1. Purpose
Establish clean shed management and control methods to ensure that the company's clean sheds meet the corresponding dust-free level requirements, so as to meet the dust-free environment required by the PCB production process and improve the "zero" defect of products.
2. Scope
This document applies to clean sheds and line clean sheds.
Clean Room definition: what is A Clean Room? | Galvani
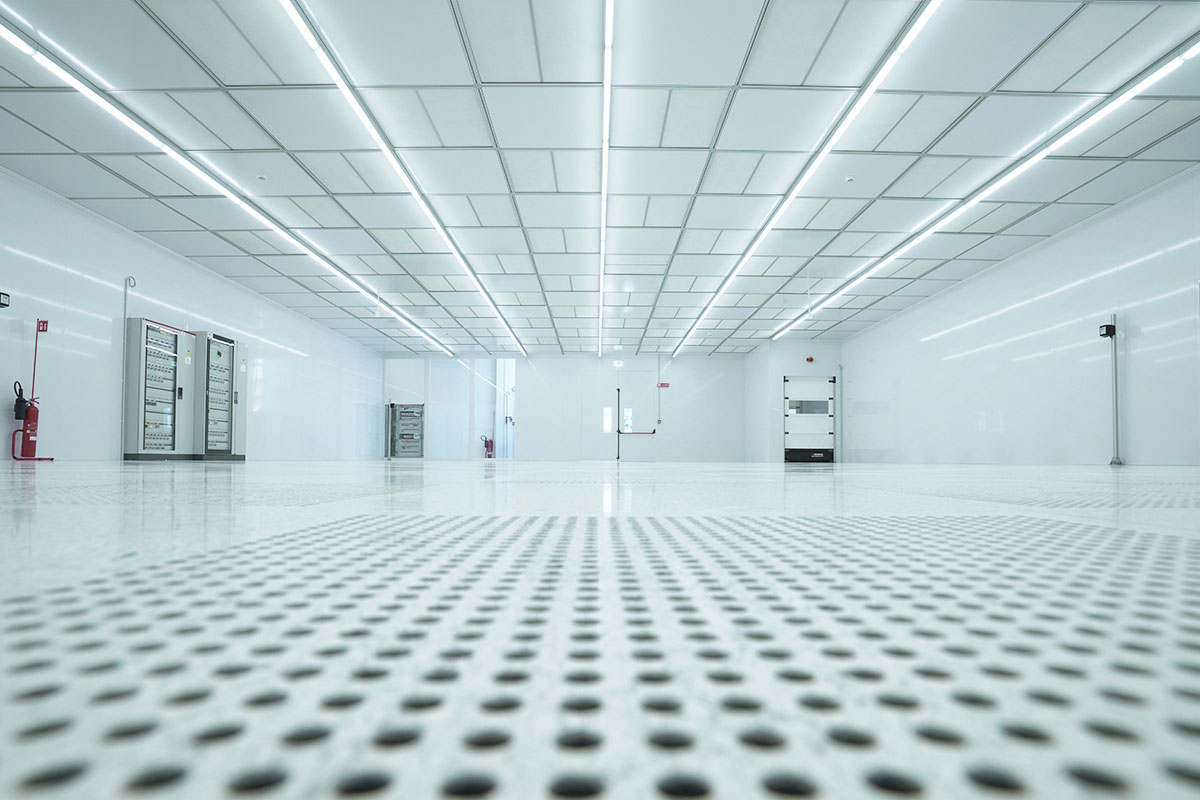
(Figure 1: Clean room)
3. Clean shed temperature and humidity conditions
Area | Humidity | Temperature |
---|---|---|
All clean sheds | 55+5% | - |
Positive soldering clean sheds, line clean sheds and rooms | - | 21+2℃ |
5. Clean shed environment requirements
5.1 Specific requirements for the Clean room environment
Cartons, mops, rusty tools and other items that are prone to dust are not allowed to be stored in the clean shed.
Any materials and tools entering the clean shed must be cleaned before entering the clean shed, and must enter through the transfer door. When moving items from the transfer door, open one door first, put the items in and close them, and then open the other door. It is not allowed to open both doors at the same time at any time.
The line clean shed requires to clean all items, equipment surfaces, walls and floors with sticky cloth every week, clean the ceiling with sticky cloth every 3 months, use a vacuum cleaner to clean the sanitation once every 3 hours, and clean the ceiling with sticky cloth every 6 months.
How Does Hydrogen Peroxide Fogging Fit into Your Cleanroom Cleaning Plan?

(Figure 2: Clean room maintenance)
5.3 Maintenance requirements for clean shed air shower
Staff entering the clean shed must wear dust-free clothing and can enter the clean shed after 15 seconds of air shower. Before air showering, both doors must be closed at the same time (the electrical switch is protected, the door is not closed, and the air shower switch cannot be turned on). During the air shower, the body must be rotated slowly so that the whole body is showered. Multiple people (2 or more) are not allowed to air shower at the same time.
The production department and the user department must clean the Air Filter in the air shower once a month and replace it once a year. The dust-sticking plate at the door of the air shower room is required to be replaced once a day.
5.4 Order of wearing clean room clothes
Order of wearing dust-free clothes: wear a hat, put on a top, put on pants, and put on dust-proof shoes.
5.5 Precautions for wearing dust-free clothes
Wear a hat properly, wrap all the hair in the hat, and tuck the hem of the hat into the collar of the top to prevent hair and dandruff from falling off.
The collar and cuffs of the top should be sealed tightly, the edge of the clothes should be tucked into the waistband of the pants (this action can be exempted for one-piece dust-proof clothes), and the zipper should be pulled to the collar to prevent debris on the body or clothes from falling off.
Trouser legs should be tucked into dustproof shoes.
After putting on dust-free shoes, shoelaces should be tied.
Correct Attire in the CleanRoom

(Figure 3: Cleanroom staff clothing)
5.6 Cleaning and replacement frequency of dust-free clothing
Dust-free clothing should be cleaned twice a week.
Related Information
What is A Clean Room management system?
Users want a clear understanding of what a Clean room management system is, including its purpose, components, and how it helps maintain cleanliness and control contamination in sensitive environments.What are the key components of a clean room management system?
People are interested in learning about the essential elements of a Clean room management system, such as air filtration, HVAC systems, environmental monitoring, cleaning protocols, gowning procedures, and personnel management.How does a clean room management system help with contamination control?
Users want to understand how a management system can minimize the risk of contamination, including the use of air filtration, monitoring systems, sterilization procedures, and personal protective equipment (PPE).What are the best practices for managing a clean room?
This question focuses on operational guidelines and protocols for running an effective clean room, such as cleaning schedules, equipment maintenance, employee training, and contamination prevention strategies.How is the cleanliness of a clean room monitored and maintained?
Users often ask about the monitoring techniques used to ensure a clean room meets cleanliness standards, including particle count testing, microbial monitoring, and air quality assessment.What standards and certifications are required for a clean room management system?
This question involves understanding the industry standards, such as ISO 14644-1 (CleanRoom Classification), GMP (Good Manufacturing Practice), and other regulatory certifications that a clean room must comply with to ensure it meets safety and cleanliness requirements.