Introduction
ISO 14644-1:1999 International Standard for Clean Rooms and Related Controlled Environments Part 1 "Air cleanliness classes" has been in use for five years since its release and is facing a time limit for re-examination. If it were not for this reason, the discussion about this standard might not be so intense.
Background of Standard Formulation
ISO/TC 209 is the technical committee responsible for the development of a series of international standards for "Clean Rooms and Related Controlled Environments". Its first working group is responsible for the drafting and review of iso 14644-1. As a member of this working group, I participated in the discussion of the revision of the standard. In the process, we found that there are some problems with the existing standard in theory and practical implementation.
Problems with the Current Standard
1. Inconsistency of Confidence
The current standard ISO 14644-1 applies different confidence levels to clean rooms of different sizes. For example, the standard clearly stipulates that the confidence level of clean rooms with 2 to 9 sampling points is calculated as 15%. The confidence level of A Clean Room can be calculated by the number of sampling points. For example, the confidence level of A Clean Room with an area of 100 m² is only 67%. When the number of sampling points is 5 to 9, if the particle concentrations of all sampling points meet the standard and the average also meets the standard, the confidence level can reach 95%. At this time, the calculation of 95% confidence level is redundant.
2. Limitations of Sampling methods
The current standard sampling method does not allow "especially clean" areas in clean rooms. If the particle concentrations of some sampling points are abnormally low, the cleanliness of the entire clean room may not meet the standard. For example, in A Clean Room with 4 sampling points, if the particle concentrations are 950 particles/m³, 950 particles/m³, 250 particles/m³, and 200 particles/m³, respectively, although these values meet the ISO 4 cleanliness level, the calculated 95% confidence level does not meet the standard.
Additional Issues:
- For a clean room with only 3 sampling points, even if one point has an abnormally low concentration, it cannot be removed, otherwise the minimum number of sampling points will not be met.
- When there are multiple sampling points with abnormally low concentrations, after removing one low value, the 95% confidence calculation of the remaining concentration may still fail to meet the standard.
Summary of Shortcomings
The current sampling method has two main shortcomings: first, different confidence standards are implemented for clean rooms of different areas; second, the location with abnormally good cleanliness is not allowed in the clean room. The current standard assumes that the particle concentration in the clean room is normally distributed, emphasizes the uniform distribution sampling mode, and uses the average value as the judgment standard. However, the practical significance of this judgment method is worth discussing.
Discussion of the New Sampling Method
The new sampling method proposes a unified confidence level for clean rooms of various areas, that is, the confidence level of all clean rooms is 95%. This means that at a 95% confidence level, particle concentrations in at least 90% of the cleanroom area meet the standards. Such improvements are intended to address the inconsistencies and limitations of current standards and improve the efficiency of Cleanroom monitoring and management.
Clean room area (m²) | Existing methods Number of sampling points | New method Minimum number of sampling points (NL) |
---|---|---|
≤ 1 | 1 | 1 |
2 | 2 | 1 |
4 | 2 | 2 |
500 | 23 | 26 |
900 | 30 | 29 |
The new method shows the number of sampling points corresponding to clean rooms of various sizes in a table, which is clear, intuitive and convenient to use. And no matter how many sampling points there are, there is no need to calculate the confidence level. As can be seen from the table, compared with the old method, the number of sampling points of the new method starts to increase when the clean room area is 8 m², and the two sides are close again when it reaches 500 m². Among them, the gap between the two sides is the largest from more than 60 m² to about 300 m², and the number of sampling points of the new method is about 50% more than that of the old method.
The new method is better than the old method in terms of confidence level and the minimum guaranteed area ratio. This also means that the sampling workload is increased, but the results are more reliable.
Random Sampling theory
Calculating the number of sampling points with confidence level shows that the sampling method for clean room air cleanliness classification detection is based on probability theory. A limited number of samples are used to reflect the characteristics of the whole or a certain proportion (such as 90%) of the whole according to a certain confidence level.
The randomness of the sample is the soul of this method. That is to say, all samples in the whole have an equal chance of being drawn and tested, and which one is drawn is just random. Regardless of the quality of the samples, they have an equal chance of being measured. This ensures the objectivity of the sampling and the reliability of the overall reflection.
Application to Clean room Testing:
- Divide the clean room into equal-area units (e.g., 4 m² each)
- Find the number of sampling points from the table
- Randomly select units for testing
- Select random location within each unit
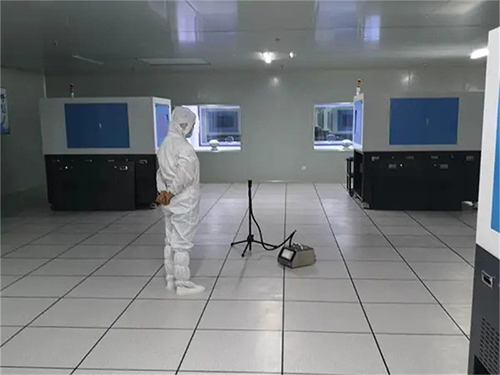
Example of Clean room sampling points distribution
The Challenge of Uniformity
But in the 4 m² space in the clean room, each 4 m² space may be different, such as under the vent, between the vents, or in the place without vents, their situations are also different. And because this small unit is not "isolated from the world", only in the empty vertical laminar flow clean room, this 4 m² unit may be in the "most ideal" state.
Since the premise of random sampling is not so "pure", and since this random sampling method may not reflect the full picture of the particle concentration distribution in the clean room, we can "improve" it with the so-called "semi-random" sampling.
It is to divide the clean room into uniform equal-area blocks according to the number of clean room samples listed in Table 1, and then select sampling points at random within each block for sampli
Semi-random sampling point distribution
Comparison of Sampling methods
Full Random Sampling
- More aligned with random Sampling theory
- Each location has equal chance of selection
- May leave large areas unsampled
- Sampling points may cluster
Semi-Random Sampling
- Considers location characteristics
- Divides room into equal areas
- Random point within each area
- Avoids clustered sampling points
- Maintains some randomness
The "full random" sampling method is more in line with the requirements and conditions of random sampling theory, while the "semi-random" sampling method also takes into account the different characteristics of different locations in the clean room under various circumstances. The "semi-random" sampling method inherits the existing method of dividing the clean room into equal-area sampling areas, and is not limited to the "mechanical" sampling location of the center point of the sampling area.
Advancing Clean room standards
The new sampling methods represent an evolution in Clean room monitoring, balancing theoretical rigor with practical considerations to provide more reliable and consistent results for critical environments.