume Hood
US$700-1500 USD/Unit
Min. Order:1 Set -
Cleanroom HVAC
US$5000-20000 USD/Unit
Min. Order:1 Set -
Clean room floor
US$5-20 USD/Sq.
Min. Order:1 Set -
Clean room ceiling
US$
Min. Order:1 Set