3 x 4m ISO 7 Softwall Cleanroom
Reference Price:US$4600.00-5500.00
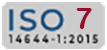

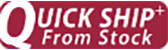
Cleanroom
3 x 4m ISO 7 Softwall Cleanroom
Choose your installation & validation options below
Quantity:
Choose your Cleanroom frame structure material
Quantity:
Choose your Cleanroom Wall enclosure materials
Quantity:
Choose your Temperature requirements
Quantity:
Choose your humidity requirements
Quantity:
Choose your Explosion-proof requirements
Quantity:
Summary
3 x 4m ISO 7 Softwall Cleanroom
Validation
Installation & Validation
Find Similar Products
-
5 x 5m ISO 7 Softwall Cleanroom
US$4000-13000 USD/Set
Min. Order:1 unit -
4 x 5m ISO 7 Softwall Cleanroom
US$4000-13000 USD/Set
Min. Order:1 unit -
4 x 4m ISO 7 Softwall Cleanroom
US$4000-13000 USD/Set
Min. Order:1 unit -
3 x 6m ISO 7 Softwall Cleanroom
US$4000-13000 USD/Set
Min. Order:1 unit -
3 x 5m ISO 7 Softwall Cleanroom
US$4000-13000 USD/Set
Min. Order:1 unit -
3 x 4m ISO 7 Softwall Cleanroom
US$4000-13000 USD/Set
Min. Order:1 unit
Cleanrooms Detail
An ISO 7 softwall cleanroom is a controlled environment designed to limit airborne particulate contamination to a specific level, defined by the ISO 14644-1 standard. In an ISO 7 cleanroom, the maximum allowable particle count is 352,000 particles per cubic meter for particles ≥0.5 micrometers.
Key Parameters and Standards
Air Quality:
352,000 particles/m³ (≥0.5 µm)
83,200 particles/m³ (≥1.0 µm)
Air Changes:Typically requires 30 to 60 air changes per hour, depending on the specific application.
Temperature: Usually maintained between 20°C to 22°C (68°F to 72°F).
Humidity: Typically kept between 30% to 60% relative humidity.
Applications
ISO 7 softwall cleanrooms are commonly used in various industries, including:
Pharmaceutical Manufacturing: Required for the production of sterile products and medications.
Biotechnology: Used in cell culture and research applications where contamination control is critical.
Electronics Manufacturing: Essential for the production of semiconductors and sensitive electronic components.
Medical Device Manufacturing: Ensures the cleanliness needed for the production of sterile devices.
These cleanrooms provide a flexible and cost-effective solution for industries that require stringent contamination control while allowing for easy configuration and scalability.
Cleanrooms Airflow
The airflow principles in an ISO 7 softwall cleanroom are essential for maintaining the desired cleanliness levels and controlling contamination. Here’s a brief overview of the key concepts involved:
Unidirectional Flow:
ISO 7 cleanrooms typically employ unidirectional airflow, where air moves in a consistent direction (usually from top to bottom or side to side). This design helps to sweep particles away from critical areas and minimizes stagnation, reducing the risk of contamination.HEPA Filtration:
High-Efficiency Particulate Air (HEPA) filters are crucial in maintaining cleanroom air quality. These filters remove at least 99.97% of particles ≥0.3 micrometers. In an ISO 7 cleanroom, air is drawn through these filters before being distributed throughout the space, ensuring that the air supplied is clean.Air Changes per Hour (ACH):
An ISO 7 cleanroom typically requires 30 to 60 air changes per hour. This rate ensures that the air within the cleanroom is regularly replaced, reducing the concentration of airborne particles and maintaining overall air quality.Positive Pressure:
The cleanroom is maintained at a positive pressure relative to adjacent areas. This pressure differential helps prevent unfiltered air from entering the cleanroom, further ensuring that contamination is kept to a minimum.Return Air Path:
Air is usually exhausted from the cleanroom through return air grilles, which are strategically placed to enhance airflow patterns. The return air is then filtered and conditioned before being reintroduced into the cleanroom, creating a continuous circulation loop.
By understanding and implementing these airflow principles, ISO 7 softwall cleanrooms can effectively maintain the required cleanliness levels necessary for various sensitive applications.
Cleanrooms Installation
ISO 7 Softwall Cleanrooms Installation Steps
Site Preparation: Clean the area and ensure a suitable, level floor.
Framework Construction: Build the support structure for softwall panels.
Wall Installation: Attach softwall panels securely to minimize gaps.
Ceiling and Lighting: Install cleanroom-compatible ceiling panels and lighting fixtures.
Airflow System Setup: Install HEPA filters, ductwork, and air supply vents.
Pressure and Temperature Control: Set up HVAC systems to maintain desired conditions.
Testing and Validation: Conduct airflow and particle count tests to ensure compliance with ISO 7 standards.
Final Inspection: Verify installation and obtain certification of cleanliness.
These steps ensure the effective installation of an ISO 7 softwall cleanroom.
Cleanrooms Testing
Air Cleanliness: The clean room must be able to control the number of particles and microorganisms in the air so that the air cleanliness meets the specified requirements.
Temperature and humidity: The clean room needs to control the indoor temperature and humidity to adapt to different production needs. Temperatures typically need to be controlled at 20-24°C and relative humidity at 45-60%.
