Standardizing cleaning, disinfection, and usage protocols to ensure testing environment compliance and scientific data integrity
Purpose
To standardize the cleaning, disinfection and use of clean laboratories, ensure that the testing environment meets the requirements and the experimental data is scientific.
Scope of Application
Applicable to clean rooms (areas).
Responsibilities
3.1 Quality Inspection Department
- 3.1.1 Formulate this system;
- 3.1.2 Strictly implement this system.
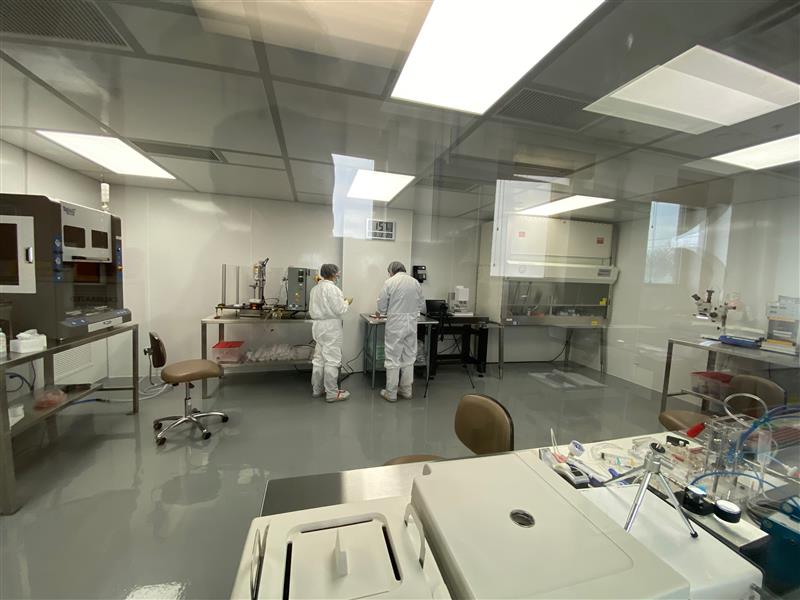
Figure 1: Daily management of clean room
CleanRoom Validation Testing for Medical Devices
Related Definitions
Clean room (area): a room or area where dust particles and microorganisms in the environment need to be controlled.
Work Procedures
5.1 Cleaning and Disinfection
5.1.1 Cleaning and Disinfection Cycle and Scope
5.1.1.1 Cleaning Scope Before and After Each Work
Clean the operating room and irradiate it with ultraviolet light for 30 minutes. Use a mercerized towel soaked in disinfectant to squeeze and wipe the outer surface of the instrument placed on the workbench, then wipe the surface of the workbench (from top to bottom), and wipe the stools and floors in the clean area (including the intermediate floor) after the operation.
5.1.1.2 Weekly Cleaning Scope
In addition to 5.1.1.1, wipe all walls and doors in the clean area, and then wipe the hooks and the floor of the locker room.
5.1.1.3 Monthly Cleaning Scope
External ceiling wipe
5.1.2 Preparation and Use of Disinfectants
Solution | Preparation | Usage |
---|---|---|
0.1% Sanisol solution | Take 40 ml of 5% Sanisol solution, add water to 2000 ml, and shake well. | Used for disinfection of hands, instruments, surfaces of utensils, floors, and walls. |
75% ethanol solution | Take 1579 ml of 95% ethanol and add water to 2000 ml. | Used for disinfection of instruments, surfaces of utensils, floors, walls, and hands. |
Note: Disinfectants are rotated once a month.
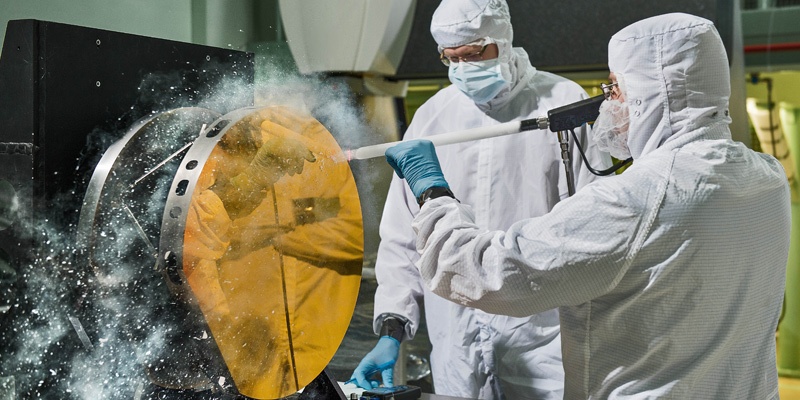
Figure 2: Clean room cleaning
5.1.3 Disinfection Methods and Cycles of Operating Rooms
UV Disinfection
Before each use or when individual sedimentation bacteria exceed the standard, ultraviolet rays can be used for 30 minutes.
Formaldehyde Fumigation
Applied every six months or when sedimentation bacteria are seriously unqualified. Use 10ml of 35-38% formaldehyde solution and 2g of potassium permanganate per cubic meter. Simmer for 16 hours.
