4 x 4m ISO 7 Softwall Cleanroom
Reference Price:US$72000.00-8500.00
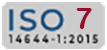
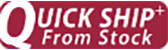



Cleanroom
4 x 4m ISO 7 Softwall Cleanroom
Choose your installation & validation options below
Quantity:
Choose your Cleanroom frame structure material
Quantity:
Choose your Cleanroom Wall enclosure materials
Quantity:
Choose your Temperature requirements
Quantity:
Choose your humidity requirements
Quantity:
Choose your Explosion-proof requirements
Quantity:
Summary
4 x 4m ISO 7 Softwall Cleanroom
Validation
Installation & Validation
Find Similar Products
-
5 x 5m ISO 7 Softwall Cleanroom
US$4000-13000 USD/Set
Min. Order:1 Set -
4 x 5m ISO 7 Softwall Cleanroom
US$4000-13000 USD/Set
Min. Order:1 Set -
4 x 4m ISO 7 Softwall Cleanroom
US$4000-13000 USD/Set
Min. Order:1 Set -
3 x 6m ISO 7 Softwall Cleanroom
US$4000-13000 USD/Set
Min. Order:1 Set -
3 x 5m ISO 7 Softwall Cleanroom
US$4000-13000 USD/Set
Min. Order:1 Set -
3 x 4m ISO 7 Softwall Cleanroom
US$4000-13000 USD/Set
Min. Order:1 Set
Cleanrooms Detail
An ISO 7 softwall cleanroom is a controlled environment designed to limit airborne particulate contamination to a specific level, defined by the ISO 14644-1 standard. In an ISO 7 cleanroom, the maximum allowable particle count is 352,000 particles per cubic meter for particles ≥0.5 micrometers.
Key Parameters and Standards
Air Quality:
352,000 particles/m³ (≥0.5 µm)
83,200 particles/m³ (≥1.0 µm)
Air Changes:Typically requires 30 to 60 air changes per hour, depending on the specific application.
Temperature: Usually maintained between 20°C to 22°C (68°F to 72°F).
Humidity: Typically kept between 30% to 60% relative humidity.
Applications
ISO 7 softwall cleanrooms are commonly used in various industries, including:
Pharmaceutical Manufacturing: Required for the production of sterile products and medications.
Biotechnology: Used in cell culture and research applications where contamination control is critical.
Electronics Manufacturing: Essential for the production of semiconductors and sensitive electronic components.
Medical Device Manufacturing: Ensures the cleanliness needed for the production of sterile devices.
These cleanrooms provide a flexible and cost-effective solution for industries that require stringent contamination control while allowing for easy configuration and scalability.
Cleanrooms Airflow
The airflow principles in an ISO 7 softwall cleanroom are essential for maintaining the desired cleanliness levels and controlling contamination. Here’s a brief overview of the key concepts involved:
Unidirectional Flow:
ISO 7 cleanrooms typically employ unidirectional airflow, where air moves in a consistent direction (usually from top to bottom or side to side). This design helps to sweep particles away from critical areas and minimizes stagnation, reducing the risk of contamination.HEPA Filtration:
High-Efficiency Particulate Air (HEPA) filters are crucial in maintaining cleanroom air quality. These filters remove at least 99.97% of particles ≥0.3 micrometers. In an ISO 7 cleanroom, air is drawn through these filters before being distributed throughout the space, ensuring that the air supplied is clean.Air Changes per Hour (ACH):
An ISO 7 cleanroom typically requires 30 to 60 air changes per hour. This rate ensures that the air within the cleanroom is regularly replaced, reducing the concentration of airborne particles and maintaining overall air quality.Positive Pressure:
The cleanroom is maintained at a positive pressure relative to adjacent areas. This pressure differential helps prevent unfiltered air from entering the cleanroom, further ensuring that contamination is kept to a minimum.Return Air Path:
Air is usually exhausted from the cleanroom through return air grilles, which are strategically placed to enhance airflow patterns. The return air is then filtered and conditioned before being reintroduced into the cleanroom, creating a continuous circulation loop.
By understanding and implementing these airflow principles, ISO 7 softwall cleanrooms can effectively maintain the required cleanliness levels necessary for various sensitive applications.
Cleanrooms Installation
ISO 7 Softwall Cleanrooms Installation Steps
Site Preparation: Clean the area and ensure a suitable, level floor.
Framework Construction: Build the support structure for softwall panels.
Wall Installation: Attach softwall panels securely to minimize gaps.
Ceiling and Lighting: Install cleanroom-compatible ceiling panels and lighting fixtures.
Airflow System Setup: Install HEPA filters, ductwork, and air supply vents.
