GMP Cleanroom monitoring Solutions
Ensuring Product Quality and Safety Through Effective Environmental Control
Introduction to GMP Cleanrooms
GMP (Good Manufacturing Practice) cleanrooms are essential for industries that require stringent environmental controls. These environments must comply with international standards to ensure product quality and safety. Effective monitoring of cleanroom areas is a crucial aspect of maintaining these standards.
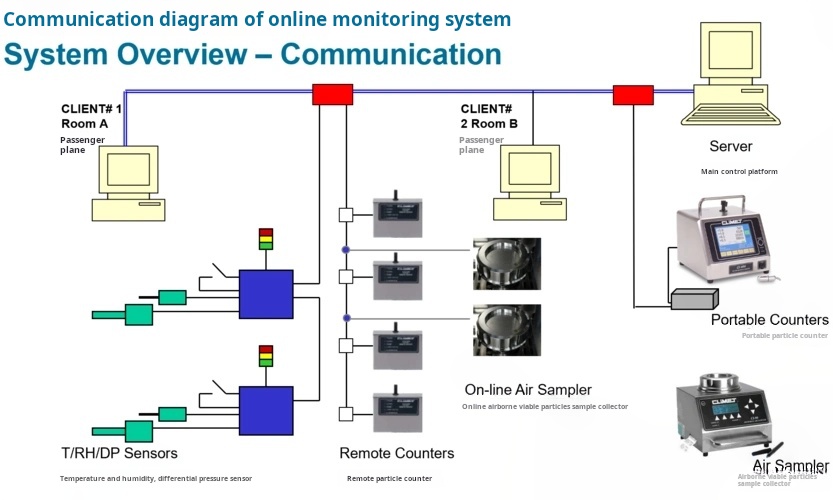
Modern gmp cleanroom facility with advanced monitoring systems
Purpose of Cleanroom Monitoring
The primary purpose of monitoring cleanroom areas is to ensure that environmental conditions remain within specified limits. This includes controlling particulate contamination, temperature, humidity, and airflow. Each of these factors plays a vital role in maintaining the integrity of products manufactured in cleanrooms.
- Ensure environmental conditions stay within specified limits
- Control particulate contamination, temperature, humidity, and airflow
- Maintain product integrity during manufacturing
- Identify deviations and implement timely corrective actions
Monitoring Parameters
Monitoring cleanroom areas involves several critical parameters that are essential for maintaining a controlled environment. Each parameter plays a unique role in ensuring product quality and safety.
Airborne Particulate Counts
Monitoring the number of airborne particles to ensure they do not compromise product integrity.
Temperature & Humidity
Controlling temperature and Relative humidity to maintain the stability of sensitive materials.
differential pressure
Maintaining differential pressure to ensure unidirectional airflow and prevent cross-contamination.
Instrumentation, Technology & Innovation
Advanced Monitoring Equipment
The selection of appropriate instrumentation and equipment is vital for effective cleanroom monitoring. Devices must comply with relevant international standards, such as ISO 14644. High-quality sensors and monitoring systems ensure accurate, reliable data collection and reporting.
Technological Innovations
The integration of advanced technology can enhance cleanroom monitoring. Innovations such as IoT-based monitoring systems allow for real-time data access and analysis, streamlining processes and improving operational efficiency.
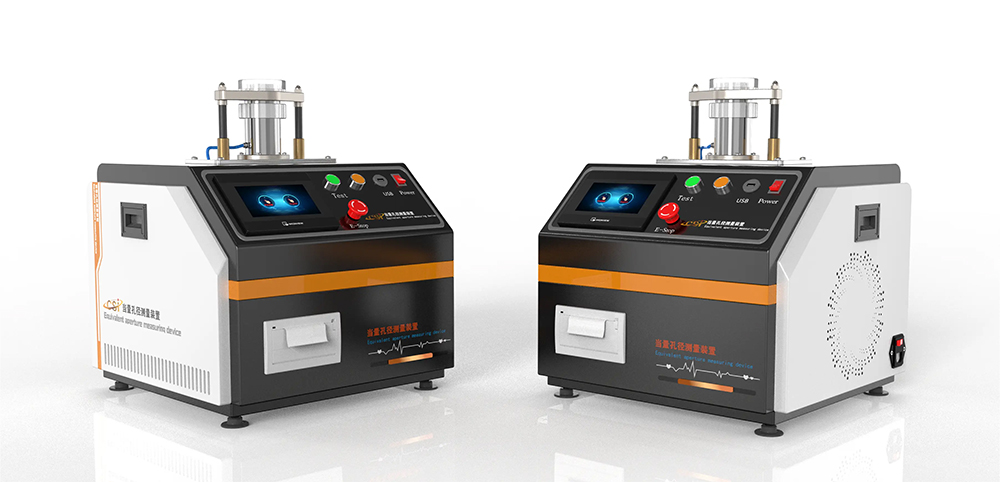
State-of-the-art cleanroom monitoring instruments
International Standards for GMP Cleanrooms
Adhering to international standards is critical for the operation of GMP cleanrooms. These standards provide guidelines for Cleanroom design, operation, and monitoring, ensuring product quality and regulatory compliance.
Standard | Description |
---|---|
ISO 14644 | Cleanrooms and Controlled Environments |
FDA 21 CFR Part 210 | Current Good Manufacturing Practice for Drugs |
FDA 21 CFR Part 211 | Current Good Manufacturing Practice for Finished Pharmaceuticals |
ISO 13485 | Medical Devices - Quality Management Systems |
ISO 9001 | Quality Management Systems - Requirements |
ICH Q7 | Good Manufacturing Practice Guidance for Active Pharmaceutical Ingredients |
Comprehensive Cleanroom Monitoring Solutions
Advanced Technology
IoT-based monitoring systems for real-time data access and analysis.
Regulatory Compliance
Solutions designed to meet international standards such as ISO 14644 and FDA regulations.
Expert Support
Trained professionals to assist with system implementation, training, and ongoing support.
© 2025 GMP Cleanroom Monitoring Solutions. All rights reserved.
Providing advanced CleanRoom monitoring solutions for pharmaceutical, medical device, and biotechnology industries.