Class 100 Clean room
A Class 100 cleanroom, also known as ISO Class 5 cleanroom under the ISO 14644-1 standard, is a highly controlled environment designed to maintain extremely low levels of airborne particles. Specifically, it allows no more than 100 particles per cubic foot of air for particles ≥0.5 microns, which translates to no more than 3,520 particles per cubic meter.
Airflow and Filtration
HEPA Filters (High-Efficiency Particulate Air filters): These filters must remove at least 99.97% of airborne particles 0.3 microns in diameter.
Laminar Flow: Often utilized to ensure that air flows in a single direction, reducing turbulence and the potential for particle contamination.
High Air Change Rates: Typically around 240-480 air changes per hour to maintain the required cleanliness.
Operational Protocols
Strict Gowning Procedures: Personnel must wear full-body coveralls, hoods, gloves, masks, and shoe covers to prevent contamination.
Regular Cleaning: Thorough cleaning protocols must be followed to maintain cleanliness levels.
Applications
Semiconductor Manufacturing: Where microscopic contamination can affect the functionality of electronic components.
Pharmaceuticals: Particularly in the production of sterile products.
Biotechnology: Where contamination can compromise biological experiments or products.
Aerospace: For the assembly of sensitive components.
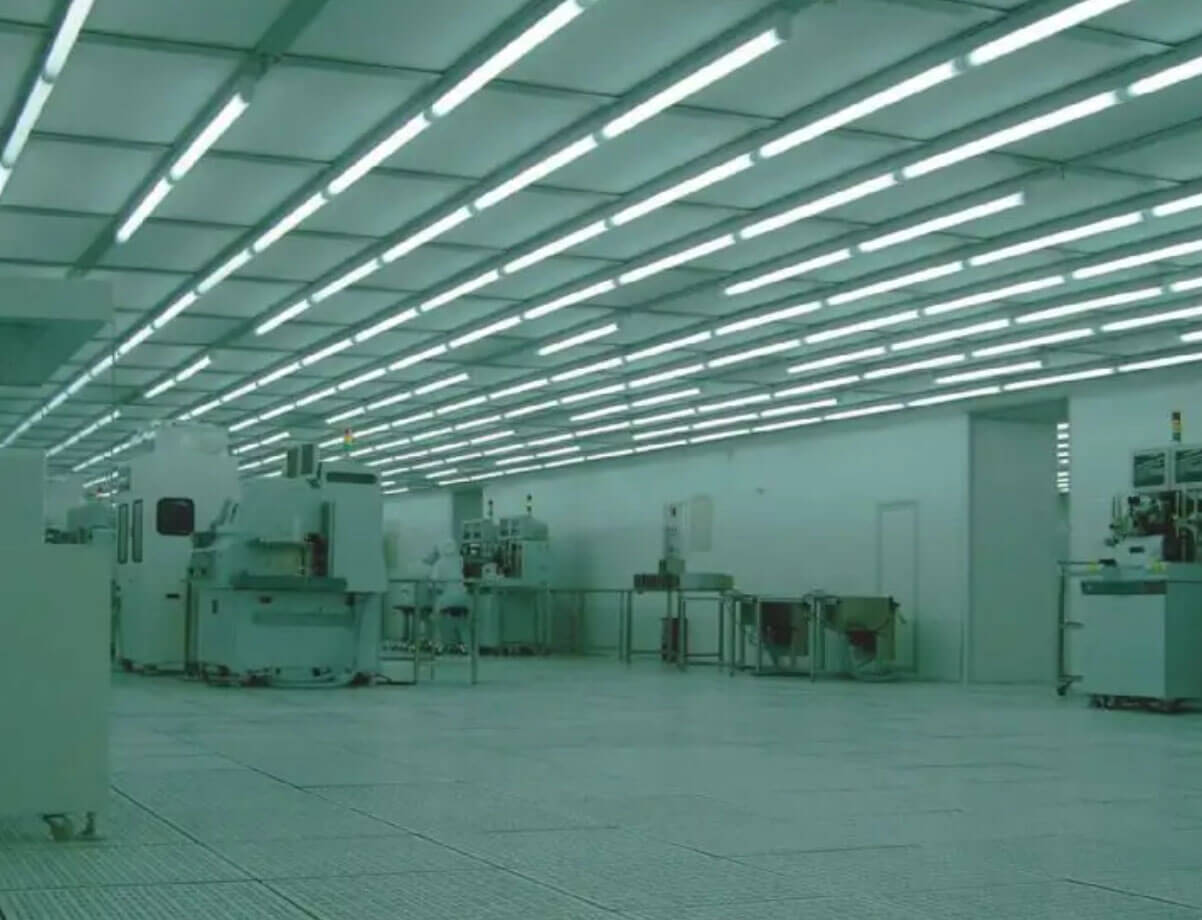
Clean room grade table
ISO Class FED STD 209E Equivalent | |||||||
ISO Class | Maximum Particles/m | FED STD 209E equivalent | |||||
≥0.1μm | ≥0.2um | ≥0.3um | ≥0.5um | ≥11m | ≥5um | ||
ISO1 | 10 | 2 | |||||
ISO2 | 100 | 24 | 10 | 4 | |||
ISO3 | 1,000 | 237 | 102 | 35 | 8 | Class1 | |
ISO4 | 10,000 | 2,370 | 1,020 | 352 | 83 | 3 | Class10 |
ISO5 | 100,000 | 23,700 | 10,200 | 3,520 | 832 | 29 | Class100 |
ISO6 | 1,000,000 | 237,000 | 102,000 | 35,200 | 8,320 | 293 | Class 1,000 |
ISO7 | 352,000 | 83,200 | 2,930 | Class10,000 | |||
ISO8 | 3,520,000 | 832,000 | 29,300 | Class 100,000 | |||
