1. Purpose
To make the use and management of clean rooms of all levels standardized and followed, so as to maintain good personnel discipline and a clean and safe production environment.
2. Working environment
Parameter | Requirement |
---|---|
Controlled temperature in clean room | 22+3℃ |
Humidity | ≤ 50% |
Cleanliness requirement | Class 10,000 clean room |
3. Scope of application
This method applies to all personnel in the product department, technical department, equipment department, etc. who need to enter and exit the clean room.
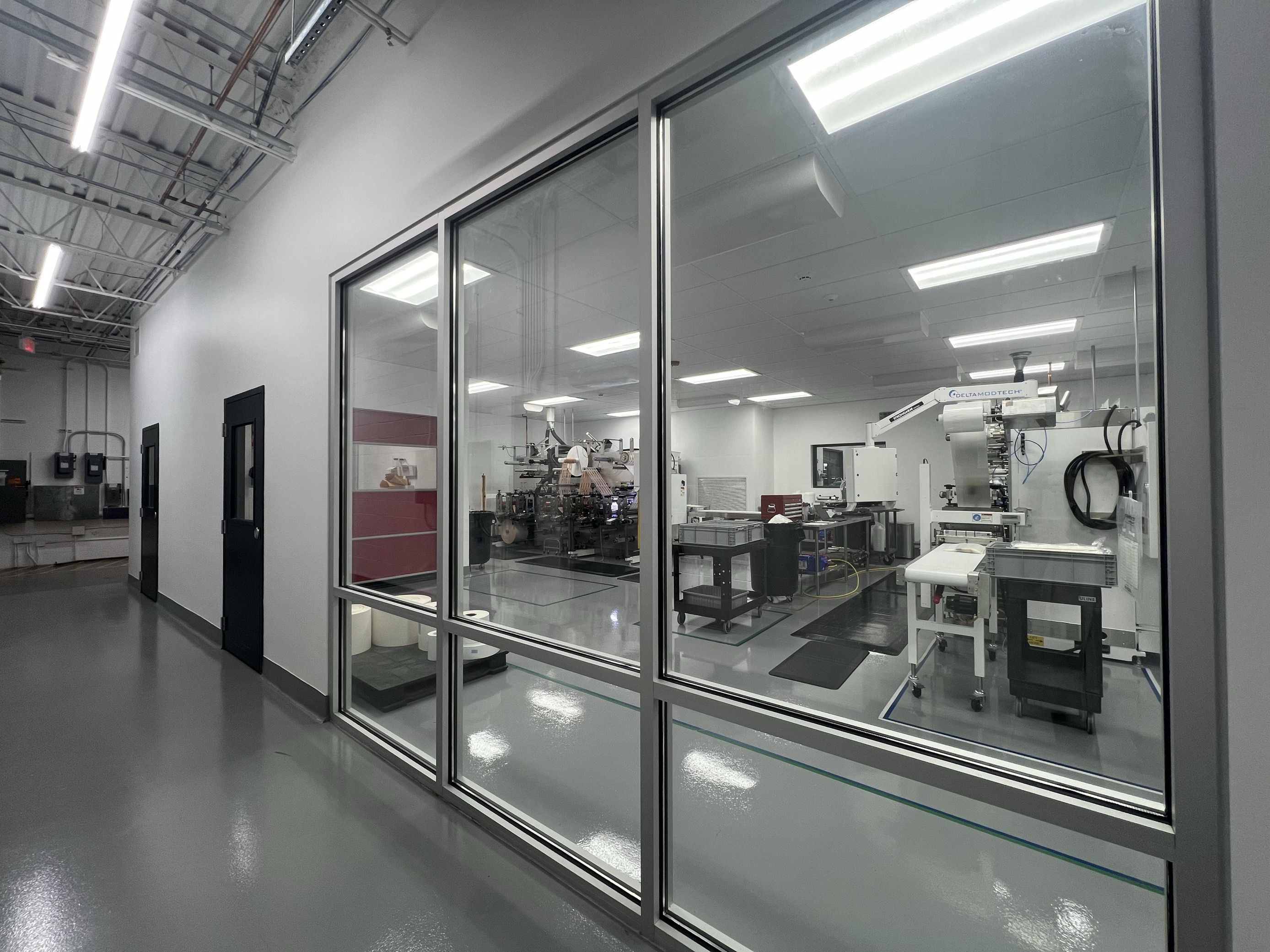
Figure 1: Clean room management
4. Responsibilities
Responsible Party | Duty |
---|---|
All personnel | Maintain Clean room environment |
Product department | Cleaning and management |
Equipment department | Peripheral facilities operation |
Quality department | Environmental parameters testing |
5. Working steps