Pressure and Temperature Control: Set up HVAC systems to maintain desired conditions.
Testing and Validation: Conduct airflow and particle count tests to ensure compliance with ISO 7 standards.
Final Inspection: Verify installation and obtain certification of cleanliness.
These steps ensure the effective installation of an ISO 7 softwall cleanroom.
Cleanrooms Testing
Air Cleanliness: The clean room must be able to control the number of particles and microorganisms in the air so that the air cleanliness meets the specified requirements.
Temperature and humidity: The clean room needs to control the indoor temperature and humidity to adapt to different production needs. Temperatures typically need to be controlled at 20-24°C and relative humidity at 45-60%.
Lighting: Clean rooms need to provide adequate lighting to ensure that staff can clearly see the objects being operated. In general, the illumination should be greater than 300 lux.
Pressure difference: In order to prevent external contamination into the clean room, need to maintain a certain indoor and outdoor pressure difference. Generally speaking, the indoor pressure should be slightly higher than the outdoor pressure.
Noise: Noise at work in the clean room should be kept within permissible limits to protect the physical and mental health of staff.
FAQ
1. How do you select the right cleanroom?
Selecting the right cleanroom involves evaluating several factors that align with the specific needs of your operation. Key considerations include the required cleanliness level, the type of processes to be conducted, and compliance with relevant industry standards. Additionally, assessing the space available and the budget can help determine the most suitable cleanroom configuration.
2. How do you handle waste in a cleanroom?
Handling waste in a cleanroom requires strict adherence to protocols to prevent contamination. Waste should be segregated into specific categories, such as hazardous, non-hazardous, and recyclable materials. This segregation is essential for effective disposal. Furthermore, waste should be removed regularly and stored in appropriate containers to minimize risks.
3. What are the common misconceptions about cleanrooms?
Common misconceptions about cleanrooms include the belief that they are completely sterile environments and that they do not require maintenance. In reality, cleanrooms are controlled environments designed to minimize contamination, but they are not entirely free of particles. Regular maintenance and cleaning are crucial for ensuring their effectiveness. Other misconceptions include that cleanrooms are only necessary for high-tech industries, whereas various sectors can benefit from their use.
4. How do you maintain an ISO 7 cleanroom?
Maintaining an ISO 7 cleanroom requires continuous monitoring of environmental conditions and adherence to strict cleaning protocols. Key practices include:
Regularly checking and calibrating monitoring equipment.
Implementing a rigorous cleaning schedule that includes daily, weekly, and monthly tasks.
Ensuring personnel follow proper gowning procedures to minimize contamination risks.
These efforts help ensure compliance with ISO standards and maintain the required cleanliness levels.
5. How do you handle emergencies in a cleanroom?
Handling emergencies in a cleanroom requires pre-established protocols and thorough training for personnel. In the event of an emergency, such as a contamination incident or equipment failure, staff should follow the emergency action plan, which typically includes isolating affected areas, notifying management, and documenting the incident. Regular drills and training sessions help prepare personnel to respond effectively to emergencies.
6. How often should cleanrooms be cleaned?
The frequency of cleanroom cleaning depends on the cleanroom classification and the specific activities conducted within it. Generally, high-traffic areas such as ISO 5 cleanrooms may require daily cleaning, while ISO 7 cleanrooms may have a less frequent schedule, such as every few days. Regularly scheduled maintenance and cleaning are essential for maintaining cleanliness and compliance with industry standards.
7. How do you install a softwall cleanroom?
Installing a softwall cleanroom involves several straightforward steps. First, designate the installation area and ensure it is clean and clear of obstructions. Next, assemble the framework, typically made of aluminum or steel, to create the structure. Finally, attach the softwall material to the framework while ensuring proper sealing to maintain cleanliness. Regular inspections during installation can help ensure that all components are correctly positioned.
8. What are the advantages of using softwall over hardwall cleanrooms?
Softwall cleanrooms offer several advantages compared to hardwall cleanrooms, including:
Cost-effectiveness: Softwall cleanrooms are generally less expensive to install and maintain.
Flexibility: They can be easily reconfigured or expanded as needs change.
Ease of installation: Softwall cleanrooms typically require less time for setup, allowing for quicker deployment.
These benefits make softwall cleanrooms an attractive option for many industries.
9. How is pressure differential maintained in a cleanroom?
Pressure differential in a cleanroom is maintained through the use of specialized HVAC systems designed to create a controlled airflow. By ensuring that air flows into the cleanroom from adjacent areas, the pressure inside the cleanroom remains higher than the surrounding environment. This positive pressure helps prevent outside contaminants from entering the cleanroom, which is essential for maintaining cleanliness standards.