ISO9 | 35,200,000 | 8,320,000 | 293,000 | Room Air |
Comparison Table GMP/USP/ISO/FED209E | ||||||||||||
project | China GMP/Europe GMP | ISO | FED STD 209E | |||||||||
Suspended particles P/m3 | level | Static | dynamic | level | Static | level | dynamic | |||||
≥0.5um | ≥5μm | ≥0.5μm | ≥5μm | ≥0.5um | ≥5μm | ≥0.5um | ≥5μm | |||||
A | 3520 | 20 | 3520 | 20 | M3.5 | 3530 | 100 | 5 | 2220 | 20 | 100 | |
B | 3520 | 29 | 352000 | 2900 | - | - | 6 | 3520 | 29 | 1000 | ||
C | 352000 | 2900 | 3520000 | 29000 | M5.5 | 353000 | 10000 | 7 | 352000 | 2930 | 10000 | |
8. | 3520000 | 29300 | 100000 | |||||||||
D | 3520000 | 29000 | No regulations | No regulations | M6.5 | 3530000 | 100000 | 9 | 3520000 | 29300 | 100000 |
Comparison table of ISO grade standards and ventilation times | |
ISO Class | ACH(AIRCHANGE PER HOUR) |
ISO 3 | 360-540 |
ISO 4 | 300-540 |
ISO 5(class 100) | 240-480 |
ISO 6(class 1000) | 50-60 |
ISO 7(class 10000) | 30-40 |
ISO 8(class 100000) | 15-25 |
ISO Class 100 Clean Room Airflow
Air Changes per Hour (ACH): ISO Class 5 cleanrooms typically require 240 to 480 air changes per hour. | Air Velocity: FFU vertical unidirectional (laminar) airflow. | Temperature and Humidity Control: Typical ranges are 20-24°C for temperature and 30-60% for relative humidity, but these may vary based on specific requirements. |
Clean Room wall
![]() | ||
Cleanroom Panel | Cleanroom doors and windows | Handmade rock wool panel |
◇ Size and appearance: Ensure that the size and shape of the product meet the design requirements and have no obvious defects. ◇ Physical properties: Such as compression, tension, impact resistance and other tests to ensure the strength and durability of the material. ◇ Surface treatment: Confirm that the surface is smooth, the coating is uniform, and there are no bubbles, peeling, etc. ◇ Test report: Fire and corrosion resistance test |
ISO Class 100 Clean Room Celling
|
| ||
|
|
ISO Class 100 Clean Room Floor
| ||
![]() | ||
| ||
|
FAQ
What is the difference between clean room 100 and 1000?