1.Clean room entry and exit management
Dressing
Hair must be covered in the dust cap and must not be exposed. |
Mouth and nose must be covered in the mask. |
The hem of the dust-free cap must be completely tucked into the collar of the dust-free clothing. |
When wearing the dust-free clothing, do not roll up the sleeves. |
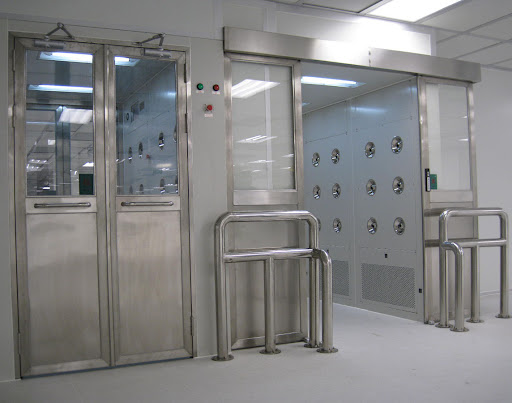
Figure 2: Air shower
Air Shower
Before entering, ensure air shower is operational |
Stand in center, raise hands and rotate >1 circle |
Do not lean on door/wall during operation |
Never force-close or modify parameters |
Items must enter via cargo shower only |
2.Management of items in the clean room
All equipment must be cleaned before entry |
Tools must be non-rusting, non-shedding, non-particulate |
No unauthorized Electronic devices with cameras |
Use dust-free paper only; no erasers/pencils |
Maintain airflow patterns; avoid blocking vents |
