As a manager in an Electronic manufacturing facility, I am acutely aware of the critical importance of maintaining a controlled environment for our production processes. As we strive to meet international quality standards and ensure the longevity and reliability of our products, the need for A CleanRoom has become increasingly evident. This investment will not only enhance our production capabilities but also help us remain competitive in the rapidly evolving electronics market.
ISO Standards & CleanRoom Classification
Our planned CleanRoom will adhere to ISO standards, specifically targeting ISO Class 7 classification. This will ensure that our manufacturing processes are protected from contamination and meet stringent regulatory requirements. The cleanroom will be equipped with state-of-the-art HEPA filters to maintain air purity by capturing 99.97% of particles as small as 0.3 microns.
ISO Class 7 Cleanroom Standards
- Particle count ≤352,000 particles/m³ (≥0.5μm)
- Suitable for precision electronic component manufacturing
- Complies with Class 10,000 standards under static conditions
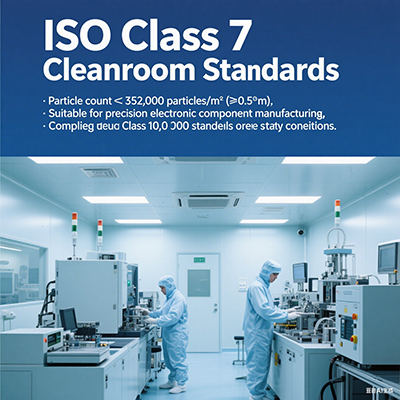
Airflow Management System
Inspired by industry leaders such as Deiiang™, our design will incorporate an advanced airflow management system capable of achieving 60-90 air changes per hour, which is critical for maintaining consistent environmental conditions.
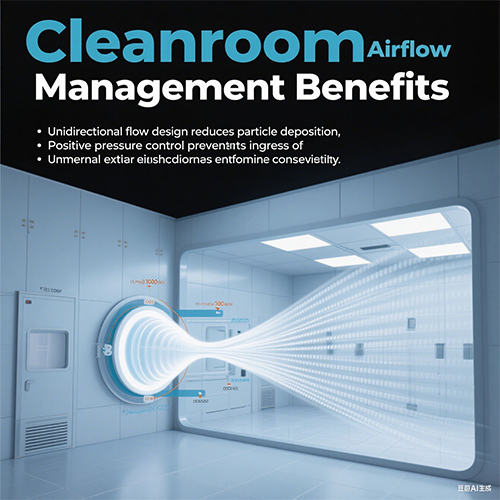
Airflow Management Benefits
- Unidirectional flow design reduces particle deposition
- Positive pressure control prevents ingress of external contaminants
- Uniform airflow distribution ensures environmental consistency
Environmental Control & Contamination Prevention
In terms of environmental control, the cleanroom will be equipped with precision systems for temperature and humidity regulation. This is crucial for preventing electrostatic discharge that could damage sensitive electronic components and ensuring process stability. The facility will also include airlocks and interlocking doors designed to minimize the inflow of contaminants during material and personnel transfers.
Environmental Control Parameters
Parameter | Control Range |
---|---|
Temperature | 22±2°C |
Humidity | 45±5% |
Static Voltage | ≤100V |

Personnel Training & Protocols
Personnel training is another critical component. We will implement rigorous gowning procedures and conduct regular training sessions to reinforce best practices and minimize the risk of contamination from human interaction.
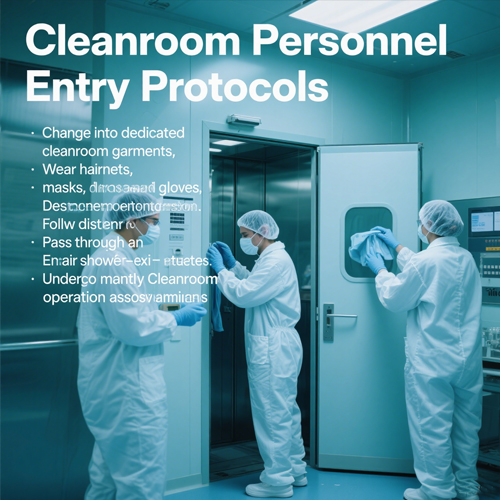
Personnel Entry Protocols
- Change into dedicated cleanroom garments
- Wear hairnets, masks, and gloves
- Pass through an air shower for decontamination
- Follow designated entry/exit routes
- Undergo monthly Cleanroom operation assessments
Real-time monitoring System
Finally, we plan to integrate a robust monitoring system to ensure continuous oversight of environmental conditions and enable rapid response to any deviations. By collaborating with experts like Deiiang Jason.peng and leveraging cutting-edge solutions from brands such as GCC®️ and Deii®️, our new cleanroom will represent a significant advancement in our operational capabilities, supporting our commitment to quality and innovation in the electronics industry.
Monitoring System Features
- Real-time particle concentration monitoring
- Continuous temperature and humidity data logging
- Differential pressure monitoring with alarm systems
- Historical data storage and trend analysis
- Mobile remote access and control
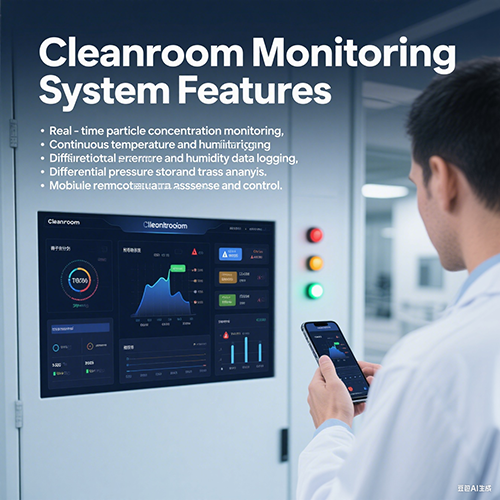
Through advanced cleanroom facilities, we are committed to driving quality standards in electronic manufacturing and providing customers with more reliable and precise product solutions