The primary difference between a Class 100 cleanroom (ISO Class 5) and a Class 1000 cleanroom (ISO Class 6) lies in the allowable concentration of airborne particles. A Class 100 cleanroom permits no more than 100 particles per cubic foot of air for particles ≥0.5 microns, translating to 3,520 particles per cubic meter, whereas a Class 1000 cleanroom allows up to 1,000 particles per cubic foot, or 35,200 particles per cubic meter, for the same particle size. This means the air in a Class 100 cleanroom is ten times cleaner than in a Class 1000 cleanroom. Consequently, Class 100 cleanrooms require more stringent air filtration systems, higher air change rates, and stricter operational protocols compared to Class 1000 cleanrooms, making them suitable for more contamination-sensitive applications.
What are the requirements for a Class 100 000 clean room?
A Class 100,000 cleanroom, also known as ISO Class 8, requires maintaining a controlled environment where the concentration of airborne particles is kept within specific limits. Specifically, it allows no more than 100,000 particles per cubic foot of air for particles ≥0.5 microns, which equates to 3,520,000 particles per cubic meter. To achieve this, the cleanroom must incorporate effective air filtration systems, such as HEPA filters, and maintain a moderate air change rate, typically around 10-25 air changes per hour. The construction materials should be smooth and easily cleanable to minimize particle generation. Personnel must follow basic gowning procedures, including wearing lab coats, hair covers, and shoe covers, to reduce contamination. Regular cleaning and maintenance protocols are essential to sustain the cleanroom's integrity, ensuring it meets the required cleanliness standards for applications such as general manufacturing, electronics assembly, and quality inspection areas.
What is a class a cleanroom?
A Class A cleanroom, as defined by the European Union GMP standards, is a high-level clean environment essential for critical processes like aseptic filling and sterile product manufacturing. Equivalent to an ISO Class 5 cleanroom, it permits no more than 3,520 particles per cubic meter for particles ≥0.5 microns. Maintaining such cleanliness requires advanced HEPA filtration, high air change rates, and strict construction standards using smooth, non-shedding materials. Personnel must wear sterile full-body suits, gloves, masks, and shoe covers, following rigorous gowning procedures. Additionally, continuous environmental monitoring and stringent cleaning protocols are mandatory to ensure compliance, making Class A cleanrooms crucial for producing sterile pharmaceuticals and other sensitive products.
How much air change for class 100 cleanroom?
A Class 100 cleanroom, equivalent to ISO Class 5, requires a high number of air changes per hour to maintain its stringent cleanliness standards, typically ranging from 240 to 480 air changes per hour. This high air exchange rate is achieved through advanced HVAC systems equipped with HEPA filters, which effectively remove airborne particles. The continuous influx of filtered air helps to dilute and remove contaminants, ensuring that the concentration of particles remains within the specified limit of no more than 100 particles per cubic foot for particles ≥0.5 microns. This rigorous air change rate is essential for maintaining the ultra-clean environment necessary for sensitive applications such as semiconductor manufacturing, biotechnology, and pharmaceutical production.
An Overview of ISO 5 Cleanroom
An ISO 5 cleanroom, also known as a Class 100 cleanroom, is a highly controlled environment that allows no more than 3,520 particles per cubic meter for particles ≥0.5 microns. It requires advanced HEPA filtration systems and high air change rates, typically between 240 to 480 air changes per hour, to maintain its stringent cleanliness standards. Construction materials must be smooth, non-shedding, and easy to clean. Personnel must adhere to strict gowning protocols, including wearing full-body suits, gloves, masks, and shoe covers. Frequent environmental monitoring and rigorous cleaning procedures are essential to ensure compliance, making ISO 5 cleanrooms critical for industries needing ultra-clean conditions, such as semiconductor manufacturing, biotechnology, and pharmaceuticals.
Clean Room Classifications & ISO Standards
Cleanroom classifications and ISO standards define the levels of cleanliness required for controlled environments, primarily focusing on the concentration of airborne particles. The ISO 14644-1 standard categorizes cleanrooms from ISO Class 1 to ISO Class 9, with ISO Class 1 being the cleanest. Each class specifies the maximum allowable particle count per cubic meter at various particle sizes. For example, an ISO Class 5 cleanroom (Class 100) allows up to 3,520 particles per cubic meter for particles ≥0.5 microns. These standards ensure that cleanrooms meet the necessary contamination control for various industries, including pharmaceuticals, biotechnology, and electronics, by detailing requirements for air filtration, air change rates, construction materials, and operational protocols.
what is a class 100 clean room ?