10. What is the process for validating a cleanroom?
The validation process for a cleanroom typically includes several key steps:
Developing a validation protocol that outlines the objectives and methods to be used.
Performing qualification tests for installation (IQ), operational (OQ), and performance (PQ) to assess compliance with design specifications.
Documenting all findings and any corrective actions taken to ensure that the cleanroom meets the necessary standards.
These steps are crucial for ensuring the cleanroom operates effectively and meets regulatory requirements.
11. How do you design a cleanroom for pharmaceutical applications?
Designing a cleanroom for pharmaceutical applications requires careful consideration of several factors. First, the cleanroom must comply with regulatory standards such as those set by the FDA. Design elements include:
Specific cleanliness levels based on the processes involved.- Controlled airflow design to ensure that air moves in a way that prevents contamination.
Materials selection that minimizes particle generation and is easy to clean.
Additionally, integrating a suitable HVAC system and ensuring proper gowning and operational procedures are vital for maintaining the required environment for pharmaceutical operations.
12. What is the importance of air quality in cleanrooms?
Air quality in cleanrooms is critical for maintaining the required cleanliness levels and ensuring product integrity. Poor air quality can lead to contamination from particles, microorganisms, and chemical pollutants, which can compromise sensitive processes. Factors that influence air quality include:
Air filtration systems that are designed to remove particulates and contaminants.
Airflow patterns that minimize dead zones and ensure a uniform distribution of clean air.
Regular monitoring of environmental parameters such as temperature, humidity, and pressure.
Maintaining high air quality is essential for compliance with industry standards and the overall success of cleanroom operations.
13. Can you customize a modular cleanroom design?
Yes, modular cleanroom designs can be highly customized to meet specific operational needs. Customization options include:
Size and layout to fit existing spaces or to accommodate unique workflows.
Wall materials and finishes that suit the cleanliness level and aesthetic preferences.
HVAC configurations tailored to specific temperature and humidity requirements.
This flexibility allows organizations to create a cleanroom that aligns perfectly with their operational demands while maintaining compliance with regulations.
14. What materials are used in modular cleanrooms?
Modular cleanrooms are typically constructed using a variety of materials that are selected based on their performance and ease of maintenance. Common materials include:
Pre-finished metal panels for walls that offer durability and ease of cleaning.
Polycarbonate or vinyl for softwall systems that allow for flexibility and modularity.
Antimicrobial coatings that help reduce the risk of contamination.
These materials ensure that modular cleanrooms are both functional and compliant with cleanliness standards.
15. What is the role of an HVAC system in a cleanroom?
The HVAC system plays a crucial role in maintaining the environmental conditions necessary for a cleanroom’s operation. Its primary functions include:
Air filtration, using HEPA or ULPA filters to remove airborne particles and contaminants.
Temperature and humidity control to create a stable environment that meets specific requirements.
Pressure control to maintain positive or negative pressure differentials as needed.
A properly designed and maintained HVAC system is essential for ensuring the effectiveness of cleanroom operations and compliance with industry standards.
16. What are common contaminants found in cleanrooms?
Common contaminants in cleanrooms can be categorized into several types, including:
Particulate matter: Dust, fibers, and other solid particles that can compromise product integrity.
Microorganisms: Bacteria, fungi, and viruses that can cause contamination in sensitive environments.
Chemical vapors: Residual solvents or cleaning agents that may be present in the air.
Identifying and controlling these contaminants is essential for maintaining compliance with cleanliness standards and ensuring the success of cleanroom applications.
Factory Production Workshop Video
Factory Photo
Product Packaging And International Logistics
Product International Certification
Find Other Common Equipment Recommendations
-
Modular CleanRoom
US$9000-10000 USD/Unit
Min. Order:1 Set -
Air Shower
US$1000.00-5000.00 USD/Unit
Min. Order:1 Set -
Downflow Booth
US$3000-6000 USD/Unit
Min. Order:1 Set -
Clean bench
US$600-2000 USD/Unit
Min. Order:1 Set -
Air Filter
US$3-50 USD/Unit
Min. Order:1 Set -
Cleanroom Wall Panels
US$10-20 USD/sq.
Min. Order:1 Set -
Pass Box
US$200-500 USD/Unit
Min. Order:1 Set -
FFU
US$135-350 USD/Unit
Min. Order:1 Set -
Fume Hood
US$700-1500 USD/Unit
Min. Order:1 Set -
Cleanroom HVAC
US$5000-20000 USD/Unit
Min. Order:1 Set -
Clean room floor
US$5-20 USD/Sq.
Min. Order:1 Set -
Clean room ceiling
US$
Min. Order:1 Set