Lighting: Clean rooms need to provide adequate lighting to ensure that staff can clearly see the objects being operated. In general, the illumination should be greater than 300 lux.
Pressure difference: In order to prevent external contamination into the clean room, need to maintain a certain indoor and outdoor pressure difference. Generally speaking, the indoor pressure should be slightly higher than the outdoor pressure.
Noise: Noise at work in the clean room should be kept within permissible limits to protect the physical and mental health of staff.
FAQ
1. What industries use ISO 7 cleanrooms?
ISO 7 cleanrooms are commonly utilized in the pharmaceutical, biotechnology, and semiconductor industries. They provide controlled environments critical for manufacturing sterile products and sensitive electronic components.
2. What are the advantages of using softwall over hardwall cleanrooms?
Softwall cleanrooms are typically more flexible and easier to modify than hardwall cleanrooms. They offer cost-effective solutions for changing layouts and are lighter, which can reduce construction and installation time.
3. What is the typical size of a modular cleanroom?
Modular cleanrooms can vary widely in size, but typical dimensions range from small units of about 200 square feet to larger installations exceeding 1,000 square feet. Their modular design allows for scalability based on specific needs.
4. What are the key performance indicators for cleanrooms?
Key performance indicators (KPIs) for cleanrooms include particle count, air changes per hour, temperature and humidity levels, and pressure differentials. Monitoring these metrics ensures compliance with cleanliness standards and operational efficiency.
5. How do contaminants enter a cleanroom?
Contaminants can enter a cleanroom through various means, including personnel, equipment, and air exchange. Even minor breaches in protocols can allow dust, microbes, and other particulates to compromise the controlled environment.
6. How do you manage airflow patterns in a cleanroom?
Airflow patterns in a cleanroom are managed by strategically placing supply and exhaust vents. Utilizing laminar airflow systems ensures that air moves in a uniform direction, minimizing turbulence and reducing the risk of contamination.
7. How can you minimize contamination risk in a cleanroom?
To minimize contamination risk, it's essential to implement strict gowning procedures, maintain regular cleaning schedules, and use appropriate materials for surfaces and equipment. Training personnel on contamination control is also crucial.
8. How do softwall cleanrooms compare to hardwall cleanrooms?
Softwall cleanrooms are typically lighter and more versatile, allowing for easier reconfiguration. In contrast, hardwall cleanrooms offer more durability and stronger structural integrity, making them suitable for long-term installations.
9. What is the difference between a cleanroom and a controlled environment?
A cleanroom specifically controls particulate contamination levels, while a controlled environment may manage temperature, humidity, and other conditions without stringent particulate controls. Cleanrooms adhere to strict ISO classifications.
10. What are the temperature and humidity requirements for ISO 7 cleanrooms?
ISO 7 cleanrooms typically maintain temperature between 20-24°C (68-75°F) and relative humidity levels of 30-60%. These conditions help ensure optimal functioning of sensitive processes and products.
11. What types of flooring are suitable for cleanrooms?
Suitable flooring for cleanrooms includes vinyl, epoxy, and rubber flooring, as these materials are non-porous, easy to clean, and resistant to chemicals. They also help minimize the accumulation of dust and particles.
12. How do cleanroom certifications work?
Cleanroom certifications involve a series of tests to measure cleanliness levels, airflow, and environmental controls. Certification bodies typically assess compliance with ISO standards, ensuring the facility meets required cleanliness criteria.
13. How do I calculate air changes per hour in a cleanroom?
To calculate air changes per hour (ACH), divide the total airflow rate (in cubic feet per minute) by the cleanroom volume (in cubic feet), then multiply by 60. This provides the frequency of air changes per hour.
14. How does an ISO 7 cleanroom differ from other ISO classifications?
An ISO 7 cleanroom allows a maximum of 352,000 particles per cubic meter, which is more lenient than ISO 5 or ISO 6 classifications. It is suitable for processes requiring lower levels of contamination control.
15. What is a pass-through chamber in a cleanroom?
A pass-through chamber is an enclosed space that allows for the transfer of materials into and out of a cleanroom without compromising its cleanliness. It minimizes exposure to the external environment during transfers.
Factory Production Workshop Video
Factory Photo
Product Packaging And International Logistics
Product International Certification
Find Other Common Equipment Recommendations
-
Modular CleanRoom
US$9000-10000 USD/Unit
Min. Order:1 unit -
Air Shower
US$1000.00-5000.00 USD/Unit
Min. Order:1 unit -
Downflow Booth
US$3000-6000 USD/Unit
Min. Order:1 unit -
Clean bench
US$600-2000 USD/Unit
Min. Order:1 unit -
Air Filter
US$3-50 USD/Unit
Min. Order:1 unit -
Cleanroom Wall Panels
US$10-20 USD/sq.
Min. Order:1 unit -
Pass Box
US$200-500 USD/Unit
Min. Order:1 unit -
FFU
US$135-350 USD/Unit
Min. Order:1 unit -
Fume Hood
US$700-1500 USD/Unit
Min. Order:1 unit -
Cleanroom HVAC
US$5000-20000 USD/Unit
Min. Order:1 unit -
Clean room floor
US$5-20 USD/Sq.
Min. Order:1 unit -
Clean room ceiling
US$
Min. Order:1 unit