A Class 100 cleanroom, also known as an ISO Class 5 cleanroom, is a controlled environment that limits airborne particles to no more than 100 particles per cubic foot of air for particles ≥0.5 microns, or 3,520 particles per cubic meter. Maintaining this level of cleanliness requires advanced HEPA filtration systems, high air change rates (typically 240 to 480 air changes per hour), and strict cleanliness protocols. Construction materials must be smooth, non-shedding, and easy to clean. Personnel must follow stringent gowning procedures, including wearing full-body suits, gloves, masks, and shoe covers. These cleanrooms are essential for industries where even minimal contamination can compromise product integrity, such as semiconductor manufacturing, biotechnology, and pharmaceuticals.
what is class 100 cleanroom ?
A Class 100 cleanroom, or ISO Class 5 cleanroom, is a highly controlled environment that restricts airborne particles to no more than 100 particles per cubic foot of air for particles ≥0.5 microns. It requires advanced HEPA filtration, high air change rates (240 to 480 per hour), and strict cleanliness protocols. Construction materials must be smooth and non-shedding, and personnel must follow rigorous gowning procedures, including full-body suits and masks. These cleanrooms are vital for industries like semiconductor manufacturing, biotechnology, and pharmaceuticals, where minimal contamination is critical.
what is a class 100 000clean room?
A Class 100,000 cleanroom, or ISO Class 8 cleanroom, limits airborne particles to no more than 100,000 particles per cubic foot of air for particles ≥0.5 microns, equivalent to 3,520,000 particles per cubic meter. Maintaining this environment requires effective air filtration systems, such as HEPA filters, and moderate air change rates, typically 10-25 air changes per hour. Construction materials should be smooth and easy to clean, and personnel must wear lab coats, hair covers, and shoe covers. These cleanrooms support less contamination-sensitive applications, including general manufacturing, electronics assembly, and quality inspection areas.
how to build a class 100clean room?
Building a Class 100 cleanroom (ISO Class 5) involves several key steps: installing advanced HEPA filtration systems to ensure high air quality and achieving 240 to 480 air changes per hour; using non-shedding, smooth, and cleanable construction materials; implementing stringent entry protocols, including airlocks and gowning areas where personnel don full-body suits, gloves, masks, and shoe covers; and establishing rigorous cleaning and maintenance schedules. Additionally, continuous environmental monitoring is essential to maintain the required particle levels, ensuring the cleanroom meets the standards necessary for sensitive industries like semiconductor manufacturing and pharmaceuticals.
what does class 100 000clean room mean?
A Class 100,000 cleanroom, or ISO Class 8, is a controlled environment that limits airborne particles to no more than 100,000 particles per cubic foot for particles ≥0.5 microns (3,520,000 particles per cubic meter). It requires effective air filtration, typically with HEPA filters, and moderate air change rates of 10-25 per hour. The room must be constructed with smooth, easy-to-clean materials, and personnel must follow basic gowning protocols, such as wearing lab coats, hair covers, and shoe covers. These cleanrooms are used for less contamination-sensitive tasks like general manufacturing and electronics assembly.
what does class 100 clean room mean?
A Class 100 cleanroom, or ISO Class 5, is a highly controlled environment that limits airborne particles to no more than 100 particles per cubic foot for particles ≥0.5 microns (3,520 particles per cubic meter). It requires advanced HEPA filtration systems and high air change rates, typically 240 to 480 per hour. The room is constructed with smooth, non-shedding materials, and stringent gowning protocols are enforced, including wearing full-body suits, gloves, masks, and shoe covers. These cleanrooms are essential for industries where minimal contamination is critical, such as semiconductor manufacturing, biotechnology, and pharmaceuticals.
what is meant by class 100clean room?
A Class 100 cleanroom, also known as an ISO Class 5 cleanroom, is an environment that limits airborne particles to no more than 100 particles per cubic foot for particles ≥0.5 microns (3,520 particles per cubic meter). It requires advanced HEPA filtration and high air change rates, typically 240 to 480 per hour, to maintain air purity. The room is constructed with smooth, non-shedding materials, and personnel must follow strict gowning protocols, including wearing full-body suits, gloves, masks, and shoe covers. These cleanrooms are essential for industries like semiconductor manufacturing, biotechnology, and pharmaceuticals, where minimal contamination is critical.