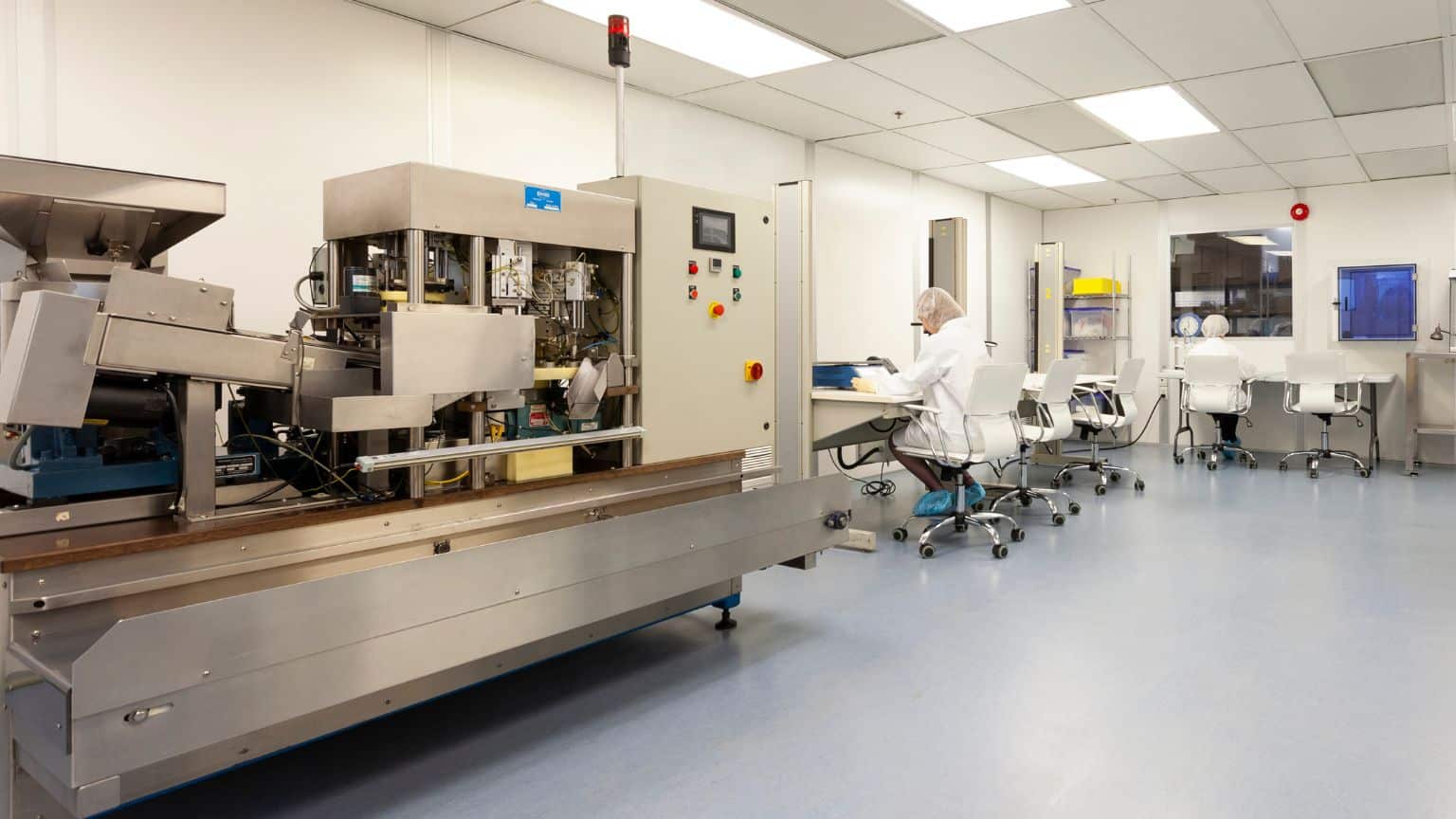
Figure 3: Management of items in A Clean Room
3.Personnel management in the clean room
Wear complete clean clothes at all times |
No playing, fighting, noise or running |
No lighters, cigarettes or flammables |
No food, drinks, or chewing gum |
No woolen clothes exposed to environment |
No makeup, lipstick, powder or long nails |
No entry within 30min after drinking/exercise |
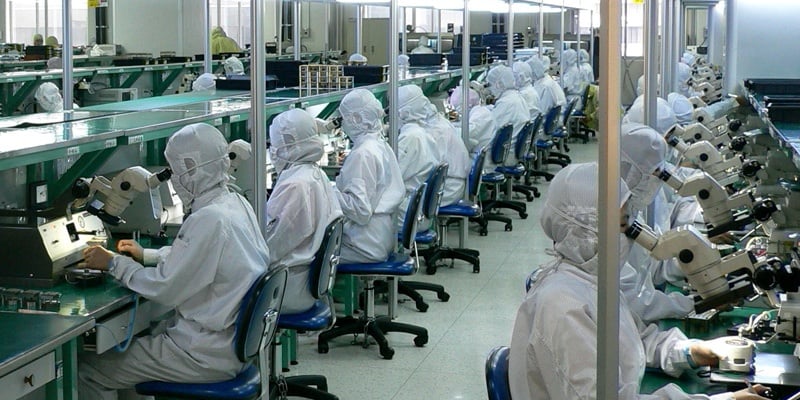
Figure 4: Personnel management in clean room
4.Cleaning and Sweeping Management in Dust-free Rooms
Maintain 24/7 positive pressure systems |
Use approved tools: vacuum, sticky rollers, etc. |
Cover entrances with foot-operated sticky pads |
Full maintenance every 3 months |
Daily cleaning of responsible areas |
Classify and dispose garbage properly |
Regularly clean return air vents |
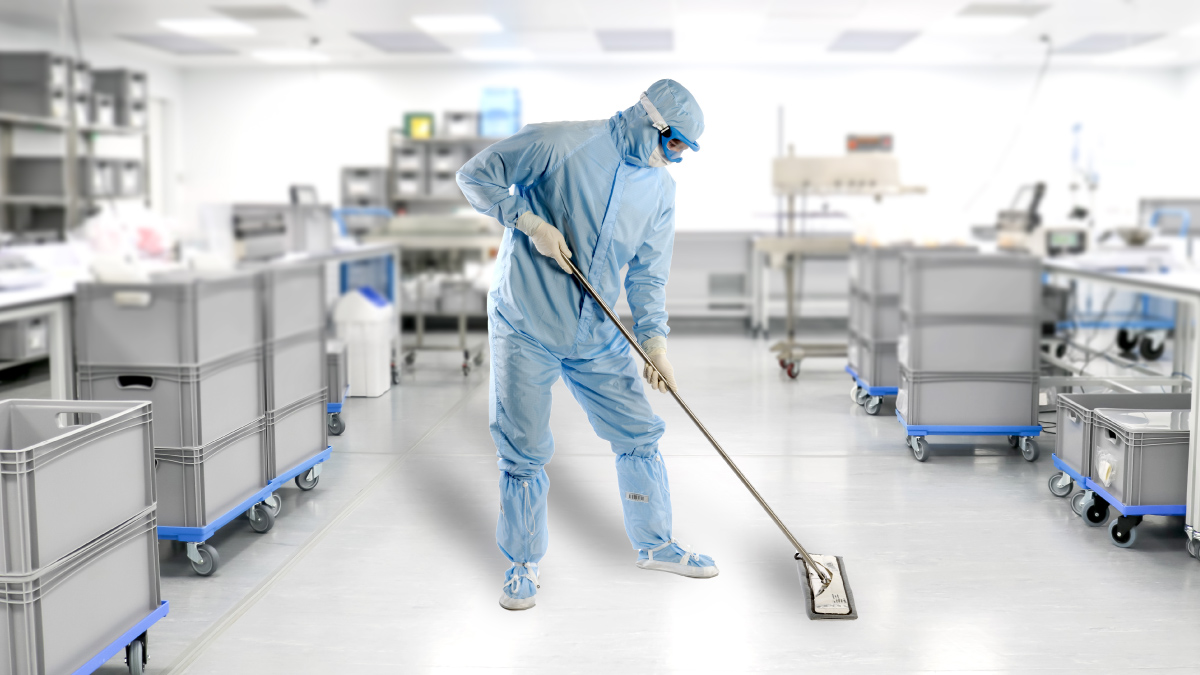
Figure 5: Clean room cleaning management
5.Clean room construction Management
Construction Type | Requirements |
---|---|
1.Internal Construction | • Requires approval from product/equipment departments • Avoid dust/debris affecting cleanliness • Clean site immediately after completion |
2.External Construction | • Submit "Construction Application Form" for approval • Bring own dust-free clothing • Clean and de-dust all items before entry |
6.Visitor Management
Approval | VP+ level authorization required |
Attire | Clean white coats, caps, and shoe covers |
Duration | ≤ 30 minutes maximum stay |
7.Clean room monitoring
Responsibility | Frequency | Parameters | Procedure |
---|---|---|---|
Quality Department | Daily | Cleanliness, Temperature, Humidity | Monitor, record, and notify departments of abnormalities |
Product/Equipment Depts | As needed | System abnormalities | Process issues and resume production after approval |