Lactic Acid Treatment
If sedimentation bacteria are poor during normal use, spray 0.33~1mol/L lactic acid (1.5ml/m³), re-steam and seal for more than 12 hours.
5.2 Entry and Exit of Personnel
Access Restrictions
- Personnel not related to the work or unauthorized are not allowed to enter the clean area.
- A maximum of 2 people can enter the sterile room.
- No cosmetics, ornaments, or long nails permitted.
- Anyone with a cold, hay fever, or rash is not allowed to enter.
Preparation Protocol
- Room must be cleaned and disinfected before operation
- Clean bench and purification systems must be turned on at least 30 minutes in advance
- Maintain temperature (18~26°C) and Relative humidity (30~70%)
5.2.4 Steps for Entering the Clean Room
Shoe Change
Take off shoes and put them in the corresponding shoe cabinet
Changing Clothes
Put on clean clothes in the changing room
Hand Washing
Thorough washing and drying of hands
Disinfection
Disinfect hands before entering work area
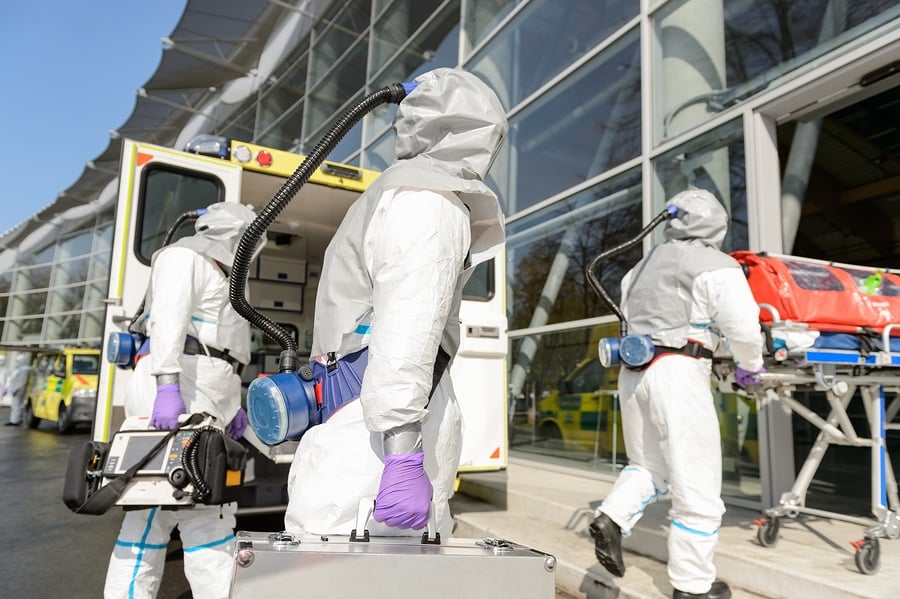
Figure 3: Clean room personnel entering and exiting
5.3 Entry and Exit of Materials
5.3.1 Transfer Requirements
- Items must Enter the clean room through the transfer window
- Items must not be brought in through the flow channel
5.3.2.1 Transfer from Non-clean to Clean Area
- Open non-clean area door and place items in transfer window
- Close window and turn on UV light for ≥15 minutes
- Open clean area door and remove items
5.3.2.2 Transfer from Clean to Non-clean Area
- Open clean area door and place items in transfer window
- Close window and open non-clean area door
- Remove items and close door
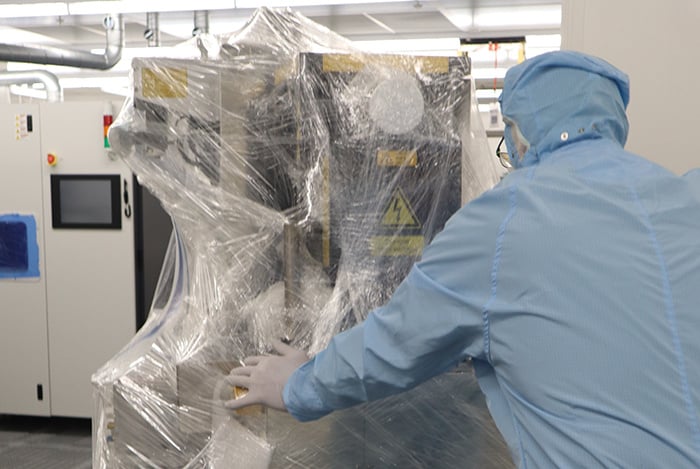
Figure 4: Clean room material in and out
5.4 Precautions
- Operators cannot leave to retrieve items once work begins
- All required items must be planned and prepared in advance
- Alcohol lamp must be lit during operations
- Regular testing of sedimentation bacteria and dust particles
- Proper cleaning and disinfection of cleaning tools
- All items entering sterile room must be properly disinfected
Laboratory Cleanliness Standards
Maintaining a controlled environment through strict protocols ensures the integrity of experimental data and compliance with industry standards. Consistent adherence to these procedures is essential for scientific validity.